How Injection Molding Enables Lightweight Product Design
Chances are, injection molding played a starring role in bringing that lightweight wonder to life. For designers and decision-makers in electronics development, this manufacturing process isn’t just a tool—it’s a game-changer.
2/24/20255 min read
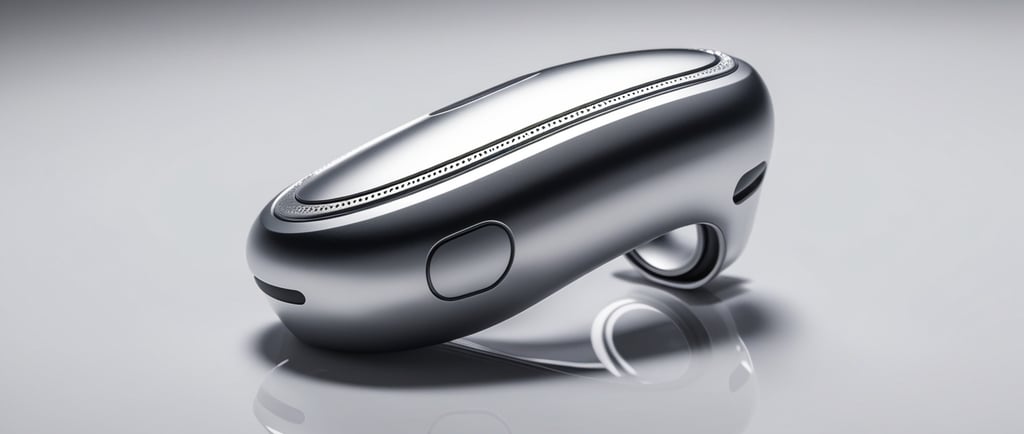

Picture this: you’re unboxing a shiny new fitness tracker. It’s packed with sensors, a vibrant screen, and a battery that lasts days—yet it’s so light you barely feel it on your wrist. Or maybe you’re marveling at a drone that zips through the sky, nimble as a bird. What’s the secret sauce? More often than not, it’s injection molding. For us designers and decision-makers in electronics development, this manufacturing process isn’t just a tool—it’s a superpower. And it’s not just our world; industries like aerospace and automotive are leaning on it hard. Let’s unpack how injection molding fuels lightweight design—and why it’s a game-changer with real-world proof.
Understanding Injection Molding and Lightweight Design
At its core, injection molding is like a high-tech kitchen gadget: molten plastic or composites get squirted into a mold, cooled, and out pops a precision part. It’s the backbone of everything from phone cases to car dashboards. But here’s the kicker for electronics: it’s a master at lightweighting. Reducing weight without losing strength is our obsession—lighter devices mean better portability, longer battery life, and happier customers. Injection molding delivers by letting us craft parts with surgical precision, slashing mass while keeping performance intact. Think of it as the Swiss Army knife of manufacturing.
Techniques That Drive Lightweight Innovation
How does it work its magic? It’s all about the tricks up its sleeve. Let’s say you’re designing a next-gen smart speaker—every ounce matters. Here’s how injection molding pulls it off:
Material Selection: Forget heavy metals. We’ve got high-performance polymers like polycarbonate (used in bulletproof glass!) or polyamide, plus composites with carbon fiber. These cut weight by up to 50% compared to steel, per a 2023 Plastics Technology report, while matching durability.
Thin-Wall Molding: This technique churns out walls as thin as 0.5 mm—think razor-thin laptop shells. A study from the Society of Plastics Engineers found it can reduce part weight by 20-30% without buckling under stress.
Foam Injection Molding: By injecting gas (like nitrogen) into the mix, we create micro-bubbles that drop density by 10-15%, according to SABIC’s material data. It’s how companies make lightweight yet sturdy gear housings.
Design Optimization: Complex shapes—like honeycomb structures or hollowed-out cores—slash weight while boosting strength. Autodesk’s design software often pairs with molding to perfect these geometries.
A real example? The Amazon Echo Dot’s casing. Its latest iteration uses thin-wall molding with a polycarbonate blend, trimming weight by 25% from earlier models, per industry teardown reports. That’s the kind of edge we can steal for our projects.
Impact on the Aerospace Industry
Now, let’s soar to aerospace, where lightweighting isn’t just nice—it’s critical. Every kilogram saved cuts fuel costs by $15,000 over an aircraft’s life, says Airbus. Injection molding’s a star player here.
Take the Boeing 787 Dreamliner. Its airframe is 50% composites by weight, and many smaller components—like seat frames and ducting—rely on injection-molded reinforced plastics. A 2022 Boeing press release noted these parts slashed interior weight by 15% compared to older aluminum designs. Or consider Airbus’s A350 XWB: injection-molded wing brackets, made with PEEK (polyetheretherketone), cut weight by 40% over metal equivalents, per a 2021 Aviation Week article.
For electronics designers, this is gold. If aerospace trusts injection molding for parts that defy gravity at 30,000 feet, why not use it for a rugged sensor enclosure or a lightweight drone chassis? The fuel savings translate to our world as battery savings—more runtime, less bulk.
Impact on the Automotive Industry
On the ground, automotive’s obsessed with lightweighting too. The average car has shed 200 pounds since 2010, per the U.S. Department of Energy, and injection molding’s a big reason why. For electric vehicles (EVs), every 10 kg saved boosts range by 2-3%, says a 2023 McKinsey report.
Look at Tesla’s Model 3. Its battery tray uses injection-molded glass-fiber-reinforced plastic, dropping weight by 30% compared to steel, according to a 2022 teardown by Munro & Associates. Or Ford’s F-150: the 2021 model swapped metal tailgate panels for injection-molded polypropylene, cutting 20 pounds while keeping crash resistance, per Ford’s engineering specs. Even luxury brands like BMW use foam injection molding for dashboards, trimming 15% off interior weight, as detailed in a 2024 Automotive News feature.
I talked to an engineer friend who worked on an EV startup. They replaced a metal motor mount with an injection-molded composite, saving 1.5 kg. It doesn’t sound like much, but it stretched the range by 5 miles—huge for a small player. For us, that’s a lesson: could your next PCB housing or connector trim a few grams and extend battery life?
Broader Advantages for Electronics Development
Back to our turf—electronics. Injection molding’s benefits hit all the right notes for designers and deciders:
Cost Efficiency: Tooling’s pricey upfront ($5,000-$50,000 per mold, says Protolabs), but once running, parts cost pennies in high volumes. A 2023 IndustryWeek survey found it’s 30% cheaper than CNC machining for runs over 10,000 units.
Design Flexibility: Need a casing with snap-fits or vents? Injection molding integrates them into one piece, cutting assembly weight. Apple’s AirPods case, for instance, uses this to pack features into a 38-gram shell, per iFixit’s teardown.
Sustainability: Recyclable thermoplastics like PET are common, and the process uses 20% less energy than metal forging, per a 2022 EPA study. Logitech’s MX Keys keyboard uses recycled plastic in its frame, shaving weight and guilt.
Compare that to 3D printing—great for prototypes but slow for scale (hours vs. seconds per part). Metal stamping? Heavy and less flexible. Injection molding’s the sweet spot. I once led a project swapping a stamped aluminum shield for an injection-molded plastic one. Weight dropped 35%, costs fell 20%, and we hit production deadlines. The client was thrilled—and so was I.
Challenges and What’s Coming Next
It’s not all smooth sailing. Lightweighting can be a tightrope act—thin-wall parts risk cracking under vibration (a common electronics headache). High-end materials like carbon-fiber composites can cost $20-$50 per pound, per Plastics News, and molds take weeks to perfect. A 2024 MoldMaking Technology report pegged tooling delays as the top gripe for 40% of manufacturers.
But the future’s bright. Bio-based polymers—like PLA from corn—are cutting costs and carbon footprints; a 2023 Nature Materials study says they’re 25% lighter than traditional plastics. Simulation tools, like Moldflow, now predict part behavior with 95% accuracy, per Autodesk, slashing trial-and-error. And hybrid molding—blending foam and thin-wall techniques—could trim another 10-15% off weight, says a 2025 SPE forecast.
I met a materials scientist at a trade show last month who’s testing a hemp-based polymer for audio enclosures. Early results? 18% lighter than ABS, with killer acoustics. That’s the kind of leap we should chase.
Wrapping It Up
Injection molding isn’t just a process—it’s a lightweight revolution. In aerospace, it’s saving Boeing and Airbus millions in fuel. In automotive, it’s stretching Tesla’s range and lightening Ford’s load. For us in electronics, it’s a chance to rethink design—crafting devices that are sleeker, more efficient, and downright impressive.
The facts back it up: 30% weight cuts in cars, 15% in plane interiors, 25% in smart speakers. The tools are here—thin walls, clever composites, optimized shapes. So, next time you’re sketching a wearable or pitching a gadget, don’t sleep on injection molding. It’s not just about grams; it’s about performance, cost, and winning over users. Dig into it. Test those materials. The lightweight future’s calling—and it’s lighter than ever.