Why Hardware Developers Should Pay Attention to the Plastic Injection Molding Machine Market in 2025 and Beyond
From sleek gadget housings to rugged industrial components, injection molding is where design meets deliverability. And based on recent market insights, this intersection is entering a new era—fueled by smart manufacturing, energy optimization, and shifting global trade winds.
5/18/20255 min read
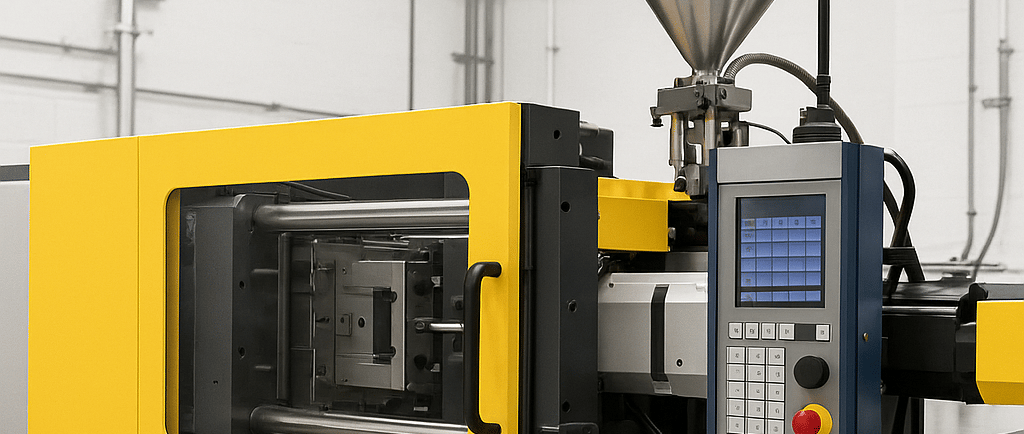
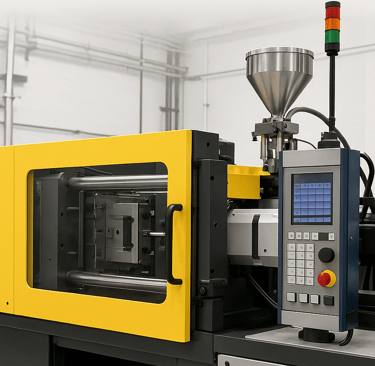
The hum of a plastic injection molding machine might not be music to everyone's ears, but for hardware developers, it's the sound of products taking form — quite literally.
From sleek gadget housings to rugged industrial components, injection molding is where design meets deliverability. And based on recent market insights, this intersection is entering a new era—fueled by smart manufacturing, energy optimization, and shifting global trade winds.
In this deep dive, we’ll explore why the plastic injection molding machine (PIMM) market is heating up, and more importantly, how hardware developers can ride the wave smartly into 2032 and beyond.
The Numbers Speak Volumes
The global plastic injection molding machine market hit $11.91 billion in 2023. That alone signals serious business. But by 2032, the market is expected to swell to $17.16 billion, according to SNS Insider. That’s a compound annual growth rate (CAGR) of 4.14%, which may not sound flashy—until you consider the scale of this transformation in terms of technology, application, and capital movement.
In the U.S. alone, the market is forecasted to leap from $2.04 billion to $3.04 billion, driven by demand across medical devices, automotive, packaging, and consumer electronics.
Why This Growth Matters to You
As a hardware developer, you might be neck-deep in PCB layout, firmware tuning, or enclosure testing. But your path to mass production likely runs through a plastic injection mold. Understanding where this industry is headed isn't just insightful — it could mean the difference between scaling a product successfully or getting stuck in prototyping purgatory.
Let’s unpack the forces driving this market.
1. Automation and Smart Manufacturing
Smarter Machines, Smarter Scaling
Modern PIMMs are no longer just mechanical beasts—they're smart systems embedded with AI algorithms, sensors, and cloud connectivity. Real-time process monitoring and predictive maintenance are becoming standard features.
Why this matters:
Reduced downtime: Smart diagnostics mean less time lost due to unexpected breakdowns.
Greater consistency: Real-time feedback loops allow machines to self-correct and produce parts within tighter tolerances.
Faster iterations: For developers, fewer surprises during the design-for-manufacturing (DFM) phase.
Many manufacturers are linking their injection molding lines to broader MES (Manufacturing Execution Systems), creating seamless production ecosystems.
Tip for developers: When vetting a manufacturing partner or choosing a supplier, ask whether their injection molding lines are Industry 4.0-enabled. The long-term efficiency will likely save you headaches — and money.
2. Energy Efficiency Is a Strategic Priority
Injection molding has historically been power-hungry. Traditional hydraulic machines consume significant electricity—and with rising energy costs and regulatory pressure, that’s becoming unsustainable.
Cue the rise of:
All-electric injection molding machines: These offer up to 70% energy savings over hydraulic models. They’re also cleaner (oil-free), quieter, and more precise.
Hybrid systems: Combining electric and hydraulic components, they strike a balance between speed and power.
What this means for you:
You can now design with sustainability in mind—not just in the product, but in the process.
Energy-efficient equipment often translates into better unit economics, especially at scale.
Many large buyers (especially in Europe) are increasingly asking about the carbon footprint of your manufacturing line. This could become a sales differentiator.
3. Global Trade Dynamics Are Shaping Tooling Strategy
The last few years taught us a lot about global supply chain fragility. Geopolitical tensions, tariffs, and freight disruptions have nudged many companies to rethink where—and how—they mold plastic.
Trends to note:
China remains dominant, especially for high-volume and low-cost tooling. But there’s growing investment in Southeast Asia (Vietnam, Malaysia, Indonesia).
Nearshoring is real in North America. More developers are working with U.S. or Mexico-based injection molders for faster iteration cycles and better IP protection.
EU manufacturers are also re-localizing, partly due to strict environmental compliance requirements.
What to do as a hardware developer:
Diversify your tooling and production partners early—don’t wait until a crisis forces a move.
Build modularity into your molds so that production can be easily transferred to different geographies.
Choose partners who understand customs, duties, and cross-border logistics (not just molding).
4. Industry-Specific Demand Is Surging
Automotive: Lighter, Faster, Cleaner
With the push for electric vehicles, there's a spike in demand for lightweight plastic parts that reduce vehicle mass without compromising strength. PIMMs are producing dashboards, battery trays, and airflow components at scale.
Medical Devices: High Precision, Regulatory Rigor
The global health industry’s expansion, especially in home diagnostics and wearable tech, means more demand for ultra-precise, high-sterility plastic parts.
Developers working on biotech hardware, diagnostic readers, or drug delivery systems need to work with molders experienced in FDA-compliant, ISO 13485-certified manufacturing.
Consumer Electronics: Style Meets Strength
Smartphones, smart home devices, earbuds—the enclosures are getting sleeker and tougher. This means complex multi-cavity molds, advanced materials (like PC/ABS blends), and surface finishing techniques integrated into molding lines.
5. Technology Spotlight: Conformal Cooling Channels
You might not think much about how fast your plastic part cools—but your mold certainly does.
What’s conformal cooling?
Unlike traditional straight-line cooling channels, conformal cooling channels “hug” the geometry of the mold, leading to:
Faster cycle times (up to 30% reduction)
Better surface finish
Less warping or shrinkage
This technique, often 3D printed using DMLS (Direct Metal Laser Sintering), is gaining traction in high-performance molds.
Why it matters: If your part needs high dimensional accuracy or pristine aesthetics (think glossy covers or snap-fit precision), consider asking for conformal-cooled tooling.
Challenges Ahead — and What Developers Should Watch For
No technology surge is without hurdles. Here are some worth your radar:
1. High Initial Investment
Small startups may struggle to afford high-precision tooling. Even a single-cavity mold can run tens of thousands of dollars, and high-volume, multi-cavity tools are easily six-figure investments.
Solution: Explore shared tooling arrangements, prototype molds (like aluminum tools), or even hybrid approaches combining 3D printing and injection molding for early batches.
2. Skills Gap in Workforce
As PIMMs get smarter, the need for skilled technicians grows. There's a global shortage of mold designers, machine programmers, and quality inspectors who can operate at this new level.
Tip: Ask your manufacturing partners about their workforce development programs and equipment training schedules.
3. Competition from 3D Printing
Additive manufacturing isn’t replacing injection molding anytime soon—but it's nibbling away at low-volume, complex-part segments.
Best approach: Use 3D printing for early-stage development and pilot runs. Switch to injection molding for sustained production once the design stabilizes.
Regional Focus: Who’s Leading the Pack?
Asia-Pacific
Commands nearly 38% of the market share
China, Japan, and India are the key players
Driving force: massive automotive and consumer goods output
North America
Rapid adoption of smart machines
Strong push for reshoring manufacturing
Medical and aerospace sectors are especially active
Europe
Sustainability and recycling are top priorities
High demand for electric and hybrid machines
Germany and Italy are innovation hubs for mold design
Final Thoughts: The Developer's Advantage
Hardware developers who understand the nuances of injection molding—from machine capabilities to mold design—have a strategic edge.
In the next decade, the real innovation may not just be what you create, but how you bring it into the physical world. And with injection molding machines evolving at warp speed, your window of opportunity just got wider.
Whether you're prototyping your next breakthrough or preparing to scale a flagship product, now is the time to partner with the right molders, ask the right questions, and think ahead.
Because in hardware, execution is everything—and execution starts at the mold.
Resources to Explore: