How to Boost Efficiency in Electronics Manufacturing: Proven Strategies for Designers and Decision-Makers
Whether you’re sketching the next big circuit board design or calling the shots on production budgets, efficiency impacts everything—cost, quality, and your ability to deliver on time.
3/7/20255 min read
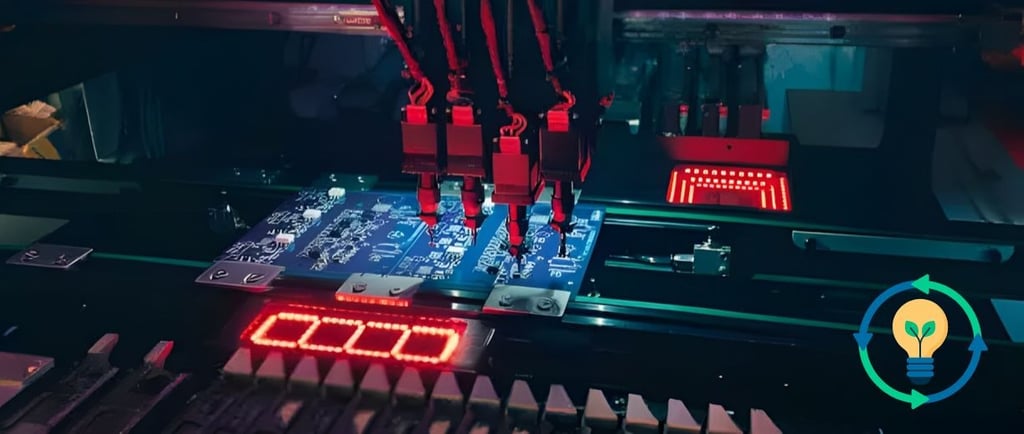
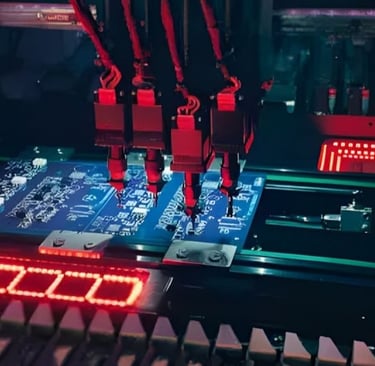
Picture this: a bustling electronics manufacturing floor where every second counts, yet a single delay in the supply chain or a glitch in the assembly line wipes out hours of progress. Sound familiar? Inefficiencies like these aren’t just minor hiccups—they’re silent profit-killers that can cost companies millions each year. For designers and decision-makers in electronics development, improving efficiency isn’t optional; it’s the key to staying competitive in a fast-moving industry.
Whether you’re sketching the next big circuit board design or calling the shots on production budgets, efficiency impacts everything—cost, quality, and your ability to deliver on time. In this article, I’ll walk you through practical, proven strategies to streamline your processes, cut waste, and boost productivity. Let’s dive into how you can transform your manufacturing operations from a chaotic scramble into a well-oiled machine.
Understanding Efficiency in Electronics Manufacturing
Efficiency in electronics manufacturing isn’t some buzzword thrown around in boardroom meetings—it’s about getting the most out of your resources while keeping quality top-notch. Think of it as maximizing output with minimal waste, whether that’s time, materials, or energy. But let’s be real: achieving this isn’t always a walk in the park.
The electronics world is riddled with challenges—supply chain bottlenecks, equipment breakdowns, and even human slip-ups can throw a wrench into your plans. I’ve seen teams scramble when a late shipment of resistors halts production or when an outdated soldering machine slows down the line. These aren’t just annoyances; they’re efficiency drains that hit your bottom line.
So why bother? Because shaving even a few minutes off production time or reducing defects by a percentage point can mean happier customers, lower costs, and a stronger market edge. Ready to tackle this? Let’s explore the how-to.
Strategies to Improve Efficiency
Adopt Lean Manufacturing Principles
If you’ve ever heard of “lean” and thought it sounded like a diet plan, think again. Lean manufacturing is about trimming the fat from your processes—eliminating anything that doesn’t add value. For designers, this might mean simplifying a PCB layout to reduce assembly steps. For decision-makers, it’s about cutting overstock that ties up capital.
Take just-in-time (JIT) production, for instance. Instead of stockpiling components “just in case,” you order what you need when you need it. I once worked with a team that slashed inventory costs by 30% using JIT, though it took some serious coordination with suppliers. It’s not magic—it’s discipline. Start small: identify one wasteful step in your workflow and axe it.
Invest in Automation and Robotics
Let’s face it—humans are amazing, but we’re not perfect. A shaky hand or a tired eye can lead to a misplaced component, and suddenly you’re reworking a batch. Automation changes that game. Robotic arms can solder with precision 24/7, and automated testing systems catch defects faster than any human eye.
I remember touring a facility where a robotic pick-and-place machine cut assembly time in half. Sure, the upfront cost stung, but the payoff? Fewer errors and a happier production crew freed up for creative tasks. Designers, think about how your layouts can play nice with automation—fewer custom steps mean faster robotic execution. Decision-makers, weigh the long-term savings against that initial invoice.
Optimize Supply Chain Management
A smooth supply chain is the backbone of efficient manufacturing, yet it’s often where things go haywire. Late deliveries or overpriced components can derail even the best-laid plans. The fix? Get proactive. Use predictive analytics to forecast demand, so you’re not caught short—or swimming in excess inventory.
Building tight-knit relationships with suppliers helps, too. I once knew a manager who negotiated shorter lead times by simply picking up the phone and chatting with vendors over coffee. It’s old-school, but it works. Designers can pitch in by spec’ing components with multiple sourcing options, giving decision-makers flexibility when shortages hit.
Upgrade Equipment and Technology
Old gear might have a nostalgic charm, but it’s a productivity killer. Modern equipment—like energy-efficient reflow ovens or high-speed CNC machines—can churn out parts faster while sipping less power. I’ve seen plants where upgrading a single bottleneck machine boosted throughput by 25%.
The catch? Cost. Decision-makers, you’ll need to crunch the numbers: will the ROI justify the spend? Designers, consider how your designs can leverage new tech—maybe that fancy 3D printer could prototype faster than outsourcing. It’s about working smarter, not just harder.
Enhance Workforce Training
Your team is your biggest asset, but only if they’re equipped to shine. A poorly trained operator can botch a run of boards faster than you can say “rework.” Regular training keeps skills sharp and errors low. Cross-skilling is a gem, too—imagine a worker who can jump from assembly to testing without missing a beat.
I once saw a company turn around a 15% defect rate by investing in hands-on workshops. Designers, make your specs clear and train-friendly—complex designs might need a quick explainer for the floor crew. Decision-makers, budget for this; it’s cheaper than fixing mistakes later.
Implement Data-Driven Decision Making
Welcome to the age of smart manufacturing. Internet of Things (IoT) sensors can track everything from machine temps to production speeds in real time. Pair that with analytics, and you’ve got a crystal ball for spotting trouble—like a motor about to fail before it does.
A friend in the industry swore by predictive maintenance after it saved his line from a week-long shutdown. Designers, build in sensor-friendly features where you can. Decision-makers, push for data tools that give you actionable insights, not just pretty dashboards. It’s like having a sixth sense for your factory.
Focus on Quality Control
Efficiency isn’t just speed—it’s doing it right the first time. A defect caught late can mean scrapping a whole batch, which is a gut punch to both time and budget. Statistical process control (SPC) or rigorous testing can nip issues in the bud.
I recall a team that cut rework by 40% just by tightening up early-stage checks. Designers, bake quality into your work—simpler designs often mean fewer failure points. Decision-makers, enforce those checkpoints; they’re your safety net.
Case Studies: Real-World Wins
Take Tesla, for example. Their obsession with automation—think massive robotic assembly lines—lets them pump out EVs at a pace others can only dream of. Or look at Samsung, a lean manufacturing champ that’s mastered cutting waste while keeping quality sky-high.
What’s the lesson? Efficiency isn’t one-size-fits-all. Tesla leans on tech; Samsung on process. Find what fits your operation and run with it.
Practical Steps to Get Started
Ready to roll up your sleeves? Here’s how:
Assess Current Processes: Grab a coffee, walk the floor, and spot where things lag. An efficiency audit doesn’t lie.
Set Clear Goals: Aim for something concrete—like slashing assembly time by 20% in six months.
Prioritize Investments: Start with low-hanging fruit, like tweaking a workflow, before splurging on robots.
Monitor Progress: Track KPIs like cycle time or defect rates. Numbers don’t sugarcoat reality.
I’ve seen teams kick off with just one of these and see results in weeks. It’s less about grand overhauls and more about steady wins.
Conclusion
Boosting efficiency in electronics manufacturing isn’t rocket science—but it does take guts, smarts, and a willingness to tweak what’s broken. From lean tricks to automation to training your crew, these strategies can turn your operation into a powerhouse. Designers, you’re crafting the blueprints for success. Decision-makers, you’re steering the ship. Together, you can make efficiency your superpower.
So, what’s your first move? Try one tip from this list and let me know how it goes—I’d love to hear your story. After all, efficiency isn’t just about saving time; it’s about building a future where your products shine brighter, faster, and smarter than the competition.