How Does Electronics Manufacturing Work? A Deep Dive into the Process for Designers and Decision-Makers
We’re peeling back the curtain on how electronics manufacturing works. We’ll walk you through each step, from brainstorming designs to shipping finished products, with a focus on what matters to those shaping the industry. Whether you’re a designer tweaking PCB layouts or a manager optimizing supply chains, here’s your guide to the journey of turning ideas into reality.
3/7/20255 min read
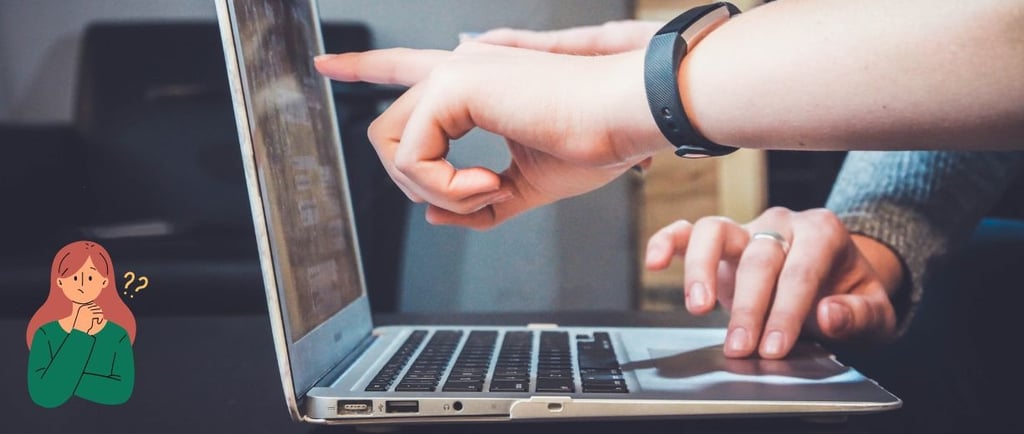
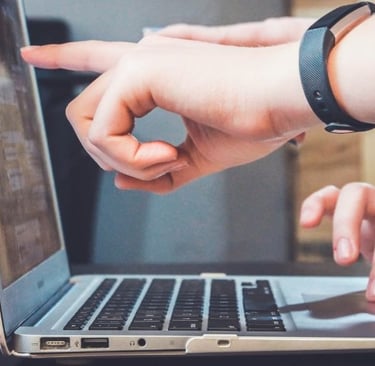
Imagine picking up your smartphone—sleek, powerful, and packed with features. Ever wonder how it went from a pile of raw materials to that shiny gadget in your hand? Electronics manufacturing is the unsung hero behind every device we use, from laptops to medical equipment. For designers crafting cutting-edge circuits and decision-makers steering production strategies, understanding this process isn’t just fascinating—it’s essential.
In this article, we’re peeling back the curtain on how electronics manufacturing works. We’ll walk you through each step, from brainstorming designs to shipping finished products, with a focus on what matters to those shaping the industry. Whether you’re a designer tweaking PCB layouts or a manager optimizing supply chains, here’s your guide to the journey of turning ideas into reality.
What Is Electronics Manufacturing?
At its core, electronics manufacturing is the art and science of creating electronic devices. It’s about taking raw materials—like silicon, copper, and plastic—and transforming them into functional components, then assembling them into the gadgets we can’t live without. Think smartphones, smartwatches, or even the control systems in your car.
This isn’t a solo gig. It’s a symphony of talent—engineers sketching blueprints, designers perfecting layouts, and manufacturers bringing it all to life. For designers, it’s where your creativity meets precision. For decision-makers, it’s a balancing act of cost, quality, and innovation. Together, you’re the architects of a trillion-dollar industry that keeps the world connected.
The Electronics Manufacturing Process: Step-by-Step
Let’s break it down. Here’s how your vision becomes a tangible product, step by meticulous step.
Step 1: Design and Prototyping
It all starts with an idea. As a designer, you’re likely hunched over CAD software, sketching out circuits and dreaming up the next big thing. This is where creativity meets technical grit. You’re not just drawing lines—you’re defining how components will talk to each other.
Once the design’s roughed out, it’s time for prototyping. Maybe you 3D-print a model or build a small batch to test. I remember chatting with a friend who designs wearables—she said this stage feels like sculpting, tweaking until it’s just right. For decision-makers, this is where you greenlight funding and set timelines. Get it wrong here, and the whole process stumbles.
Step 2: Sourcing Raw Materials
Next up: gathering the building blocks. Silicon powers microchips, copper conducts electricity, and gold ensures connections don’t corrode. Plastics and ceramics round out the mix. For decision-makers, this is a logistical puzzle—sourcing from global suppliers while dodging shortages (remember the chip crisis of 2021?).
Designers, you’re not off the hook. Your specs dictate what’s needed, so choosing materials that balance performance and cost is key. It’s like picking ingredients for a recipe—too cheap, and the dish flops; too rare, and no one can afford it.
Step 3: Component Fabrication
Now, those raw materials become the tiny heroes of electronics: semiconductors, resistors, capacitors. This happens in high-tech factories, often in cleanrooms where a speck of dust could ruin a microchip. I’ve seen videos of these places—workers in bunny suits, machines humming, turning silicon wafers into intricate circuits.
For designers, this is where your specs get real. A slight tweak in a transistor’s size could boost efficiency—or tank it. Decision-makers, you’re watching yields here. Low output means higher costs, and that’s your headache to solve.
Step 4: Printed Circuit Board (PCB) Production
The PCB is the backbone of any device. It’s that green board with squiggly lines you’ve probably glimpsed inside a gadget. Designers, this is your playground—laying out traces, etching copper, and stacking layers to make everything fit. It’s like urban planning for electrons.
Manufacturers take your design and bring it to life, using processes like photolithography and soldering. Decision-makers, you’re eyeing scalability—can this PCB be mass-produced without breaking the bank? A well-designed board saves headaches down the line.
Step 5: Assembly
Here’s where it all comes together. Components get mounted onto the PCB, either by hand (for prototypes) or via automated pick-and-place machines churning out thousands of units. Surface-mount technology (SMT) dominates—tiny parts soldered right onto the board’s surface. For older-school designs, through-hole techniques still linger.
I once toured a factory where robots danced in sync, placing chips faster than I could blink. Designers, your layout dictates how smooth this goes. Decision-makers, you’re juggling automation costs versus labor. Get it right, and production sings.
Step 6: Testing and Quality Control
No one wants a dud device. Testing is brutal but necessary—automated optical inspections scan for flaws, functional tests ensure the thing actually works. I’ve heard engineers groan about this stage, poring over data to catch a single glitch.
Designers, your prototypes face their trial by fire here. Decision-makers, you’re setting standards—how many failures are too many? It’s about trust. A solid product builds your brand; a faulty one trashes it.
Step 7: Packaging and Distribution
Finally, the device gets its shell—plastic casing, sleek metal, whatever your market demands. It’s boxed up, shipped out, and lands on shelves or doorsteps. Designers, your work’s done, but decision-makers, you’re tracking logistics. Delays here can sour a perfect launch.
Technologies and Innovations in Electronics Manufacturing
The game’s always changing. Automation and robotics have turned assembly lines into high-speed marvels—fewer errors, faster output. Designers love this; it means your wildest ideas can hit production sooner. Decision-makers, you’re calculating ROI on those shiny new bots.
Miniaturization’s another beast. Devices keep shrinking, packing more power into less space. Think about the evolution from clunky PCs to slim laptops. For designers, it’s a challenge—cramming functionality into a pinhead-sized chip. For decision-makers, it’s a goldmine—smaller often means cheaper to ship.
Sustainability’s creeping in, too. Eco-friendly materials and recycling programs are hot topics. I chatted with a manager who’s pushing for greener PCBs—tough sell, but customers love it. You’re both shaping a future where tech doesn’t trash the planet.
Challenges in Electronics Manufacturing
It’s not all smooth sailing. Supply chain hiccups—like those pesky chip shortages—can stall everything. Designers, you might need to pivot fast, swapping parts mid-project. Decision-makers, you’re on the phone with suppliers, begging for miracles.
Complexity’s a killer, too. Modern devices are insanely intricate—think 5G chips or AI processors. One misstep in design or production, and you’re sunk. Then there’s cost. Balancing quality with affordability in a cutthroat market keeps everyone up at night.
Real-World Example: How a Smartphone Is Made
Picture this: a smartphone starts as a designer’s sketch in Silicon Valley. Months later, silicon’s mined in Australia, turned into chips in Taiwan, and assembled in China. PCBs get etched, components soldered, screens added—all in six months. It’s tested, boxed, and shipped to your pocket. That’s the magic you’re driving, from concept to consumer.
Conclusion
From design to distribution, electronics manufacturing is a dance of precision and strategy. Designers, you’re the visionaries, crafting the blueprints that spark innovation. Decision-makers, you’re the navigators, steering through costs, timelines, and tech trends. Together, you’re building the future—one circuit at a time.
Next time you power up a device, think about the journey it took. Got a favorite gadget? Drop it in the comments—I’d love to hear what inspires you.