The Rise of Flexible Electronics: Applications and Manufacturing Challenges
Flexible electronics, once a futuristic concept, are now becoming an integral part of modern technology. From foldable smartphones to wearable health monitors, this innovation is shaping the future of product design. But while the potential applications are vast, manufacturing challenges continue to slow widespread adoption.
2/16/20255 min read
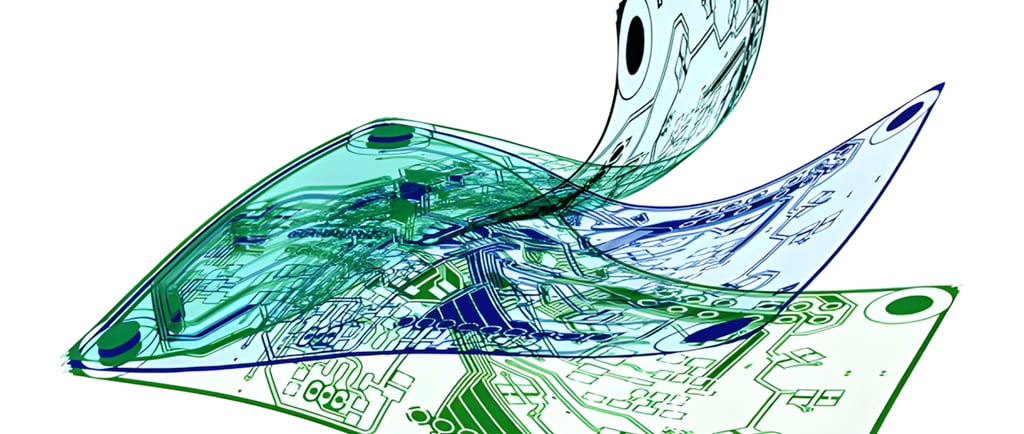
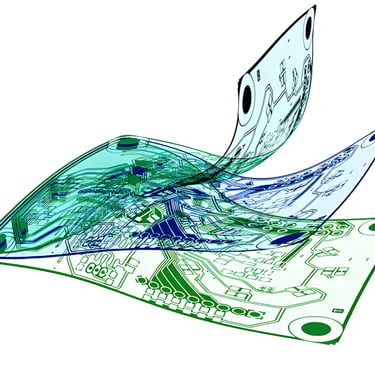
The world of electronics is undergoing a revolution—one that bends, twists, and stretches. Flexible electronics, once a futuristic concept, are now becoming an integral part of modern technology. From foldable smartphones to wearable health monitors, this innovation is shaping the future of product design. But while the potential applications are vast, manufacturing challenges continue to slow widespread adoption.
For designers and decision-makers in electronics product development, understanding the possibilities and constraints of flexible electronics is crucial. Whether you’re looking to integrate flexible components into your next product or evaluating the feasibility of mass production, this article will walk you through the key applications and hurdles you need to consider.
Key Applications of Flexible Electronics
1. Wearable Technology
The demand for wearables has surged, thanks to consumer interest in fitness tracking, health monitoring, and smart fashion. Devices like smartwatches, fitness bands, and even flexible e-textiles are powered by bendable sensors and circuits.
Imagine a yoga shirt that monitors your posture or a fitness band that seamlessly conforms to your wrist without rigid components digging into your skin. These innovations wouldn’t be possible without flexible electronics. Companies like Apple and Fitbit have already started integrating flexible sensors into their wearables, improving both comfort and performance.
2. Medical and Healthcare Devices
The healthcare industry is another major beneficiary of flexible electronics. Traditional medical devices can be uncomfortable, limiting their adoption and effectiveness. But flexible biosensors, implantable electronics, and stretchable medical devices are changing the game.
For instance, skin-like patches embedded with ultra-thin circuits can track glucose levels, heart rate, and hydration in real-time—without the need for bulky wearables. Some companies are even developing biodegradable, flexible medical implants that dissolve in the body after fulfilling their purpose, reducing the need for removal surgeries.
3. Consumer Electronics
Foldable smartphones like Samsung’s Galaxy Z series and rollable displays from LG and TCL have captured headlines, demonstrating the capabilities of flexible screens. But beyond flashy designs, flexible electronics are also paving the way for ultra-thin, lightweight e-paper tablets and next-generation displays that roll up like scrolls.
For product developers, this shift means rethinking traditional device structures. Battery placement, circuit routing, and heat dissipation need to be reconsidered when working with flexible components.
4. Automotive and Aerospace Applications
Flexible electronics are making vehicles smarter and more adaptable. Modern car dashboards now feature curved OLED screens, offering a futuristic, space-saving design. Aircraft manufacturers are also exploring flexible sensors for lightweight, adaptive monitoring systems.
Consider a scenario where an aircraft’s wing has embedded flexible sensors that detect micro-fractures in real-time, preventing catastrophic failures. Such innovations are set to redefine safety and efficiency in transportation.
5. IoT and Smart Packaging
Smart packaging is another emerging application of flexible electronics. Interactive product labels, temperature-sensitive indicators for food safety, and printed NFC or RFID tags enhance both functionality and user experience.
For example, a pharmaceutical company might use smart blister packs with flexible circuits that notify patients when it’s time to take their medication. This level of interactivity opens new doors for branding and product differentiation.
6. Energy and Sustainability
Flexible solar panels and energy-harvesting devices are gaining momentum. These ultra-thin, rollable solar cells can be integrated into clothing, backpacks, or even building facades, making renewable energy more accessible.
Additionally, researchers are developing wearable batteries and printed supercapacitors that can conform to any shape, enabling truly flexible and self-powered electronics.
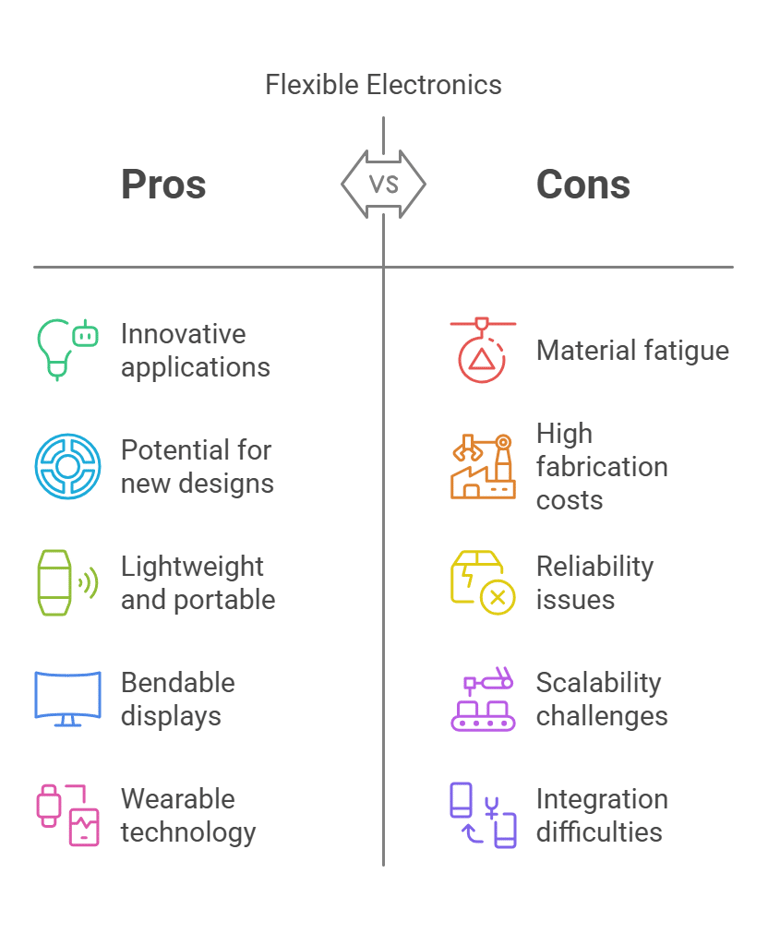

Manufacturing Challenges in Flexible Electronics
While the applications are exciting, flexible electronics pose significant manufacturing hurdles. Product designers and engineers need to consider these challenges early in the development process.
1. Material Limitations
Unlike traditional rigid circuit boards, flexible electronics require materials that can bend without breaking while maintaining electrical conductivity. Options like conductive polymers, graphene, and silver nanowires offer promising solutions, but they come with trade-offs in cost, durability, and performance.
A major concern is material fatigue. How many bends can a flexible device withstand before performance degrades? Finding the right balance between flexibility and longevity is an ongoing challenge.
2. Fabrication Complexity
Traditional semiconductor manufacturing relies on rigid substrates like silicon. Flexible electronics, on the other hand, require entirely new fabrication methods—such as roll-to-roll printing and inkjet printing of conductive materials.
This shift presents a learning curve for manufacturers. Unlike well-established PCB assembly processes, flexible electronics demand specialized equipment and techniques, which can lead to higher initial costs and lower yield rates.
3. Reliability and Durability Issues
Flexible electronics must withstand bending, twisting, and stretching without losing functionality. However, mechanical stress can cause tiny cracks in conductive traces, leading to reliability issues.
To address this, researchers are developing self-healing materials and encapsulation techniques that prevent environmental damage. But for now, ensuring long-term durability remains one of the biggest obstacles.
4. Scalability and Cost Challenges
While flexible electronics hold great potential, mass production is still expensive. The industry lacks standardized manufacturing techniques, making economies of scale difficult to achieve.
For startups and smaller product developers, high upfront costs for R&D and production setup can be a significant barrier. Unless the demand justifies the investment, flexible electronics may not be a viable option for every product.
5. Integration with Existing Electronics
Another challenge is how flexible components interact with traditional electronics. Hybrid designs—where flexible and rigid parts coexist—require careful engineering to maintain performance and reliability.
For instance, how do you integrate a flexible display with a standard rigid battery? These design questions require creative problem-solving and often lead to unconventional product architectures.
Future Trends and Innovations
Despite these challenges, flexible electronics continue to advance rapidly. Here’s what’s on the horizon:
New Materials: Graphene, liquid metal circuits, and self-healing polymers are being developed to improve durability and conductivity.
3D Printing & Additive Manufacturing: These methods could revolutionize how flexible electronics are produced, reducing costs and improving customization.
AI in Manufacturing: Machine learning is being used to optimize production processes, reduce defects, and improve material selection.
Self-Powered Devices: Advances in energy harvesting could lead to wearables and IoT devices that don’t need batteries.
For product designers and decision-makers, staying ahead of these trends is crucial. The companies that successfully navigate these challenges will be the ones defining the next generation of consumer electronics.
Conclusion
Flexible electronics are reshaping industries, from healthcare and consumer tech to automotive and IoT. But while the potential is vast, manufacturing challenges must be carefully managed.
For designers and developers, success in this field will require a deep understanding of materials, fabrication techniques, and integration strategies. Those who invest in overcoming these hurdles will be at the forefront of innovation, driving the next wave of groundbreaking electronic products.
If you're considering integrating flexible electronics into your next project, start by identifying the key constraints early. Collaborate with material scientists, explore emerging fabrication techniques, and keep an eye on evolving industry standards.
The future of electronics isn’t just rigid—it’s flexible, adaptable, and full of possibilities. Are you ready to take advantage of it?