How AI is Revolutionizing Fully Automated Precision Manufacturing
From the assembly lines of Henry Ford to the robotic factories of today, the industry has consistently embraced technology to push boundaries. Now, artificial intelligence (AI) stands poised to take this evolution to the next level, promising to usher in an era of fully automated precision manufacturing.
3/25/20256 min read
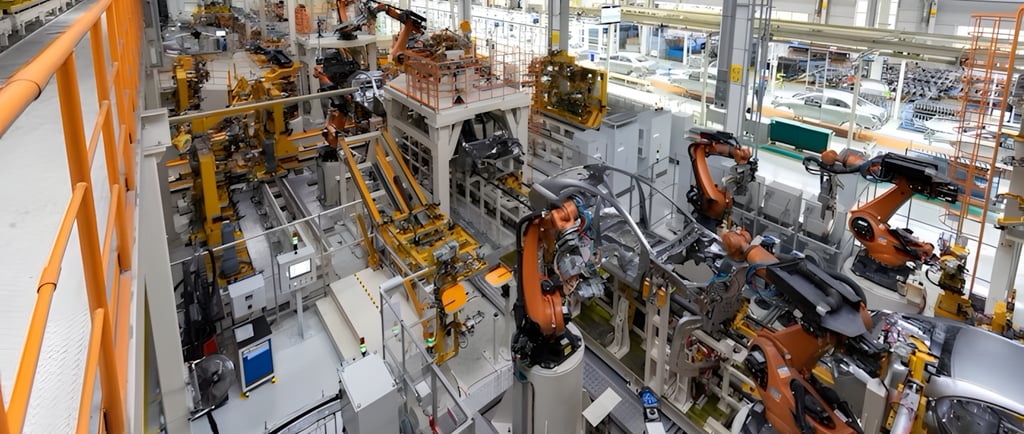
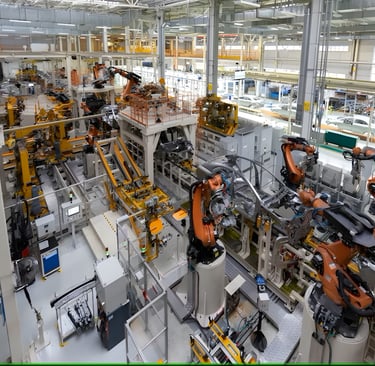
In the ever-evolving world of manufacturing, the pursuit of precision, efficiency, and scalability has long been a driving force behind innovation. From the assembly lines of Henry Ford to the robotic factories of today, the industry has consistently embraced technology to push boundaries. Now, artificial intelligence (AI) stands poised to take this evolution to the next level, promising to usher in an era of fully automated precision manufacturing. This transformative potential is not just theoretical—it’s already being explored by forward-thinking companies, as highlighted in a recent article from SupplyChainBrain titled "Can AI Usher in the Age of Fully Automated Precision Manufacturing?" In this blog post, we’ll dive deep into how AI is reshaping precision manufacturing, the opportunities it presents, the challenges it faces, and what the future might hold.
The Precision Manufacturing Challenge
Precision manufacturing refers to the production of parts and components with extraordinarily tight tolerances—often within two to three microns, where a single micron is 1/70th the thickness of a human hair. Industries like aerospace, automotive, and medical device production rely on this level of accuracy to ensure safety, performance, and reliability. Traditionally, achieving such precision has required highly skilled human workers, sophisticated machinery, and meticulous quality control processes. However, this approach comes with limitations: human error, labor shortages, and the inability to operate 24/7.
The COVID-19 pandemic exacerbated these challenges, accelerating the retirement of an aging workforce and leaving manufacturers grappling with a shrinking pool of skilled labor. As Bernard Mariette, executive chairman of Watch Out—a French/Swiss company pioneering AI-driven manufacturing systems—notes in the SupplyChainBrain article, “We can see every day that we’re missing people.” This labor gap, combined with rising demands for higher-quality parts and faster production cycles, has created a perfect storm—one that AI is uniquely positioned to address.
AI as the Backbone of Automation
At its core, AI is about enabling machines to perform tasks that typically require human intelligence, such as decision-making, problem-solving, and pattern recognition. In the context of precision manufacturing, AI can power fully autonomous systems that operate with minimal human intervention, delivering consistent quality and efficiency. Here’s how AI is making this possible:
Real-Time Error Correction
One of the standout features of AI in manufacturing is its ability to integrate with sensors and algorithms to monitor and adjust processes in real time. Traditional manufacturing relies on post-production inspections to catch defects, but AI-driven systems can detect deviations as they happen—whether it’s a misalignment of a tool or a fluctuation in material properties—and correct them instantly. This capability not only reduces waste but also ensures that every part meets exacting standards, a critical requirement in precision industries.Round-the-Clock Operations
Unlike human workers, AI-powered machines don’t need breaks, sleep, or shift changes. By automating precision manufacturing with AI, factories can operate 24/7, dramatically increasing throughput. This is particularly valuable in industries where demand is high and timelines are tight, such as aerospace component production or medical device manufacturing during a health crisis.Optimization of Complex Processes
Precision manufacturing often involves intricate workflows with multiple variables—tool speeds, material temperatures, cutting angles, and more. AI excels at analyzing vast datasets to identify optimal settings for these variables, far surpassing human capabilities in speed and accuracy. The result is a streamlined process that minimizes energy use, reduces costs, and maximizes output.Predictive Maintenance
Downtime is the enemy of efficiency, and in precision manufacturing, even minor equipment failures can lead to costly delays. AI can predict when machines are likely to fail by analyzing patterns in sensor data—vibration, heat, or wear—and schedule maintenance proactively. This keeps production lines running smoothly and extends the lifespan of expensive equipment.
A Case Study: Watch Out’s Vision
The SupplyChainBrain article highlights Watch Out, a company that exemplifies AI’s potential in precision manufacturing. Led by Bernard Mariette, Watch Out has developed a system that claims to cut costs and carbon footprints by at least 30% while reducing the need for human workers on the assembly line. Their approach integrates AI with advanced automation to achieve “fully autonomous” technology, a bold step toward reimagining manufacturing from the ground up.
Watch Out’s system isn’t just about replacing humans—it’s about enhancing what machines can do. By leveraging AI-based algorithms, their technology ensures higher-quality parts through continuous monitoring and adjustment. The reduction in carbon footprint also speaks to a broader trend: AI’s ability to optimize resource use aligns with growing demands for sustainable manufacturing practices. For industries like automotive and aerospace, where precision and environmental responsibility are increasingly intertwined, this dual benefit is a game-changer.
Opportunities Beyond Efficiency
While efficiency and precision are the immediate benefits of AI in manufacturing, the technology opens doors to even greater possibilities:
Scalability
AI-driven automation allows manufacturers to scale production up or down with ease. Need to ramp up output for a new product launch? AI can reconfigure workflows and optimize resources in hours, not weeks. This flexibility is invaluable in a world where market demands shift rapidly.Customization
Precision manufacturing often caters to bespoke needs—think custom implants in medicine or tailored components in aerospace. AI can adapt production processes to handle small-batch runs without sacrificing efficiency, making it easier for manufacturers to meet niche demands.Data-Driven Innovation
Every AI-powered machine generates a wealth of data—performance metrics, error logs, environmental conditions. Manufacturers can harness this data to refine their processes, develop new products, or even predict market trends, turning the factory floor into a hub of innovation.Sustainability
By optimizing energy use, reducing material waste, and minimizing downtime, AI contributes to greener manufacturing. This aligns with global efforts to combat climate change and meets the expectations of environmentally conscious consumers and regulators.
The Challenges of AI Adoption
Despite its promise, integrating AI into precision manufacturing isn’t without hurdles. The SupplyChainBrain article identifies several key challenges that manufacturers must navigate:
High Up-Front Costs
Implementing AI requires significant investment in hardware (sensors, robots, computing power), software (AI algorithms, integration platforms), and infrastructure upgrades. For small and medium-sized enterprises (SMEs), this can be a daunting barrier, even if the long-term savings are substantial.Legacy System Integration
Many manufacturers still rely on decades-old equipment that wasn’t designed with AI in mind. Retrofitting these systems—or replacing them entirely—adds complexity and cost to the transition. As Mariette points out, “The skill isn’t on the [plant] floor. It’s at the center—to analyze and make sure they’ve improved.” Bridging the gap between old and new technology is a critical step.Workforce Retraining
While AI reduces the need for manual labor, it increases the demand for workers who can oversee, maintain, and optimize automated systems. Retraining existing staff—or hiring new talent with the right skills—requires time and resources. Manufacturers must also address fears that AI will eliminate jobs, emphasizing instead how it shifts roles toward higher-value tasks.Data and Cybersecurity Risks
AI thrives on data, but collecting and storing vast amounts of production information introduces vulnerabilities. A cyberattack could disrupt operations or expose proprietary designs, making robust security measures essential.
Overcoming the Barriers
To realize AI’s full potential in precision manufacturing, manufacturers can adopt a strategic approach:
Start Small
Rather than overhauling an entire factory, companies can pilot AI in a single production line or process. This minimizes risk, builds confidence, and provides a proof of concept for broader adoption.Partner with Experts
Collaborating with AI specialists—like tech firms or universities—can accelerate implementation and reduce costs. Watch Out’s success, for instance, likely stems from a deep understanding of both manufacturing and AI, a synergy that others can replicate through partnerships.Invest in People
Training programs that upskill workers in AI, data analysis, and automation will create a workforce ready to thrive in an autonomous factory. Clear communication about how AI enhances—not replaces—human roles can also ease resistance.Leverage Government Support
Many governments offer grants, tax incentives, or research funding for AI adoption in manufacturing. Tapping into these resources can offset initial costs and encourage innovation.
The Future of Fully Automated Precision Manufacturing
Looking ahead, AI’s role in precision manufacturing is set to grow exponentially. As algorithms become more sophisticated and hardware costs decline, the barriers to entry will lower, making this technology accessible to a wider range of manufacturers. We might see “lights-out” factories—fully automated facilities requiring no human presence—become the norm in high-precision industries. Companies like FANUC in Japan, which already uses robots to build other robots, offer a glimpse of this future.
Moreover, AI could integrate with other emerging technologies, such as 3D printing or the Internet of Things (IoT), to create even more powerful manufacturing ecosystems. Imagine a factory where AI not only controls production but also designs parts on the fly, adjusts to real-time supply chain disruptions, and communicates seamlessly with suppliers—all while maintaining micron-level precision.
Conclusion: A New Era Beckons
AI is more than just a tool for automation—it’s a catalyst for reimagining precision manufacturing. As the SupplyChainBrain article suggests, companies like Watch Out are leading the charge, proving that AI can deliver higher quality, lower costs, and greater sustainability. While challenges remain, the rewards—efficiency, scalability, and innovation—are too significant to ignore.
For manufacturers willing to embrace this shift, the age of fully automated precision manufacturing is not a distant dream but an imminent reality. By investing in AI today, they can position themselves at the forefront of an industry on the cusp of transformation—one where machines don’t just follow instructions but think, adapt, and perfect the art of making. The question isn’t whether AI can usher in this new era, but how quickly we’ll let it.