Injection Molding for Outdoor Products: Durability Meets Design
Injection molding isn’t just for shovels and chairs—it’s a goldmine for creating outdoor electronics that marry durability with eye-catching design.
2/25/20256 min read
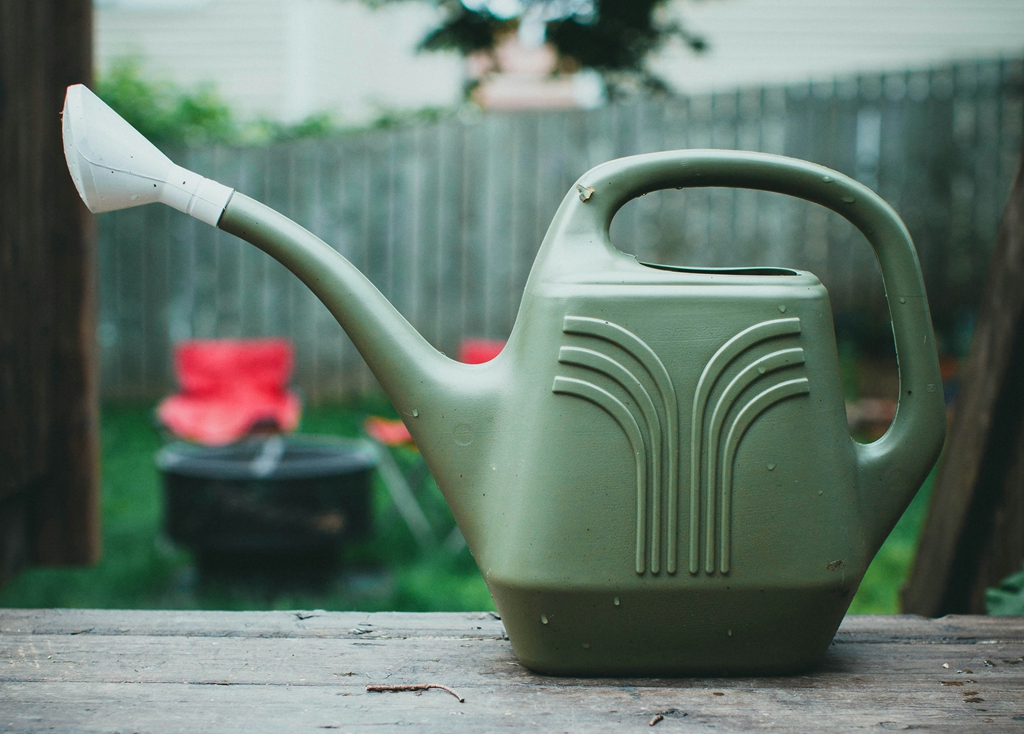
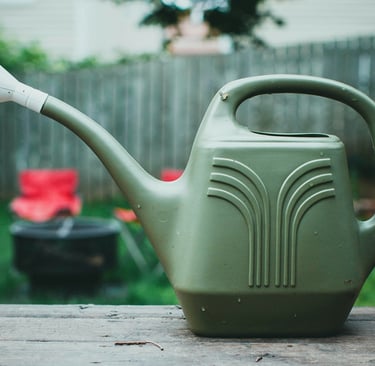
Picture this: It’s a scorching July afternoon, and I’m hauling a watering can across my backyard to rescue my wilting tomatoes. The sun’s relentless, the humidity’s thick, and yet this little green can—light as a feather but tough as nails—keeps doing its job, year after year. No cracks, no fading, just reliable performance. Or take my patio chairs: sleek lines, a pop of color, and they’ve survived countless rainstorms without a hint of rust or wobble. What’s the secret behind these unsung heroes of outdoor living? Injection molding—a process that’s quietly revolutionizing how we design and build products meant to brave the elements.
If you’re a designer or decision-maker in electronics development, you’re probably used to thinking about circuit boards, sleek casings, and cutting-edge tech. But hear me out: the same manufacturing magic that makes durable garden tools and patio furniture can inspire your next weather-resistant gadget. Injection molding isn’t just for shovels and chairs—it’s a goldmine for creating outdoor electronics that marry durability with eye-catching design. Let’s dive into why this process deserves a spot on your radar.
What is Injection Molding, Anyway?
At its core, injection molding is pretty straightforward. You take a material—usually a plastic like ABS or polypropylene—heat it until it’s molten, and shoot it into a precisely crafted mold. Once it cools, you’ve got a part that’s strong, consistent, and ready to take on the world. It’s like baking a cake, but instead of a fluffy sponge, you get a rock-solid component that can handle UV rays, rain, or a clumsy drop onto concrete.
For outdoor products, this process shines because it’s all about precision and toughness. You’re not just making something that works—you’re making something that lasts. And here’s the kicker: the materials you choose can be tweaked to stand up to whatever Mother Nature throws at them. Designers in electronics, think about that rugged outdoor speaker or weatherproof smart garden sensor you’ve been sketching. Injection molding could be the key to bringing it to life.
Durability in Harsh Weather Conditions
Let’s face it—outdoor products have a tough gig. One day they’re baking in the sun, the next they’re soaked in a downpour, and then there’s that random freeze-thaw cycle just to keep things interesting. For garden tools, patio furniture, or even an outdoor security camera, weather resistance isn’t a nice-to-have—it’s non-negotiable.
This is where injection molding flexes its muscles. The secret sauce? Materials. You’ve got options like UV-stabilized ABS that laughs in the face of sunlight, or polypropylene that shrugs off moisture like it’s no big deal. I’ve seen garden shovels made this way—light enough to wield without breaking a sweat, but sturdy enough to dig through rocky soil season after season. No rust, no splintering, just pure reliability.
Patio furniture’s another great example. My neighbor’s got this injection-molded table that’s been sitting outside for years—through thunderstorms, blazing summers, and even a freak hailstorm. It still looks as good as the day he bought it, no fading or warping. Compare that to the rusty metal chairs I used to have, and it’s night and day.
For you electronics folks, think about enclosures for outdoor devices. A weatherproof smart sprinkler controller needs a shell that can handle the elements without cracking or letting water sneak in. Injection molding lets you use reinforced polymers that seal tight and stand firm, keeping your circuitry safe while the rain pours down.
Design Flexibility for Outdoor Aesthetics
Now, let’s talk about the fun part—design. Durability’s great, but nobody wants a clunky, ugly tool or a patio set that looks like it belongs in a junkyard. Injection molding doesn’t just make things tough—it makes them beautiful. The process lets you craft intricate shapes, smooth curves, and finishes that feel premium, all while keeping production practical.
Take garden tools. Ever held a pair of pruning shears with an ergonomic handle that fits your hand just right? That’s injection molding at work. Designers can tweak the mold to add grip textures or subtle contours, turning a basic tool into something you actually enjoy using. I’ve got a hose nozzle like that—lightweight, with a comfy grip that makes watering the garden feel less like a chore.
Patio furniture takes it up a notch. You can mold chairs with flowing lines or tables with a faux-wood texture that screams sophistication. And colors? You’re not stuck with boring beige or gray—think vibrant reds, cool blues, or earthy greens that tie into outdoor trends. For electronics designers, this is huge. Imagine a sleek, colorful outdoor speaker that blends into a patio vibe, or a smart bird feeder with a modern, molded casing that homeowners won’t hide away.
The best part? Customization doesn’t slow you down. Once the mold’s set, you can pump out thousands of identical parts, each one flawless. It’s a designer’s dream—freedom to get creative without sacrificing scalability.
Real-World Applications
Let’s get concrete for a sec. Garden tools are a no-brainer—think lightweight watering cans that don’t crack when you accidentally drop them, or pruning shears with handles that won’t snap mid-cut. I’ve got a buddy who swears by his injection-molded trowel; he says it’s outlasted every metal one he’s ever owned, and it’s easier on his wrists to boot.
Patio furniture’s where the magic really shines. Stackable chairs that don’t wobble, tables with drainage built into the design—it’s the little details that make a difference. I saw a set at a local café once: bright yellow, molded curves, and tough enough to handle daily use by clumsy customers. Years later, they still looked brand new.
Now, pivot to electronics. Outdoor smart devices are exploding—think weather stations, security cams, or even solar-powered chargers. Injection molding gives you casings that protect the guts of your tech while looking sharp. I’ve seen a smart garden sensor with a molded shell that’s survived two summers in my yard—no leaks, no fading, just steady data on my phone.
And it’s not just tools or furniture. Playground slides, outdoor storage bins, even kayak paddles—anything that lives outside can benefit. For decision-makers in electronics, this is your cue to think bigger. That next rugged IoT device? Injection molding could be the ticket.
Advantages Over Other Manufacturing Methods
So why pick injection molding over, say, metal forging or 3D printing? Let’s break it down. Metal’s tough, sure, but it rusts, it’s heavy, and it’s pricey to shape into anything fancy. I had a metal patio set once—looked great until the first winter, then it was a peeling, creaky mess. Wood’s another option, but good luck keeping it intact without constant maintenance.
3D printing’s cool for prototypes—I’ve tinkered with it myself—but it’s slow and pricey for mass production. Injection molding, though? It’s the sweet spot. Once your mold’s ready, you can churn out parts fast and cheap. The upfront cost of the mold pays off when you’re making thousands of units, and the quality’s unmatched.
For weather resistance, it’s a no-contest. Plastics like polycarbonate or nylon beat out untreated metals hands down. And for electronics designers, that precision matters—think tight-fitting enclosures that keep dust and water out, no fiddling with post-production fixes.
I’ve talked to manufacturers who swear by it. One told me he switched from metal to injection-molded parts for his outdoor lighting line—cut costs by 30% and doubled his design options. That’s the kind of win that gets decision-makers nodding in the boardroom.
Wrapping It Up
Here’s the bottom line: injection molding is the unsung hero of outdoor products, blending durability and design in a way that’s tough to beat. From garden tools that shrug off mud and sun to patio furniture that turns your backyard into a showpiece, it delivers. And for you in electronics development, it’s a chance to rethink how you protect and present your tech in the wild.
Next time you’re sketching a weatherproof gadget or pitching a new product line, give injection molding a hard look. It’s not just about surviving the elements—it’s about thriving out there, looking good while doing it. Whether you’re a designer dreaming up the next big thing or a decider crunching the numbers, this process has your back.
So, what’s your next outdoor project? A smart sprinkler that doesn’t flinch at a storm, or a patio speaker that’s as tough as it is stylish? Whatever it is, injection molding might just be the tool that gets it done. From my trusty watering can to your cutting-edge electronics, it’s proof that durability and design don’t have to fight—they can win together.