How to Design Enclosures for Harsh Environments: A Comprehensive Guide
Designing enclosures for harsh environments isn’t just about slapping on a metal box and calling it a day. It’s a meticulous dance between material science, engineering, and foresight.
2/8/20254 min read
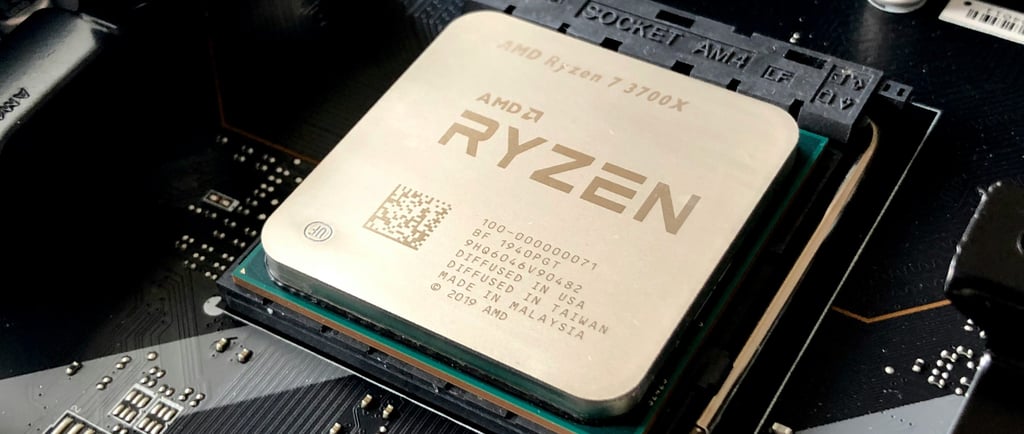
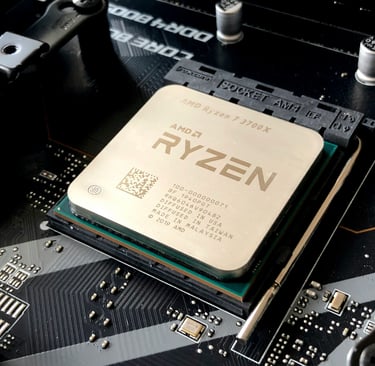
Imagine this: You’ve spent months developing cutting-edge IoT sensors for a smart agriculture project. They’re deployed across a vast farmland, collecting data to optimize crop yields. But after the first heavy rain, half the units fail. Water seeped into the enclosures, frying the circuits. Sound familiar?
Designing enclosures for harsh environments isn’t just about slapping on a metal box and calling it a day. It’s a meticulous dance between material science, engineering, and foresight. Whether it’s a sweltering desert, a salt-sprayed ship deck, or a vibration-heavy factory floor, your enclosure needs to be tougher than the challenges it faces. Let’s break down how to create enclosures that don’t just survive but thrive in extreme conditions.
1. What Even Is a Harsh Environment? Let’s Get Specific
A “harsh environment” is any setting where electronics face Mother Nature’s wrath or human-made chaos. Think offshore oil rigs battling corrosive saltwater, desert solar panels baking at 120°F, or mining equipment shaking like a washing machine on spin cycle. Common culprits include:
Moisture: Rain, humidity, or full submersion.
Dust & Debris: Fine particles that creep into seams.
Temperature Extremes: From Arctic cold to foundry-level heat.
Physical Stress: Drops, vibrations, or crushing forces.
Chemical/UV Exposure: Acids, solvents, or relentless sunlight.
Industry-Specific Nightmares
Oil & Gas: Enclosures must laugh at corrosive chemicals.
Outdoor IoT: Waterproofing + UV resistance = non-negotiable.
Aerospace: Lightweight yet rugged—like a titanium backpack.
2. The 5 Pillars of Bulletproof Enclosure Design
A. Material Matters: Picking the Right “Armor”
Your material choice is the foundation. Get it wrong, and the rest crumbles.
Metals:
Aluminum: Light, naturally corrosion-resistant, and great at shedding heat. Perfect for drones or outdoor cameras.
Stainless Steel: The Hulk of metals. Ideal for chemical plants or marine gear but heavier.
Plastics:
Polycarbonate: Nearly unbreakable (think “riot shield” toughness). Use it for impact-prone areas.
UV-Stabilized ABS: Resists yellowing and brittleness under sunlight. Great for solar equipment.
Composites: Fiber-reinforced plastics or hybrids for niche needs, like EMI shielding in military apps.
Pro Tip: Always ask, “What’s the worst-case scenario here?” If your enclosure will face acid spills, stainless steel with a PTFE coating might save the day.
B. IP Ratings Decoded: Not All Waterproofing Is Equal
IP ratings (Ingress Protection) are your cheat sheet for environmental defense.
IP67: Dust-tight and survives 30 minutes underwater at 1m depth. Good for temporary submersion (e.g., a sensor caught in a flood).
IP68: The submarine of ratings—handles prolonged underwater use. Think underwater drones.
IP69K: For high-pressure, high-temperature washdowns (food processing plants, anyone?).
Gotcha Moment: IP ratings don’t cover UV resistance or chemical exposure. Always cross-reference with other standards!
C. Thermal Management: Keeping Cool (or Warm)
Electronics hate temperature swings. A Raspberry Pi left in a sealed box under the sun? That’s a recipe for a baked Pi.
Passive Cooling: Heat sinks, thermal pads, or choosing materials like aluminum that dissipate heat naturally.
Active Cooling: Fans or Peltier coolers for high-heat zones. But remember—fans need vents, which can compromise seals!
Insulation: For freezing temps, use aerogel or foam layers to keep components cozy.
Case Study: A railway signal box in Norway uses heated enclosures with thermostats to prevent ice buildup—no more frozen circuits!
D. Shock & Vibration: Surviving the Shake-Up
Machinery vibrations or off-road terrain can shake screws loose or crack PCBs.
Internal Padding: Use silicone or rubber mounts to isolate components.
Ruggedized Mounts: Bolt enclosures to surfaces with anti-vibration brackets.
Material Flexibility: TPU (thermoplastic polyurethane) can absorb impacts better than rigid plastics.
E. Corrosion Resistance: Fighting the Rust
Saltwater, acids, or even humidity can turn metals into Swiss cheese.
Coatings: Powder coating or anodizing adds a protective layer.
Material Swap: Marine-grade aluminum (5052 or 6061 alloys) resists saltwater corrosion.
Pro Hack: For coastal apps, use stainless steel hinges and fasteners—they won’t fuse shut like regular steel.
3. Tailoring Designs to Specific Threats
Moisture: The Silent Killer
Gaskets & Seals: Use silicone or EPDM rubber for door seals.
Cable Glands: Waterproof connectors like Bulgin’s Buccaneer series keep ports dry.
Dust: The Creeping Invader
Double-Sealed Latches: Ensure doors close tightly.
Filtered Vents: Let heat escape but block dust with Gore-Tex membranes.
UV Radiation: The Slow Fade
UV-Stabilized Housings: Look for materials with additives like carbon black.
Shade Structures: Design recessed displays or overhangs to limit sun exposure.
Temperature Extremes
Reflective Coatings: White or mirrored finishes deflect heat in deserts.
Heated Enclosures: For Arctic use, integrate small heating elements.
4. Testing: The “Break It Before It Breaks” Phase
Prototypes are like crash test dummies—they exist to fail so the final product won’t.
Standards to Live By:
MIL-STD-810: Military-grade tests for drops, vibrations, and temp extremes.
IEC 60529: Validates IP ratings with dust chambers and water jets.
UL 50: Certifies safety for hazardous locations.
Real-World Testing Ideas:
Thermal Shock Test: Move enclosures from -40°C freezers to +85°C ovens. Repeat.
Salt Spray Test: Simulate years of marine corrosion in days.
Drop Test: Toss it off a 2-story scaffold. Did the PCB survive?
5. Customization: Because One Size Fits None
Modular Designs: Need to swap a sensor? Use hinged panels with quick-release seals.
Surface Finishes: Anodized colors for corrosion resistance and brand flair.
Cable Management: Waterproof glands with strain relief to prevent tug damage.
Example: A custom enclosure for a wildfire camera used modular compartments—one for electronics, another for battery swaps—all IP68 rated.
6. Real-World Wins: Enclosures That Nailed It
Outdoor IoT Soil Sensor:
Polycarbonate body with IP68 rating.
UV-stabilized to prevent sun degradation.
Integrated heat sink for passive cooling. Result? 3+ years in Texas heat with zero failures.
Industrial Control Box:
Stainless steel with powder-coated finish.
Shock-mounted internals survived a 6.0 Richter factory tremor.
Marine GPS Unit:
Marine-grade aluminum with anti-corrosion coating.
Submersible to 10m—outlasted a hurricane-induced flood.
7. Why Go It Alone? Partner with the Pros
Designing rugged enclosures is a team sport. Experienced manufacturers bring:
Material Mastery: Knows which composites withstand sulfuric acid.
Cost vs. Durability Balance: Avoid over-engineering (no need for titanium in a garden sensor).
Why Peakingtech?
We’ve crafted enclosures for Mars-like deserts and deep-sea ROVs. Our secret? Listening. Tell us your horror stories—we’ll engineer the solution.
Conclusion: Build Tough Early, Save Pain Later
Designing for harsh environments isn’t an afterthought—it’s the blueprint. Prioritize materials, IP ratings, and thermal strategies upfront. Test like you’re trying to break it. And remember: A well-designed enclosure isn’t a cost; it’s insurance against field failures.
Your Turn: Hit a roadblock with your enclosure design? Share your challenge below, or reach out to Peakingtech for a consult. Let’s make your next project indestructible.
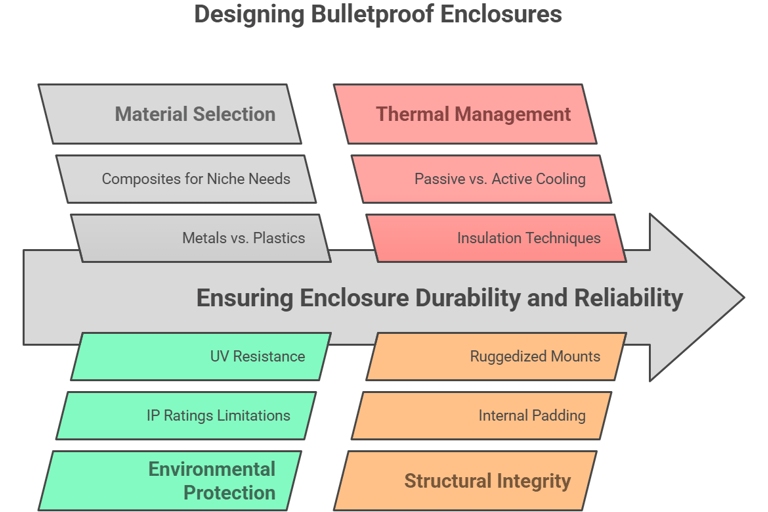
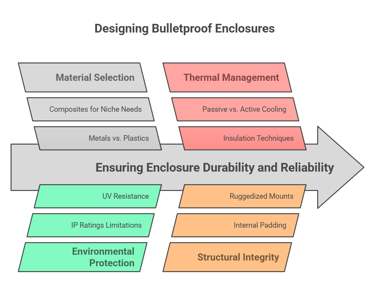