How to Avoid Common Defects in Electronics Manufacturing
Manufacturing electronics is a multifaceted process. From PCB design and sourcing components to assembly and testing, even the smallest mistake at any stage can cause defects that affect the entire production line.
2/15/20255 min read
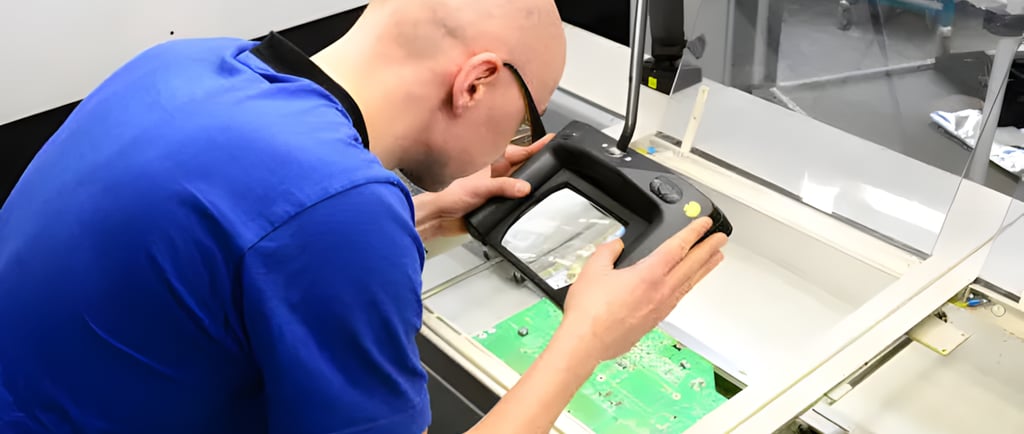
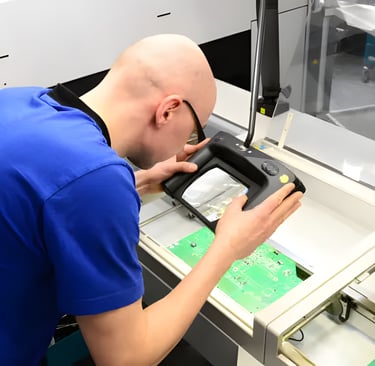
In electronics manufacturing, quality is everything. A single defect can lead to product failures, costly recalls, and significant damage to your company’s reputation. Whether you’re designing a new product or scaling up production, it’s critical to understand the common defects that can occur and how to prevent them.
Manufacturing electronics is a multifaceted process. From PCB design and sourcing components to assembly and testing, even the smallest mistake at any stage can cause defects that affect the entire production line. In this article, we'll take a deep dive into the most common manufacturing defects and explore actionable strategies to avoid them.
1. Understanding Common Defects in Electronics Manufacturing
Soldering Defects
Soldering is where many issues arise in electronics manufacturing. Problems like cold solder joints, excessive solder bridges, and insufficient solder can happen due to improper heating or poor solder paste application. These defects are not just technical—they can lead to weak electrical connections that affect performance and reliability.
Cold solder joints: These occur when there isn't enough heat, leading to weak connections.
Solder bridging: This happens when too much solder connects adjacent pads, causing short circuits.
Insufficient solder: When there isn’t enough solder, it leads to weak, unreliable connections.
Component Placement Errors
Misplaced components can lead to disastrous results. Whether it’s misalignment, reversed components, or simply placing the wrong part, these issues often stem from incorrect machine settings or outdated design files.
Misaligned components: If components don’t connect properly, they can cause total failure.
Reverse polarity errors: This happens with components like diodes or capacitors, leading to malfunctions.
Incorrect part placement: Mismatched footprints or inconsistent designs can cause major headaches in assembly.
PCB Issues
PCB defects can arise from multiple sources—whether it’s the design, materials, or manufacturing errors. These can lead to issues like delamination, broken traces, or poor surface finishes.
Delamination: This happens when the layers of the PCB separate, often due to excessive heat or moisture.
Broken traces: Mechanical stress or poor etching during fabrication can cause traces to break.
Poor surface finish: If the surface isn’t properly treated, soldering becomes difficult and unreliable.
Electrostatic Discharge (ESD) Damage
ESD is a silent but deadly enemy of electronics components. A small static charge can discharge onto a sensitive part and cause irreparable damage. This kind of damage is often invisible at first, but the component may fail prematurely later on.
Thermal Stress and Overheating Problems
Heat management is crucial in electronics design and manufacturing. If components are not properly designed to handle heat, it can lead to premature degradation, reducing the product’s lifespan.
Overheating components: Inadequate heat sinks or ventilation can cause components to overheat.
Thermal cycling failures: Repeated temperature fluctuations can weaken components over time.
Cold solder joints: These can also occur when the reflow soldering process is not evenly applied.
2. Best Practices to Avoid Manufacturing Defects
A. Optimized PCB Design and DFM (Design for Manufacturability)
One of the best ways to prevent defects is to ensure that the design phase is as smooth as possible. Working within Design for Manufacturability (DFM) guidelines is key to reducing errors before the production process even starts.
Trace width and spacing: Follow proper standards to prevent shorts and maintain signal integrity.
Industry-standard PCB layout: Stick to the guidelines to ensure the design can be easily manufactured.
Early manufacturer collaboration: By working with your manufacturers early in the process, you can catch potential issues before they become major problems.
B. High-Quality Materials and Components
Using low-quality or counterfeit components can be disastrous, even if everything else in the process is perfect. It’s essential to only use certified, reputable suppliers and thoroughly verify the authenticity of the parts you’re using.
Source from certified suppliers: Always choose reliable suppliers that follow quality assurance practices.
Verify authenticity: Implement checks to ensure that the components you receive are genuine and meet industry standards.
Reliable PCB materials: Ensure the materials used in the PCB can withstand environmental stresses and soldering temperatures.
C. Precision in Assembly and Soldering
Assembly and soldering precision is a make-or-break aspect of the manufacturing process. Automating these tasks and regularly calibrating equipment can minimize human error and lead to more consistent results.
Automate soldering processes: Automation reduces human error and ensures precision in the soldering process.
Calibrate equipment regularly: This ensures that the right temperatures are used during soldering.
Use high-quality solder paste: Choose the right solder paste and reflow profiles to ensure strong, reliable joints.
D. Proper Handling and Storage of Components
Components can be easily damaged during handling and storage, especially those sensitive to electrostatic discharge (ESD). Proper care is crucial to keeping them safe.
ESD-safe workstations: Make sure you have the right grounding equipment, such as wrist straps and mats, to prevent electrostatic damage.
Controlled storage environments: Store components in controlled environments to prevent oxidation and moisture buildup.
Proper packaging: Use packaging that minimizes the risk of mechanical damage during transport or storage.
E. Stringent Quality Control and Testing
One of the best ways to prevent defects from reaching the final product is by implementing rigorous testing and inspection protocols. Catching problems before they leave the factory saves time and money in the long run.
Automated Optical Inspection (AOI): This system detects defects in soldering and placement automatically, saving time and improving accuracy.
X-ray inspection: Useful for inspecting hidden solder joints in complex PCB assemblies like BGAs (Ball Grid Arrays).
Functional testing: This ensures that the assembled PCB operates correctly before it is sent out.
3. Implementing Process Improvements to Minimize Defects
Lean Manufacturing and Continuous Improvement
Manufacturers who embrace lean principles focus on eliminating waste and improving product quality. This approach encourages a continuous improvement mindset, which is essential for reducing defects.
Identify bottlenecks: Pinpoint areas in the production process that are causing delays or defects.
Standardize procedures: Consistent practices across batches help reduce variability and errors.
Foster continuous improvement: Encourage feedback loops and the sharing of knowledge across teams to optimize processes over time.
Data-Driven Defect Prevention
Using real-time data and analytics to monitor manufacturing processes can help detect patterns and predict where defects may occur. By making data-driven decisions, you can proactively fix problems before they affect the product.
Track defect rates: Keep an eye on trends and failure patterns to understand where improvements are needed.
Predictive maintenance: This approach helps anticipate equipment failures, reducing downtime and production delays.
AI anomaly detection: Machine learning can help identify anomalies in production, helping to detect potential issues before they escalate.
Employee Training and Skill Development
Even with all the right systems in place, human error remains a significant cause of manufacturing defects. Investing in regular training ensures that employees are equipped with the knowledge and skills to prevent mistakes.
Hands-on training: Offer practical training in areas like soldering, assembly, and inspection.
Cross-functional knowledge: Encourage teams to learn from each other to improve overall problem-solving.
Continuous updates: Keep training programs up to date with new industry standards and technologies.
Implementation of Automatic Tools
Automation is one of the best ways to reduce errors in electronics manufacturing. By incorporating automatic tools, manufacturers can achieve a level of precision and efficiency that is hard to match with manual labor.
Automated Optical Inspection (AOI): AOI systems can automatically check for visual defects in real-time.
Automated X-ray inspection (AXI): AXI is especially useful for detecting hidden defects in complex assemblies.
Robotic pick-and-place: These machines ensure components are placed correctly, reducing human error.
Automated functional testing: This ensures each product performs as expected before it leaves the factory.
AI-driven predictive maintenance: AI tools can monitor equipment in real-time, predicting potential failures before they cause downtime.
Conclusion
Preventing defects in electronics manufacturing requires a comprehensive approach—good design, high-quality materials, precise assembly, and strong quality control. By addressing issues early in the process and continuously improving manufacturing practices, you can improve product reliability and customer satisfaction.
For engineers and decision-makers, taking a proactive approach to defect prevention is not just about minimizing losses; it’s about creating a reputation for excellence. By staying ahead of potential issues, your company can consistently deliver high-quality products that perform flawlessly from production to the end-user.
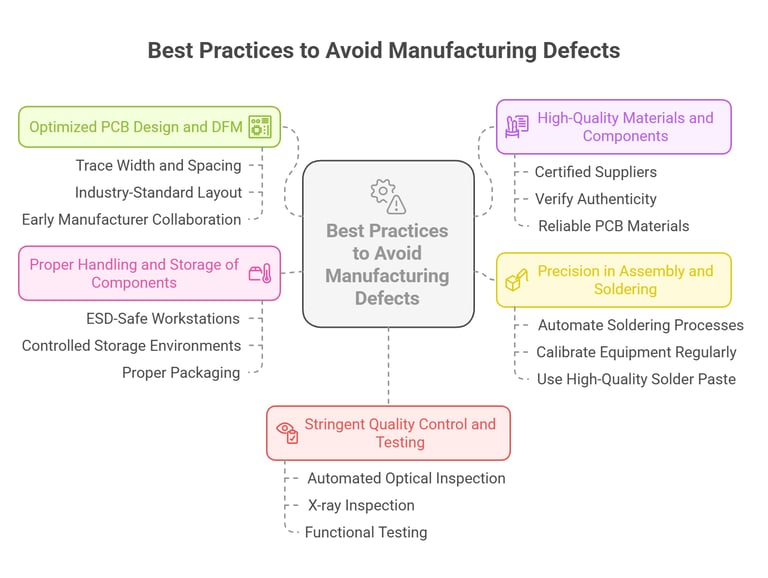
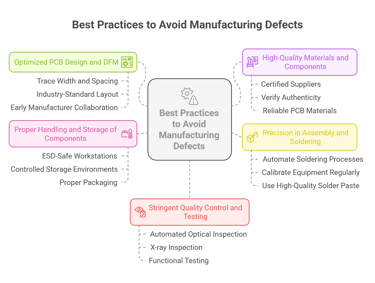