Industry 4.0 and Its Influence on Electronics Metal Fabrication
Imagine a manufacturing floor where machines communicate seamlessly, adjust their operations in real-time, and predict failures before they happen. This is not a vision of the distant future—it’s happening now, thanks to Industry 4.0.
2/26/20254 min read
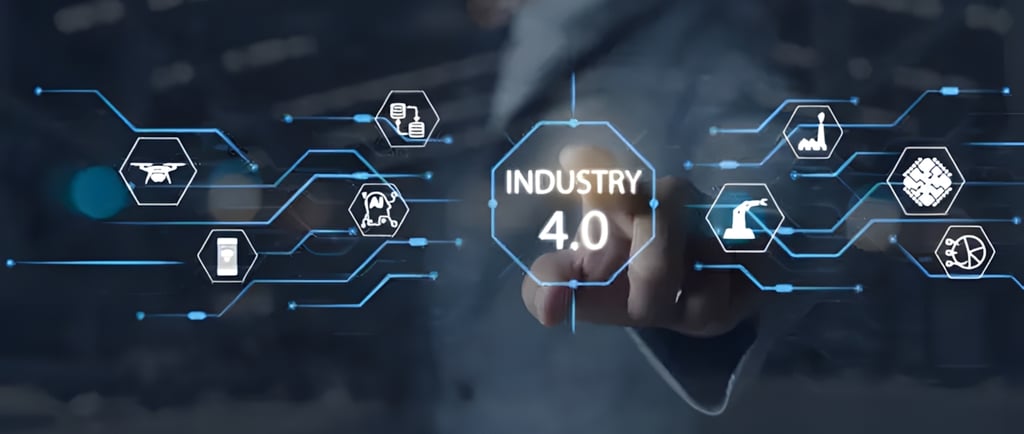
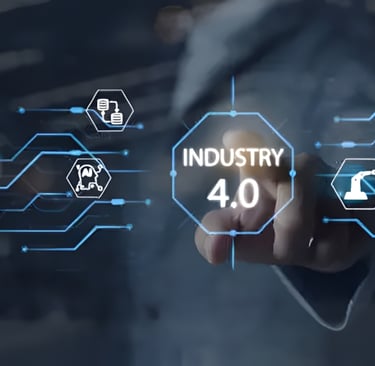
How Smart Technologies and Automation Are Transforming Metal Fabrication
Introduction: The Digital Revolution in Metal Fabrication
Imagine a manufacturing floor where machines communicate seamlessly, adjust their operations in real-time, and predict failures before they happen. This is not a vision of the distant future—it’s happening now, thanks to Industry 4.0.
For designers and decision-makers in electronics development, metal fabrication has always been a crucial step in bringing ideas to reality. Whether it’s the chassis of a consumer gadget, the enclosure of an industrial controller, or intricate heat sinks, the precision and efficiency of fabrication directly impact product quality, costs, and time to market.
With the rise of smart technologies, traditional metal fabrication is evolving. The old ways of manual machining and trial-and-error prototyping are giving way to intelligent, automated systems that offer greater efficiency, precision, and scalability. But what does this mean for electronics development? And how can companies, from startups to established manufacturers, leverage these advancements?
Let’s explore the transformation of metal fabrication through the lens of Industry 4.0.
Understanding Industry 4.0 in Manufacturing
The term "Industry 4.0" refers to the fourth industrial revolution, where manufacturing integrates digital technologies such as:
The Internet of Things (IoT): Machines equipped with sensors that collect and share real-time data.
Artificial Intelligence (AI) and Machine Learning (ML): Systems that analyze data and optimize production automatically.
Automation and Robotics: Robots that handle precision tasks with minimal human intervention.
Cloud Computing and Edge Computing: Data processing closer to the factory floor, enabling real-time decision-making.
These innovations are not just buzzwords; they are actively shaping how products are designed and manufactured. For electronics metal fabrication, this means better quality control, shorter lead times, and reduced waste—all critical factors in staying competitive.
The Evolution of Metal Fabrication in Electronics
Before diving into how Industry 4.0 is transforming the field, let’s take a moment to reflect on how metal fabrication has traditionally worked.
Manual Machining & Stamping: Skilled operators used lathes, drills, and presses to shape metal components. These methods required extensive human labor and had a high risk of inconsistency.
Computer Numerical Control (CNC) Machining: While CNC machines improved precision, programming and setup time remained a bottleneck.
Laser Cutting & Sheet Metal Fabrication: Introduced better accuracy, but still required significant manual intervention.
3D Printing for Prototyping: Enabled quick iterations, but scaling for production remained a challenge.
While these traditional processes were effective, they often resulted in long lead times, material waste, and unpredictable costs. With Industry 4.0, metal fabrication is becoming smarter, faster, and more cost-efficient.
Smart Technologies Transforming Metal Fabrication
Let’s break down the core Industry 4.0 innovations that are revolutionizing metal fabrication for electronics.
1. Automation and Robotics: The New Workforce
Automation is replacing repetitive manual tasks with robotic systems that enhance efficiency and precision.
Robotic Welding & Assembly: Welding robots, guided by AI, ensure consistent quality, reducing defects.
Automated CNC Machining: AI-driven CNC machines self-adjust based on sensor data, minimizing errors.
Collaborative Robots (Cobots): These robots work alongside humans, handling intricate fabrication tasks without safety risks.
For electronics companies, this means lower labor costs, improved product consistency, and faster production cycles.
2. IoT and Connected Machines: Real-Time Monitoring
Traditionally, production issues were only identified after defects appeared. IoT changes that by providing:
Real-time Data Collection: Machines track their own performance, sending alerts before failures occur.
Predictive Maintenance: AI analyzes machine wear-and-tear, scheduling maintenance only when necessary.
Energy Efficiency Monitoring: Smart sensors optimize power consumption, reducing energy costs.
A connected fabrication line means fewer disruptions, lower maintenance costs, and a more agile production process.
3. AI and Machine Learning: Smarter Decision-Making
AI is playing a growing role in optimizing metal fabrication through:
Defect Detection: High-speed cameras and AI algorithms detect microscopic defects that human inspectors might miss.
Production Optimization: AI analyzes workflow patterns, recommending process improvements.
Dynamic Pricing Models: AI predicts material costs, helping companies optimize procurement strategies.
By integrating AI, electronics manufacturers can drastically reduce waste and increase yield, making production more cost-effective.
4. Additive Manufacturing (Metal 3D Printing): A New Frontier
While 3D printing was initially limited to plastic prototypes, advances in metal 3D printing are unlocking new possibilities:
Complex Geometries: Parts with intricate internal structures can now be fabricated without machining.
Rapid Prototyping: Electronics enclosures and custom metal parts can be produced in days instead of weeks.
Material Efficiency: Unlike traditional methods that cut away excess material, 3D printing builds parts layer by layer, reducing waste.
For electronics designers, this means more freedom to innovate without worrying about tooling costs.
5. Digital Twins and Virtual Prototyping
Digital twins—virtual simulations of physical fabrication processes—are enabling:
Faster Design Iterations: Engineers can test designs in a virtual environment before committing to production.
Process Optimization: Digital simulations identify bottlenecks, improving efficiency before production starts.
Cost Savings: Reducing trial-and-error means fewer wasted materials and less rework.
For decision-makers, digital twins provide a data-driven approach to refining product designs before investing in costly production.
Benefits of Industry 4.0 for Electronics Metal Fabrication
The integration of smart technologies is delivering measurable benefits to electronics manufacturers:
✔ Increased Efficiency: Automated workflows streamline production, cutting down lead times.
✔ Higher Quality: AI-driven quality control minimizes defects and improves reliability.
✔ Reduced Costs: Predictive maintenance and optimized material usage lower production expenses.
✔ Scalability: Companies can easily adjust production capacity without massive retooling.
✔ Faster Time to Market: Digital prototyping accelerates the transition from design to mass production.
In a competitive market where innovation speed matters, these benefits translate into a strong competitive edge.
Challenges and Considerations
While the promise of Industry 4.0 is exciting, adopting these technologies comes with challenges:
🔹 High Initial Investment: Upgrading to smart machinery and AI systems requires capital.
🔹 Workforce Training: Employees need to develop new skills to work with automation and data analytics.
🔹 Cybersecurity Risks: Connected machines are vulnerable to cyber threats if not properly secured.
🔹 Integration Complexity: Legacy systems may require extensive modifications to work with new technologies.
For companies transitioning to Industry 4.0, starting small—such as implementing IoT sensors for monitoring—can be a practical first step.
Future Trends and Opportunities
Looking ahead, several trends will further shape the industry:
🚀 AI-Driven Adaptive Manufacturing: AI systems will self-optimize production based on real-time demand.
🌱 Sustainable Fabrication: Eco-friendly practices like closed-loop recycling will reduce environmental impact.
📶 5G and Edge Computing: Faster data transfer will enable even more precise and responsive automation.
For electronics companies, staying ahead of these trends will be key to maintaining a competitive advantage.
Conclusion: Why Designers and Decision-Makers Should Care
Industry 4.0 is not just a buzzword—it’s a shift that is reshaping electronics metal fabrication in profound ways. Whether you’re designing enclosures for the next-generation IoT device or managing production for a high-volume consumer product, smart manufacturing can:
✅ Improve product consistency
✅ Speed up time to market
✅ Reduce costs and material waste
For decision-makers, the choice is clear: adopt these innovations or risk being left behind. The future of metal fabrication is smart, and it’s already here.