How to Maintain Injection Molding Machines for Longevity: A Guide for Designers and Decision-Makers in Electronics Development
An injection molding machine—one of those workhorses shaping plastic enclosures for circuit boards—starts coughing up defective parts. Downtime creeps in, deadlines loom, and your team scrambles to figure out why.
2/24/20256 min read
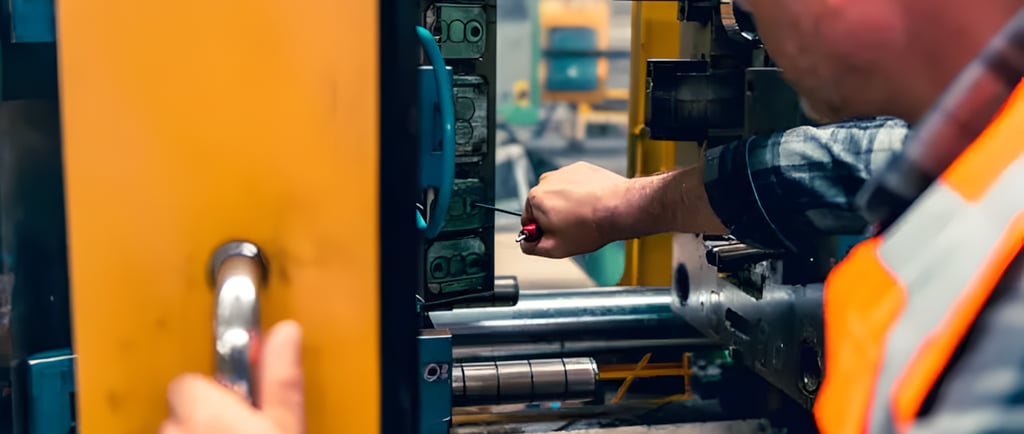
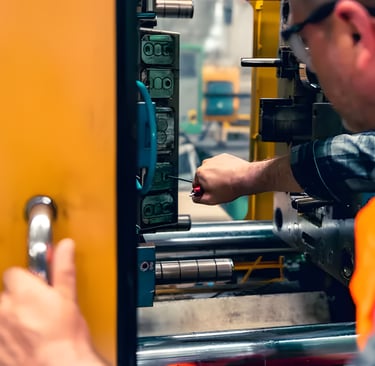
Picture this: It’s a hectic Monday morning, and your production line screeches to a halt. An injection molding machine—one of those workhorses shaping plastic enclosures for circuit boards—starts coughing up defective parts. Downtime creeps in, deadlines loom, and your team scrambles to figure out why. Sound familiar? If you’re a designer or decision-maker in electronics development, you know these machines aren’t just tools; they’re the heartbeat of your operation. A breakdown isn’t just an inconvenience—it’s a hit to your budget, schedule, and reputation.
The good news? Most of these headaches are preventable with a little TLC. Maintaining injection molding machines isn’t glamorous, but it’s the secret to keeping your production humming and your electronic components top-notch. Whether you’re a facility manager juggling efficiency metrics or a hands-on technician tweaking molds for that perfect fit, this guide is for you. Let’s dive into practical tips to extend your machine’s life, cut repair costs, and keep those plastic housings for your latest gadget rolling off the line flawlessly.
Understanding Your Injection Molding Machine: The Basics Matter
Before we get our hands dirty, let’s talk about what’s under the hood. Injection molding machines are marvels of precision, turning molten plastic into everything from tiny connectors to rugged device casings. At their core, they’ve got a few key players: the injection unit (melts and shoots plastic), the clamping unit (holds the mold tight), the hydraulic system (powers the muscle), and the control panel (the brains keeping it all in sync).
Why does this matter to you? If you’re designing the next big thing in electronics—like a sleek wearable or a durable router housing—you’re counting on these parts to work together seamlessly. Knowing the machine’s anatomy helps you spot trouble before it snowballs. For instance, a worn-out nozzle could mess up tolerances on your latest prototype, while a sluggish hydraulic pump might delay a big batch of USB casings.
For decision-makers, here’s a nugget: invest a couple of hours in training your team on these basics. I once worked with a crew who thought “funny noises” were just part of the machine’s charm—until a $10,000 repair bill proved otherwise. A little knowledge goes a long way.
Daily Maintenance Habits: The 15-Minute Game-Changer
Let’s start small. You don’t need a PhD in engineering to keep your machine happy—just a few daily habits. Think of it like brushing your teeth: skip it, and the consequences creep up.
Keep It Clean
Dust, stray resin, or grease can gunk up molds and surfaces faster than you’d believe. Grab a rag and some non-abrasive cleaner (check the manual for recommendations), and wipe down the mold and machine exterior daily. I’ve seen technicians skip this because “it’s still running fine,” only to find a layer of grime throwing off part quality a week later. For electronics, where precision is king, that’s a risk you can’t take.
Lubricate Like a Pro
Moving parts—like toggles or slides—need love too. Check the manufacturer’s guide for the right lubricant, and apply it daily or as recommended. Too much grease, though, can attract dirt or drip into places it shouldn’t, so don’t go overboard. One tech I knew turned a routine lube job into a slippery mess that took hours to clean up—lesson learned.
Listen and Look
Spend a minute each day listening to the machine. Does it hum smoothly, or is there a rattle that wasn’t there yesterday? Peek for leaks or vibrations too. These are your early warning signs. Technicians, keep a quick log—scribble down anything odd. It’s like a diary for your machine, and it’ll help you catch patterns before they become emergencies.
These daily checks take maybe 15 minutes, but they’re gold. For designers, it means fewer scrapped parts; for managers, it’s less unplanned downtime eating into your margins.
Scheduled Maintenance: Your Long-Term Playbook
Daily care keeps the wheels turning, but scheduled maintenance is where you build longevity. Think of it as taking your car for an oil change instead of waiting for the engine to seize.
Weekly Tune-Ups
Once a week, pop the hood (figuratively). Check hydraulic fluid levels—low fluid starves the system, and dirty fluid (cloudy or gritty) wears it down. Swap it out if it looks off. Then, test the heaters and temperature controls. If they’re inconsistent, your plastic might not melt right, leaving you with brittle casings or flashing on your connectors. I’ve seen a team catch a failing heater during a weekly check and save a whole batch of IoT device shells—crisis averted.
Monthly Deep Dives
Every month, give your molds some attention. Look for wear, cracks, or corrosion—especially if you’re molding tricky resins for high-heat electronics. A quick polish can keep them sharp. Then, check electrical connections. Loose wires can cause shorts or erratic performance, and in electronics production, that’s a recipe for disaster. Tighten anything that’s wiggled free.
Quarterly Overhauls
Every three months, go big. Calibrate the pressure settings and clamping alignment—misalignment can stress the machine and ruin part precision. Replace hydraulic filters too; clogged ones choke the system. I once saw a shop delay this step, and their pump burned out mid-run. The cost? A week of downtime and a hefty repair bill. Don’t let that be you.
Facility managers, here’s your cue: whip up a maintenance calendar. Stick it on the wall or in an app—whatever keeps your team on track. It’s a small effort for a big payoff.
Troubleshooting Common Hiccups: Stay Ahead of the Curve
Even with great care, machines throw curveballs. Here’s how to handle two headaches I’ve seen pop up in electronics molding.
Inconsistent Part Quality
Say your latest batch of battery casings has uneven walls or sink marks. Chances are, the nozzle’s worn, or the pressure’s off. Inspect the nozzle for wear—replace it if it’s shot—and recalibrate the settings. Designers, this one’s on you too: if your mold design pushes the machine’s limits, tweak it to play nice.
Hydraulic Leaks
Spot a puddle under the machine? Check the seals and hoses. Cracked seals or brittle hoses are usually the culprits. Swap them out, and make it a habit to eyeball those lines monthly. One shop I visited ignored a slow drip until it fried a motor—$15,000 later, they wished they’d acted sooner.
Technicians, don’t wait for the red light to blink. Proactive fixes beat firefighting every time.
Lean on Manufacturer Guidelines: Your Cheat Sheet
Here’s a tip that sounds obvious but gets overlooked: read the manual. That dusty booklet (or PDF) from the manufacturer isn’t just filler—it’s tailored to your machine. Follow its maintenance schedule like gospel. It’ll tell you when to grease, what fluid to use, and how often to swap parts.
Stock up on spares too—O-rings, heaters, nozzles. If a part fails mid-run, you’ll be back online in hours, not days. And for the big stuff—like a hydraulic pump overhaul—consider a service contract. Managers, weigh the cost against downtime; it’s usually a no-brainer.
I once chatted with a guy who ignored the manual’s filter change advice. His machine limped along until it didn’t. The manual’s not bossy—it’s smart.
Tech to the Rescue: Smarter Maintenance
Modern machines are getting clever, and that’s a win for electronics production. Many now come with sensors that ping you if something’s off—overheating barrels, pressure dips, you name it. Pair that with maintenance software, and you’ve got a crystal ball. Log every task, track wear trends, and predict when parts might fail.
For designers, this means tighter specs with fewer surprises. For decision-makers, it’s uptime and cost savings wrapped in one. I’ve seen shops cut maintenance guesswork by 20% with these tools. If your budget allows, it’s worth a look.
Wrapping It Up: Your Machine, Your Success
So, there you have it—a roadmap to keep your injection molding machines purring for years. Start with daily habits: clean, lube, listen. Layer on weekly, monthly, and quarterly checks to catch wear before it bites. Troubleshoot smart, lean on the manual, and let tech give you an edge.
Technicians, kick things off tomorrow with a quick inspection—your machine will thank you. Managers and designers, build that maintenance plan this week. It’s not just about avoiding breakdowns; it’s about protecting your investment and delivering electronics that wow your customers.
A well-maintained machine isn’t just gear—it’s the backbone of your success. Keep it strong, and it’ll carry you far.