Electronics Manufacturing News Unveiled: Must-Know Trends and Challenges for Designers and Decision-Makers in 2025
The electronics manufacturing world is buzzing louder than a soldering iron on a fresh circuit board. The stakes have never been higher—new tech is exploding onto the scene, supply chains are twisting like a bad PCB trace, and everyone’s asking, “What’s next?”
2/28/20257 min read
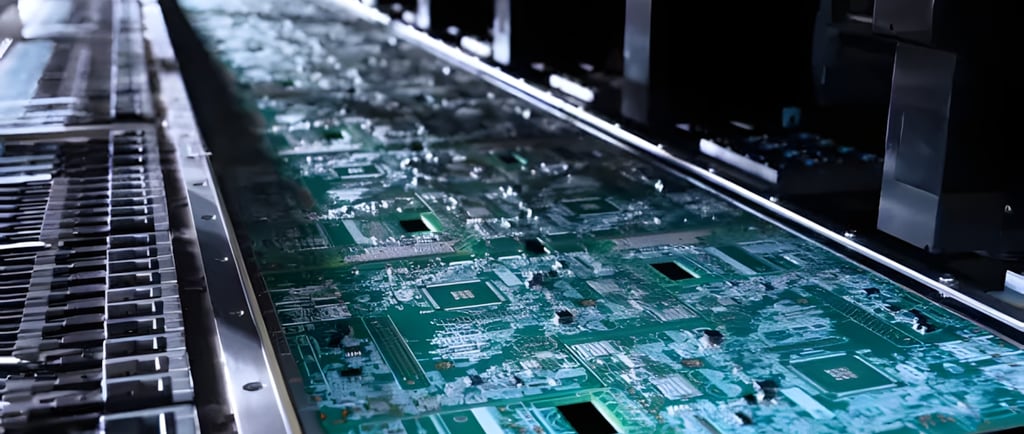
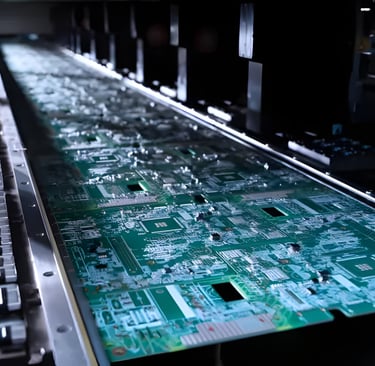
Imagine this: you’re sketching out the next big thing in wearable tech, or maybe you’re the one signing off on a multi-million-dollar factory expansion. Either way, the electronics manufacturing world is buzzing louder than a soldering iron on a fresh circuit board. The stakes have never been higher—new tech is exploding onto the scene, supply chains are twisting like a bad PCB trace, and everyone’s asking, “What’s next?” If you’re a designer or decision-maker in electronics development, staying ahead isn’t just smart—it’s survival.
This article dives into the pulse of electronics manufacturing today. From jaw-dropping innovations to the headaches keeping industry leaders up at night, we’re unpacking it all. By the end, you’ll have a clearer picture of where things stand in early 2025 and how to steer your projects—or your company—through the chaos. Let’s get started.
Industry Trends and Innovations
The electronics manufacturing landscape is shifting fast, and it’s thrilling to watch. For designers, these trends aren’t just headlines—they’re the tools and constraints shaping your next prototype. For decision-makers, they’re the bets you’re placing on the future.
Emerging Technologies
First up, semiconductors are shrinking again. We’re talking 3nm chips now hitting production lines, courtesy of giants like TSMC and Samsung. Smaller nodes mean more power in less space—perfect for that sleek fitness tracker you’re designing or the edge AI device your team’s pitching. Meanwhile, flexible electronics are bending the rules (literally). Picture a foldable display that doesn’t crack under pressure or a sensor woven into fabric. These aren’t sci-fi dreams anymore—they’re on factory floors, and they’re begging for creative minds to push them further.
Automation and AI Integration
Factories aren’t what they used to be. Robots don’t just assemble parts—they optimize workflows. I talked to a friend who toured a smart factory last month, and he couldn’t stop raving about how AI predicts machine failures before they happen. Companies like Foxconn are leaning hard into this, cutting downtime and boosting output. For designers, this means tighter tolerances and faster prototyping. For decision-makers, it’s a chance to slash costs—if you can stomach the upfront investment.
Sustainability Efforts
Green isn’t just a buzzword—it’s a mandate. Regulators are cracking down on e-waste, and consumers are demanding eco-friendly gadgets. I’ve seen manufacturers swap out toxic materials for biodegradable alternatives, and recycling programs are popping up everywhere. It’s a headache to retool a supply chain, sure, but it’s also an opportunity. Imagine pitching a device that’s as planet-friendly as it is cutting-edge. That’s a win designers and execs can both get behind.
Recent News Highlights
Let’s zoom in on what’s making waves right now. These aren’t just stories—they’re the context for your next big move.
Major Company Updates
TSMC dropped a bombshell last fall: a new $12 billion plant in Arizona’s cranking up production. More chips stateside could ease your supply woes if you’re stateside too. Meanwhile, Samsung’s eyeing a merger rumor with a smaller rival—nothing’s confirmed, but the buzz has decision-makers rethinking partnerships. Closer to home, I heard from a colleague at a trade show that smaller firms are teaming up to compete with the big dogs. Collaboration might be your ticket to staying agile.
Supply Chain Developments
Remember the chip shortage that had us all scrambling? It’s easing—sort of. Analysts say automotive-grade chips are flowing again, but high-end consumer stuff’s still bottlenecked. China’s export restrictions aren’t helping, and with tensions simmering, decision-makers are sweating over where to source next. Designers, this might mean tweaking specs to dodge delays. I’ve been there—swapping a part mid-design isn’t fun, but it beats missing a deadline.
Breakthrough Products
On the bright side, new toys are hitting shelves. Nvidia’s latest GPU is a beast—perfect for the gaming rig you’re dreaming up. And quantum computing? IBM’s teasing hardware that could change everything. I saw a demo clip online—mind-blowing stuff. These breakthroughs aren’t just cool—they’re challenges. Can your team design for them? Can your budget afford them?
Challenges Facing the Industry
It’s not all shiny circuits and victory laps. The road ahead’s got some potholes, and they’re hitting designers and decision-makers square in the gut.
Economic Pressures
Inflation’s biting hard. Raw materials like copper and rare earths are pricier than ever, and that trickles down to your BOM (bill of materials). I chatted with a designer buddy who’s scrambling to keep a project under budget—sound familiar? For execs, it’s a pricing dilemma: absorb the hit or pass it to customers who’re already stretched thin?
Workforce and Skills Gap
Talent’s another headache. The industry needs engineers who can code, design, and troubleshoot—yesterday. But schools aren’t churning them out fast enough. I’ve heard decision-makers groan about training costs, while designers lament burnout from wearing too many hats. It’s a grind, and there’s no quick fix.
Environmental and Ethical Concerns
Then there’s the human cost. Reports of rough labor conditions in some manufacturing hubs keep surfacing—think long hours, low pay. Plus, cranking out millions of devices leaves a carbon footprint the size of a small country. Designers, you’re caught between specs and ethics. Decision-makers, you’re juggling PR and profit. It’s messy, but ignoring it isn’t an option.
Future Outlook
So, where’s this rollercoaster headed? Let’s peek around the corner.
Predictions for 2025 and Beyond
IoT’s exploding—smart homes, cities, you name it. 5G’s finally hitting its stride, and electric vehicles are gobbling up chips like candy. I’d bet my last coffee on quantum tech making waves too. But disruptions loom—new tariffs or a surprise breakthrough could flip the script overnight. Designers, keep your sketches flexible. Decision-makers, hedge those bets.
Opportunities for Stakeholders
Here’s the silver lining: growth means room to shine. Designers can pioneer that killer app for IoT or EV. Execs can lock in suppliers early or pivot to green tech for a PR boost. I’ve seen small teams outmaneuver giants by jumping on trends first—could that be you?
Conclusion
The electronics manufacturing world in 2025 is a wild ride—equal parts thrilling and terrifying. From tiny chips to global supply chains, every move counts. Designers, you’ve got the tools to innovate like never before. Decision-makers, your calls today shape tomorrow’s wins. Keep your ear to the ground, your hands on the wheel, and don’t be afraid to take a risk.
What do you think—ready to tackle this beast? Drop your thoughts below, share this with your team, or dig into more resources to stay sharp. The future’s bright, a little scary, and totally ours to build.
Brainstorm:
Automation and AI Integration in Electronics Manufacturing
1. Streamlined Assembly Lines
Robotic Arms with Precision: Think of those nimble robotic arms you see in car factories—now they’re placing tiny capacitors on circuit boards with micron-level accuracy. No more shaky human hands fumbling with tweezers.
Pick-and-Place Systems: Automated machines grab components from reels or trays and slap them onto PCBs faster than you can blink. AI tweaks their movements in real-time to avoid errors, like a maestro conducting a symphony of metal and silicon.
Dynamic Line Balancing: AI watches the flow—say one station’s lagging—and reroutes tasks to keep the whole line humming. It’s like traffic control for production.
2. Quality Control That Never Sleeps
Vision Systems: Cameras paired with AI scan every solder joint or chip placement. They catch defects—like a hairline crack or misaligned pin—that a tired inspector might miss after a long shift.
Predictive Defect Detection: AI learns from past mistakes. If a batch of resistors keeps failing at a certain temp, it flags the pattern before the whole run’s toast.
Automated Testing: Robots run electrical tests on finished boards, tweaking parameters on the fly based on AI insights. Cuts down on rework and scrap.
3. Supply Chain and Inventory Smarts
Real-Time Inventory Tracking: AI keeps tabs on every screw and chip in the warehouse, predicting when you’ll run low based on production pace and lead times. No more “oops, we’re out” moments.
Demand Forecasting: By crunching sales data, market trends, and even weather (think holiday gadget rushes), AI tells you how many units to ramp up—or down.
Supplier Optimization: Automation bots negotiate with suppliers or flag cheaper alternatives, while AI weighs quality vs. cost. It’s like having a tireless procurement team.
4. Predictive Maintenance
Machine Health Monitoring: Sensors on a reflow oven or CNC machine feed data to AI, which predicts when a motor’s about to burn out—before it halts the line. Think of it as a crystal ball for breakdowns.
Self-Healing Systems: Some setups tweak themselves—adjusting belt tension or recalibrating lasers—based on AI’s nudge, cutting downtime to near zero.
Scheduled Downtime Planning: AI picks the least painful moment to swap a part, so you’re not scrambling mid-rush.
5. Design-to-Production Bridge
Simulation and Prototyping: AI runs virtual stress tests on a new PCB layout, flagging weak spots before the first solder melts. Designers get feedback in hours, not weeks.
Tool Path Optimization: For CNC milling or 3D printing parts, automation plots the fastest, least wasteful path, while AI fine-tunes it for material quirks.
Digital Twins: A virtual replica of the factory runs alongside the real one. AI plays “what if” with production tweaks—say, a new chip spec—without risking the actual floor.
6. Worker Support and Upskilling
Cobots (Collaborative Robots): These aren’t replacing humans—they’re helping. A cobot hands you tools or holds a board steady while you debug, like a trusty apprentice.
AI Training Guides: New hires pop on AR goggles, and AI walks them through soldering a tricky joint, step-by-step, adapting to their pace.
Ergonomic Adjustments: Automation repositions heavy equipment or adjusts workstation heights based on AI’s analysis of worker fatigue data. Keeps the team fresh.
7. Energy and Resource Efficiency
Smart Power Management: AI dials down idle machines or shifts high-energy tasks to off-peak hours, slashing the electric bill.
Material Waste Reduction: Automation cuts components with surgical precision, while AI predicts exactly how much raw stock you’ll need—no excess bins of copper scraps.
Heat Recycling: In plants with reflow ovens, AI optimizes heat recapture, turning waste into savings.
8. Customization at Scale
Mass Personalization: Ever ordered a gadget with your name etched on it? Automation swaps parts or tweaks finishes on the fly, guided by AI crunching customer specs.
Batch-of-One Production: AI reconfigures the line for a single unique order—like a custom medical device—then flips back to mass production without missing a beat.
Rapid Iteration: Designers tweak a product mid-run; AI reprograms the bots, and boom—new version’s rolling out by morning.
9. Data-Driven Decision Making
Real-Time Analytics: Dashboards fed by AI show execs output rates, defect trends, or bottlenecks as they happen—not in next week’s report.
Scenario Planning: AI models “what if we double GPU production?” and spits out costs, timelines, and risks. Decision-makers aren’t guessing anymore.
Competitor Benchmarking: AI scrapes public data (say, from X posts or press releases) to see how rivals are using automation—keeping you one step ahead.
10. Pushing the Envelope
Self-Optimizing Factories: Imagine a plant where AI doesn’t just react—it experiments. It tests new layouts or speeds overnight, learning what works best.
Swarm Robotics: Tiny bots work like ants, coordinating via AI to assemble complex devices—no central control, just pure hive-mind efficiency.
AI-Designed Processes: Why stop at products? AI could dream up entirely new manufacturing methods, like a radical way to fuse circuits we haven’t thought of yet.