How Much Does Injection Molding Cost? A Detailed Breakdown
Whether you’re designing a sleek wearable device or a rugged industrial controller, understanding injection molding costs can make or break your timeline and bottom line.
2/22/20256 min read
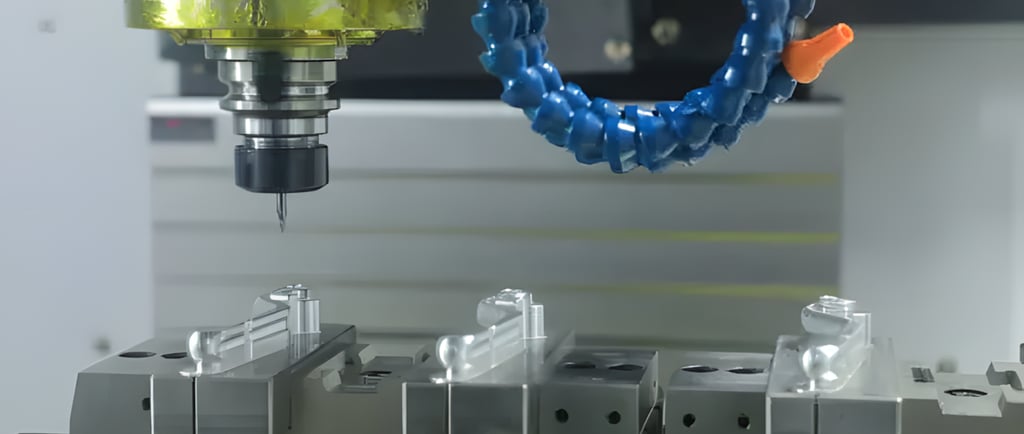
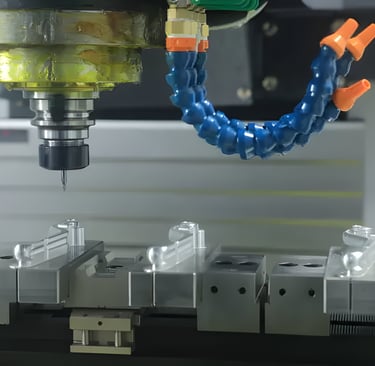
If you’re a designer or decision-maker in electronics development, you’ve likely faced the moment where your brilliant circuit board design needs a real-world home—an enclosure, a connector, or maybe a custom housing. That’s where injection molding comes in, the go-to manufacturing process for producing precise, durable plastic parts. But here’s the million-dollar question (or maybe the $10,000 question): How much does it actually cost?
I’ve been around enough product development cycles to know that “it depends” isn’t the answer you want to hear. So, let’s break it down—really break it down—into something tangible you can use to budget your next project. Whether you’re designing a sleek wearable device or a rugged industrial controller, understanding injection molding costs can make or break your timeline and bottom line. In this article, we’ll walk through the factors driving those costs, throw in some real-world examples, and share tips to keep your wallet from crying. Ready? Let’s get started.
Overview of Injection Molding Costs
First things first: injection molding isn’t cheap, but it’s not always outrageously expensive either. Costs can range anywhere from $1,000 for a small, simple project to over $100,000 for a high-volume, complex run. That’s a big spread, right? The reason is simple—every project is unique. A tiny headphone jack cover isn’t going to hit your budget the same way a multi-part IoT device enclosure will.
Think of injection molding costs in two buckets: upfront costs (mostly the mold itself) and per-unit production costs. The mold is your big investment—it’s like buying the canvas and brushes before you paint. Once it’s made, the per-unit cost is more like buying paint tubes—relatively affordable, especially as you scale up. For electronics folks, this split is critical because your production volume (50 prototypes vs. 50,000 consumer units) changes everything.
Key Factors Influencing Injection Molding Costs
Let’s peel back the layers. Here’s what’s really driving the price tag on your next injection-molded part.
Part Design Complexity
You know that moment when you sketch a part with a dozen undercuts, snap-fits, and tight tolerances because it’s “perfect” for your PCB? Yeah, that’s going to cost you. The more complex your design, the trickier (and pricier) the mold becomes. A simple rectangular enclosure might be a breeze, but add some curved surfaces or thin walls for a lightweight wearable, and the moldmaker’s job gets harder. For example, a basic housing might run $2,000 for the mold, while a multi-feature connector with tight specs could push that to $15,000 or more.
Mold Material and Construction
The mold itself is the heart of the operation, and it’s not a one-size-fits-all deal. For short runs—like prototyping a new sensor casing—you might go with an aluminum mold. It’s softer, quicker to machine, and costs $1,000 to $5,000. But if you’re launching a consumer electronics product with a 100,000-unit run, you’ll want a steel mold. Steel’s tougher, lasts longer, and can handle the wear and tear of high volumes, but it’ll set you back $10,000 to $100,000 depending on size and complexity. I’ve seen teams agonize over this choice—cheap now or durable later? It’s a classic trade-off.
Material Selection
Electronics parts need the right plastic. ABS is a solid, affordable choice for enclosures—think $2–$3 per pound. Want something tougher like polycarbonate for a rugged device? That’s more like $4–$6 per pound. And if your wearable needs to be flame-retardant or UV-resistant, additives bump that up further. I once worked on a project where we switched from a basic resin to a specialty blend mid-design. The material cost doubled, but it saved us from failing safety certifications. Lesson learned: spec your material early.
Production Volume
Here’s where the math gets fun. Let’s say your mold costs $20,000. For 100 units, that’s $200 per part just to break even on the mold—plus material and machine time. But crank that up to 10,000 units, and the mold cost drops to $2 per part. For electronics, this is huge. Prototyping a few dozen units for testing? Expensive. Mass-producing a smart home gadget? Way more cost-effective. Volume is your leverage.
Cycle Time and Machine Size
Bigger parts—like a tablet housing—need bigger machines with higher tonnage, which means higher hourly rates ($50–$150/hour). Smaller parts, like a USB port cover, use smaller presses and shorter cycles, keeping costs down. Cycle time matters too. If your part cools slowly or needs extra steps, you’re racking up machine time. I’ve seen teams shave seconds off cycles with clever design tweaks—it’s like finding loose change in the couch cushions.
Labor and Location
Where your mold is made and parts are produced makes a difference. In the U.S. or Europe, labor rates are higher, and you might pay a premium for quality and proximity—think $50–$100/hour for skilled work. In Asia, it’s cheaper, often $10–$30/hour, but shipping and communication can add headaches. Automation helps, but for small runs or custom finishes, human hands still play a role. I’ve dealt with both—local for speed, overseas for scale. It’s a balancing act.
Additional Services
Don’t forget the extras. Prototyping a few parts before full production? That’s $500–$2,000. Need a glossy finish or custom painting for your device? Add a few cents per unit. Packaging matters too—electronics often need protective inserts, which can tack on costs. These “little” things pile up if you’re not careful.
Typical Cost Breakdown
Let’s put some numbers to this. Here are three scenarios tailored to electronics development.
Low-Cost Scenario: Prototyping a Sensor Housing
Details: Simple rectangular enclosure, 500 units, aluminum mold, ABS plastic.
Mold Cost: $2,000.
Production Cost: $2 per unit (material + machine time).
Total: $3,000 ($6/unit).
Use Case: Perfect for testing a new IoT sensor before scaling up.
Mid-Range Scenario: Consumer Device Enclosure
Details: Moderately complex housing with snap-fits, 10,000 units, steel mold, polycarbonate.
Mold Cost: $25,000.
Production Cost: $1.50 per unit.
Total: $40,000 ($4/unit).
Use Case: Think a smart thermostat or fitness tracker hitting the market.
High-End Scenario: Industrial Controller
Details: Complex multi-part housing, 100,000 units, high-grade steel mold, flame-retardant resin.
Mold Cost: $80,000.
Production Cost: $0.70 per unit.
Total: $150,000 ($1.50/unit).
Use Case: A rugged controller for factory automation.
Here’s a quick table to visualize it:
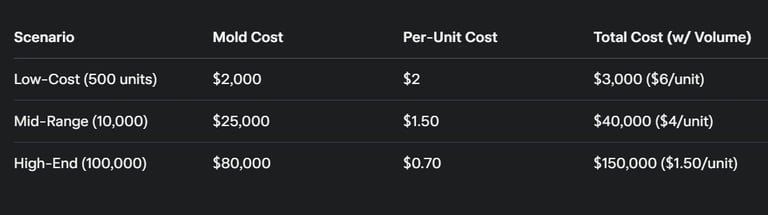
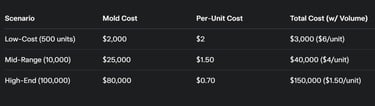
Hidden Costs to Watch Out For
Just when you think you’ve got it figured out, surprises pop up. Mold maintenance is one—steel lasts longer, but even it needs repairs after heavy use ($500–$5,000 over time). Shipping molds or finished parts can sting, especially internationally. Design changes midstream? Ouch—reworking a mold might cost thousands. And don’t skip quality control—testing for fit or durability adds expense but saves you from recalls. I’ve seen teams scramble when they ignored these. Plan ahead.
How to Reduce Injection Molding Costs
You’re not powerless here. Here’s how to keep costs in check:
Simplify Your Design: Fewer features mean a cheaper mold. Can that extra rib wait for version 2?
Pick the Right Mold: Aluminum for prototypes, steel for production. Match it to your volume.
Choose Smart Materials: ABS works fine for many enclosures—don’t over-spec unless you need to.
Scale Up: More units = lower per-part costs. Push for bigger runs if you can.
Collaborate Early: Work with your manufacturer to tweak designs for efficiency. They’ve seen it all.
I once cut 20% off a mold cost by flattening a curved edge. It didn’t change the function but made machining a breeze. Small wins add up.
Getting an Accurate Quote
Want a real number? Here’s the playbook:
Send detailed drawings—3D CAD files are gold.
Specify your volume, material, and tolerances.
Ask for a breakdown—mold vs. production costs.
Get multiple quotes—vendors vary.
Talk to your manufacturer early, even during design. They’ll spot issues you might miss. Most turn quotes around in a few days, and production can start in weeks if you’re ready. It’s like dating—communication is everything.
Conclusion
Injection molding costs can feel like a rollercoaster, but they don’t have to be a mystery. From mold complexity to material choices to production volume, every decision shapes the price tag. For electronics designers and decision-makers, it’s about finding that sweet spot—quality parts that don’t bankrupt the project. Whether you’re prototyping a gadget or launching a bestseller, start with a clear plan and lean on your manufacturer’s expertise.
So, what’s your next step? Sketch out that part, crunch some numbers, or call up a vendor. The sooner you dig in, the sooner your design becomes reality. Got questions? I’d love to hear them—drop a comment or reach out. Let’s make something great.