Green Electronics Manufacturing: Reducing Waste and Energy Consumption
The electronics industry, a driving force behind modern innovation, is also one of the most resource-intensive sectors, consuming vast amounts of energy and generating significant waste. With growing environmental concerns, regulatory pressures, and an increasingly eco-conscious market, the need for green electronics manufacturing has never been greater.
2/16/20254 min read
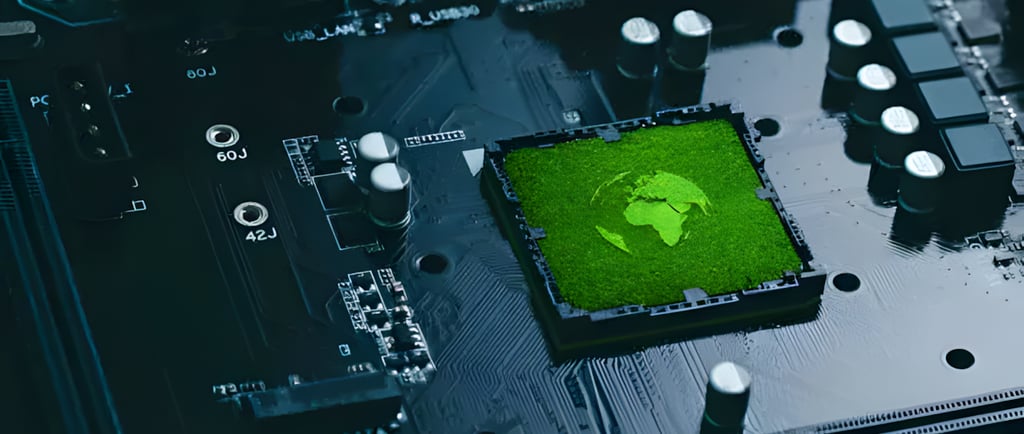
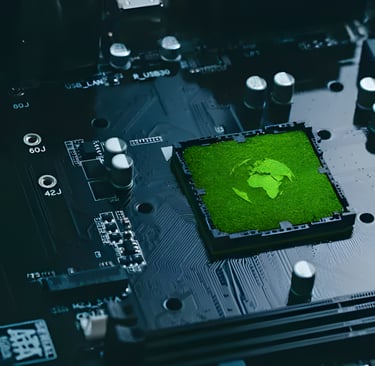
In today’s world, sustainability is no longer just a buzzword; it’s a necessity. The electronics industry, a driving force behind modern innovation, is also one of the most resource-intensive sectors, consuming vast amounts of energy and generating significant waste. With growing environmental concerns, regulatory pressures, and an increasingly eco-conscious market, the need for green electronics manufacturing has never been greater.
For designers and decision-makers in electronics development, transitioning to sustainable practices isn’t just about compliance—it’s about future-proofing businesses, reducing costs, and meeting consumer expectations. In this article, we’ll explore practical strategies to minimize waste and energy consumption while maintaining efficiency and innovation in electronics manufacturing.
The Environmental Impact of Electronics Manufacturing
Before diving into solutions, let’s examine the problem. The electronics industry contributes to pollution in several ways:
Massive Energy Consumption: Manufacturing electronic devices requires substantial energy, with semiconductor fabrication and PCB production among the biggest culprits.
Hazardous Materials: Many electronic components contain lead, mercury, and other toxic substances that can seep into ecosystems if not disposed of properly.
E-Waste Crisis: According to the Global E-Waste Monitor, the world generated over 53 million metric tons of electronic waste in 2019, and this number continues to grow. Unfortunately, only a small fraction is properly recycled.
The urgency is clear: we must adopt sustainable strategies to minimize these environmental impacts.
Strategies to Reduce Waste in Electronics Manufacturing
1. Sustainable Material Sourcing
One of the most effective ways to reduce waste starts at the material level. Many traditional electronics rely on finite resources such as rare earth metals and plastics derived from fossil fuels. Designers and manufacturers can make more sustainable choices by:
Using Recycled Materials: Many companies are now incorporating recycled plastics and metals into their designs, reducing the need for virgin materials.
Sourcing Ethical Minerals: The mining of minerals such as cobalt and lithium has significant environmental and human rights concerns. Sourcing from ethical suppliers helps mitigate these issues.
Exploring Biodegradable Alternatives: Researchers are developing biodegradable circuit boards and other eco-friendly alternatives to traditional electronic components.
2. Design for Sustainability (DfS)
Designing for sustainability is about creating products that minimize environmental impact throughout their lifecycle. Key principles include:
Modular and Repairable Designs: By designing electronics with replaceable components, manufacturers can extend product lifespans and reduce waste.
Reducing Toxic Components: Opting for lead-free solder and RoHS-compliant materials ensures a lower environmental impact.
Optimizing for Recyclability: Ensuring easy disassembly at the end of a product’s life can significantly improve recycling rates.
3. Waste Reduction in Production
Waste isn’t just about discarded products—it also occurs during manufacturing. Electronics production generates scrap materials, chemical byproducts, and excess packaging. Manufacturers can cut waste by:
Adopting Lean Manufacturing: By minimizing overproduction and streamlining processes, companies can reduce material waste.
Implementing Closed-Loop Systems: Recycling materials within the production cycle reduces the need for new resources.
Upcycling and Reusing Components: Salvaging functional components from discarded devices can significantly cut down on waste.
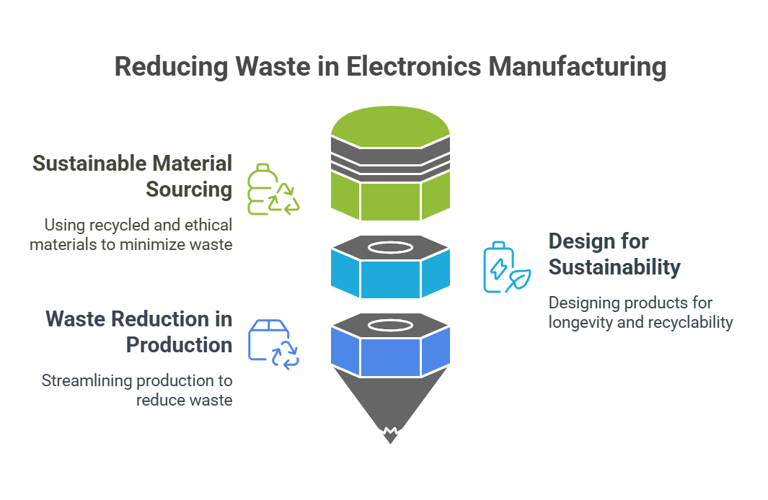
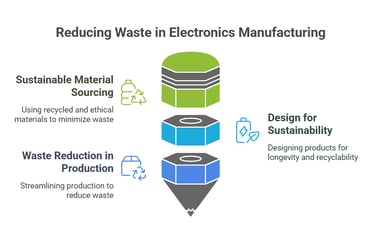
Reducing Energy Consumption in Manufacturing Processes
Energy efficiency is another pillar of green electronics manufacturing. With factories consuming vast amounts of electricity, reducing energy usage can have a profound environmental and financial impact.
1. Energy-Efficient Production Methods
Many factories still rely on outdated, energy-hungry processes. Updating to more efficient systems can yield significant savings. Key strategies include:
Switching to Renewable Energy: Solar, wind, and hydroelectric power can dramatically cut a factory’s carbon footprint.
Upgrading to Energy-Efficient Equipment: Modern machinery often features energy-saving technology, reducing consumption without sacrificing performance.
Optimizing HVAC and Lighting Systems: Simple upgrades, such as LED lighting and smart climate control, can cut energy use without major investment.
2. Smart Manufacturing & IoT Integration
The Internet of Things (IoT) and smart manufacturing tools are transforming efficiency in electronics production. By leveraging real-time data, companies can:
Monitor and Optimize Energy Use: Sensors and AI-powered analytics can identify inefficiencies and suggest improvements.
Implement Predictive Maintenance: Reducing machine downtime and preventing failures can save both energy and resources.
Automate Energy-Intensive Processes: Smart automation ensures that only necessary energy is used at any given time.
3. Sustainable Packaging Solutions
Packaging waste is another major concern in electronics manufacturing. Traditional plastic and foam packaging are non-biodegradable and contribute to landfills. Sustainable alternatives include:
Recyclable and Biodegradable Packaging: Materials like molded pulp, recycled cardboard, and plant-based plastics offer eco-friendly options.
Minimalist Packaging Designs: Reducing unnecessary layers and using compact designs cuts down on waste.
Reusable Packaging for B2B Shipping: Encouraging the use of returnable packaging solutions for bulk shipments can greatly reduce waste.
Case Studies & Industry Leaders in Green Electronics
Several companies are leading the way in sustainable electronics manufacturing. Here are a few examples:
Apple: The company aims to be 100% carbon neutral by 2030 and already uses recycled aluminum in its devices.
Dell: Known for its closed-loop recycling system, Dell incorporates recovered materials from old devices into new ones.
Fairphone: This company designs modular smartphones that prioritize repairability and ethical sourcing.
By learning from these pioneers, other manufacturers can adopt best practices to achieve sustainability goals.
Challenges and Future Outlook
Despite the many benefits of green electronics manufacturing, challenges remain. Some of the main obstacles include:
High Initial Costs: Transitioning to sustainable practices often requires significant upfront investment in new materials and technologies.
Supply Chain Complexity: Ensuring that every component comes from an eco-friendly source can be difficult.
Consumer Behavior: While sustainability is growing in importance, many consumers still prioritize price and performance over eco-friendliness.
However, the future is promising. As governments introduce stricter regulations and consumers become more conscious of sustainability, green electronics manufacturing will become the norm rather than the exception. Innovations in energy storage, biodegradable electronics, and AI-driven efficiency solutions will further drive the industry toward a more sustainable future.
Conclusion
Sustainability in electronics manufacturing isn’t just an ethical choice—it’s a strategic one. By reducing waste and energy consumption, companies can lower costs, improve brand reputation, and comply with evolving regulations.
For designers and decision-makers, the time to act is now. Whether through material choices, energy-efficient production, or waste reduction strategies, every step toward sustainability makes a difference. By embracing these practices, the electronics industry can move toward a greener, more responsible future—one circuit board at a time.