How Automation is Revolutionizing Injection Molding
Injection molding has long been the go-to for crafting the plastic parts that power our gadgets, from tiny PCB enclosures to durable phone casings. Robotics, artificial intelligence (AI), and the buzzword of the decade—Industry 4.0—are turning this workhorse process into something smarter, faster, and more sustainable.
2/24/20255 min read
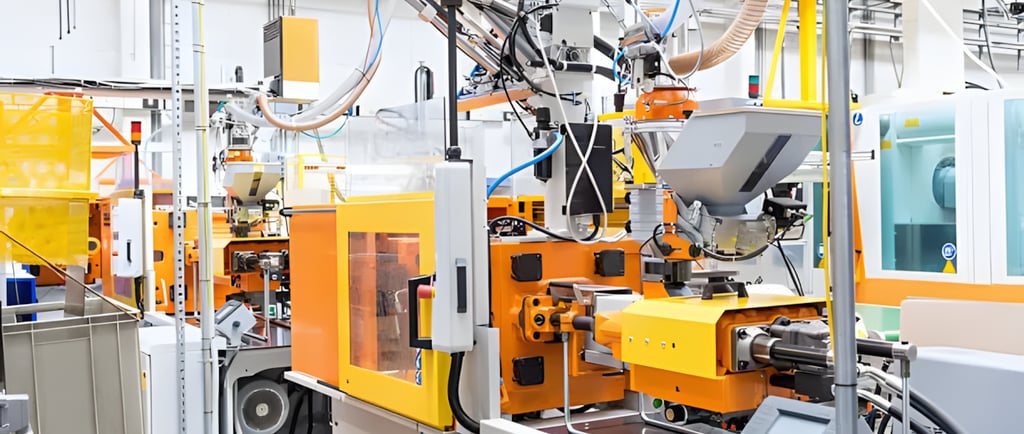
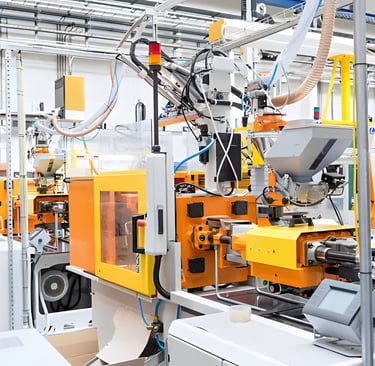
Picture this: You’re designing the next big thing in electronics—a sleek, lightweight housing for a wearable device or a precision connector for a high-speed circuit. You’ve got deadlines looming, cost pressures mounting, and a team counting on you to deliver. Now imagine a world where the manufacturing process doesn’t just keep up but actually makes your job easier. That’s where automation steps in, and it’s shaking up injection molding like never before. For designers and decision-makers in electronics development, this isn’t just a trend—it’s a lifeline to staying competitive.
Injection molding has long been the go-to for crafting the plastic parts that power our gadgets, from tiny PCB enclosures to durable phone casings. But today, it’s not enough to rely on the old ways. Robotics, artificial intelligence (AI), and the buzzword of the decade—Industry 4.0—are turning this workhorse process into something smarter, faster, and more sustainable. Let’s dive into how these game-changers are reshaping the landscape and why they matter to you.
The Rise of Robotics in Injection Molding
If you’ve ever watched a factory floor in action, you know injection molding can be a grind—literally. Hot plastic gets shot into molds, parts cool, and someone (or something) has to pull them out, trim them, and stack them. Enter robotics, the unsung hero of modern manufacturing. These aren’t the clunky robots of sci-fi movies; they’re sleek, precise machines that take the grunt work off your plate.
Think about robotic arms zipping along, pulling freshly molded connectors from a press in seconds, or collaborative robots—cobots—working side-by-side with your team to assemble components. I saw this firsthand at a trade show last year: a cobot delicately placing tiny electronic housings into trays while a technician fine-tuned the mold nearby. It was like watching a dance—smooth, efficient, and oddly satisfying.
For electronics, where precision is everything, robots shine. They don’t get tired, don’t fumble small parts, and don’t need coffee breaks. That means faster cycle times—think shaving seconds off each part, which adds up when you’re producing thousands of units. Plus, they handle the messy stuff, like dealing with hot molds or sharp edges, keeping your team safer and focused on the creative side of design.
Take the automotive sector as a cue—they’ve been using robotic arms to churn out molded dashboards and sensor housings at scale. For you, that could translate to cranking out casings for smartwatches or IoT devices without breaking a sweat. The payoff? Lower labor costs, fewer errors, and a production line that hums along like a well-oiled machine.
AI-Powered Precision and Optimization
Now, let’s talk about the brains behind the operation: artificial intelligence. If robotics is the muscle, AI is the mind, and it’s bringing a whole new level of smarts to injection molding. Imagine designing a complex enclosure with tight tolerances—say, for a next-gen wireless earbud. You need the material to flow just right, the temperature to stay perfect, and zero defects. AI makes that happen.
Here’s how it works: AI systems monitor every step of the molding process in real time. Sensors track pressure, temperature, even the viscosity of the plastic as it flows into the mold. If something’s off—like a clog forming or a machine starting to wear—AI catches it before it becomes a problem. I’ve heard engineers call it “predictive maintenance,” but I think of it as having a super-smart assistant who whispers, “Hey, fix this now, and save yourself a headache later.”
Even better, AI learns. Machine learning algorithms study past runs to tweak settings—like how much pressure to apply or how long to cool—until the process is dialed in perfectly. Fewer warped parts, fewer rejects, and happier customers. For electronics designers, that’s gold. You’re not just getting parts; you’re getting parts that meet your exact specs, every time.
And it’s not just about fixing things. AI can simulate how a mold will perform before you even build it. Picture this: You tweak your CAD file, run it through an AI tool, and see if that intricate vent design will hold up under pressure—all without wasting material or time. It’s like having a crystal ball for prototyping, and it’s cutting weeks off development cycles.
The cherry on top? Energy savings. Optimized processes use less power, which matters when you’re pitching sustainability to stakeholders or just trying to keep costs down. AI isn’t futuristic hype—it’s here, and it’s making your designs come to life more reliably than ever.
Industry 4.0 and the Connected Factory
Okay, so robotics and AI are impressive on their own, but Industry 4.0 is where they really team up to steal the show. If you’re scratching your head over the term, think of it as the “internet of manufacturing”—a world where machines, data, and people talk to each other seamlessly. For injection molding, it’s the glue that ties everything together.
Imagine a factory where every molding press is fitted with smart sensors. They’re tracking output, spotting bottlenecks, and sending updates to your phone while you’re sipping coffee at your desk. That’s Industry 4.0 in action. Or picture a “digital twin”—a virtual version of your molding setup that you can tweak and test without touching the real thing. I spoke to a designer last month who used a digital twin to perfect a tricky USB-C housing. He said it felt like playing a video game, except the prize was a flawless product launch.
The real magic happens with connectivity. Cloud systems let you monitor production from anywhere—say, checking on a batch of circuit board mounts while you’re at a client meeting. Data flows between machines, so if one press slows down, the others adjust automatically. It’s not just efficient; it’s flexible. Need a small run of custom enclosures for a prototype? Industry 4.0 makes it possible without retooling the whole line.
For electronics, where trends move fast and customization is king, this is a big deal. You can pivot from mass-producing phone cases to small-batch IoT sensors without missing a beat. And the dream of “lights-out” factories—fully automated plants running 24/7 with minimal human oversight? It’s closer than you think. I’ve seen demos where entire molding lines churned out parts overnight, no babysitting required. That’s the kind of scalability that keeps you ahead of the curve.
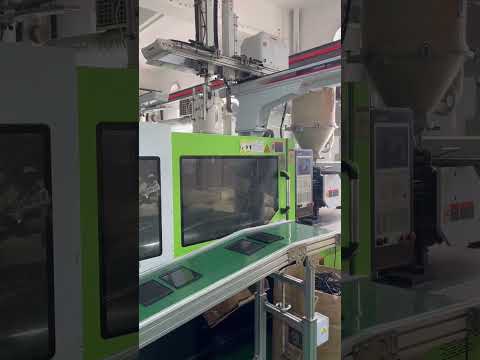
Challenges and Opportunities
Of course, it’s not all smooth sailing. Automation sounds great until you see the price tag. Upgrading to robotic arms, AI software, and smart sensors isn’t cheap, and for smaller shops, it can feel like a leap of faith. Then there’s the human side—your team might balk at learning new tech or worry their jobs are on the chopping block. I get it; change is messy.
But here’s the flip side: the opportunities are massive. Yes, the upfront cost stings, but the long-term savings—in labor, materials, and downtime—add up fast. I talked to a decision-maker at an electronics firm who said their ROI hit within 18 months of going automated. That’s not pie-in-the-sky stuff; it’s real numbers. Plus, in a market where speed and quality win contracts, automation isn’t just nice-to-have—it’s your edge.
The trick is balance. You don’t need to ditch your skilled workers; you need to retrain them. Pair their know-how with these tools, and you’ve got a powerhouse. One designer told me his team went from dreading mold tweaks to loving the challenge, thanks to AI handling the tedious bits. It’s about empowering people, not replacing them.
Conclusion
So, where does this leave you? Robotics, AI, and Industry 4.0 aren’t just buzzwords—they’re rewriting the rules of injection molding. For designers in electronics development, they mean faster prototyping, tighter tolerances, and happier production teams. For decision-makers, they’re the key to slashing costs, boosting output, and staying ahead of competitors who are still stuck in the past.
The message is clear: embrace automation now, or risk getting left behind. It’s not about chasing trends; it’s about building a future where your designs don’t just work—they thrive. The next time you sketch out a casing or pitch a project, think about this: the factory of tomorrow isn’t coming—it’s here, and it’s smarter than ever. Are you ready to plug in?