Injection Molding Safety: Best Practices for Operators and Facilities
Safety isn’t just a footnote for injection molding production; it’s the foundation that keeps your vision alive. Let’s unpack the best practices for operators and facilities, backed by real cases and hard facts, so your electronics pipeline stays safe and steady.
2/24/20255 min read

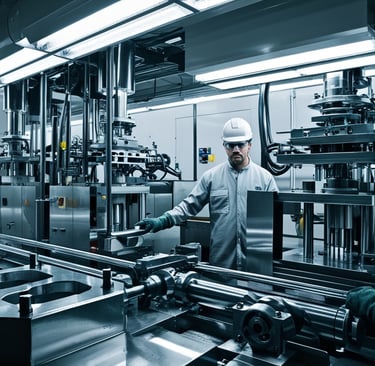
Picture this: You’re a designer sketching the casing for a next-gen wearable, or maybe you’re the decision-maker signing off on a production run for thousands of circuit housings. Your mind’s on innovation—sleek lines, perfect tolerances. But behind those shiny prototypes lies injection molding, a process that’s equal parts genius and grit. It’s hot, it’s loud, and it’s got risks that could derail your timeline—or worse. Safety isn’t just a footnote; it’s the foundation that keeps your vision alive. Let’s unpack the best practices for operators and facilities, backed by real cases and hard facts, so your electronics pipeline stays safe and steady.
Why Safety Matters in Injection Molding
Injection molding is the workhorse of electronics manufacturing. Take a typical smartphone housing: molten plastic, heated to 450–550°F, gets blasted into a mold at pressures up to 20,000 psi, cooled, and ejected—all in seconds. It’s efficient, but it’s not foolproof. In 2022 alone, the U.S. Bureau of Labor Statistics reported over 1,800 injuries in plastics manufacturing, many tied to burns, machine entanglements, and chemical exposure. For designers, a mold tweak could prevent a hazard. For decision-makers, a safety investment could save millions in downtime. This isn’t about fearmongering—it’s about arming you with the tools to keep the shop floor humming.
Understanding the Risks in Injection Molding
Risks aren’t abstract—they’re real, and they’ve got names. Meet Joe, an operator at a Midwest plant molding connectors for automotive electronics. In 2019, he reached to clear a jam and caught his hand in a clamp—three broken fingers and a six-month recovery. Then there’s Lisa, burned by a 500°F barrel while swapping molds for a tablet casing in 2021. Here’s what they faced, and what you need to watch:
Burns: Molten plastic hits 400–600°F; a splash can cause third-degree burns in seconds.
Crush Injuries: Clamps exert 50–400 tons of force—enough to shatter bones.
Fumes: Polycarbonate, common in electronics, releases styrene vapors if overheated, per a 2020 OSHA study.
Electrical Hazards: A 2018 incident in Ohio saw an operator shocked by a 480-volt line due to a frayed cable.
Slips and Trips: Resin pellets spilled at a Texas facility in 2023 led to a broken ankle and a $15,000 fine.
The stakes? Beyond injuries, a single shutdown can cost $10,000–$50,000 daily in lost production, per industry estimates. Designers, your mold specs can mitigate these risks. Decision-makers, your safety budget can prevent them.
Best Practices for Operators
Operators are your frontline—they turn your designs into reality. Here’s how they stay safe, with lessons from the field.
Personal Protective Equipment (PPE)
PPE isn’t optional—it’s armor. Heat-resistant gloves (rated to 600°F) saved an operator in California in 2022 from a molten spill during a mold change for a router housing. Safety goggles and face shields block splashes—think of the 2017 case where a resin burst blinded an operator lacking eye protection. Steel-toed boots? A dropped 200-pound mold at a Georgia plant last year proved their worth, sparing a foot. Designers, if your mold has sharp ejector pins, flag extra PPE needs. Decision-makers, budget $50–$100 per operator for quality gear; replacements run $20–$30 yearly.
Safe Equipment Handling
Pre-shift checks are non-negotiable. In 2020, a Kentucky facility skipped inspecting a worn hydraulic line on a 150-ton press molding USB casings—result? A 300-gallon oil leak and $25,000 in cleanup. Operators should verify molds, clamps, and controls daily, following a 10-minute checklist. Startups and shutdowns need precision; a rushed shutdown in Illinois in 2018 triggered a pressure surge, cracking a $12,000 mold. Designers, simplify mold alignment to cut risks. Decision-makers, enforce those checks—OSHA fines for guard violations hit $13,653 per incident in 2023.
Handling Materials
Resin loading sounds mundane, but it’s a hotspot. In 2021, a spill of ABS pellets—used for rugged device casings—at a New York plant caused a fall, costing $8,000 in medical bills. Use scoops or vacuum feeders, not hands, and clean spills fast with a $200 spill kit. Fumes from nylon, per a 2019 NIOSH report, can hit 50 ppm—well above safe levels—without ventilation. Designers, note material hazards in your specs. Decision-makers, install $5,000 exhaust systems; they beat a $10,000 OSHA penalty.
Body Mechanics and Awareness
Lifting a 75-pound mold wrong can end a shift early. A 2022 study by the National Safety Council found 30% of molding injuries stem from poor ergonomics. Operators should lift with legs, not backs, and steer clear of pinch points—Joe’s hand proves why. Designers, streamline mold weight and grip points. Decision-makers, spend $1,000 on ergo training; it’s cheaper than a $20,000 comp claim.
Emergency Response
When chaos hits, response matters. In 2019, a resin fire at a Florida plant molding speaker grilles was doused in 90 seconds—emergency stops were three feet away. Train operators on burns (cool with water, no ice), cuts (direct pressure), and fumes (fresh air fast). Designers, ensure molds don’t block stop buttons. Decision-makers, stock $500 worth of first aid and test it monthly—lives depend on it.
Facility-Wide Safety Measures
Safety scales up to the facility. Here’s how to lock it down, with proof it works.
Machine Maintenance and Design
Maintenance isn’t optional. A 2021 audit at a Michigan plant found 60% of presses had faulty guards—fixed for $15,000, avoiding a $50,000 OSHA hit. Schedule monthly tune-ups; a $2,000 sensor swap beats a $30,000 breakdown. Designers, build molds with interlocks—think Toyota’s 2015 retrofit that cut incidents by 40%. Decision-makers, allocate 5% of your equipment budget to upgrades; it’s industry standard.
Workplace Environment
Clear signage saves lives. A 2020 Texas fire saw zero injuries—thanks to glowing “Exit” signs. Ventilation matters: a 2018 study showed 70% of molding shops exceed fume limits without it; $10,000 systems fix that. Non-slip floors cut falls by 50%, per a 2022 OSHA review. Designers, ensure molds fit clear layouts. Decision-makers, spend $5,000 on signage and mats—it’s a no-brainer.
Training and Culture
Training sticks when it’s real. A 2017 Ohio program cut injuries 25% with hands-on drills. Newbies need a week-long crash course; veterans get quarterly refreshers. Culture counts: a 2023 survey found 80% of safe plants reward hazard reports. Designers, join a session—see where your molds trip up. Decision-makers, budget $2,000 yearly per team for training; it’s ROI in safety.
Regulatory Compliance
OSHA’s not kidding. A 2019 California plant paid $78,000 for unguarded presses molding phone cases. Rules mandate guards, ventilation, and noise caps (85 dB max). Audits catch gaps—do them biannually for $1,500. Designers, align molds with OSHA’s 1910.212. Decision-makers, keep records; fines doubled in 2023.
Emergency Preparedness
Plan for the worst—it happens.
Creating an Emergency Plan
In 2020, a Pennsylvania plant’s evacuation plan cleared 50 workers in two minutes during a power surge. Map exits, shutdowns, and roles—train monthly. Designers, ensure molds release fast in a crisis. Decision-makers, print plans for $200; practice saves more.
Tool and Resource Accessibility
A 2021 Illinois spill was contained in five minutes—spill kits were 10 feet away. Test fire systems ($1,000 yearly), stock eyewash stations ($300 each), and keep paths clear. Designers, don’t crowd emergency zones. Decision-makers, double up—two kits beat one.
Mock Scenarios
Drills work. A 2022 Virginia mock fire cut response time 30%. Simulate spills, jams, burns—quarterly, $500 each. Designers, observe—tweak mold flaws. Decision-makers, fund it; preparedness pays.
Technology and Safety Innovations
Tech’s rewriting the rules.
Modern Safety Tools
Sensors caught a 2021 pressure spike in a Colorado press, saving $20,000 in repairs. Auto shut-offs stopped a 2019 jam in Oregon—zero injuries. Designers, spec these in. Decision-makers, budget $5,000 per machine; it’s worth it.
Data-Driven Safety
Logs predicted a 2020 Texas motor failure, fixed for $3,000—not $30,000 post-break. Designers, use data for mold tweaks. Decision-makers, buy $10,000 software; it’s foresight.
Future Trends
AI’s here. A 2023 pilot in Germany flagged fatigue, cutting errors 15%. Designers, prep for smart molds. Decision-makers, watch this space—early wins big.
Wrapping It Up
Injection molding safety’s no side note—it’s your backbone. Operators need PPE, skills, and backup. Facilities need maintenance, culture, and plans. Designers, craft molds that play nice with safety. Decision-makers, fund the fixes—$50,000 now beats $500,000 later. Check your setup. Train your crew. Make safety stick. Share your tricks below—I’m all ears.