Ensuring Excellence: Quality Assurance in Electronics Metal Fabrication
Metal fabrication isn’t just some industrial grunt work; it’s the backbone of reliable electronics. From the chassis holding your circuit boards to the shielding that keeps interference at bay, these components have to be spot-on.
2/26/20256 min read
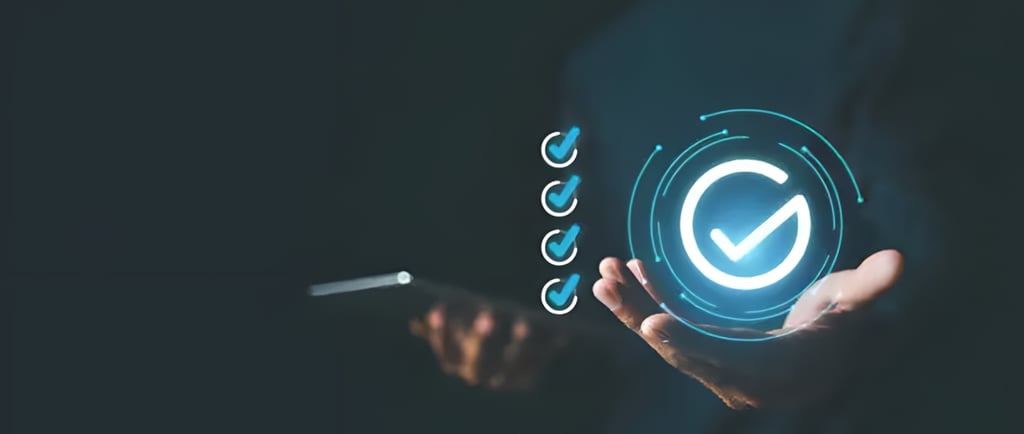
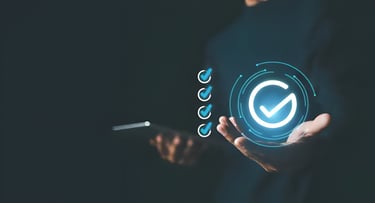
Imagine you’re designing the next big thing in electronics—a sleek wearable that tracks health metrics or a compact module powering a self-driving car. You’ve got the circuits mapped out, the software humming, and a vision that could change the game. But then, a tiny metal enclosure warps under heat, or a connector bends just enough to throw off the whole assembly. Suddenly, your brilliant idea is a pile of scrap. That’s where quality assurance in metal fabrication steps in—because in electronics, the smallest oversight in metalwork can tank the biggest dreams.
Metal fabrication isn’t just some industrial grunt work; it’s the backbone of reliable electronics. From the chassis holding your circuit boards to the shielding that keeps interference at bay, these components have to be spot-on. For designers and decision-makers, understanding how precision and quality control in this process tie directly to performance—and your bottom line—isn’t optional. It’s essential. Let’s dive into why this matters and how it ensures your products not only meet industry standards but exceed expectations.
The Unsung Hero: Metal Fabrication in Electronics
Picture this: you’re piecing together a puzzle, and every part has to fit just right. That’s metal fabrication in electronics. It’s the art of cutting, bending, welding, and assembling metal into the bits that make your devices tick—think heat sinks pulling heat off a processor, enclosures protecting delicate internals, or connectors linking it all together. These aren’t glamorous parts, but they’re the unsung heroes keeping your electronics alive.
Why does the metal itself matter? It’s not just about looking shiny. The right alloy conducts electricity without frying, stands up to humidity or vibration, and lasts through years of use. Designers, you know that a flimsy heat sink can cook a chip faster than you can say “thermal runaway.” Decision-makers, you’ve seen how a single failure in the field can spiral into a PR nightmare. Metal fabrication sets the stage for everything else—so it’s got to be done right.
Precision: Where the Magic Happens
Let’s talk precision. In metal fabrication, it’s not about “close enough.” It’s about hitting tolerances tighter than a gnat’s eyelash—sometimes down to thousandths of an inch. Why? Because in electronics, a hairline gap can mean a loose fit that rattles apart or a misaligned shield that lets EMI (electromagnetic interference) wreak havoc. Precision ensures every piece slots in perfectly, like Lego bricks snapping together.
How do fabricators pull this off? They lean on tools like CNC machines that carve metal with robotic accuracy, laser cutters that slice cleaner than a chef’s knife, and measuring gear that could spot a flaw you’d need a microscope to see. I once toured a shop where they showed me a connector pin—barely bigger than a pencil tip—crafted so precisely it mated with its socket like they were made for each other. A fraction off, and it’d either jam or fall out. That’s the stakes designers face: your specs might look great on paper, but if the metalwork doesn’t match, you’re sunk.
For you decision-makers, precision isn’t just a buzzword—it’s a cost saver. Get it right the first time, and you’re not scrapping parts or fielding warranty claims. It’s the difference between a prototype that sings and one that sits in the “lessons learned” bin.
Quality Control: Catching Trouble Before It Strikes
Now, precision’s only half the battle. Even the best machines can hiccup, and that’s where quality control (QC) comes in. Think of QC as the eagle-eyed coach who spots every fumble before the game’s on the line. It’s about catching defects—scratches, burrs, or wonky dimensions—before they sneak into your assembly line.
What does QC look like in action? It starts simple: a worker squinting at a surface to spot pits or cracks. Then it ramps up with tools like calipers or fancy CMMs (Coordinate Measuring Machines) that map a part in 3D to confirm it matches the blueprint. They’ll test the metal itself—does it resist rust? Can it take a beating without bending? And for critical parts, they might stress-test it, mimicking years of heat and vibration in a few hours.
I heard about a company once that skipped a QC step on a batch of enclosures. Looked fine, shipped fine—until users noticed their devices buzzing like angry bees. Turns out, a tiny warp let interference leak in. A quick dimensional check could’ve saved them a recall. That’s the power of QC: it’s your safety net.
For designers, this means your wildest ideas—those razor-thin profiles or intricate shapes—can work if QC backs you up. Decision-makers, it’s your insurance policy. Automation’s kicking in here, too—AI systems now scan parts faster than any human, flagging issues with eerie accuracy. It’s not about replacing people; it’s about giving them superpowers to keep quality sky-high.
Playing by the Rules: Industry Standards
Let’s get real: electronics isn’t a free-for-all. There are standards—think IPC for electronics manufacturing or ISO 9001 for quality systems—that set the bar. These aren’t just hoops to jump through; they’re the playbook for making sure your stuff works, plays nice with other tech, and doesn’t catch fire in someone’s pocket.
Take IPC standards. They dictate everything from solder joints to component spacing, but metal fabrication’s in there too—ensuring enclosures don’t short out circuits or heat sinks actually sink heat. ISO 9001’s broader—it’s about your whole process, from raw metal to finished product, proving you’ve got quality locked down. Meet these, and you’re golden in the market. Miss them, and you’re risking everything from compatibility headaches to legal messes.
I talked to an engineer who’d seen a competitor cut corners on shielding to save a buck. Worked fine in the lab—until it hit the field and interfered with nearby devices. Regulators stepped in, and that company’s still digging out of the hole. Standards aren’t optional; they’re your ticket to credibility. Designers, you’ll love how they give you clear targets to hit. Decision-makers, they’re your shield against chaos.
Why It All Pays Off
So, what’s the payoff for sweating the small stuff in metal fabrication? First, reliability. When your parts are precise and QC’d to death, they don’t fail halfway through a product’s life. Your smartwatch keeps ticking, your server keeps humming—customers notice that. I’ve got a buddy whose decade-old stereo still works because the metal guts were built to last. That’s the goal.
Then there’s cost. Yeah, upfront investment in precision tools or QC tech isn’t cheap—but compare that to reworking a batch or eating a recall. A shop I know caught a defect early with a $10 gauge; skipping it would’ve cost them $50,000 in scrapped units. Penny-wise, pound-foolish doesn’t fly here.
Customer trust ties it all together. Deliver a device that doesn’t flake out, and people come back. Designers, you get to push boundaries—think slimmer phones or denser boards—because quality fabrication can handle it. Decision-makers, you’re not just shipping products; you’re building a reputation. And in a world where one viral teardown can tank a brand, that’s gold.
Oh, and innovation? Precision and QA let you dream big. That wild concept with micro-components or extreme conditions—it’s doable if the metalwork’s flawless. I saw a prototype for a drone motor housing so tiny yet tough it blew my mind. Quality made it possible.
Wrapping It Up: The Stakes Are High
Here’s the bottom line: in electronics, metal fabrication isn’t just a step—it’s a make-or-break moment. Precision ensures your designs come to life as intended, while quality control keeps the gremlins out. Together, they guarantee your products hit those industry standards that keep you in the game. For designers, it’s the freedom to create without fear of failure. For decision-makers, it’s the confidence that your investment won’t end up as tomorrow’s landfill.
So, what’s the move? Invest in the good stuff—cutting-edge fabrication tech, rigorous QA workflows, and a team that gets it. Tour a shop, ask hard questions, and don’t settle for “good enough.” In a world where we’re all glued to our gadgets, the metal behind the magic matters more than ever. Make it excellent, and you’ll not only meet expectations—you’ll redefine them.