Injection Molding for Medical Devices: Precision and Standards
Welcome to the world of injection molding for medical devices, where precision meets purpose, and the stakes couldn’t be higher. The global medical device injection molding market is on track to hit billions by 2030, fueled by a relentless demand for parts that are not just accurate but also safe and repeatable.
2/23/20255 min read
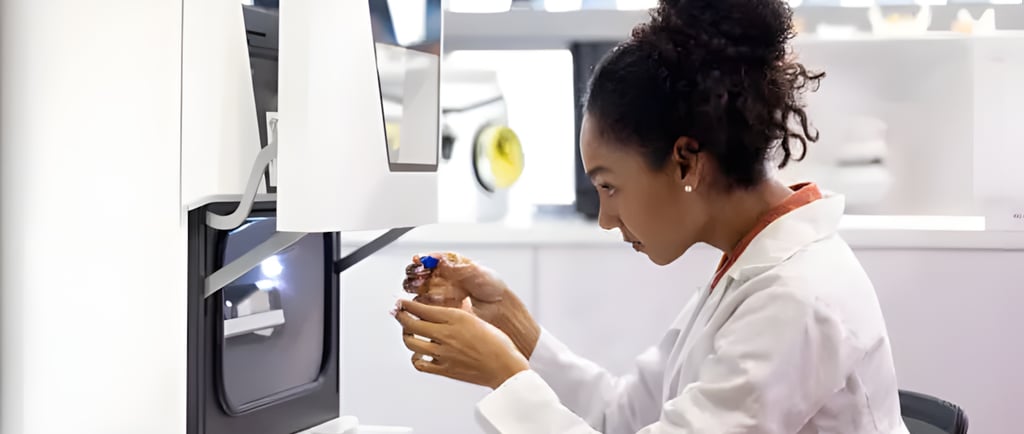
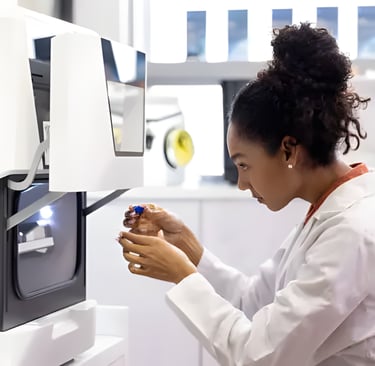
Picture this: a surgeon hovers over a patient, relying on a tiny, impeccably crafted tool to perform a life-saving procedure. That tool—maybe a catheter housing or a diagnostic sensor—didn’t just appear out of thin air. It was born from a process so precise it’s measured in thousandths of an inch, under standards so strict they could make a perfectionist sweat. Welcome to the world of injection molding for medical devices, where precision meets purpose, and the stakes couldn’t be higher.
The global medical device injection molding market is on track to hit billions by 2030, fueled by a relentless demand for parts that are not just accurate but also safe and repeatable. For designers and decision-makers in electronics development, this isn’t just a manufacturing method—it’s a lifeline to innovation. Let’s dive into why injection molding is the unsung hero of medical tech, how it meets sky-high standards, and what you need to know to make it work for your next project.
Why Injection Molding is a Designer’s Best Friend
If you’ve ever sketched out a circuit-laden housing or a microfluidic chip, you know the headache of turning a brilliant idea into a physical reality. Injection molding takes that sketch and makes it real by forcing molten material—think medical-grade plastics like PEEK or polycarbonate—into a mold under high pressure. The result? Parts so consistent you’d swear they were cloned.
Why does this matter to you? Precision, for one. We’re talking tolerances down to ±0.001 inches, perfect for the intricate components you’re dreaming up—like a sensor casing that needs to fit just right with a PCB. Then there’s scalability. Once your mold is dialed in, you can churn out thousands (or millions) of parts without losing that pristine quality. And the materials? They’re a playground for creativity—biocompatible, durable, even flexible if you’re working with silicone for wearables.
Take a syringe, for example. That smooth barrel and plunger aren’t just plastic tubes; they’re injection-molded marvels designed to deliver exact doses every time. Or consider implantable defibrillator housings—tiny, tough, and packed with electronics. Injection molding makes it happen, and it’s why you should care.
The High-Value Niche: Where Electronics Meet Life-or-Death Stakes
Here’s where it gets juicy: the niche that keeps me up at night (in a good way). Think implantable devices, microfluidics for diagnostics, or tools for minimally invasive surgery. These aren’t your run-of-the-mill gadgets—they’re the heavy hitters where electronics and medical precision collide. A pacemaker’s casing needs to shield sensitive circuits while surviving years inside a chest. A diagnostic chip might rely on channels smaller than a hair to analyze blood samples. These are the projects that make your palms sweaty and your designs legendary.
The catch? There’s no room for error. A defect in a consumer gadget might mean a warranty claim; in a medical device, it could mean a life. That’s why this niche is high-value—it’s high-stakes. You’re not just designing for function; you’re designing for trust. And injection molding is your partner in crime, tackling tiny geometries and embedding electronics without breaking a sweat.
Regulatory Standards: The Rulebook You Can’t Ignore
Now, let’s talk about the elephant in the room: regulations. If you’ve ever navigated the FDA’s maze or pored over ISO standards, you know it’s not for the faint of heart. In the U.S., the FDA splits devices into Class I, II, and III—think everything from tongue depressors to heart valves—and enforces 21 CFR Part 820, the Quality System Regulation. Globally, ISO 13485 is your golden ticket, ensuring your quality management system is up to snuff. And don’t forget ISO 10993, which tests whether your materials play nice with human tissue.
Sound daunting? It is. But injection molding was practically built for this. The process thrives on control—every cycle is tracked, validated, and documented to satisfy the pickiest auditor. Many manufacturers run cleanrooms (think ISO Class 7 or 8) to keep contaminants out, especially for sterile devices. I once toured a facility where the air was so pure you could taste the difference—it’s that serious.
The flip side? Mess this up, and you’re looking at recalls, lawsuits, or worse. I’ve seen companies scramble after skipping a validation step—don’t be that team. Lean on injection molding’s repeatability, and you’ve got a head start on compliance.
Quality Control: Where Precision Becomes Personal
Let’s get practical. You’ve got a design—say, a housing for a wearable glucose monitor. It’s sleek, it’s smart, and it’s got electronics galore. How do you ensure every unit off the line is flawless?
It starts with Design for Manufacturability (DfM). I learned this the hard way years ago when a prototype’s sharp corners caused mold flow issues—hours wasted. Work with your molding team early to tweak wall thicknesses or add draft angles; it’ll save you headaches later. Then there’s the mold itself. Steel molds cost more upfront but last forever—perfect for high-volume runs. Aluminum’s cheaper but wears out faster; pick your poison based on your timeline.
During production, it’s all about vigilance. Modern machines use sensors to catch defects in real time—think pressure spikes or temperature dips. I’ve watched operators tweak settings mid-run like maestros, ensuring every part hits spec. Post-production, you’re testing everything: dimensions, sterilization resistance, even how it holds up under stress. One company I know caught a batch of warped casings with a laser scanner—saved them from a disaster.
Here’s a real nugget: a friend in the industry once oversaw a cardiac monitor project. Their molding partner used in-line imaging to spot micro-cracks invisible to the eye. That’s the kind of obsessive quality that keeps patients safe—and your reputation intact.
Innovations That’ll Make Your Jaw Drop
The tech keeps getting better, and it’s a goldmine for electronics folks. New materials like bioresorbable polymers (think dissolving stents) or antimicrobial coatings (goodbye, infections) are game-changers. Multi-shot molding lets you combine hard and soft plastics in one part—imagine a rigid base with a grippy overlay, all in a single cycle. And micro-molding? It’s crafting parts so small you need a magnifying glass, perfect for next-gen sensors.
Sustainability’s creeping in too. I’ve seen firms experiment with recyclable plastics that still meet biocompatibility—tricky, but doable. Looking ahead, AI’s starting to optimize mold designs, cutting waste and time. Pair that with 3D-printed prototypes, and you’ve got a workflow that’s fast and fierce.
Challenges and Solutions: Real Talk
Let’s not sugarcoat it—there are hurdles. Cost is a big one. High-quality molds and cleanroom setups aren’t cheap, and regulatory hoops add to the bill. But here’s the fix: automate where you can. Robots don’t tire, and they don’t miss specs. Plus, a durable mold pays off over millions of parts—think long-term.
Material choice is another beast. You need strength, biocompatibility, and maybe heat resistance for sterilization. I’ve watched teams agonize over PEEK versus polypropylene—get a material scientist on speed dial and test relentlessly. Time’s the third kicker. Clients want it yesterday, but validation takes weeks. Streamline by partnering with a molding pro who’s been around the block—they’ll know the shortcuts that don’t cut corners.
Wrapping It Up: Your Next Move
So, where does this leave you? Injection molding isn’t just a process—it’s your ticket to turning wild ideas into medical miracles. It delivers the precision your electronics designs demand, scales with your ambitions, and bends over backward to meet standards. Whether you’re sketching a wearable packed with circuits or a diagnostic tool that’ll rewrite healthcare, this is your foundation.
My advice? Find a molding partner who lives and breathes regulatory know-how. Quality isn’t negotiable, and neither is trust. As you tweak those CAD files and pitch to the C-suite, remember: every perfect part starts with a perfect process. Injection molding’s got your back—now go build something that saves lives.