Injection Molding for Consumer Electronics: Meeting High-Demand Standards
We’re unpacking how injection molding shapes the consumer electronics landscape, from phone cases to keyboards to that smartwatch on your wrist. We’ll explore why it’s the go-to for precision and scale, the challenges it throws at you, and the innovations keeping it ahead of the curve.
2/23/20256 min read
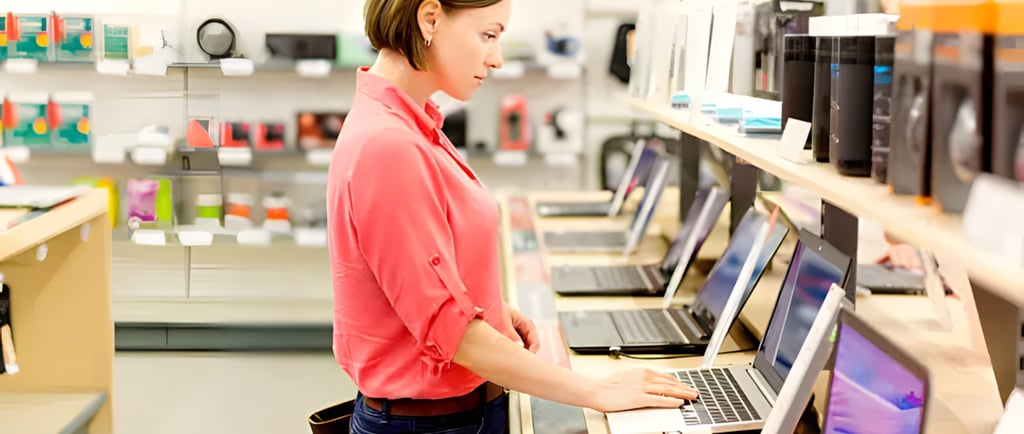
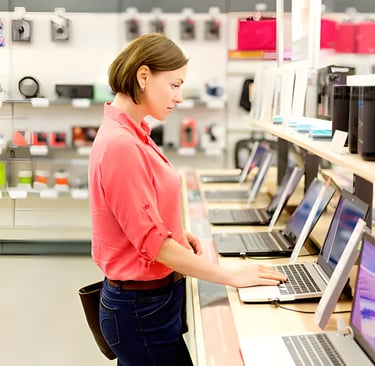
Picture this: you’re holding your brand-new smartphone, admiring how the case fits like a glove—sleek, lightweight, with every button cutout perfectly aligned. Or maybe you’re typing away on a keyboard, the keys clicking just right under your fingers, each one molded to perfection. Ever stopped to wonder how these everyday gadgets come to life, millions of times over, without a hitch? The answer lies in a manufacturing hero you might not think about often: injection molding. For designers and decision-makers in the electronics world, this process isn’t just a production method—it’s the backbone of delivering high-quality, high-demand products that consumers can’t get enough of.
In this deep dive, we’re unpacking how injection molding shapes the consumer electronics landscape, from phone cases to keyboards to that smartwatch on your wrist. We’ll explore why it’s the go-to for precision and scale, the challenges it throws at you, and the innovations keeping it ahead of the curve. Whether you’re sketching the next big gadget or signing off on production budgets, here’s why injection molding should be on your radar.
What is Injection Molding, Anyway?
If you’re new to the game—or just need a refresher—think of injection molding like baking with a high-tech twist. You’ve got a mold, a souped-up oven (the machine), and some molten plastic instead of dough. The process is simple in theory: heat the plastic until it’s liquid, inject it into a precision-crafted mold under pressure, let it cool, and pop out a finished part. But don’t let the simplicity fool you—this is engineering artistry at its finest.
For consumer electronics, injection molding is the sweet spot where design dreams meet mass-production reality. It’s how you get those intricate shapes and tiny details—think the raised logo on a phone case or the smooth curve of a keycap—without breaking the bank or the timeline. And when you’re designing gadgets that need to fly off the shelves, this process delivers every time.
The Role of Injection Molding in Your Favorite Gadgets
Let’s get specific. You’re a designer sketching a phone case or a decision-maker greenlighting a keyboard line—here’s how injection molding makes your vision tangible.
Phone Cases: Style Meets Substance
Phone cases are the poster child for injection molding’s prowess. You’ve got a consumer base demanding slim profiles, grippy textures, and flawless port alignments—all while keeping costs low enough for a $20 price tag. Injection molding nails it. The process churns out cases with wall thicknesses as thin as 0.5mm, intricate patterns for grip, and cutouts so precise you’d think they were laser-etched by hand (spoiler: they’re not).
I remember a late-night design session with a colleague years back, brainstorming a case for a flagship phone. We wanted a matte finish that didn’t scratch and a lip just high enough to protect the screen. Injection molding let us tweak the mold, test materials like polycarbonate, and scale up production once the client gave the nod. That’s the flexibility you need when deadlines loom and consumers are picky.
Keyboards: Precision Under Pressure
Now, keyboards—those unsung heroes of productivity. Whether it’s a mechanical beast for gamers or a chic laptop setup, every keycap and frame owes its life to injection molding. You’re dealing with tolerances tighter than a drum—sometimes down to 0.01mm—to ensure keys don’t wobble or wear out after a million clicks. The process delivers uniformity across thousands of units, so the “A” key feels the same whether it’s on a keyboard in Tokyo or Texas.
A friend in product development once told me about the headache of designing a backlit keyboard. The keycaps needed to be translucent in just the right spots for the LEDs to shine through, all while keeping the structural integrity. Injection molding, with its ability to handle multi-material molds, turned that headache into a win. It’s the kind of reliability you lean on when quality can’t falter.
Beyond the Basics: Earbuds, Watches, and More
Don’t stop at phones and keyboards. Think about the housing for your wireless earbuds—tiny, ergonomic, and tough enough to survive a drop. Or the smartwatch band that’s flexible yet durable, molded to fit wrists of all sizes. Injection molding’s versatility shines here, adapting to small-batch prototypes or full-scale runs for the next viral gadget. It’s like having a Swiss Army knife in your manufacturing toolkit.
How Injection Molding Meets High-Demand Standards
So why does injection molding dominate consumer electronics? It’s not just about making parts—it’s about making them right, every time, at the scale your market demands. Here’s the breakdown.
Precision and Consistency: No Room for Error
When you’re designing a phone case or a keyboard, “close enough” doesn’t cut it. A misaligned port or a warped key ruins the user experience—and your reputation. Injection molding’s magic lies in its molds—steel or aluminum masterpieces machined to exact specs. Once you’ve got the mold dialed in, every part comes out identical, down to the micron. That’s peace of mind when you’re shipping millions of units.
Scalability: From One to One Million
Consumer electronics isn’t a boutique business. You’re not handcrafting ten phone cases—you’re flooding stores with them. Injection molding scales like a dream. A single mold can pump out thousands of parts a day, and multi-cavity molds crank that number even higher. I’ve seen production lines where a single shift could outfit an entire product launch. That’s the kind of firepower you need when pre-orders are stacking up.
Material Flexibility: The Right Stuff
Plastics aren’t one-size-fits-all. You might want ABS for a keyboard frame’s toughness, polycarbonate for a phone case’s clarity, or a TPU blend for a watch band’s stretch. Injection molding lets you pick the perfect material, tweak it with additives for strength or color, and test it in real-world conditions. It’s like being a chef with an endless pantry—except you’re cooking up gadgets, not dinner.
Cost-Effectiveness: Big Wins, Smart Spends
Let’s talk money. Molds aren’t cheap—think five or six figures for a complex design. But once that upfront cost is covered, the per-unit price drops to pennies. For high-volume products like phone cases or keyboard components, that’s a no-brainer. I’ve sat in meetings where execs balked at the initial quote, only to cheer when the long-term math worked out. It’s an investment that pays off when the orders roll in.
Speed to Market: Beat the Clock
In electronics, timing is everything. A competitor beats you to the shelf, and you’re playing catch-up. Injection molding’s fast cycle times—sometimes under a minute per part—keep you in the race. Pair that with rapid prototyping (more on that later), and you’re iterating designs while others are still sketching. It’s the edge you need in a cutthroat industry.
Challenges and Innovations: Staying Ahead
Nothing’s perfect, right? Injection molding’s got its hurdles, but the industry’s not sitting still. Here’s what you’re up against—and how to tackle it.
The Challenges
Upfront Costs: That mold price tag can sting, especially for startups or small runs. It’s a hurdle if you’re testing the waters with a new design.
Design Complexity: Thin walls, tiny features, sharp corners—these can lead to defects like warping or sink marks if the mold or material isn’t spot-on. I’ve seen late-night redesigns to fix a stubborn flaw.
Sustainability: Plastic waste is the elephant in the room. Consumers and regulators are pushing for greener options, and traditional molding can feel out of step.
The Innovations
Mold Design Advances: Multi-cavity molds and hot-runner systems boost efficiency, cutting waste and speeding up cycles. It’s like upgrading from a single-lane road to a highway.
Sustainable Materials: Recycled plastics and bio-based resins are gaining traction. I’ve worked with teams experimenting with these—they’re not perfect yet, but they’re close.
Prototyping Power: Pair injection molding with 3D-printed molds for quick, low-cost prototypes. It’s a game-changer for iterating designs without breaking the bank.
Real-World Impact: From Vision to Victory
Let’s ground this in reality. Imagine you’re launching a phone case for the latest 5G blockbuster. Injection molding turns your CAD file into a million units, each one sporting a premium finish and a price consumers love. Or picture a gaming keyboard hitting the market—every keycap molded for perfect feedback, scaling to meet holiday demand. These aren’t hypotheticals; they’re the wins designers and decision-makers like you pull off daily.
The consumer payoff? Affordable gadgets that feel like luxury. The industry trend? A relentless push for more—more units, more features, more sustainability. Injection molding keeps pace, evolving with every product cycle.
Wrapping It Up
Injection molding isn’t just a process—it’s your partner in the consumer electronics grind. From phone cases that hug every curve to keyboards that click just right, it delivers the precision, scale, and speed you need to thrive. Sure, it’s got challenges, but the innovations bubbling up mean it’s not going anywhere soon.
So next time you’re sketching a gadget or crunching production numbers, give a nod to injection molding. It’s the unsung hero making your ideas real—and keeping consumers coming back for more. Got thoughts on this? Drop them below—I’d love to hear how you’re navigating this space.