Injection Molding Design Tips: Avoiding Common Mistakes for Electronics Development
Injection molding is the backbone of manufacturing plastic parts for electronics—think enclosures, connectors, and tiny clips that hold circuit boards in place. It’s fast, cost-effective, and scalable, but here’s the catch: the process doesn’t forgive sloppy design.
2/22/20256 min read
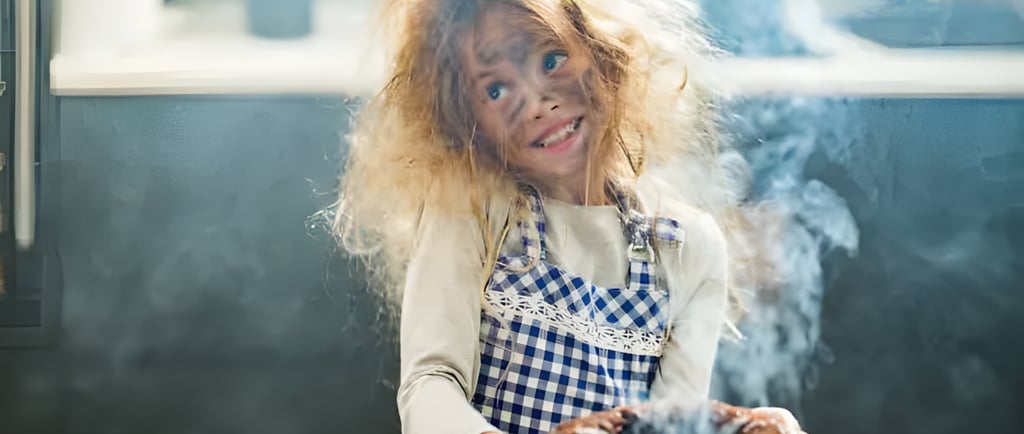
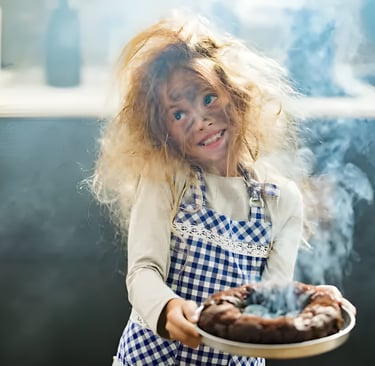
Picture this: You’ve spent weeks perfecting a sleek new housing for your latest electronic gadget—a cutting-edge wearable, maybe, or a compact IoT device. The renders look flawless, the team’s buzzing with excitement, and you’re ready to send it off to production. Then, the first batch comes back warped, with sink marks glaring at you like a bad review. Suddenly, you’re staring down delays, budget overruns, and a whole lot of frustration. Sound familiar? If you’re a designer or decision-maker in electronics development, you’ve probably felt this sting at least once. The culprit? Injection molding design gone wrong.
Injection molding is the backbone of manufacturing plastic parts for electronics—think enclosures, connectors, and tiny clips that hold circuit boards in place. It’s fast, cost-effective, and scalable, but here’s the catch: the process doesn’t forgive sloppy design. In fact, industry stats suggest over 70% of molding defects trace back to design flaws. That’s a sobering number when you’re racing to beat competitors to market. But don’t worry—I’ve got your back. In this article, we’ll walk through six essential injection molding design tips to help you sidestep the most common mistakes. Whether you’re sketching the next big thing or signing off on production, these pointers will save you headaches, cash, and maybe even a few gray hairs.
Understanding Injection Molding Basics
First things first—what’s injection molding all about? Imagine it like baking a cake, but instead of batter, you’re using molten plastic. The material gets heated until it’s gooey, injected into a mold under pressure, cooled until it hardens, and then popped out as a finished part. Simple, right? Well, not quite. In electronics, where tolerances are tight and aesthetics matter, every detail in your design affects how that plastic flows, cools, and behaves.
Poor design can lead to a laundry list of woes: parts that warp like a funhouse mirror, sink marks that scream “cheap,” or incomplete fills that leave you with half a housing. For designers and deciders in electronics, these aren’t just cosmetic issues—they can compromise functionality, like sealing out moisture or securing delicate components. So, let’s roll up our sleeves and tackle the big mistakes—and how to avoid them.
Tip 1: Optimize Wall Thickness
If there’s one thing I’ve learned from years of watching designs go from screen to reality, it’s that wall thickness is the unsung hero of injection molding. Get it wrong, and you’re in for a world of hurt. Too thick, and your part takes forever to cool, risking warping or sink marks where the plastic shrinks unevenly. Too thin, and it might not fill properly or crack under stress—bad news for an enclosure protecting sensitive electronics.
Here’s the sweet spot: aim for uniform wall thickness, typically between 1-3 mm, depending on your material. For something like ABS, common in electronics housings, 1.5-2 mm often works great. Avoid sudden jumps—say, a 3 mm base thinning to 0.5 mm at the edge. That’s a recipe for stress points and flow issues. Instead, use smooth transitions. Think of it like easing into a turn on a bike, not jerking the handlebars.
I once worked with a team designing a smart thermostat housing. They insisted on thick walls for “durability,” but the first run came back with sink marks so deep you could see them from across the room. We trimmed the thickness, added some ribs (more on those later), and voilà—problem solved. Check your material’s spec sheet—polycarbonate might handle slightly thicker walls than polypropylene, for instance—and you’ll be golden.
Tip 2: Incorporate Proper Draft Angles
Ever tried pulling a tight-fitting lid off a container and felt that stubborn resistance? That’s what happens when you skip draft angles in injection molding. Without a slight taper on vertical walls, your part clings to the mold like a kid hugging a teddy bear, making ejection a nightmare. Scratched surfaces, damaged parts, or even a worn-out mold—none of these are fun when you’re on a deadline.
The fix is simple: add a draft angle of 1-2° per side. For textured surfaces, like a grippy finish on a remote control, you might need a bit more—say, 3°—to let it slide out cleanly. I remember a junior designer once shrugging this off, saying, “It’s just a tiny connector, who’ll notice?” Turns out, the mold shop noticed when they had to pry out every piece by hand. A quick tweak to the CAD file, and we were back on track.
Talk to your mold maker early—they’ll tell you if your part’s depth or complexity calls for adjustments. It’s a small change that pays off big in production.
Tip 3: Avoid Undercuts Where Possible
Undercuts are the sneaky gremlins of injection molding. Picture a snap-fit tab or a recessed button on your design—looks cool, right? But if that feature traps the part in the mold, you’ve got an undercut. To free it, you’ll need side actions or a multi-part mold, which jacks up costs and complexity faster than you can say “budget meeting.”
The smarter move? Redesign to eliminate undercuts. Can that snap-fit angle outward instead of inward? Maybe a slight reposition avoids the issue entirely. If you can’t dodge it—like for a clip securing a battery—use sliders or lifters, but sparingly. I once saw a team sink thousands into a fancy mold for an undercut-heavy prototype, only to realize a simpler tweak would’ve worked just as well. Run your design through a CAD ejection simulation—it’s like a crystal ball for spotting trouble.
Tip 4: Pay Attention to Ribs and Bosses
Ribs and bosses are your best friends for adding strength without bulk—crucial for electronics parts like circuit board mounts or reinforced enclosures. But mess them up, and they’re a fast track to sink marks or weak spots. I’ve seen it happen: a designer beefs up ribs to “make it sturdy,” and the surface ends up dimpled like a golf ball.
Keep ribs thin—50-60% of your wall thickness is the magic ratio. So, for a 2 mm wall, aim for 1-1.2 mm ribs. Add gussets to bosses (those little posts for screws) instead of making them chunky cylinders. It’s like giving them a tripod to stand on—stable, not wasteful. A buddy of mine once ignored this on a speaker housing, and the bosses cracked under screw torque. A quick gusset fix, and it held like a champ. Stress-test your design in simulation software—it’ll show you where to reinforce without overdoing it.
Tip 5: Select the Right Material
Materials can make or break your design—literally. Pick the wrong one, and you’re looking at shrinkage that throws off tolerances, cracking under heat, or flow issues that leave gaps in your part. For electronics, you’re often juggling needs like impact resistance (hello, ABS), heat deflection (polycarbonate’s your guy), or flexibility (think nylon for clips).
The mistake I see most? Designers locking in a material without double-checking how it behaves in the mold. ABS shrinks about 0.5-0.8%, while polypropylene might hit 1-2%. If your tight-fitting PCB mount doesn’t account for that, it won’t fit. I once had a client insist on a glossy polycarbonate for a sleek look, but it cracked under assembly stress. Switched to a tougher blend, adjusted the design, and crisis averted.
Chat with your supplier—they’ll give you the nitty-gritty on flow rates and cooling times. It’s not just about function; it’s about moldability too.
Tip 6: Design for Proper Gate Placement
Gates are where the plastic enters the mold, and they’re like the front door to your part. Ignore them, and you’ll end up with flow lines on your shiny enclosure or weak spots where the plastic didn’t knit together. For electronics, where looks and strength both matter, that’s a double whammy.
Place gates in low-visibility areas—like the inside of a housing—or spots with low mechanical stress. Flow simulation tools are a lifesaver here, showing you how the plastic will spread. I once worked on a remote casing where the gate sat right on the front panel—talk about an eyesore. Moved it to the edge, and it blended right in. Your molder can weigh in too—sometimes they’ll suggest a tweak that balances beauty and brawn.
Tools and Techniques to Stay Ahead
So, how do you catch these mistakes before they bite? Lean on CAD software with design-for-manufacturability (DFM) plugins—they’ll flag wall thickness issues or tricky undercuts in minutes. Prototyping’s another ace up your sleeve—3D print a mock-up or run a soft tool to test fit and finish. And don’t go it alone—loop in your mold maker and manufacturer early. They’ve seen it all and can spot a problem you might miss.
Wrapping It Up
Injection molding doesn’t have to be a minefield. Nail your wall thickness, add those draft angles, dodge undercuts, finesse your ribs and bosses, pick the right material, and mind your gates—and you’ll be churning out parts that look good, work great, and don’t break the bank. As designers and deciders in electronics, you’re shaping the gadgets that define our world. Why not make the process smoother?
Try these tips on your next project—I’d love to hear how it goes. Drop a comment or shoot me a question if you’re stuck. Good design isn’t just about creativity; it’s about making production sing. Now, go build something awesome.