Injection Molding in Packaging: Creating Durable and Aesthetic Solutions
In the fast-moving world of electronics, where products live or die by their ability to protect delicate components and woo picky consumers, injection molding has become a quiet hero.
2/24/20256 min read
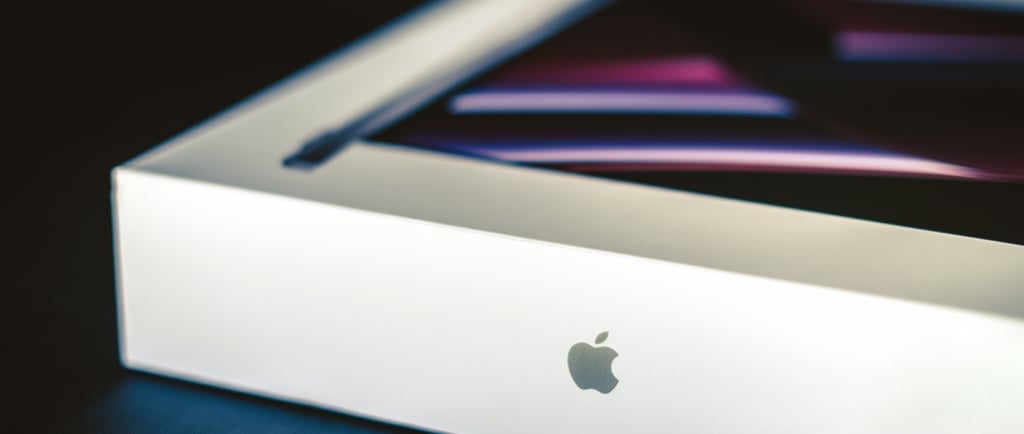
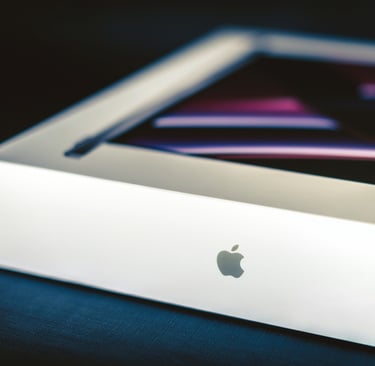
Imagine you’re holding a sleek, lightweight plastic case for your latest wireless earbuds. It’s tough enough to survive a drop from your desk, yet polished enough to catch the eye of a customer browsing a store shelf. Or picture a tamper-evident cap on a battery pack—simple, functional, but with a satisfying click that tells you it’s secure. These aren’t accidents of design; they’re the result of a manufacturing marvel called injection molding. For designers and decision-makers in electronics development, this process isn’t just a tool—it’s a game-changer that blends durability with aesthetics in ways that elevate packaging from an afterthought to a competitive edge.
In the fast-moving world of electronics, where products live or die by their ability to protect delicate components and woo picky consumers, injection molding has become a quiet hero. Let’s dive into why this method matters, how it’s shaping packaging for things like containers and caps, and what it means for your next big project.
What is Injection Molding?
At its heart, injection molding is like a high-tech kitchen recipe. You take a material—say, polypropylene or PET—melt it down to a gooey liquid, shoot it into a precisely crafted mold, let it cool, and pop out a finished piece. It sounds simple, but the magic lies in the execution. Those molds? They’re engineered with tolerances tighter than a drum, letting you crank out thousands of identical parts in a single day.
For electronics packaging, the go-to materials are plastics that can take a beating without adding bulk—think polyethylene for flexibility or polycarbonate for crystal-clear strength. Why do designers love it? Speed, for one. You can go from sketch to production in weeks, not months. Scalability, too—whether you need 500 prototypes or 5 million units, injection molding delivers. And then there’s the ability to craft shapes that’d make a 3D printer blush—think intricate battery housings or snap-fit lids with built-in hinges.
I’ve seen engineers light up when they realize they can tweak a mold to add a rib here or a curve there, all without breaking the bank. That’s the kind of flexibility that keeps injection molding at the top of the heap.
The Role of Injection Molding in Packaging
Electronics development isn’t just about circuit boards and firmware—it’s about getting those innovations into customers’ hands safely and stylishly. Packaging is your first handshake with the user, and injection molding makes it a firm one. The electronics industry demands lightweight designs that don’t skimp on strength, cost-effective production that scales with demand, and parts that look good doing it. Injection molding checks all those boxes.
Take containers, for instance. Picture the clamshell case for a high-end smartwatch—tough enough to shield the device during shipping, but with a glossy finish that screams premium. Or think about battery enclosures for IoT gadgets, molded to hug every contour of the cells inside while keeping them safe from dust and jostling. Then there’s caps—those little unsung heroes. A screw-on lid for a power bank, a flip-top cover for a headphone charging case, or a tamper-evident seal for a medical device battery pack. These aren’t just functional; they’re the difference between a product that feels cheap and one that feels like a keeper.
And let’s not sleep on sustainability. I’ve talked to decision-makers who’ve lost sleep over eco-conscious consumers and stricter regs. Injection molding can help—using recyclable plastics or cutting waste by nailing the design on the first shot. It’s not perfect, but it’s a step toward packaging that doesn’t end up haunting a landfill.
Durability Through Design
Here’s where the rubber—or plastic—meets the road. Electronics packaging has to survive real life: shipping crates stacked like Jenga towers, kids tossing gadgets into backpacks, or that inevitable fumble onto a concrete floor. Injection molding doesn’t just make parts; it makes them tough.
It starts with the mold. Designers can tweak wall thickness to avoid weak spots, add reinforcing ribs for extra oomph, or curve edges to shrug off impacts. I remember a project where a team was sweating over a drone battery case—needed it light but sturdy. They used injection molding to build in a honeycomb pattern inside the walls. The result? A container that could take a 6-foot drop and still pop open like nothing happened.
Caps get the same treatment. A threaded lid for a power adapter might look simple, but mold it right, and it’ll endure a hundred twists without stripping or cracking. Tamper-evident caps—say, for a sealed sensor pack—can be designed with breakaway rings that snap clean, proving the product’s untouched. It’s not just about surviving; it’s about inspiring confidence.
I’ve heard designers joke that injection molding is like giving their packaging a suit of armor. It’s not far off—except this armor’s custom-tailored and ready for mass production.
Aesthetic Advantages
Durability’s great, but let’s be real: in electronics, looks can seal the deal. A clunky, dull package won’t cut it when you’re competing for shelf space or unboxing videos. Injection molding doesn’t just churn out parts—it crafts experiences.
The precision is unreal. Molds can replicate details down to the micron, giving you smooth surfaces, sharp lines, or textured grips that feel good in the hand. Want a matte finish on a smart speaker case? Done. A glossy cap with your logo embossed in 3D? No problem. Colors? Mix them into the plastic before molding, and you’ve got vibrant hues that won’t chip or fade.
I once chatted with a designer who’d spent weeks agonizing over a wireless charger’s packaging. They went with an injection-molded container—jet black, with a soft-touch finish and a subtle wave pattern. It wasn’t just a box; it was a statement. Customers raved about it online, and sales spiked. That’s the power of aesthetics done right.
Caps can shine here, too. A flip-top lid with a satisfying snap or a translucent cap showing off the tech inside—it’s these touches that turn packaging into a billboard for your brand. Decision-makers take note: when your product looks this good, it’s not just packaging; it’s marketing.
Innovations and Trends
Injection molding isn’t sitting still—it’s evolving with the electronics world. New tricks like multi-material molding let you combine hard and soft plastics in one shot—think a rigid container with a grippy overmold. Thinner walls are cutting weight, perfect for wearable tech where every gram counts. I’ve seen teams shave ounces off a fitness tracker case without losing an ounce of strength.
Sustainability’s heating up, too. Bio-based plastics—think corn-derived PLA—are sneaking into molds, and biodegradable options are on the horizon. It’s not mainstream yet, but for eco-minded brands, it’s a way to stand out. And then there’s smart packaging: caps with molded-in RFID tags for tracking, or child-safe lids that click into place with a twist. I’ve got a hunch we’ll see more of this as IoT gadgets multiply.
One engineer I know was buzzing about a project where they molded a sensor housing with integrated vents—cut assembly time in half and looked slick to boot. That’s the kind of innovation that keeps injection molding ahead of the curve.
Benefits for the Packaging Industry
So, why should you care? If you’re a designer, injection molding hands you a toolkit to dream big—detailed, durable, dazzling parts, fast. For decision-makers, it’s about the bottom line. High-volume runs slash per-unit costs, and the consistency means fewer returns from cracked cases or leaky caps. Quality control’s baked in—once the mold’s dialed, every piece is a carbon copy.
Flexibility’s the kicker. Need a BPA-free enclosure for a kid’s toy? Switch materials. Facing a new safety spec? Tweak the design. I’ve watched teams pivot mid-project—say, adding a snap-fit lid to a prototype—and still hit deadlines. That’s gold in an industry where speed is survival.
And the numbers don’t lie. A well-molded package can cut shipping damage by double digits, saving you headaches and cash. It’s not just a process; it’s a strategic play.
Conclusion
Injection molding isn’t glamorous—no one’s snapping selfies with a mold press. But for designers and decision-makers in electronics development, it’s the secret sauce behind packaging that protects, performs, and persuades. From rugged containers cradling your latest gadget to caps that click with confidence, this method delivers durability and aesthetics in equal measure.
So, next time you’re sketching a housing or greenlighting a production run, give injection molding a hard look. It’s not just about making parts—it’s about making your product unforgettable. In a world where consumers judge books by their covers (and gadgets by their cases), that’s a win worth chasing.