From Vacuum Tubes to Smart Factories: The Evolution of Electronics Manufacturing for Designers and Decision-Makers
Where electronics manufacturing began: in the hands of tinkerers, dreamers, and inventors who laid the groundwork for the tech we take for granted today.
2/27/20255 min read
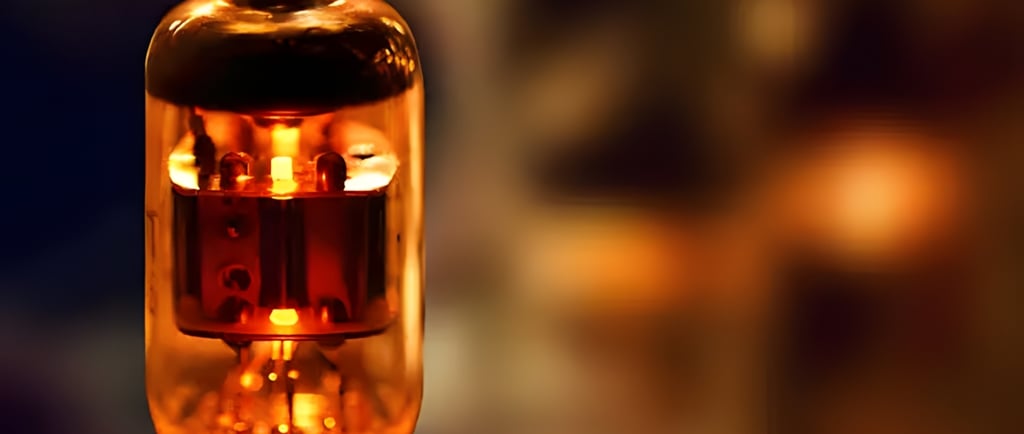
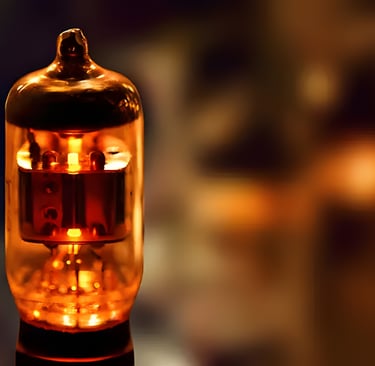
Imagine a world where your smartphone didn’t exist. No sleek touchscreens, no lightning-fast processors—just the crackle of a bulky radio or the hum of a vacuum tube-powered TV. It’s hard to picture, right? Yet, that’s where electronics manufacturing began: in the hands of tinkerers, dreamers, and inventors who laid the groundwork for the tech we take for granted today. For you—designers and decision-makers shaping the future of electronics—this journey isn’t just history. It’s a roadmap of innovation, challenges, and opportunities. Let’s walk through the evolution of electronics manufacturing, from its humble sparks to the smart factories of 2025, and see what it means for your next big project.
1. The Early Sparks: Pre-20th Century Foundations
Picture the late 1700s: candlelight flickers in a lab as Alessandro Volta stacks metal discs to create the first battery. It’s a crude contraption, but it’s the seed of everything electronic. Fast forward to the 1830s, and Michael Faraday is unraveling electromagnetism, giving us the principles that would power circuits. These weren’t "manufactured" electronics in today’s sense—think of them as bespoke experiments, hand-crafted by curious minds.
By the late 19th century, inventors started playing with vacuum tubes—glass bulbs that could control electrical currents. They were fragile, power-hungry, and a pain to produce, but they sparked a revolution. For early designers, the challenge was clear: how do you turn these lab curiosities into something practical? The answer was still decades away, but the stage was set.
2. The Dawn of Modern Electronics: Early 20th Century
Jump to 1904. John Ambrose Fleming, a British engineer with a knack for problem-solving, invents the vacuum tube diode. Suddenly, signals could be amplified, and the world of communication changed forever. Radios and telegraphs sprang to life, and manufacturers faced a new reality: people wanted these gadgets in their homes.
Production shifted from one-off experiments to something resembling a factory line. Workers—often women with nimble fingers—assembled tubes and wired circuits by hand. It was slow, messy, and expensive, but it worked. For decision-makers back then, the question was scale: how do you meet growing demand without breaking the bank? The answer came with better tools and a bit of elbow grease, but the real game-changer was still on the horizon.
3. The Mid-20th Century Boom: Transistors and the Post-War Era
Now, let’s step into 1947. It’s a chilly December day at Bell Labs when three engineers—John Bardeen, Walter Brattain, and William Shockley—unveil the transistor. This tiny semiconductor could do everything a vacuum tube could, but it was smaller, tougher, and cheaper. For designers, it was a dream come true: circuits shrank, devices multiplied, and possibilities exploded.
The post-World War II boom fueled this shift. Factories that once churned out tanks pivoted to TVs and radios. By the 1950s, you’d find families gathered around glowing screens, marveling at black-and-white broadcasts. Assembly lines got faster, and automation crept in—think clunky machines spitting out parts while engineers tweaked designs on the fly. Decision-makers had to balance cost, quality, and speed, a juggle you’re probably familiar with today. The transistor wasn’t just a component; it was a signal that electronics manufacturing was becoming an industry, not a craft.
4. The Silicon Age: Late 20th Century Innovations
Fast forward to 1958. Jack Kilby at Texas Instruments and Robert Noyce at Fairchild Semiconductor independently crack the code for integrated circuits (ICs). Picture this: instead of wiring transistors one by one, you etch them onto a silicon chip. It’s like moving from handwriting letters to printing books. Devices got smaller—think calculators fitting in your pocket instead of filling a room—and manufacturing had to keep up.
Silicon Valley became the beating heart of this revolution, but the real action spread globally. Japan honed precision manufacturing, churning out transistor radios that flooded markets. Designers wrestled with cramming more power into less space, while decision-makers eyed new hubs like Taiwan for cost-effective production. By the 1980s, personal computers from IBM and Apple were hitting desks, and mobile phones—those brick-sized relics—were ringing. The lesson? Innovation drives demand, but manufacturing makes it real.
5. Globalization and Mass Production: 1980s–2000s
Let’s zoom into the 1990s. You’re a designer sketching the next must-have gadget, and your decision-making counterpart is on the phone with a factory in Shenzhen. China’s rise as "the world’s factory" changed everything. Cheap labor, massive scale, and relentless efficiency turned ideas into products faster than ever. Walk into any home by 2000, and you’d see it: gaming consoles, flip phones, and DVD players, all born from this global shift.
Automation took a leap too. Robots didn’t just assemble; they soldered, tested, and packaged. For designers, this meant tighter tolerances and bolder ideas—think flexible PCBs or early wearable tech. But for decision-makers, it was a double-edged sword: outsourcing slashed costs but sparked debates over quality and ethics. Remember the first iPhone in 2007? It was a design marvel, but its manufacturing story—spanning continents—showed how interconnected the industry had become.
6. The Modern Era: 2010s to Today
Here we are in 2025, and the stakes are higher than ever. You’re designing for a world of AI, IoT, and flexible electronics—think bendable screens or chips powering self-driving cars. Manufacturing has gone "smart." Factories hum with sensors, data streams, and 3D printers spitting out prototypes overnight. I’ve seen engineers tweak a design in California while a Shanghai plant adjusts in real time—it’s seamless, almost magical.
But it’s not all smooth sailing. E-waste piles up, and rare earth metals for your chips come with ethical baggage. Sustainability isn’t a buzzword; it’s a mandate. Designers are pushing for modular devices—think repairable phones—while decision-makers weigh green tech against profit margins. Miniaturization still rules (hello, 2nm chips!), but the future whispers of quantum computing and nanotechnology. Your next project might not just be a product—it could redefine the industry.
Conclusion
From Volta’s battery to today’s smart factories, electronics manufacturing has been a wild ride. It’s a story of human grit—engineers hunched over workbenches, factory workers racing against quotas, and leaders betting big on untested ideas. For you, the designers and decision-makers of 2025, this history isn’t just nostalgia. It’s a reminder: every leap forward came from solving real problems, whether it was scaling vacuum tubes or greening supply chains.
The impact? It’s in your pocket, your car, your home—electronics shape how we live. Looking ahead, quantum leaps and nano-scale wonders are on the horizon. So, what’s your next move? Will you design the gadget that changes the game or greenlight the factory that builds it sustainably? The future’s yours to wire.
Call to Action
What’s your favorite piece of retro tech—the clunky Walkman or the indestructible Nokia 3310? Or maybe you’ve got a wild prediction for where electronics manufacturing is headed. Drop it in the comments—I’d love to hear your take!