Injection Molding for Toys: From Concept to Store Shelves
Injection Mold is the unsung hero of toy manufacturing, and if you’re a designer or decision-maker in electronics development, this process is more relevant to your world than you might think.
2/24/20256 min read
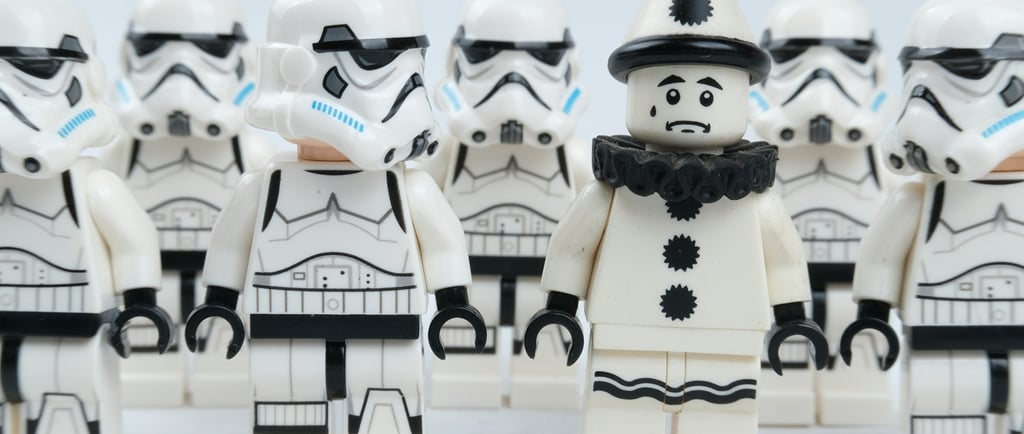
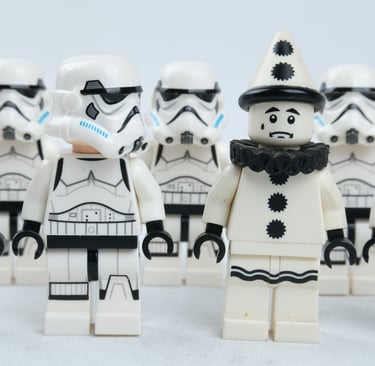
Picture this: It’s a rainy afternoon, and my nephew is sprawled across the living room floor, gleefully assembling a plastic robot toy that shoots little foam discs. I’m watching him, coffee in hand, marveling at how this chunk of brightly colored plastic went from someone’s wild idea to a kid’s obsession. Turns out, the secret sauce behind it—and so many toys like it—is injection molding. It’s the unsung hero of toy manufacturing, and if you’re a designer or decision-maker in electronics development, this process is more relevant to your world than you might think. Let’s take a walk through the journey, from that first spark of inspiration to the moment it lands on store shelves, and see how injection molding bridges creativity, electronics, and mass production.
Dreaming Up the Toy – The Conceptual Stage
Every toy starts with a dreamer. Maybe it’s a designer doodling in a notebook, inspired by the latest superhero flick, or a team brainstorming the next big thing in interactive play. For you folks in electronics development, this is where the fun begins—because today’s toys aren’t just hunks of plastic. They’re packed with circuits, sensors, and LEDs, turning a simple car into a remote-controlled marvel or a doll into a chatbot with a personality.
The process kicks off with sketches—rough, messy, and full of possibility. Then comes the leap to 3D modeling, where CAD software turns those scribbles into something tangible. I’ve talked to designers who swear by this stage, tweaking every curve and angle until it’s just right. But here’s the kicker: even at this early point, injection molding is lurking in the back of their minds. Why? Because the way a toy’s designed—its shape, its parts, how it’ll snap together—has to play nice with the molding process. Think of LEGO bricks: those perfect little studs and clips didn’t happen by accident. They’re a masterclass in designing for manufacturability.
For electronics pros, this is your moment to shine. If that toy’s got a battery compartment or a speaker, you’re already thinking about tolerances, material choices, and how to keep the guts safe from a kid’s inevitable tantrum. It’s less about “will it look cool?” and more about “can we mold it, wire it, and make it last?” That’s the magic of this stage—blending imagination with practicality.
Designing for Injection Molding – The Blueprint
Now, let’s get into the nitty-gritty. Designing for injection molding isn’t just art—it’s science with a deadline. You’ve got to nail the basics: uniform wall thickness so the plastic cools evenly, draft angles to pop the part out of the mold without a fight, and no funky undercuts that’ll trap it inside. I remember chatting with a mold designer once who likened it to baking a cake—you don’t want it sticking to the pan, right?
Materials are the next big decision. Most toys lean on trusty plastics like ABS—tough, colorful, and kid-safe—or polypropylene for its flexibility. If you’re embedding electronics, ABS is your buddy because it’s stable and can handle a little heat without warping. Imagine designing a toy drone: the shell needs to be light yet sturdy, and the plastic’s got to encase those delicate circuits without frying them during production. That’s where your expertise as an electronics decision-maker comes in—picking a material that balances cost, performance, and safety.
Prototyping is the reality check. Designers might 3D-print a few versions or run a small mold to test the fit. I’ve seen teams tweak a battery hatch ten times just to get the snap perfect. Ever wonder how Barbie’s tiny shoes stay on? That’s decades of molding know-how at work. For you, it’s about ensuring the LED blinks through the plastic just right or the motor hums without rattling loose. It’s a dance between form and function, and injection molding is the choreography.
Crafting the Mold – The Heart of the Process
Here’s where the rubber—or rather, the plastic—meets the road. The mold is the beating heart of injection molding, and it’s a marvel of engineering. These aren’t cheap plastic trays; they’re precision-cut steel or aluminum beasts, built to crank out thousands of toys without flinching. I once toured a mold shop and watched a CNC machine carve out a mold cavity—it was like watching a sculptor, but with way more math.
Making a mold is an investment. We’re talking five or six figures for a complex toy with multiple parts, like a transforming robot with electronic guts. But here’s why it’s worth it: once that mold’s done, you can pump out toys at pennies a piece. For decision-makers, this is the cost-benefit equation you live for—high upfront cost, massive payoff in scale. And the quality? A good mold means every toy comes out smooth, shiny, and ready for action. That sleek finish on a toy controller? Thank the mold’s polished surface.
For electronics integration, molds get even trickier. You’re designing cavities for buttons, screens, or wiring channels. One slip-up, and the plastic floods where it shouldn’t, shorting out your circuit. It’s a reminder that your role isn’t just picking components—it’s collaborating with mold-makers to ensure the toy’s brain and body work in harmony.
Injection Molding in Action – Bringing the Toy to Life
Now, let’s step onto the factory floor. The injection molding machine is a beast—think of it as a giant syringe meets a pressure cooker. Plastic pellets melt into a gooey soup, get shot into the mold under insane pressure, cool off, and voilà—a toy part pops out. I’ve seen it in action, and it’s oddly satisfying, like watching a 3D printer on steroids.
Speed is the name of the game here. A cycle can take seconds, meaning thousands of toys roll out daily. For a hot holiday release—like a singing dinosaur with glowing eyes—that’s gold. Precision is just as clutch. Tolerances are tight, down to fractions of a millimeter, so that gear clicks into place or that circuit board slots in without a hitch. Imagine designing a toy car: if the axle holes are off by a hair, it won’t roll. Your electronics need that same exactness—misalign a speaker port, and the sound’s muffled.
I once asked a factory tech what he loved most about the job. “The sound of the mold opening,” he said, grinning. “It’s like the toy’s born right there.” For you, it’s the moment your design—plastic and circuits alike—becomes real.
Finishing Touches – From Mold to Market
The toy’s out of the mold, but it’s not ready for prime time yet. Post-processing is where it gets its personality. Painting turns a gray blob into a fire-engine-red truck. Assembly snaps the arms onto the body or screws the battery cover shut. For electronics folks, this is crunch time—wiring up the guts, testing the buttons, making sure the lights flash on cue. I’ve seen teams cheer when a prototype’s speaker crackles to life for the first time.
Quality control is non-negotiable. Toys get dropped, twisted, and chewed (yep, kids are brutal). The plastic’s got to hold up, and the electronics can’t spark or overheat. Safety regs are strict—no sharp edges, no toxic junk. Then comes packaging—bright, bold, and begging to be grabbed off the shelf. Ever notice how a toy’s box screams “pick me”? That’s no accident.
Injection molding keeps this whole show affordable. Without it, that $20 robot would cost triple. For decision-makers, it’s the efficiency you dream of—low per-unit costs, high output, happy customers.
On the Shelves – The Final Destination
Finally, the toy hits the stores. Whether it’s a local toy shop or a Walmart aisle, this is the payoff. Kids squeal, parents shell out cash, and your design’s a hit—or at least, that’s the hope. Injection molding makes seasonal crazes possible—think movie tie-ins that flood shelves overnight—or keeps classics like Hot Wheels rolling year after year.
There’s a sustainability angle, too. Some companies are molding with recycled plastics or experimenting with biodegradable stuff. For electronics designers, that’s a challenge—can the circuits play nice with greener materials? It’s a curveball worth tackling.
Next time you spot a toy in the wild, think about the journey. That plastic shell, those blinking lights—it’s a story of creativity, engineering, and a little molten magic.
Conclusion
So, there you have it: from a designer’s sketch to a kid’s grubby hands, injection molding is the thread tying it all together. For you designers and decision-makers in electronics development, it’s a process that demands your input—from concept to mold to market. You’re not just building toys; you’re crafting experiences, powered by plastic and circuits.
Take a second to appreciate it. Maybe even sketch your own toy idea—I’d bet there’s a kid out there who’d love it. Behind every playtime moment is a team like yours, and injection molding’s the quiet genius making it happen.