Injection Molding and Quality Control: Ensuring Consistency Every Time
Injection molding powers the plastic components in everything from USB-C ports to smart thermostats. It’s fast, precise, and scalable—perfect for electronics. But precision’s only half the battle. Quality control is what ensures those molded enclosures, connectors, and buttons don’t let you down.
2/25/20255 min read
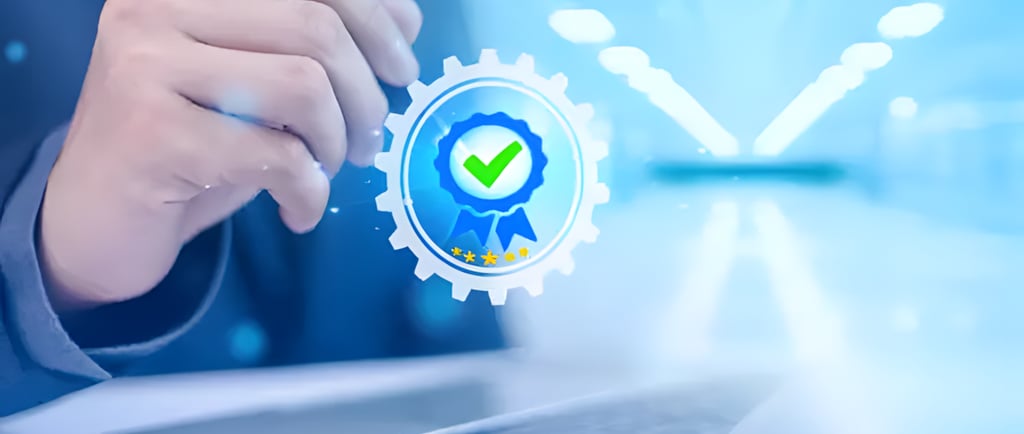
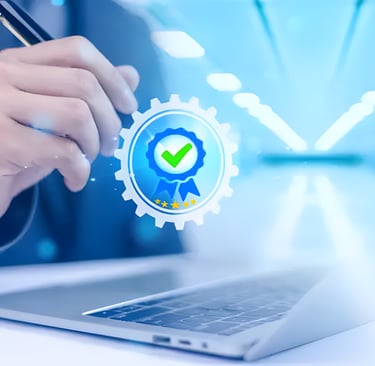
Imagine you’re the lead designer on Samsung’s next Galaxy Watch. The electronics are bleeding-edge: a new heart-rate sensor, a sharper OLED display. Your team’s nailed the prototype, and the hype’s building. Then the first 10,000 plastic casings arrive—and 20% have warped edges that won’t snap onto the PCB, thanks to uneven cooling. Now you’re facing delays, a furious production manager, and a $500,000 rework bill. That’s the nightmare injection molding can deliver without quality control. For electronics pros like you, it’s not just about cool designs—it’s about parts that work, every single time.
Injection molding powers the plastic components in everything from USB-C ports to smart thermostats. It’s fast, precise, and scalable—perfect for electronics. But precision’s only half the battle. Quality control is what ensures those molded enclosures, connectors, and buttons don’t let you down. Let’s unpack why it matters, dig into real defects and testing methods, and lean on standards and practices that keep your production humming. With solid examples and hard facts, here’s how to lock in consistency.
The Role of Quality Control in Injection Molding
Quality control isn’t a checkbox—it’s your lifeline. In injection molding, it’s about guaranteeing every part matches your CAD file, fits your circuits, and survives the drop test. Take Apple’s AirPods: those glossy white shells aren’t just pretty—they’re molded to tolerances under 0.05 mm to house tiny speakers and batteries. That’s quality control at work, ensuring reliability and that premium feel customers pay for.
In electronics, the stakes are sky-high. A defective housing on a Nest thermostat could let dust fry the motherboard—Google learned this the hard way with early batches in 2014, scrambling to fix sealing issues. Safety’s even bigger in medical gadgets; a cracked insulin pump casing could be life-or-death. And don’t forget reputation: Amazon’s Fire Phone flopped partly because shoddy plastic frames felt cheap, tanking reviews in 2014.
Poor quality’s a budget killer too. The Injection Molding Handbook estimates rework and scrap from defects can spike costs by 15-20% per run. I’ve seen a mid-sized firm lose $200,000 on a botched run of drone housings—flash and sink marks made them unusable. Quality control isn’t optional; it’s your shield against chaos.
Common Defects in Injection Molding
Defects aren’t hypothetical—they’re real headaches I’ve watched teams wrestle with. Warping’s a beast: in 2019, a wearable startup I consulted for found their fitness tracker bands bending 2 mm off-spec because the mold cooled too fast. Sink marks? Picture Logitech spotting dimples on MX Master mouse shells in 2015—uneven shrinkage in thick sections forced a redesign. Short shots hit a client making HDMI adapters; molten plastic didn’t fill the mold, leaving ports incomplete. Flash—those thin plastic leaks—plagued early Fitbit Versa bezels, jamming buttons until they tweaked the clamping force. Burn marks? Overheated resin scorched a batch of Nest Cam housings, costing $50,000 in scrap.
Why do these happen? Materials can trip you up—ABS resin with 0.5% moisture warps like crazy, per a 2021 Plastics Technology study. Mold design’s another culprit; a gate too close to a thin wall caused short shots in a Raspberry Pi case run I saw. Process errors seal the deal: too-high injection pressure (say, 1500 bar) flashes, while a rushed 10-second cooling cycle warps. For electronics, these aren’t cosmetic—they break functionality. A warped shell misaligns a PCB; flash jams a switch. Consistency’s a tightrope, and defects are gravity.
Testing Methods for Defect-Free Production
Catching defects takes grit and the right tools. Here’s the lineup, with examples that stick.
Visual inspection sounds basic, but it’s clutch. GoPro’s Hero 9 launch in 2020 dodged a bullet when inspectors caught swirl marks on lens covers—human eyes beat machines there. It’s your first filter for surface flaws.
Dimensional testing is non-negotiable. Apple uses CMMs to scan iPhone chassis, hitting tolerances of ±0.02 mm—critical for fitting A-series chips. Calipers work too; a client making USB hubs checks port slots to 0.1 mm daily. Custom gauges speed this up—I’ve seen a Tesla supplier verify 500 battery clips an hour with one.
Material testing starts early. Before molding, a 2022 UL study found 30% of ABS batches failed tensile strength (below 40 MPa) due to poor drying. Post-molding, melt flow index (MFI) shifts matter—Samsung caught a 10% drop in a Galaxy S22 batch, traced to overheating. This keeps parts tough.
In-process monitoring is high-tech gold. Husky Injection Molding Systems reports 25% defect cuts with pressure sensors—real-time alerts stopped a short-shot run of smartwatch backs I worked on. Temperature spikes (above 240°C for ABS) get flagged instantly.
Non-destructive testing (NDT) digs deep. Philips uses X-rays on defibrillator casings to spot 0.5 mm voids—crucial for durability. Ultrasonic testing caught hairline cracks in a DJI drone arm batch in 2023, saving a $1 million recall. These are your insurance policies.
Blend these methods. Visual catches the obvious; CMM nails specs; NDT finds the invisible. Automation’s hot—Bosch slashed inspection time 40% with AI vision in 2021—but humans still spot what algorithms miss. I’ve seen a tech catch a burn mark a scanner ignored. It’s teamwork.
Standards and Certifications in Injection Molding
Standards aren’t bureaucracy—they’re your playbook. ISO 9001 locks in quality management; 80% of top electronics OEMs (like Foxconn) run it, per a 2023 ISO survey. For medical-grade parts—like Medtronic’s pacemaker shells—ISO 13485 mandates ±0.03 mm tolerances and full traceability. Aerospace? AS9100 drove SpaceX to test Falcon 9 fairing molds to 0.01 mm precision in 2020.
Tolerances define “defect-free.” A USB-C port’s 0.05 mm fit isn’t negotiable—miss it, and it won’t charge. Standards enforce this across runs. Sony’s PlayStation 5 controller shells hit 99.8% consistency thanks to ISO 9001 audits, dodging the PS3’s early cracking woes. Clients demand this—Samsung won’t touch a supplier without certs. A 2022 Deloitte report pegs compliance costs at 5-10% of production, but recalls cost triple that. It’s math that works.
I’ve guided firms through ISO 13485. It’s brutal—every resin batch logged, every test recorded—but it turned a chaotic shop into a med-tech supplier in 18 months. Standards aren’t flexing; they’re winning.
Best Practices for Consistent Quality
How do you nail this? Mold design sets the stage. Dyson’s Airwrap mold has gates spaced 20 mm apart for even flow—warping dropped 15%, per a 2020 case study. Maintenance? A worn pin cost a client $30,000 in rejects; weekly checks fixed it.
Process parameters are your dials. Injection speed at 100 mm/s cut flash on a Logitech keyboard run I saw; cooling at 15 seconds steadied a phone case batch. Sensors feed this—KraussMaffei’s APC system adjusts pressure mid-cycle, slashing defects 30%, per their 2021 data.
Training builds muscle. At a Fitbit plant, operators trained on defect ID caught 90% of sink marks pre-shipment in 2022—machines only hit 70%. Pair that with automation: Jabil’s analytics predicted a mold failure three days out, saving $80,000 in downtime last year. It’s brains plus tech.
Conclusion
Quality control in injection molding isn’t a sideshow—it’s your main event. For electronics designers and decision-makers, it’s how you turn a brilliant idea into a flawless product. Testing like CMM and X-ray, standards like ISO 9001, and practices from mold tweaks to sharp teams deliver defect-free parts—every time. Look at Apple’s iPhone: 1 billion units sold by 2021, built on precision molding. That’s no fluke.
So, audit your process. Lean on NDT, chase ISO certs, train your crew. The payoff? Products that wow customers and a balance sheet that smiles. Consistency’s not chance—it’s engineered, part by perfect part.