How to Design Electronics for Manufacturability (DFM): A Beginner’s Guide
For beginners, DFM might feel like learning to ride a bike while juggling. But here’s the truth: ignoring DFM costs time, money, and sanity. This guide isn’t about stifling creativity—it’s about empowering you to design with the entire product lifecycle in mind.
2/18/20255 min read
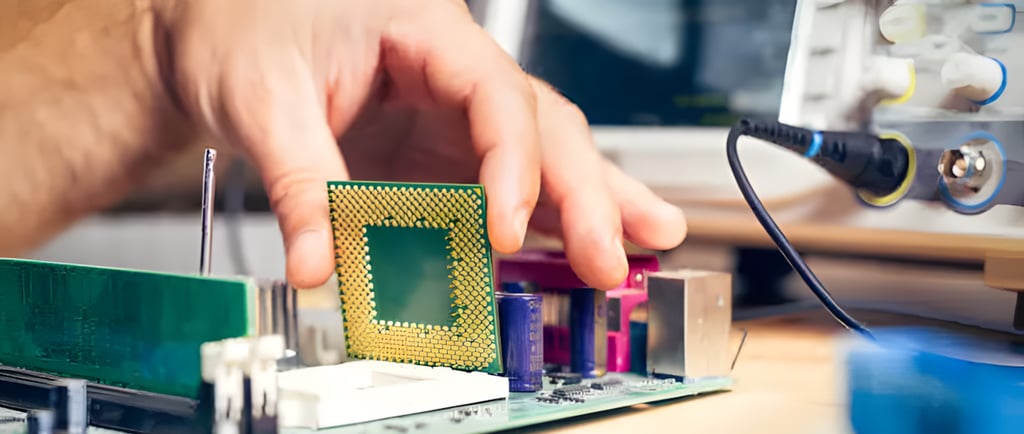
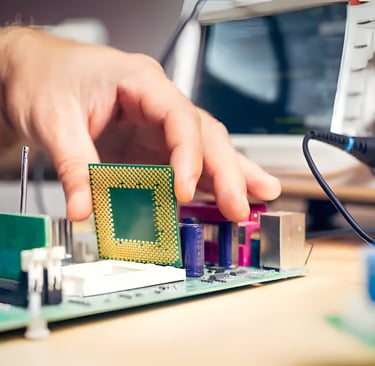
Introduction: The Importance of DFM in Modern Electronics Design
In the fast-paced world of electronics, where innovation and speed to market are paramount, Design for Manufacturability (DFM) stands as a critical yet often overlooked aspect. Imagine dedicating countless hours perfecting your PCB design, only to find out that a key component is unavailable or that your meticulously crafted prototype fails during assembly due to soldering issues. These scenarios highlight why DFM isn't just a buzzword but a fundamental practice that can turn your brilliant ideas into reliable, scalable products.
For beginners venturing into electronics design, understanding DFM might seem like learning to ride a bike while juggling multiple balls. However, it's crucial to recognize that ignoring DFM principles can lead to significant financial losses, project delays, and frustration. This guide aims to demystify DFM by providing practical insights, real-world examples, and actionable tips to help you design with manufacturability in mind from the outset.
Understanding DFM Basics: Beyond Checklists and Best Practices
At its core, DFM involves designing electronic products in a way that optimizes their ease and cost-effectiveness of manufacturing. It's akin to preparing a recipe for mass production; you wouldn't choose an exotic spice available only in one remote village if you're aiming to produce thousands of dishes daily. Similarly, DFM ensures your designs avoid hard-to-source components and overly complex assembly processes.
Key Objectives of DFM:
Cost Reduction: By minimizing the number of components and opting for standardized parts, you can significantly lower material costs.
Enhanced Reliability: Designs that withstand the rigors of the assembly process are less likely to fail once deployed in the field.
Accelerated Time-to-Market: Avoiding redesign loops through early consideration of manufacturability helps bring products to market faster.
Dispelling Common Misconceptions About DFM
Myth 1: "DFM is Only Relevant for Large Companies"
Reality: Even small startups face manufacturing challenges. A single design flaw can derail budgets and timelines, emphasizing the importance of DFM across all scales of operation.
Myth 2: "DFM Stifles Innovation"
Reality: Constraints foster creativity. Consider how foldable smartphones emerged as innovative solutions within the confines of existing manufacturing capabilities—a testament to how DFM can coexist with groundbreaking ideas.
Essential Principles of DFM: Simplification and Standardization
Simplifying Your Design
Every additional resistor or capacitor introduces another potential point of failure. Embrace minimalism by questioning each component's necessity and replacing custom ICs with readily available alternatives whenever feasible.
Standardizing Components
Opt for widely used package types such as QFP (Quad Flat Package) or BGA (Ball Grid Array), unless there's a compelling reason not to. For instance, using 0805 resistors instead of 0603s if your contract manufacturer's pick-and-place machine is optimized for larger sizes can streamline production without compromising performance.
Component Availability: Navigating Supply Chain Challenges
The global semiconductor shortage of 2021 highlighted the risks associated with relying on scarce components. One startup experienced firsthand the consequences of choosing a microcontroller with a staggering 52-week lead time, causing significant project delays. Always verify distributor stock levels and lifecycle statuses through platforms like Texas Instruments' website or Digi-Key to mitigate supply chain disruptions.
PCB Layout Optimization: Strategic Approaches to Enhance Manufacturability
Board Size and Shape
Rectangular boards maximize panel yield compared to irregular shapes, reducing waste and overall costs. When planning your PCB layout, consider how efficiently it fits onto standard-sized panels used by manufacturers.
Layer Count Management
Adding layers increases complexity and expense; a four-layer board typically costs around 40% more than a two-layer counterpart. Reserve multi-layer configurations for situations where signal integrity requirements necessitate them.
Strategic Component Placement
Align polarized components consistently to simplify assembly procedures. Maintain adequate spacing between elements—approximately 0.5mm—to accommodate solder paste stencils effectively and prevent bridging during reflow soldering.
Trace Routing Techniques
Adhere to industry-standard guidelines outlined in documents like IPC-2221 when determining trace widths and spacings. Insufficiently wide traces may result in etching errors during fabrication. Implement thermal relief patterns ("thermal spokes") on ground pads to minimize tombstoning effects during reflow soldering.
Component Selection Strategies: Ensuring Accessibility and Compatibility
Avoid Footprint Fails
Ensure compatibility between chosen components and your manufacturer's equipment capabilities. For example, selecting a QFN (Quad Flat No-Leads) package without verifying whether your CM's reflow oven supports its thermal profile could lead to unforeseen complications.
Monitor Lifecycle Statuses
Utilize tools such as SiliconExpert or Octopart to track obsolescence notices promptly. If a component reaches end-of-life status, proactively seek replacements before proceeding with prototyping stages.
Soldering Process Considerations: Preventing Assembly Mishaps
Reflow vs Wave Soldering
Understand the implications of different soldering techniques based on your component mix. Through-hole parts generally require wave soldering, whereas mixed technology assemblies may necessitate selective soldering methods at higher costs.
Tackling Tombstoning Issues
Equalize pad sizes at both ends of passive components to counteract uneven heat distribution during reflow cycles, which commonly causes tombstoning defects.
Testing Methodologies: Identifying Flaws Proactively
Integrate test points throughout your design to facilitate thorough validation via flying probe testers. Position fiducials strategically and avoid placing tall components near board edges to enable effective Automated Optical Inspection (AOI).
Collaborative Engagement With Manufacturers
Early Involvement Pays Off
A wearable tech company learned this lesson the hard way after submitting a high-density interconnect (HDI) board featuring ten layers, unaware that their chosen manufacturer lacked the necessary equipment to handle microvias. Engage closely with your CM right from the conceptual phase to align expectations regarding technical specifications and limitations.
Seek Clarifications Actively
Clarify preferences related to aspects like preferred PCB thicknesses or maximum allowable panel dimensions directly with your partner. Establish open lines of communication to address any queries promptly.
Iterate Based On Feedback Loops
Submit Design Validation Test (DVT) prototypes ahead of final sign-off to incorporate valuable feedback gathered from initial trials.
Leveraging Tools & Resources To Enhance Your DFM Skills
Software Solutions
Take advantage of advanced features offered by popular EDA suites like Altium Designer’s built-in DFM checker or Cadence Allegro’s comprehensive suite tailored specifically towards optimizing manufacturability aspects during schematic capture and PCB layout phases.
Educational Opportunities
Enroll in specialized courses focusing on digital manufacturing practices available through reputable online platforms such as Coursera. Stay updated with evolving standards set forth by organizations like IPC (Institute for Printed Circuits), particularly concerning footprint definitions under IPC-7351 guidelines.
Community Support Networks
Join vibrant communities centered around printed circuit board enthusiasts found on social media forums like Reddit’s r/PrintedCircuitBoard subreddit or participate actively within dedicated threads hosted by respected industry veterans over at EEVblog discussions.
Real-Life Case Study Illustrating The Impact Of Ignoring DFM Principles
A startup specializing in wearable technology encountered substantial setbacks stemming from neglecting basic tenets of DFM during initial product development stages. They opted for a bespoke lithium battery configuration rather than leveraging off-the-shelf alternatives readily accessible within established supply chains. Consequently, they incurred exorbitant expenses amounting up to $50,000 merely to develop customized molds required solely for accommodating said non-standard cell format. Upon reassessing priorities amidst escalating overheads coupled alongside extended delivery schedules plaguing their operations pipeline – they eventually pivoted towards adopting conventional pouch cells thereby slashing total expenditures by approximately seventy percent overnight!
Conclusion: Elevating Your Design Game Through Effective Application Of DFM Concepts
Embracing DFM isn’t about playing conservatively; instead, it empowers designers to create empathetic solutions considering downstream stakeholders involved throughout entire product lifecycles. Start implementing these strategies incrementally starting perhaps with something straightforward like prioritizing component standardization efforts within upcoming projects gradually expanding horizons thereafter. Remember - every journey begins with taking that first step forward!