FAQs: Metal Fabrication for Electronics Manufacturers
What’s the secret behind these everyday miracles of durability? Spoiler alert: it’s metal fabrication. We’re tackling the most common questions you’ve likely Googled late at night: What is metal fabrication in electronics? How does it make your designs tougher? And why should you care?
2/26/20256 min read
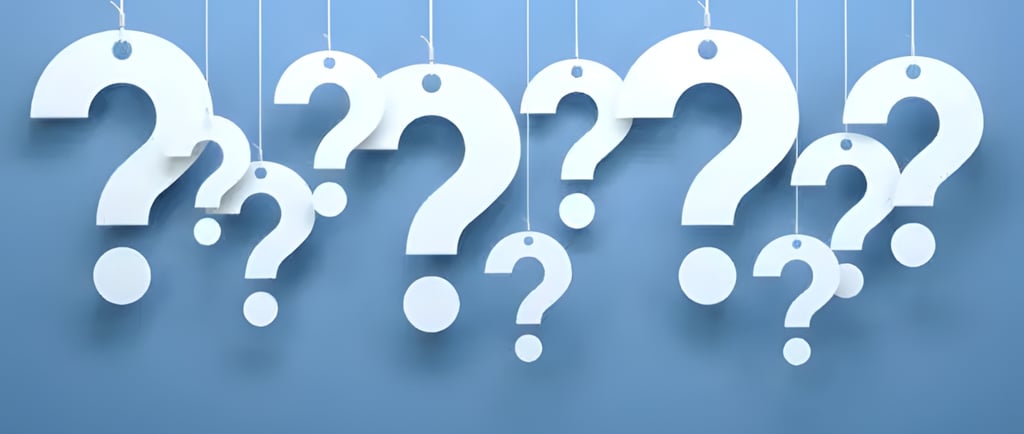
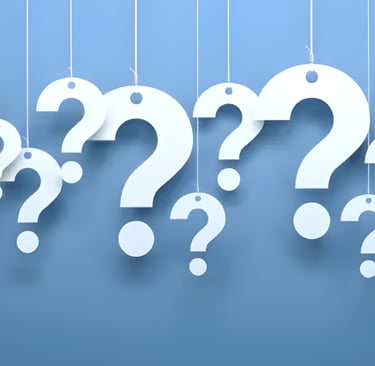
Imagine dropping your smartphone on the pavement—again—and it still powers up without a hitch. Or picture a server humming away in a dusty basement, unfazed by years of heat and grime. What’s the secret behind these everyday miracles of durability? Spoiler alert: it’s metal fabrication. For designers and decision-makers in electronics development, understanding this craft isn’t just a nice-to-have—it’s a game-changer. In this article, we’re tackling the most common questions you’ve likely Googled late at night: What is metal fabrication in electronics? How does it make your designs tougher? And why should you care? Let’s dive in and get you the answers you need to impress your team—and your clients.
What Is Metal Fabrication in Electronics?
Let’s start with the basics. Metal fabrication is the art of turning raw metal into the backbone of your electronic devices. Think of it as the hands-on process of cutting, bending, and assembling metal to create everything from sleek laptop enclosures to rugged circuit board frames. It’s not just about slapping some steel together—it’s about precision, purpose, and making sure those tiny chips and wires have a home that won’t let them down.
In the electronics world, fabrication shows up in parts like chassis, heat sinks, connectors, and shielding. If you’ve ever marveled at how a tablet feels solid yet lightweight, you’ve got metal fabrication to thank. Designers, this is your playground for turning sketches into reality. Decision-makers, this is where you ensure your product doesn’t end up as a paperweight after a single tumble.
Why Is Metal Fabrication Important for Electronics Manufacturers?
Here’s where it gets real. Metal fabrication isn’t just a step in the process—it’s a lifeline for your product’s success. For designers, it’s about nailing precision down to the micrometer. For decision-makers, it’s the difference between a prototype that wows investors and one that flops.
First, there’s durability. Metal gives your electronics the guts to survive drops, vibrations, and even the occasional coffee spill (we’ve all been there). Then there’s precision—modern tools like CNC machines and laser cutters let you craft parts so exact that every screw fits like it was born for the job. And don’t forget customization. Need a heat sink with an odd shape to fit your latest design? Metal fabrication’s got your back. It’s like having a tailor for your tech, stitching together solutions that off-the-shelf parts can’t touch.
How Does Metal Fabrication Improve Durability in Electronics?
Let’s talk toughness. You’re designing a gadget that’s going to get tossed in backpacks, bolted into machinery, or left out in the rain—durability isn’t optional. Metal fabrication steps up with materials like aluminum, stainless steel, and copper that laugh in the face of wear and tear.
Take aluminum: it’s lightweight but packs a punch against corrosion—perfect for that sleek, portable device you’re sketching out. Stainless steel? It’s the go-to for rugged environments, like industrial controllers that need to shrug off dust and dents. And copper? It’s not just conductive—it’s a heat-dissipating champ, keeping your circuits cool under pressure.
Then there’s thermal management. Ever fried a laptop by running too many tabs? Heat sinks—those finned metal heroes—pull heat away from delicate components, giving your device a longer life. I once worked on a project where a military-grade radio outlasted its warranty by years, all thanks to a beefy fabricated enclosure that kept the insides safe and cool. That’s the kind of reliability you’re signing up for.
What Are the Common Metal Fabrication Techniques Used in Electronics?
Now, let’s peek under the hood at how this magic happens. Metal fabrication isn’t one-size-fits-all—it’s a toolkit of techniques, each with a job to do.
Cutting: Laser cutting is the rockstar here. It slices through metal with pinpoint accuracy, perfect for intricate parts like brackets or frames for circuit boards. Waterjet cutting’s another contender, blasting through thicker sheets without heating things up.
Forming: This is where flat metal gets its personality. Bending presses and stamping machines shape sheets into enclosures or mounts. Ever wonder how a laptop lid gets that smooth curve? That’s forming at work.
Joining: Welding fuses parts together for strength, while riveting or soldering handles delicate assemblies. Picture the tiny connectors inside your phone—soldering keeps them tight and functional.
Designers, these are your brushes—pick the right one, and your vision comes to life. Decision-makers, knowing these techniques helps you spot a fabrication partner who can deliver on your specs.
What Materials Are Typically Used in Metal Fabrication for Electronics?
Choosing the right metal is like picking the perfect coffee roast—it depends on what you’re going for. Here’s the lineup:
Aluminum: The lightweight champ. It’s corrosion-resistant and easy to work with, making it a favorite for portable devices like tablets or wearables. Bonus: it’s affordable.
Stainless Steel: The tough guy. It’s heavier but unbeatable for strength and durability—think industrial machinery or medical equipment that can’t fail.
Copper: The heat-and-electricity wizard. It’s pricier, but when you need conductivity or thermal performance (hello, heat sinks), copper’s your VIP.
What’s the catch? Weight, cost, and performance trade-offs. Aluminum’s light but not as strong as steel. Copper’s a dream for heat, but it’ll dent your budget. Designers, sketch with these in mind. Decision-makers, weigh these against your product’s goals—durability vs. portability, cost vs. quality.
How Does Metal Fabrication Affect Cost and Production Time?
Let’s talk dollars and days—because no one’s got an unlimited budget or calendar. Fabrication costs hinge on a few things: the metal you pick, how complex your design is, and how many units you’re cranking out. Aluminum’s cheaper than copper, sure, but throw in a dozen custom bends and laser-cut details, and the bill climbs. Scale up to mass production, though, and per-unit costs drop like a rock.
Production time’s a similar story. A one-off prototype with manual tweaks might take weeks. But fire up a CNC machine for a big run, and you’re looking at days—or hours. I once saw a team shave a month off their timeline by switching to automated laser cutting for a server chassis. The upfront investment stung, but the speed paid off when deadlines loomed.
Here’s the kicker: quality fabrication saves cash long-term. A flimsy enclosure might be cheap now, but when it cracks and your warranty claims pile up, you’ll wish you’d spent more upfront. Balance is everything.
Can Metal Fabrication Be Sustainable for Electronics?
Sustainability’s not just a buzzword—it’s a selling point, especially when your clients care about green creds. Good news: metal fabrication can play nice with the planet.
Most metals—like aluminum and steel—are recyclable, meaning your old prototypes don’t have to clog landfills. Modern techniques help too. Laser cutting wastes less material than old-school hacksaws, and smart design software optimizes every sheet to squeeze out extra parts. I’ve seen shops turn scrap into new stock, cutting costs and carbon footprints.
Decision-makers, this is your pitch to eco-conscious buyers. Designers, it’s a chance to flex your creativity—can you tweak that enclosure to use less metal without losing strength? It’s a win-win.
How Do Electronics Manufacturers Choose a Metal Fabrication Partner?
So, you’re sold on fabrication—now what? Picking the right partner is like dating: you need compatibility, trust, and a little spark. Here’s what to look for:
Expertise: They should know electronics inside out—think EMI shielding for sensitive circuits or tolerances tighter than a drum. Generalists won’t cut it.
Certifications: ISO 9001 or AS9100 mean they’re serious about quality. It’s your insurance against sloppy work.
Capacity: Can they handle your wild prototype and crank out 10,000 units? Flexibility matters.
Pro tip: Ask about lead times and where they source materials. A shop that’s fast but uses sketchy suppliers might tank your timeline—or your reputation. I once worked with a fabricator who promised the moon but delivered late because their steel shipment got stuck overseas. Lesson learned: dig into the details.
Conclusion
Metal fabrication isn’t just a manufacturing step—it’s the unsung hero behind every durable, precise, and downright impressive electronic device you’ve ever designed or approved. From shielding fragile circuits to dissipating heat like a pro, it’s the backbone that turns your ideas into products people trust. Designers, it’s your ticket to pushing boundaries. Decision-makers, it’s your assurance that quality meets the bottom line.
So, what’s next? Whether you’re sketching your next big thing or scouting a fabrication partner, now’s the time to lean into this craft. Ready to enhance your electronics with metal fabrication? Reach out to an expert—or drop a comment below with your own fabrication wins. Let’s keep the conversation going.