How Additive Manufacturing Helps Manufacturers Navigate Trade Wars and Tariff Challenges
Global trade wars and increasing tariffs have created challenges for manufacturers worldwide. Rising costs, disrupted supply chains, and geopolitical uncertainties have made it difficult for businesses to maintain profitability and efficiency. However, one technology has emerged as a potential solution: Additive Manufacturing (AM), commonly known as 3D printing.
3/25/20255 min read
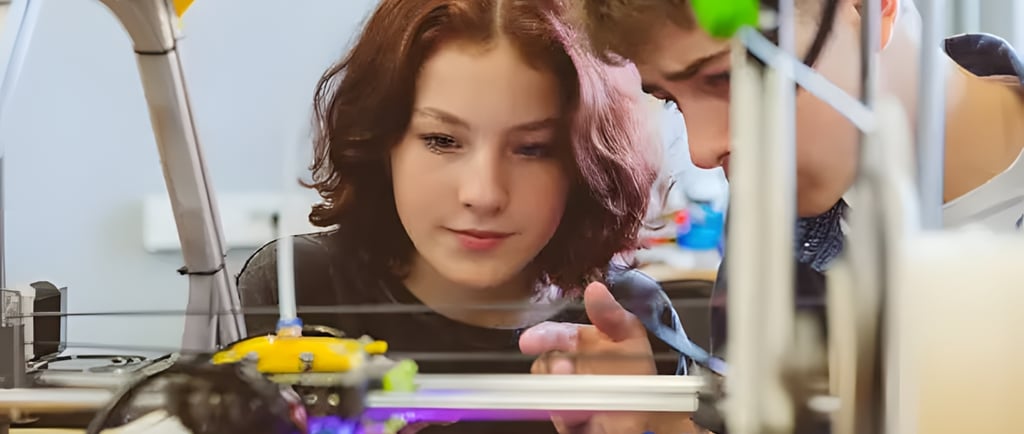
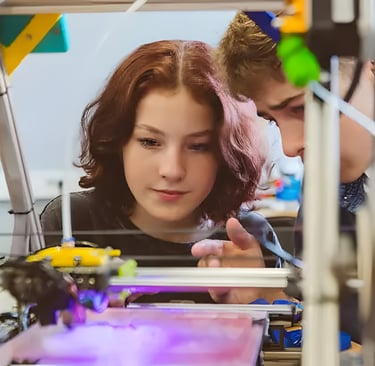
In recent years, global trade wars and increasing tariffs have created challenges for manufacturers worldwide. Rising costs, disrupted supply chains, and geopolitical uncertainties have made it difficult for businesses to maintain profitability and efficiency. However, one technology has emerged as a potential solution: Additive Manufacturing (AM), commonly known as 3D printing. AM enables manufacturers to shift production closer to home, reduce dependence on overseas suppliers, and minimize tariff-related costs. This article explores how AM can serve as a strategic advantage in navigating trade conflicts and ensuring business resilience.
The Impact of Trade Wars and Tariffs on Manufacturing
Trade wars, particularly between major economies like the U.S. and China, have led to increased tariffs on a wide range of goods, including raw materials, components, and finished products. These tariffs result in higher costs for manufacturers, ultimately affecting pricing, competitiveness, and supply chain reliability. Key consequences of trade wars include:
Increased Costs: Tariffs raise the price of imported goods, making raw materials and components more expensive for manufacturers.
Supply Chain Disruptions: Restrictions on imports and exports cause delays, leading to production bottlenecks.
Market Uncertainty: Constant policy changes make long-term planning difficult for businesses, increasing financial risk.
Relocation Pressure: Many manufacturers are considering shifting operations to different countries or reshoring production to mitigate the impact of tariffs.
In this challenging landscape, AM offers a viable alternative to traditional manufacturing methods, providing cost-effective, flexible, and decentralized production solutions.
Advantages of Additive Manufacturing in a Trade War Environment
1. Reduced Dependence on Global Supply Chains
One of the biggest advantages of AM is its ability to localize production. Traditionally, manufacturers rely on international supply chains for sourcing materials and components, making them vulnerable to tariffs and trade restrictions. AM allows companies to produce parts on-site, reducing the need for imported goods and minimizing exposure to trade-related disruptions.
By leveraging AM, businesses can create a more self-sufficient production model, reducing lead times and lowering transportation costs. This is particularly beneficial for industries like electronics, automotive, and aerospace, where supply chain efficiency is critical.
2. On-Demand and Just-in-Time Production
In a volatile trade environment, maintaining large inventories of imported goods can be risky and expensive. AM enables on-demand production, allowing manufacturers to print components as needed rather than stockpiling them in advance. This just-in-time approach helps reduce warehouse costs and eliminates the financial burden of unsold inventory.
Additionally, companies can quickly adapt to changing market demands without worrying about supply chain interruptions. This flexibility is especially important for businesses operating in industries with frequent design updates or customization requirements.
3. Avoiding Tariffs on Finished Goods
Many trade policies impose high tariffs on finished products rather than raw materials. Instead of importing fully assembled goods, manufacturers can ship raw materials and use AM to produce final products domestically. This approach helps companies avoid some of the heaviest tariff burdens while maintaining product quality and consistency.
For example, rather than importing complete electronic devices, businesses can import essential components and use AM to fabricate casings, enclosures, or other structural elements locally. This strategy not only reduces tariff costs but also improves customization options for regional markets.
4. Customization Without Additional Costs
Traditional manufacturing often requires different molds, tools, or machinery for each product variation, making customization expensive and time-consuming. AM eliminates these barriers by allowing manufacturers to modify designs digitally without incurring additional setup costs. This is particularly beneficial in sectors like medical devices, consumer electronics, and industrial equipment, where product differentiation is crucial.
With AM, manufacturers can tailor products to specific customer needs without worrying about trade restrictions on specialized components. This capability enhances competitiveness and provides a unique selling proposition in markets affected by tariffs.
5. Lower Material Waste and Cost Efficiency
Tariff wars often drive up the cost of raw materials such as metals and polymers, making waste reduction a top priority. Unlike traditional subtractive manufacturing, which removes material to shape a product, AM builds components layer by layer, using only the necessary material. This results in significant cost savings and reduces the environmental impact of manufacturing.
By optimizing material usage, AM helps businesses maintain cost efficiency despite rising material prices due to trade policies. This sustainable approach also aligns with global efforts to reduce industrial waste and promote eco-friendly manufacturing practices.
6. Faster Prototyping and Innovation
Trade wars can delay the development of new products by restricting access to essential components or increasing procurement costs. AM accelerates the prototyping process, allowing companies to design, test, and iterate new products quickly. By eliminating the need to outsource prototype manufacturing, businesses can shorten their development cycles and bring products to market faster.
Additionally, AM enables rapid experimentation with new materials and geometries, fostering innovation in industries such as consumer goods, healthcare, and aerospace. This agility is crucial for staying competitive in a rapidly changing global trade environment.
7. Resilience Against Trade Disruptions
Trade policies and tariffs can change suddenly, leaving manufacturers scrambling to adjust their operations. AM provides a buffer against such uncertainties by decentralizing production. Instead of relying on a single country for manufacturing, companies can establish multiple AM facilities worldwide, reducing their exposure to geopolitical risks.
This decentralized approach ensures business continuity even in the face of trade restrictions, supply chain disruptions, or natural disasters. By distributing production capabilities, manufacturers can respond more effectively to regional market demands and regulatory changes.
8. Enabling Nearshoring and Reshoring Strategies
As trade tensions continue, many companies are reconsidering their reliance on offshore production. AM makes nearshoring (moving production closer to target markets) and reshoring (bringing manufacturing back to the home country) more viable by reducing labor and tooling costs.
For instance, companies in the U.S. that previously relied on Chinese manufacturing can establish AM facilities domestically, avoiding tariffs while maintaining competitive production costs. Similarly, European manufacturers can leverage AM to shift production away from high-tariff regions to more stable locations.
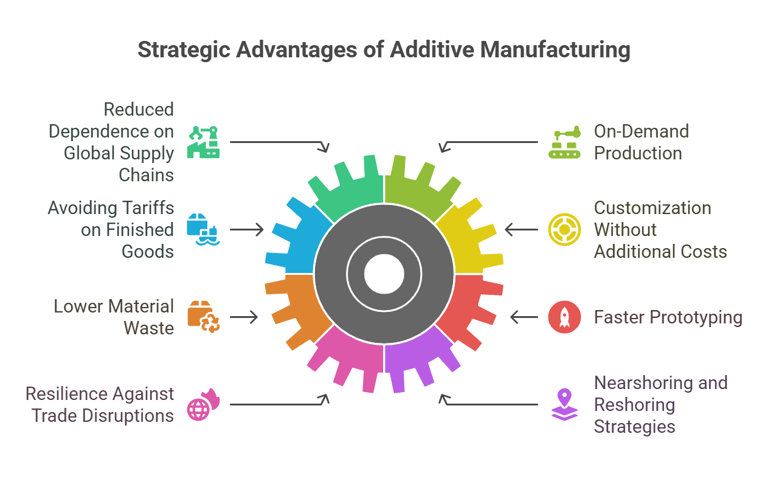
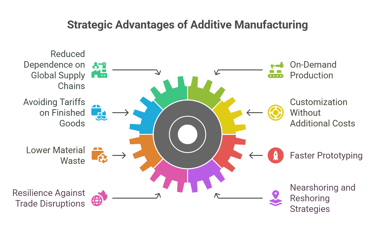
Challenges and Considerations
While AM offers numerous advantages in a trade war environment, it is not without challenges. Some factors manufacturers must consider include:
Material Limitations: Not all materials used in traditional manufacturing are compatible with AM processes, which may limit its applicability for certain products.
Production Speed: AM is generally slower than mass production methods like injection molding, making it less suitable for high-volume manufacturing.
Initial Investment Costs: Setting up AM facilities requires upfront investment in equipment, software, and skilled labor, which may be a barrier for some businesses.
Quality Control and Certification: Ensuring consistent quality and meeting industry regulations for AM-produced parts can be challenging, particularly in highly regulated sectors.
Despite these hurdles, advancements in AM technology are continually improving speed, material options, and scalability, making it an increasingly attractive solution for manufacturers facing trade uncertainties.
Conclusion
As trade wars and tariffs continue to reshape the global manufacturing landscape, businesses must find innovative ways to remain competitive. Additive Manufacturing presents a powerful solution by reducing reliance on international supply chains, lowering costs, and increasing production flexibility. By leveraging AM, manufacturers can navigate trade disruptions, avoid excessive tariffs, and create more resilient production strategies.
Although challenges exist, the long-term benefits of AM outweigh its limitations, making it a key enabler of the future of manufacturing. Companies that embrace this technology will be better positioned to thrive in an increasingly complex global trade environment. Now is the time for manufacturers to explore the potential of AM and integrate it into their operations to safeguard against the uncertainties of trade conflicts.