Injection Molding for Prototyping: Is It Worth It?
Injection molding is sneaking its way into the prototyping conversation more often these days, especially in electronics development where precision and material performance matter. But it’s not a one-size-fits-all solution.
2/22/20256 min read
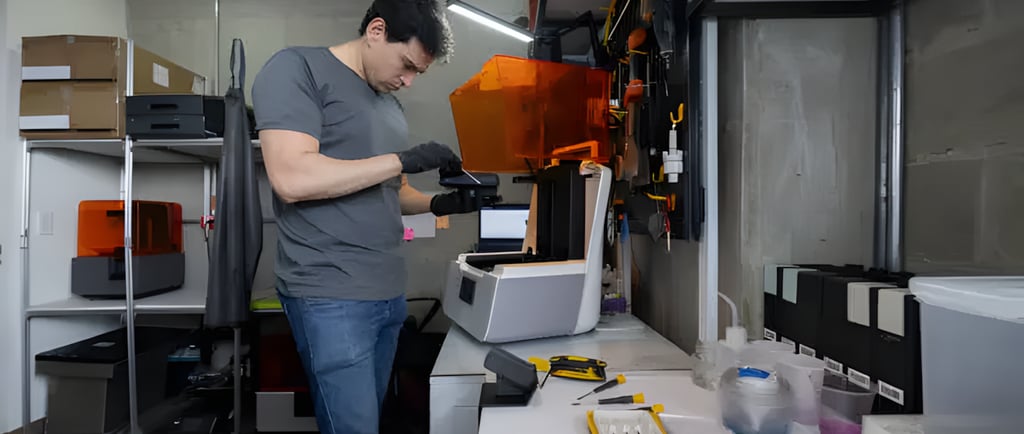
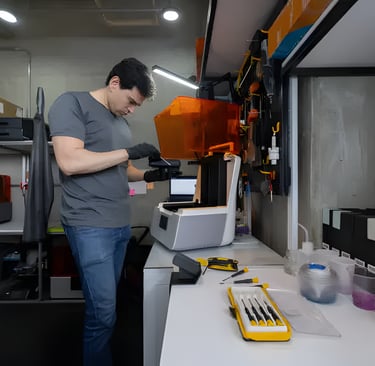
Picture this: You’re an electronics designer, hunched over your desk, sipping lukewarm coffee, staring at a 3D model of a sleek new gadget housing on your screen. It’s perfect—at least in theory. But now comes the hard part: turning that digital dream into a physical prototype that doesn’t just look good but works in the real world. You’ve got options—3D printing, CNC machining, maybe even urethane casting—but someone in your team pipes up with a curveball: "What about injection molding?" You pause. Isn’t that for mass production? Is it even worth considering for prototyping? Let’s dive in and figure this out together.
The truth is, injection molding is sneaking its way into the prototyping conversation more often these days, especially in electronics development where precision and material performance matter. But it’s not a one-size-fits-all solution. As designers and decision-makers, you’re juggling timelines, budgets, and that relentless pressure to get it right the first time. So, let’s break down whether injection molding is your prototyping hero—or a costly detour.
Understanding Injection Molding in Prototyping
First things first: what is injection molding? If you’ve ever seen those satisfying factory videos where molten plastic gets squirted into a mold, cools into a perfect shape, and pops out like a Lego brick, that’s it. It’s the go-to for cranking out millions of identical parts—think phone cases or keyboard keys. But prototyping? That’s a different beast.
Traditionally, injection molding was the domain of production runs, not one-off experiments. Yet, here we are in 2025, and it’s popping up in design labs. Why? Because it delivers parts that don’t just look like the final product—they act like it too. For electronics, where enclosures need to snap together just right or withstand heat from a circuit board, that’s a big deal.
Here’s the catch: prototyping molds aren’t the same as production molds. The ones for prototyping are simpler—think aluminum instead of hardened steel—and cheaper to make. They’re built for dozens or hundreds of parts, not millions. So, if you’re testing a new wearable device casing or a connector that needs to feel production-ready, injection molding might just deserve a seat at the table.
Benefits of Injection Molding for Prototyping
Let’s talk perks, because injection molding brings some serious firepower to the prototyping game—especially for electronics folks like us.
High Precision and Quality
You know that moment when you’re testing a prototype, and the tolerances are off by a hair, so the PCB doesn’t fit? Infuriating, right? Injection molding laughs at that problem. It churns out parts with tolerances as tight as ±0.005 inches, and the surface finish is smooth enough to skip extra sanding or polishing. For an electronics housing that needs to align perfectly with tiny components, that’s gold.
Material Versatility
Here’s where it gets fun. With injection molding, you’re not stuck with flimsy 3D printing resins. You can use real-deal thermoplastics—ABS, polycarbonate, even glass-filled nylon—that match what you’ll use in production. Want a prototype that can handle the heat of a running processor or the drop-test from a clumsy coworker? This is your ticket.
Scalability
Ever had a prototype that worked great… until you scaled it up and everything fell apart? Injection molding bridges that gap. Since it mimics the production process, your prototype is basically a dress rehearsal for the real thing. For electronics teams, that means fewer nasty surprises when you hand off to manufacturing.
Speed for Larger Runs
Okay, mold-making isn’t instant—it’s not 3D printing—but once that mold is ready, you can pump out parts fast. Need 50 or 100 prototypes for user testing or a trade show demo? Injection molding can deliver in a fraction of the time it’d take to machine each one by hand.
I remember a project from my early days designing smart home sensors. We needed 200 units for a pilot test, and injection molding saved our bacon. The parts were consistent, the material held up, and we didn’t blow the deadline. That’s the kind of win that sticks with you.
Drawbacks and Challenges
Now, let’s not get too starry-eyed. Injection molding isn’t all sunshine and perfectly molded parts. There are some hurdles—big ones—that might make you think twice.
High Upfront Costs
The mold is the kicker. Even a simple aluminum one can set you back $1,000 to $10,000, depending on complexity. Compare that to a $50 3D print job, and your CFO might start sweating. For a small electronics startup or a one-off proof-of-concept, that price tag stings.
Longer Lead Times
Patience isn’t always a virtue in prototyping. While 3D printing spits out a part overnight, injection molding takes weeks—designing the mold, machining it, testing it. If your deadline’s tight or your boss is breathing down your neck, this could be a dealbreaker.
Design Limitations
Here’s a personal pet peeve: once the mold’s made, changes are a hassle. Found a flaw in your enclosure design after the mold’s cut? You’re either living with it or shelling out for a new one. In electronics, where we’re tweaking circuits and layouts constantly, that rigidity can chafe.
Not Ideal for Small Runs
If you just need one or two prototypes to show the team, injection molding’s overkill. The economics don’t pencil out until you hit dozens—or hundreds—of parts. For early-stage tinkering, it’s like using a sledgehammer to crack a walnut.
Comparing Alternatives
So, how does injection molding stack up against the usual suspects? Let’s run the numbers for electronics prototyping.
3D Printing
The darling of rapid prototyping. It’s cheap, fast, and lets you iterate like crazy. I’ve lost count of how many late-night 3D print jobs I’ve run to test a new idea. But the parts? Often too brittle or rough for serious functional testing—especially for electronics housings that need durability.
CNC Machining
This one’s a precision champ. CNC can carve a metal or plastic prototype that’s spot-on for testing fit and finish. But for complex geometries—like a curvy smartwatch casing—it’s slow and pricey per part. Fine for one-offs, less so for batches.
Urethane Casting
A middle ground. You make a silicone mold (cheap!), pour in resin, and get decent parts for small runs. It’s great for 10–20 prototypes, but the materials don’t always match production specs, and consistency can wobble.
When Injection Molding Wins
For electronics, injection molding shines when you need 50+ parts in production-grade materials—like a batch of IoT device casings for field testing. It’s less about speed and more about nailing the endgame.
Is It Worth It? Factors to Consider
Alright, decision time. Is injection molding worth it for your next electronics prototype? Here’s what to chew on.
Project Goals
What’s the prototype for? If it’s a quick visual mockup for a pitch, skip injection molding. But if you’re stress-testing a housing for a new fitness tracker—drop resistance, heat dissipation, snap-fit assembly—it’s a contender.
Budget
Be honest: can you stomach the upfront hit? A mold might cost $5,000, but if it saves you from a $50,000 redesign later, it’s a bargain. Run the numbers with your team.
Timeline
Got a month? Injection molding could work. Got a week? Stick to 3D printing. In electronics, we’re often racing the clock, so this one’s critical.
Volume
How many do you need? For a single prototype, it’s a no-go. But 100 units for a pilot run? Now we’re talking.
I once worked with a team launching a Bluetooth speaker. We went with injection molding for 75 prototypes—needed the real material to test acoustics and durability. Cost us a chunk upfront, but the feedback we got was priceless. Compare that to a 3D-printed run that cracked during testing, and the choice was clear.
Tips for Making Injection Molding Work for Prototyping
Convinced it might fit? Here’s how to make it painless.
Use Soft Tooling
Go for aluminum molds over steel. They’re cheaper (think $1,000–$3,000) and faster to make. Perfect for electronics prototypes where you don’t need a million cycles.
Partner with Experts
Find a mold maker who gets electronics. They’ll tweak your design—draft angles, wall thickness—so it molds like a dream and doesn’t trap your budget in rework.
Start Small
Test with a single-cavity mold. It’s less risk, less cost, and if it works, you can scale up to multi-cavity later.
Combine with Other Methods
Don’t ditch 3D printing entirely. Use it for early concepts, then switch to injection molding when you’re ready to simulate production. It’s like sketching before painting.
Conclusion
So, is injection molding worth it for prototyping in electronics development? It’s not a slam dunk, but it’s not a hard pass either. If you need precision, production-like materials, and a decent batch size—say, 50+ units—it’s a powerhouse. The upfront cost and time sting, sure, but the payoff in reliability can be huge. For quick one-offs or tight budgets, though, stick to 3D printing or casting.
As designers and deciders, it’s about matching the tool to the job. Weigh your goals, crunch the numbers, and maybe chat with a prototyping pro. Have you tried injection molding for your projects? Drop your story in the comments—I’d love to hear how it worked out. For now, I’ll finish this coffee and get back to my own designs. Happy prototyping!