How Injection Molding Supports Mass Production Efficiency
How do we make thousands of these without breaking the bank or missing deadlines? For designers and decision-makers in electronics development, this is where injection molding steps into the spotlight. It’s not just a manufacturing process; it’s a lifeline for scaling production efficiently.
2/23/20256 min read
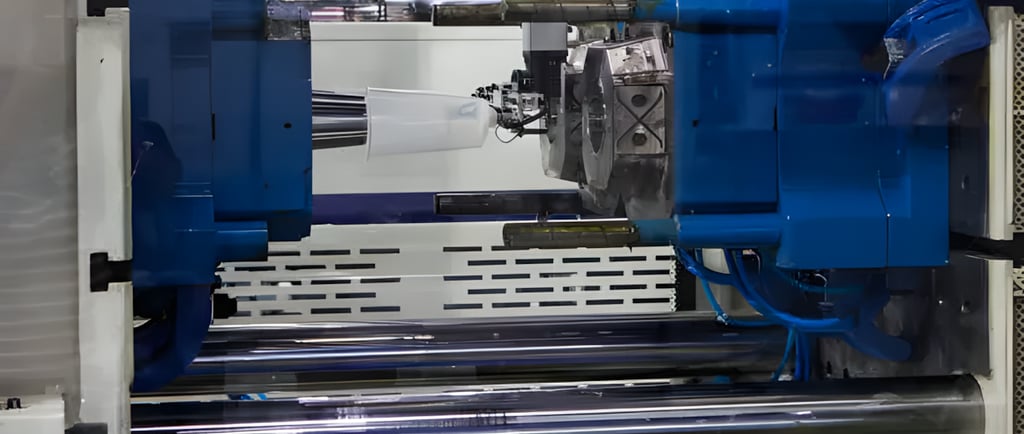
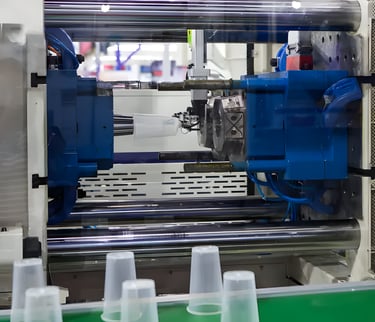
Imagine you’re sitting in a meeting, coffee in hand, sketching out the next big thing in electronics—a sleek new wearable, maybe, or a game-changing IoT device. The ideas are flowing, the prototypes are promising, but then the inevitable question hits: How do we make thousands of these without breaking the bank or missing deadlines? For designers and decision-makers in electronics development, this is where injection molding steps into the spotlight. It’s not just a manufacturing process; it’s a lifeline for scaling production efficiently. Let’s dive into how injection molding empowers your team to turn concepts into mass-produced realities—fast, precise, and cost-effective.
Understanding Injection Molding
If you’re new to the game, injection molding might sound like some industrial magic trick. In a way, it kind of is. Picture this: you take a material—say, a tough thermoplastic like ABS or polycarbonate—melt it down into a gooey, workable state, and shoot it into a custom-designed mold under high pressure. Once it cools and hardens, you pop it out, and voilà: a perfectly shaped component, ready to house your circuit boards or snap into your device’s casing. Rinse and repeat—thousands of times, if you need.
The process itself is straightforward but brilliant. It starts with choosing the right material (more on that later), designing a mold that’s basically a negative of your part, injecting the molten stuff, letting it cool, and ejecting the finished piece. For electronics, where tiny tolerances and durability matter, this precision is a game-changer. You’ve probably seen injection molding at work without realizing it—those smooth plastic enclosures on your smart thermostat or the buttons on your TV remote? Yep, that’s the stuff.
In the electronics world, injection molding isn’t just a niche tool—it’s everywhere. From phone cases to connector housings to intricate internal mounts, it’s the go-to for producing parts that need to be both functional and scalable. And that’s where the real magic happens: scaling.
Key Benefits of Injection Molding for Mass Production
Let’s get into the meat of it—why injection molding is your best friend when you’re staring down a production run of 10,000 units (or a million). First off, it’s precise. I’m talking tolerances down to fractions of a millimeter, every single time. When you’re designing a housing for a delicate PCB or a snap-fit cover that needs to align perfectly, consistency isn’t optional—it’s everything. Injection molding delivers that repeatability, so your 10,000th part is as spot-on as your first.
Then there’s speed. Once the mold is ready, the cycle time is lightning-fast—sometimes as quick as 15-30 seconds per part. For a designer, that means your prototype-to-market timeline shrinks dramatically. Imagine telling your boss, “Yeah, we can have a million enclosures ready by Q3.” That’s the kind of confidence injection molding brings to the table.
Material versatility is another big win. Electronics folks like you have a buffet of options: ABS for toughness, polycarbonate for clarity and heat resistance, or even metal-filled plastics for EMI shielding. Whatever your spec sheet demands, there’s a material that fits. And here’s a bonus: injection molding is stingy with waste. The process uses just what it needs, trimming excess costs and keeping your green credentials intact—something your sustainability team will appreciate.
Scaling Production with Injection Molding
Now, let’s talk scaling—the part that keeps decision-makers awake at night. You’ve got a hit design, orders are piling up, and suddenly you need to go from a hundred units to a hundred thousand. Injection molding makes that leap possible without sending your budget into a tailspin.
Sure, there’s an upfront cost to design and build the mold. It’s not cheap—think thousands of dollars, depending on complexity. But here’s the kicker: once that mold is done, the per-unit cost drops like a stone as volume rises. For electronics, where margins can be tight, that’s a lifeline. I’ve seen teams balk at the initial tooling price, only to realize it pays for itself tenfold when they hit high-volume production.
Automation is another ace up the sleeve. Pair injection molding with robotic arms and conveyor systems, and you’ve got a lean, mean production machine. Less human labor, fewer errors, and a throughput that keeps your supply chain humming. For a decision-maker, that’s peace of mind—knowing your factory can churn out parts 24/7 without missing a beat.
What about tweaking designs on the fly? Say your wearable’s clip isn’t quite ergonomic—you can tweak the mold and keep rolling without scrapping the whole operation. That flexibility is gold when you’re racing to beat a competitor to market. Take Fitbit, for example. Their sleek, mass-produced bands and casings? Injection molding helped them scale from startup to household name, churning out millions of units with pinpoint accuracy.
Cost Efficiency and Economic Impact
Let’s crunch some numbers—because I know you’re the type who loves a good ROI story. Picture a typical electronics part: a small housing, maybe 50 grams of plastic. With injection molding, once the mold’s paid off (say, after 5,000 units), your cost per part might drop to pennies. Compare that to CNC machining or 3D printing at scale, and it’s no contest. The economics of injection molding shine brightest when you’re pushing volume.
Labor costs take a hit, too. Automation handles the heavy lifting, so you’re not paying a small army to babysit the process. And those molds? They’re built to last—hundreds of thousands of cycles, sometimes millions, with minimal upkeep. For a decision-maker, that’s a predictable cost structure you can bank on, freeing up cash for R&D or marketing.
I once chatted with a product manager at a mid-sized electronics firm. They’d been outsourcing low-volume runs, bleeding money on shipping and delays. Switching to in-house injection molding cut their costs by 40% and slashed lead times. That’s the kind of story that gets a CFO’s attention.
Challenges and Solutions in Injection Molding for Mass Production
It’s not all sunshine and roses, though—let’s be real. That upfront tooling cost I mentioned? It’s a hurdle, especially for startups or small runs. But here’s the fix: plan for the long game. If you know demand will ramp up, the investment makes sense. Spread it across a million units, and it’s a rounding error.
Design complexity can trip you up, too. A mold for a simple box is one thing; a multi-part housing with undercuts and threads? That’s a job for a seasoned engineer. Luckily, modern CAD tools and simulation software take the guesswork out of it. Work with a good molding partner, and they’ll spot issues before the first shot’s fired.
Lead time’s another sticking point. Building a mold can take weeks, even months for intricate electronics parts. Miss your window, and the market moves on. The workaround? Start early—get your tooling in motion while you’re still testing prototypes. Once it’s ready, you’ll be pumping out parts faster than you can say “supply chain bottleneck.”
The Future of Injection Molding in Mass Production
So, where’s this all headed? For electronics designers like you, the future’s bright. Innovations are popping up left and right—3D-printed molds are cutting lead times, letting you test concepts without committing to steel. New materials, like bio-based plastics or conductive polymers, are opening doors to greener, smarter devices. Imagine a wearable that’s recyclable and shields RF interference— injection molding’s making it happen.
Sustainability’s a big driver, too. Energy-efficient machines and closed-loop recycling are shrinking the carbon footprint. Your customers care about that, and so should you—it’s a selling point. And as global demand for electronics skyrockets (hello, 5G and IoT), injection molding’s scalability keeps you ahead of the curve. It’s not just about meeting today’s orders; it’s about owning tomorrow’s market.
Conclusion
Injection molding isn’t sexy—it’s not the part of your job that lands you on a magazine cover. But for designers and decision-makers in electronics, it’s the unsung hero that turns your vision into a million shipped units. It’s fast, precise, and scales like a dream, all while keeping costs in check. Whether you’re sketching the next must-have gadget or crunching numbers for the board, this process is your ticket to staying competitive.
So, next time you’re brainstorming over that lukewarm coffee, think about injection molding. Explore it, test it, lean into it. Because in the high-stakes world of electronics development, efficiency isn’t just an advantage—it’s survival.