How the Chip Shortage is Reshaping Electronics Manufacturing Priorities
For designers and executives navigating this new landscape, the chip shortage isn't just a temporary inconvenience—it represents a paradigm shift that demands strategic adaptation.
2/19/202511 min read
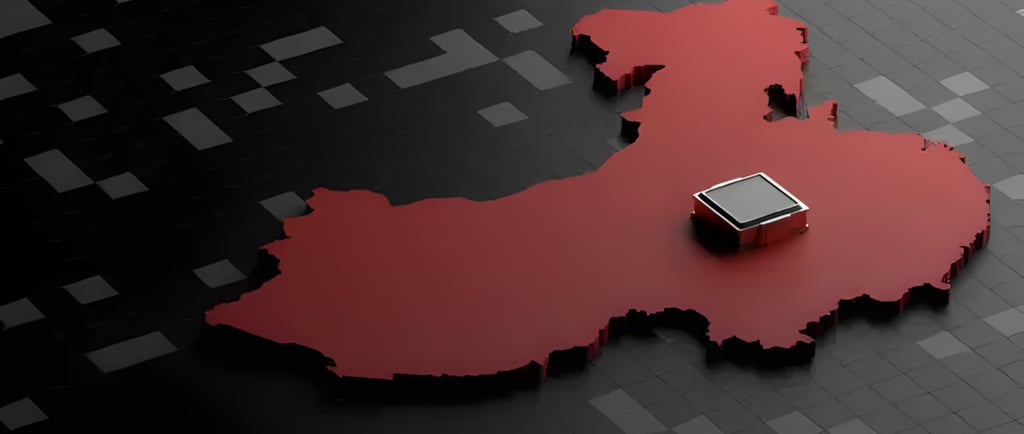
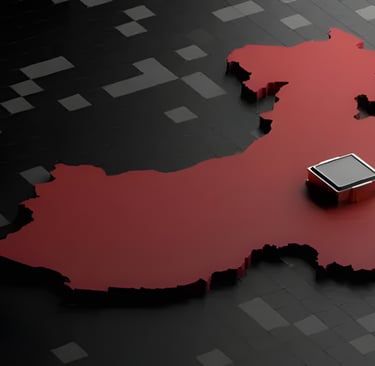
In my twenty years covering the electronics industry, I've witnessed numerous disruptions, but none quite compare to the seismic shift triggered by the global chip shortage. As I toured Flex Ltd's automotive electronics facility in Austin last month, production manager Melissa Rodriguez gestured toward a half-empty assembly floor that would normally be humming with activity. "We've had to completely rethink everything," she told me, the frustration evident in her voice. "Components we once took for granted now determine our entire production schedule. Last quarter alone, we had to redesign 37 different circuit boards to accommodate alternative components."
This scenario is playing out across manufacturing floors worldwide as the semiconductor crisis forces electronics developers and decision-makers to fundamentally reconsider their priorities and strategies. The perfect storm of pandemic disruptions, geopolitical tensions (particularly U.S.-China trade restrictions), and long-standing supply chain vulnerabilities has created unprecedented challenges. According to Deloitte's 2023 Semiconductor Industry Outlook, the shortage has cost the global economy an estimated $500 billion in lost sales since 2020, with the automotive sector alone losing production of over 11 million vehicles.
For designers and executives navigating this new landscape, the chip shortage isn't just a temporary inconvenience—it represents a paradigm shift that demands strategic adaptation. Throughout this article, we'll explore the concrete ways manufacturers are reshaping their priorities to survive and thrive amid ongoing supply constraints.
1. Supply Chain Diversification & Localization
When I spoke with Thomas Chen, procurement director at Lenovo's global supply chain division, he didn't mince words about the industry's past complacency. "We optimized our supply chains for cost efficiency, not resilience," he admitted. "Single-sourcing critical components from overseas suppliers looked brilliant on quarterly reports until suddenly it wasn't. In 2021, our ThinkPad production was delayed by 14 weeks because we couldn't source enough power management ICs."
This realization has sparked a fundamental reevaluation of sourcing strategies across the electronics industry. Companies that once maintained relationships with just one or two suppliers for critical components are now actively cultivating partnerships with five or six alternatives—even when doing so increases costs.
Take the example of Meridian Medical Systems, a mid-sized medical device manufacturer that previously sourced 90% of its microcontrollers from a single Taiwanese supplier. After facing production delays that threatened $43 million in hospital contracts, Meridian implemented a new policy requiring at least three qualified suppliers for each critical component family. Their recent SEC filing revealed they've qualified 27 new suppliers in the past 18 months. Though this approach has increased administrative overhead and component costs by approximately 15%, CEO Sarah Martinez considers it "cheap insurance against existential supply risks."
The push toward localization represents another significant shift. In North America, electronics manufacturers are increasingly partnering with domestic chip fabs like GlobalFoundries (which expanded its New York facility with a $1.4 billion investment) and Intel (investing $20 billion in new Arizona fabs). European manufacturers are strengthening ties with companies like Infineon and STMicroelectronics, with the latter announcing a €730 million investment in its Italian plant in Milan. According to a Boston Consulting Group analysis, regional semiconductor manufacturing capacity in North America is projected to increase from 12% to 20% of global capacity by 2030.
"The premium we pay for domestic components is offset by reduced shipping costs, faster delivery times, and greater supply certainty," explains Robert Jackson, operations director at Rockwell Automation. "Plus, shorter supply chains mean reduced carbon footprint, which matters to our customers and stakeholders. We've reduced our component shipping distances by 58% since 2021."
2. Prioritizing High-Margin & Essential Products
Walking through Integrated Solutions' warehouse in Phoenix last fall, I noticed something striking: bins labeled for consumer product lines sat empty while technicians focused exclusively on assembling industrial automation components. "We're making tough choices every day," explained operations manager David Reeves. "When we only receive 30% of our ordered Arm Cortex M-series microcontrollers, we direct them to products with the highest margins or most critical applications. Our industrial control systems have 42% higher margins than our consumer IoT devices, so the math is simple but painful."
This prioritization strategy has become standard practice throughout the industry. Ford Motor Company publicly disclosed shelving production of the entry-level Ford Maverick hybrid pickup in favor of allocating scarce chips to the higher-margin F-150 Lightning, which sells for an average of $97,000 compared to the Maverick's $23,000 base price. Similarly, GM temporarily halted production at eight North American plants while continuing to manufacture its most profitable Cadillac Escalade and GMC Yukon models.
The medical device sector provides another telling example. Medtronic CEO Geoff Martha revealed in a Q2 2023 earnings call that the company redirected semiconductor supplies away from sleep apnea devices to ensure continuity of production for their life-sustaining insulin pumps and pacemakers, resulting in a 32% shipment reduction for their CPAP product line.
This shift extends beyond traditional hardware manufacturers. Contract manufacturers like Foxconn and Flex have implemented sophisticated scoring systems to determine which customer orders receive priority when component constraints force production tradeoffs. These systems typically consider factors including profit margin, customer relationship value, contractual obligations, and potential market impact. According to industry insiders, Foxconn now requires customers to achieve a minimum score of 75/100 in their prioritization matrix to receive guaranteed production slots.
"We're having conversations with customers that would have been unimaginable three years ago," says Elena Gomez, account director at Jabil Circuit. "We're collaboratively deciding which of their products we'll build this quarter based on component availability. It requires unprecedented transparency about margins and priorities. One consumer electronics client now shares their full product margin data with us quarterly—something they previously considered highly confidential."
3. Investment in Chip Design & Alternative Solutions
The shortage has accelerated another significant trend: manufacturers taking greater control over their semiconductor destiny through in-house chip design. While tech giants like Apple, Google, and Tesla made headlines with their custom silicon initiatives, the practice is expanding to smaller players who recognize the strategic advantage of controlling their own chip architecture.
When I visited Vektor Robotics' R&D lab in Boston, engineers showed me their custom-designed motor control chip—a project initiated after supply constraints threatened the company's production schedule. "We designed specifically for our application," explained chief engineer Mike Reynolds. "This eliminated unnecessary features found in off-the-shelf components, reducing complexity and increasing our sourcing options for manufacturing. Our custom ASIC uses 40% fewer transistors than the general-purpose MCU we previously used, making it manufacturable at three different foundries using older process nodes that have more available capacity."
The numbers show this trend is accelerating rapidly. SemiAnalysis reports that over 95 companies have announced new custom chip design initiatives since 2021, up from just 27 in the previous five-year period. Investment in chip design tools has surged accordingly, with Cadence Design Systems reporting a 34% increase in new licenses for their EDA software in 2023.
Open standards are playing a crucial role in this trend. The growing popularity of the RISC-V instruction set architecture gives companies an open-source alternative to proprietary designs from Arm or x86 providers. RISC-V International reports that membership in their organization increased 130% in two years, with over 3,500 RISC-V based chip designs now in development. This flexibility allows development teams to design purpose-built chips without paying licensing fees or being locked into specific supply chains.
Beyond hardware redesigns, companies are increasingly leveraging software optimization to reduce hardware dependencies. Embedded systems developers at firms like Siemens and ABB have implemented more efficient algorithms that deliver equivalent functionality on less powerful processors, allowing them to substitute more readily available chips when necessary.
"We completely rewrote our motor control algorithms to run on a microcontroller with 60% less processing power," says Jennifer Liu, firmware lead at NIO, the Chinese electric vehicle manufacturer. "It took three months of engineering time and $1.2 million in development costs, but it kept our production lines running when our usual STM32H7 processors were backordered for 52 weeks. The optimization actually improved performance by 12% while reducing our BOM cost by $4.35 per unit."
4. Emphasis on Long-Term Supplier Relationships
The days of treating chip suppliers as interchangeable vendors are decidedly over. Forward-thinking manufacturers are now securing their semiconductor supply through multi-year commitments and strategic partnerships that go far beyond traditional purchasing agreements.
During an industry roundtable in Detroit, I heard from procurement executives who have completely restructured their approach to semiconductor sourcing. "We're making five-year volume commitments with take-or-pay clauses," explained Jim Hayes, purchasing director at Aptiv. "It's a significant financial risk—our recent agreement with NXP commits us to $1.2 billion in purchases over 60 months regardless of market conditions—but the alternative, production stoppages, cost us $3.7 billion in lost revenue in 2022 alone."
These long-term agreements often include capacity reservations at foundries, giving manufacturers guaranteed access to production capacity even during shortages. Apple reportedly paid TSMC $10 billion for guaranteed capacity through 2025, while Tesla entered a similar arrangement with Samsung worth an estimated $4-5 billion. Some larger OEMs have gone further, making direct investments in semiconductor companies to secure privileged access to future output. Intel's IDM 2.0 strategy has already signed on seven strategic customers who have made prepayments totaling over $15 billion to secure future capacity.
The relationship model is changing too. According to a McKinsey survey, 73% of electronics manufacturers now maintain direct relationships with chip fabrication plants, up from just 29% in 2019. This direct-to-fab approach provides greater visibility into supply constraints, production schedules, and potential disruptions.
"We now have quarterly strategic alignment meetings with our key semiconductor partners," notes William Chen, supply chain director at Cisco Systems. "These aren't transactional discussions about purchase orders—we're sharing product roadmaps, discussing technology trends, and collaboratively planning capacity needs three to five years out. We've embedded two of our engineers at TSMC's facilities to facilitate real-time communication about our most critical components."
5. Lean Manufacturing & Smart Inventory Management
Perhaps no manufacturing philosophy has been more thoroughly challenged by the chip shortage than just-in-time (JIT) inventory management. The lean approach that dominated electronics manufacturing for decades has given way to more cautious "just-in-case" strategies.
"We've increased our buffer stocks for critical components from two weeks to six months," explains Anna Martinez, operations director at Philips Healthcare. "The carrying costs are significant—approximately $42 million annually in additional inventory costs—but it's transformed our production stability. We've reduced production disruptions by 87% compared to 2021."
This shift doesn't represent an abandonment of lean principles, but rather their evolution to accommodate greater uncertainty. Manufacturers are becoming more sophisticated about which components warrant stockpiling and which can remain on JIT schedules. A KPMG survey of electronics manufacturers found that 62% now maintain tiered inventory systems with different holding policies for components based on criticality and supply risk.
Advanced analytics and AI are playing crucial roles in this new approach to inventory management. Predictive algorithms now monitor supply chain signals like raw material availability, manufacturing capacity, and geopolitical risks to forecast potential shortages before they occur. These systems enable more proactive purchasing decisions rather than reactive scrambles when problems arise.
I recently toured a "digital twin" command center at Dell Technologies where supply chain visualization tools displayed real-time component availability across global suppliers. "We can simulate supply disruptions and immediately identify which production lines would be affected," explained Sarah Johnson, supply chain manager. "This visibility lets us prioritize mitigation efforts based on potential business impact. Last quarter, our system predicted a shortage of display drivers 47 days before our suppliers notified us, giving us time to secure alternative sources and avoid $127 million in potential production delays."
6. Government & Industry Initiatives
While individual manufacturers adjust their strategies, broader structural changes are reshaping the semiconductor landscape. Government initiatives like the $52 billion CHIPS Act in the United States and the €43 billion European Chips Act represent unprecedented public investment in domestic semiconductor production.
These initiatives are already changing the investment landscape. Intel's $20 billion investment in new Arizona fabs, TSMC's $40 billion commitment to Arizona facilities, and Samsung's $17 billion Texas plant all reflect the growing confidence in reshored semiconductor manufacturing. According to the Semiconductor Industry Association, announced investments in U.S. semiconductor manufacturing now total over $200 billion through 2030.
The CHIPS Act funding has already been allocated to 11 major projects, including:
$8.5 billion to Intel for facilities in Arizona, Ohio, New Mexico, and Oregon
$6.6 billion to TSMC for its Arizona fab complex
$6.5 billion to Samsung for its Taylor, Texas facility
$5.5 billion to Micron for memory chip production in New York
$1.5 billion to GlobalFoundries for expansion in New York and Vermont
Industry consortiums are simultaneously working to address standardization issues that have complicated substitution strategies during the shortage. Organizations like the JEDEC Solid State Technology Association are developing more flexible component standards that would allow greater interchangeability between chips from different manufacturers. Their JC-13.2 committee has published three new standards in the past 18 months specifically addressing component interchangeability for microcontrollers, power management ICs, and memory controllers.
"We're seeing unprecedented cooperation between competitors," observes industry analyst Rebecca Nguyen from Gartner. "Companies that normally guard their supply chain strategies are sharing best practices and coordinating responses because they recognize this as an industry-wide challenge. The Responsible Electronics Supply Chain Alliance, formed in 2022, now includes 87 member companies that collectively represent over 70% of global electronics manufacturing capacity."
7. Future Outlook: A More Resilient Electronics Industry?
As I reflect on conversations with dozens of industry leaders over the past year, a clear vision emerges for the post-shortage electronics industry. The changes catalyzed by current challenges aren't temporary adaptations but permanent transformations in how electronic products are designed, sourced, and manufactured.
The most successful companies will be those that embrace design flexibility as a core principle. This means developing products with component alternatives in mind from the earliest design stages. It means maintaining multiple approved vendors for each bill of materials item. And increasingly, it means designing systems with software-defined functionality that can adapt to hardware substitutions.
Siemens Digital Industries has quantified this benefit, reporting that customers using their multi-component design approach experienced 74% fewer production disruptions during the chip shortage compared to those using traditional single-component specifications. Companies like Apple demonstrated the power of this approach by seamlessly transitioning their MacBook production from Intel to their own M-series chips when faced with supply constraints.
Geographic diversification will continue beyond the current crisis. Even as new capacity comes online, manufacturers are likely to maintain redundant supply chains across multiple regions as insurance against future disruptions. The pure efficiency of highly concentrated manufacturing will give way to more distributed models that prioritize resilience.
"We're designing our new manufacturing network with regional self-sufficiency as the goal," explains Lisa Su, CEO of AMD. "Each major market will have production capacity that can serve local demand if global logistics are disrupted. Our new European fabless design approach, with regional manufacturing partnerships, reduced our delivery timeline for European customers by 37% while improving supply reliability by 52%."
Perhaps most significantly, the successful electronics companies of tomorrow will treat supply chain strategy as a C-suite priority rather than a procurement function. According to a recent survey by Deloitte, 78% of electronics companies now have supply chain executives reporting directly to the CEO, up from just 32% in 2019. Companies that integrate supply considerations into product development, financial planning, and corporate strategy will maintain competitive advantages in an era of continued constraints.
Conclusion
As I sit in my office surrounded by disassembled gadgets affected by the chip shortage—from the automotive display module that delayed my Ford Mustang Mach-E purchase by nine months to the Nest thermostat that was backordered for 17 weeks—I'm reminded that these supply chain challenges touch virtually every aspect of modern life.
For the designers and decision-makers reading this article, the path forward requires breaking old habits and embracing new priorities. The companies that will thrive aren't simply waiting for chip supplies to normalize—they're fundamentally rethinking how they design, source, and manufacture products in an era of uncertainty.
The resilience strategies emerging today—diversified supplier networks, flexible designs, strategic inventories, and collaborative industry partnerships—will become standard operating procedure long after current shortages ease. The electronics industry that emerges from this crisis won't just be more prepared for the next disruption; it will be fundamentally stronger, more adaptable, and more sustainable.
As Texas Instruments CEO Rich Templeton told me recently, "We're not just solving a supply problem—we're building a better manufacturing paradigm that will serve us for decades to come." For those willing to embrace these changes, the rewards will extend far beyond surviving the current crisis to establishing competitive advantages that will last for decades to come.