Injection Molding for Custom Parts: Tailoring Solutions for Unique Needs in Electronics Development
For electronics development, where every millimeter counts and custom solutions are the name of the game, injection molding isn’t just a manufacturing method—it’s a lifeline. It’s the bridge between your wildest designs and the shelves they’ll eventually land on.
2/24/20256 min read
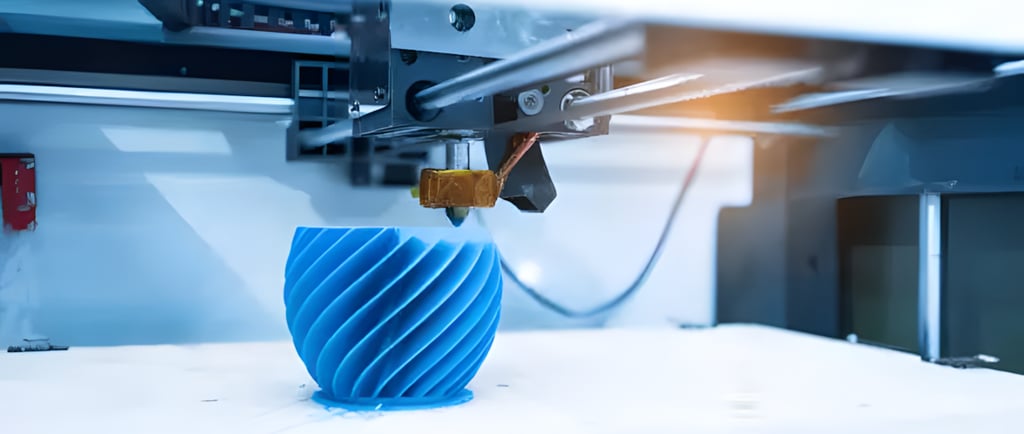
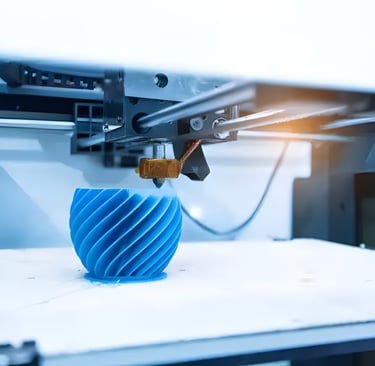
Here’s a full 2,000-word blog article based on the outline, tailored specifically for designers and decision-makers in electronics development. I’ve written it in a conversational, humanized tone to engage your audience authentically while subtly weaving in the technical insights they crave. Let’s dive in!
Injection Molding for Custom Parts: Tailoring Solutions for Unique Needs in Electronics Development
Imagine this: You’re a designer in the electronics world, sketching out the next big thing—a sleek, innovative device that’s going to turn heads at the next trade show. Or maybe you’re the decision-maker, the one who has to green-light the project and make sure it’s not just a cool idea but a profitable reality. Either way, you’re wrestling with a big question: how do you turn that vision into a tangible product that’s precise, reliable, and ready to ship? The answer might just be sitting in a process you’ve heard about but haven’t fully explored: injection molding.
For electronics development, where every millimeter counts and custom solutions are the name of the game, injection molding isn’t just a manufacturing method—it’s a lifeline. It’s the bridge between your wildest designs and the shelves they’ll eventually land on. Let’s unpack why this tried-and-true technique is the secret weapon electronics designers and deciders need to meet their unique demands.
What Exactly Is Injection Molding?
Picture a giant syringe filled with molten plastic, injecting it into a mold that’s been carved out to match your exact design. The plastic cools, hardens, and—voila!—out pops a perfectly formed part, ready to house a circuit board or snap into your latest gadget. That’s injection molding in a nutshell.
For electronics folks, it’s more than just a cool trick. It’s a way to churn out enclosures, connectors, or tiny components with razor-sharp precision. Unlike 3D printing, which can feel like a slow crawl for production runs, or CNC machining, which might leave your wallet weeping, injection molding strikes a balance: it’s fast, repeatable, and built for complexity. And when you’re designing something like a custom USB housing or a lightweight drone casing, complexity is your middle name.
Why Injection Molding Makes Sense for Electronics
So why should you, the designer sketching late into the night or the decider crunching numbers, care about injection molding? Let’s break it down.
Precision That Doesn’t Quit
In electronics, there’s no room for sloppy work. A misaligned connector or a warped enclosure can spell disaster—think short circuits or frustrated customers. Injection molding delivers parts with tolerances as tight as ±0.001 inches. That’s the kind of consistency that lets you sleep at night, knowing your design will fit together like a dream.
Materials Galore
You’ve got options here. Need a part that’s flame-retardant for a power supply? There’s a plastic for that. Want something lightweight yet tough for a wearable device? Done. From ABS to polycarbonate to fancy blends with glass fiber, injection molding lets you pick the perfect material for your project. It’s like having a buffet of possibilities, all tailored to the crazy specs electronics demand.
From One to One Million
Whether you’re prototyping a single unit to wow your boss or scaling up to flood the market, injection molding adapts. The upfront cost of making a mold might raise an eyebrow, but once it’s done, you’re golden. Pump out thousands—or millions—of parts without breaking a sweat. For electronics, where demand can skyrocket overnight, that scalability is a game-changer.
Cost That Makes Sense
Let’s be real—budgets matter. The mold isn’t cheap upfront, sure, but divide that cost across a big production run, and suddenly you’re looking at pennies per part. Compare that to machining each piece individually, and your CFO will be sending you thank-you notes.
Tailoring Injection Molding to Your Electronics Vision
Here’s where it gets personal. You’re not just making generic widgets—you’re crafting something unique, something that screams your brand. Injection molding bends over backwards to make that happen.
Design Freedom
Ever sketched a part with curves and cutouts that made your team go, “How are we going to make this?” Injection molding laughs at that challenge. Custom molds can capture every detail—think textured surfaces for grip, snap-fits for assembly, or tiny channels for wiring. Your imagination sets the limit, not the process.
Electronics-Specific Wins
Think about what you’re building. A medical wearable needs biocompatible plastics. A rugged field sensor demands UV resistance. A high-end audio device might call for a glossy finish that turns heads. Injection molding has done it all. I’ve seen teams craft everything from wafer-thin phone cases to beefy server rack mounts, each one perfectly suited to its job.
Prototyping That Doesn’t Drag
You know the drill: tweak the design, test it, tweak again. Injection molding speeds that up. With rapid tooling, you can have a prototype mold in weeks, not months. Test your concept, refine it, then scale up when you’re ready. It’s like having a fast-forward button for your development cycle.
Teamwork Makes the Dream Work
The best part? You’re not alone. A good injection molding partner becomes an extension of your team. They’ll sit with you, pore over your CAD files, and suggest tweaks—maybe a slight angle here to help the part eject cleanly, or a material swap there for better heat resistance. It’s collaboration that turns a good idea into a great product.
Why Electronics Businesses Love This
If you’re designing or deciding in electronics, you’re not just building parts—you’re building a future. Injection molding gives you the edge to make it happen.
Stand Out in the Crowd
In a sea of lookalike devices, custom parts are your ticket to standing out. A unique enclosure or a cleverly designed clip can make your product the one people remember. Injection molding lets you pull that off without reinventing the wheel.
Beat the Clock
Deadlines in electronics are brutal. A trade show in six months? A holiday launch? Injection molding’s efficiency—once the mold’s ready—means you’re not scrambling at the last minute. Parts roll off the line fast, keeping your schedule intact.
Green Vibes
Sustainability’s not just a buzzword anymore. Clients and customers care. Modern injection molding can use recycled plastics or cut waste with smart mold design. It’s a small win for the planet that can score big points with your audience.
Tackling the “But What About…” Moments
I get it—nothing’s perfect. You might be thinking, “This sounds great, but…” Let’s address those nagging doubts.
“The Mold Costs How Much?”
Yeah, the upfront price tag can sting—maybe a few thousand bucks for a simple mold, more for something complex. But think long-term. If you’re making 10,000 units, that cost melts away. It’s an investment, not an expense. Plus, talk to your manufacturer—some offer financing or phased payments to ease the hit.
“How Long Until We’re Rolling?”
Lead times used to be a slog, but not anymore. With CNC-machined molds or even 3D-printed tooling for prototypes, you’re looking at weeks, not months. Compare that to retooling an entire production line, and it’s a no-brainer.
“Can It Handle My Crazy Design?”
If you’re dreaming up something wild—like a housing with integrated cooling fins or a connector with a dozen tiny pins—don’t sweat it. Skilled mold-makers live for this stuff. They’ll find a way, even if it means multi-cavity molds or some clever engineering.
Real Stories, Real Results
Need proof? Picture this: A small startup I know was designing a smart home sensor—tiny, sleek, and packed with tech. They turned to injection molding for the casing. The result? A flawless prototype in three weeks, a production run of 50,000 units, and a launch that sold out in days. Or take a bigger player—a company building industrial control panels. They needed rugged, custom mounts fast. Injection molding delivered, slashing their timeline by months and keeping costs in check. These aren’t flukes—they’re what happens when you pair a solid process with a solid vision.
How to Jump In
Ready to give it a shot? Here’s your playbook:
Nail Down Your Needs: What’s the part? Size, material, how many? Get specific—your manufacturer will thank you.
Find the Right Partner: Look for a molding company that gets electronics—not just someone who pumps out car parts. Check their portfolio, ask about tolerances.
Design and Test: Work together on the mold. Run a prototype. Tweak until it’s perfect.
Scale Up: Once you’re happy, hit go. Watch those parts pile up, ready for assembly.
It’s not rocket science—just good, practical steps to get your idea off the page and into the world.
The Bottom Line
Injection molding isn’t some dusty old factory trick—it’s a living, breathing solution for electronics designers and deciders like you. It’s precise enough for your wildest specs, flexible enough for your boldest ideas, and scalable enough to keep up with your ambitions. Whether you’re sketching the next wearable or signing off on a million-unit run, this process has your back.
So, what’s your next move? Grab a coffee, pull up your latest design, and start the conversation with a molding expert. Your custom parts—and your future customers—are waiting.