Electronics Manufacturing Case Studies: Real-World Success Stories for Designers and Decision-Makers
Success in this fast-paced electronics manufacturing world doesn’t come from guesswork. It comes from learning what works—and what doesn’t—straight from the trenches. That’s where case studies swoop in like a trusty mentor.
3/4/20255 min read
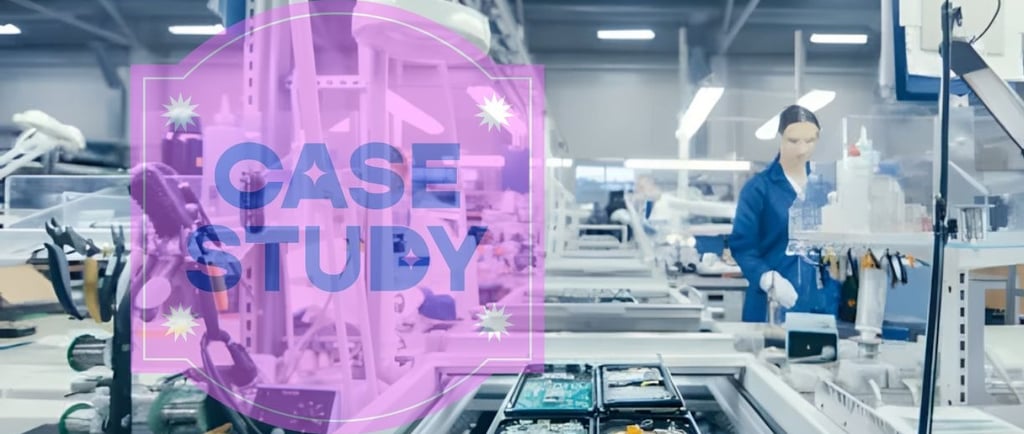
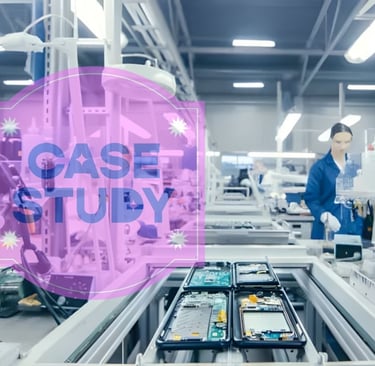
Imagine this: the global electronics manufacturing industry is barreling toward a staggering $1 trillion valuation by 2030, fueled by relentless innovation and razor-sharp efficiency. For designers sketching the next big gadget and decision-makers steering production, this isn’t just a statistic—it’s a call to action. Electronics manufacturing isn’t some abstract process humming away in sterile factories; it’s the heartbeat of everything from smartphones to smart homes.
But here’s the kicker: success in this fast-paced world doesn’t come from guesswork. It comes from learning what works—and what doesn’t—straight from the trenches. That’s where case studies swoop in like a trusty mentor. They’re real-world stories of triumph, grit, and ingenuity, offering a roadmap for anyone in electronics development. In this article, we’re diving into three standout electronics manufacturing case studies that unpack innovation, problem-solving, and sustainability. Whether you’re a designer dreaming up circuits or a decider signing off on budgets, these tales are for you.
The Importance of Case Studies in Electronics Manufacturing
Let’s get real—electronics production is a beast. One misstep in design or a hiccup in the supply chain can tank a project faster than you can say "prototype." Case studies aren’t just dry reports; they’re goldmines of insight. They show how others have tackled the same headaches you’re facing—like sourcing rare components or shaving seconds off assembly time.
Think of them as a backstage pass to the industry’s biggest trends: automation zipping through factories, sustainability climbing the priority list, and miniaturization pushing the limits of physics. For designers, they spark ideas for smarter layouts. For decision-makers, they’re proof of what delivers ROI. By the end of this piece, you’ll walk away with lessons you can actually use—no fluff, just results.
Case Study 1: Flex – Overcoming Supply Chain Disruptions
Picture this: it’s 2021, and the world’s still reeling from a pandemic. Flex, a giant in electronics manufacturing services (EMS), is staring down a nightmare—chip shortages are choking their production lines. They’re building everything from medical devices to automotive tech, and clients are breathing down their necks.
The Challenge: Supply chains were a mess. Semiconductors, those tiny lifebloods of electronics, were stuck in a global bottleneck. Lead times stretched from weeks to months, and costs spiked.
The Solution: Flex didn’t just sit there wringing their hands. They leaned hard into diversification—scouting new suppliers across Asia, Europe, and the Americas. They also partnered with local firms to cut shipping delays and even redesigned some products to use more available components. It was a scramble, sure, but it worked.
The Outcome: By mid-2022, Flex slashed downtime by 30% and kept their clients happy. Costs stabilized, and they even gained a rep for being unflappable under pressure.
Key Takeaway: For designers, this screams adaptability—sometimes you’ve got to tweak your blueprints to match reality. For decision-makers, it’s a lesson in resilience: spread your bets, and you’ll weather the storm. Next time your supply chain hiccups, think beyond the usual suspects.
Case Study 2: Jabil – Implementing Automation for Efficiency
Now, let’s zoom into Jabil, a mid-tier player in circuit board manufacturing. They’re not as flashy as some tech titans, but they’ve got a story that’ll make any production geek sit up straight. A few years back, their Florida plant was churning out boards for consumer electronics—think smart TVs and wearables—but it wasn’t fast enough.
The Challenge: Manual assembly was the culprit. Workers were skilled, but human hands couldn’t keep up with demand. Errors crept in, too—solder joints failing QA checks—and scrap rates were eating into profits.
The Solution: Jabil went all-in on automation. They rolled out robotic arms for precision soldering and AI-driven cameras to catch defects in real time. It wasn’t cheap—upfront costs hit seven figures—but they trained their team to run the new tech, not replace them. Designers got involved early, tweaking layouts to play nice with the robots.
The Outcome: Output jumped by 40%, cranking out an extra 10,000 units a day. Defects dropped by half, and the plant’s energy bill even dipped thanks to streamlined workflows.
Key Takeaway: Designers, here’s your cue—build with automation in mind, and you’ll save headaches downstream. Decision-makers, don’t shy away from the price tag; the long-game payoff in electronics production efficiency is worth it. Jabil’s story proves tech isn’t the enemy—it’s your teammate.
Case Study 3: Samsung – Sustainable Manufacturing Breakthrough
Samsung’s a household name, but they’re not just about shiny phones. Behind the scenes, they’ve been wrestling with a planet-sized problem: electronics waste. With millions of devices shipped yearly, they knew the old take-make-dump model wasn’t cutting it anymore.
The Challenge: E-waste was piling up, and energy-hungry factories were drawing scrutiny. Consumers—and regulators—wanted greener tech, but profitability couldn’t take a hit.
The Solution: Samsung got creative. They launched their Galaxy Upcycling program, turning old phones into IoT gadgets, but the real magic happened in manufacturing. They switched to recycled plastics for packaging and cut energy use with solar-powered plants. Designers reworked components to use less rare-earth metals, too.
The Outcome: By 2023, Samsung slashed their carbon footprint by 15% across key facilities. They saved millions in material costs and earned eco-cred that boosted brand loyalty.
Key Takeaway: Designers, sustainability isn’t a buzzword—it’s a design constraint that sparks innovation. Decision-makers, going green can fatten your bottom line, not just your conscience. Samsung’s proof that eco-friendly electronics development isn’t a pipe dream—it’s good business.
Common Themes and Lessons Learned
Step back, and these stories start to rhyme. Innovation is the spark—whether it’s rethinking supply chains, embracing robotics, or reimagining materials. Adaptability keeps the wheels turning; no one wins by digging in their heels. Technology—think IoT, AI, or renewable energy—isn’t optional anymore; it’s table stakes. And sustainability? It’s not a nice-to-have—it’s a must, driven by customers and common sense.
I’ve seen this firsthand chatting with folks in the industry. A buddy who designs wearables once told me, “You can’t just draw pretty schematics anymore—you’ve got to think about where the parts come from and where they’ll end up.” That’s the mindset these case studies hammer home.
How to Apply These Insights to Your Business
So, how do you take this and run with it? Here’s a no-nonsense playbook:
Assess Your Pain Points: Are you bleeding cash on delays? Struggling with quality? Map out what’s holding you back.
Borrow Smart: Flex’s supply hacks, Jabil’s automation, Samsung’s green pivot—pick what fits your world. Designers, tweak your CAD files; deciders, crunch the numbers.
Test Small, Win Big: Don’t bet the farm. Pilot a new process—like a robotic pick-and-place line—and scale up once it clicks.
Try it. I dare you. Then drop a comment below and tell me how it went—I’m dying to hear your war stories.
Conclusion
From Flex dodging supply chain chaos to Jabil’s robot revolution and Samsung’s green glow-up, these electronics manufacturing case studies aren’t just tales—they’re blueprints. They show how ingenuity, grit, and a willingness to evolve can turn challenges into wins. For designers and decision-makers in electronics development, the message is clear: the industry’s moving fast, and standing still isn’t an option.
So, grab a coffee, sketch out your next move, and let these stories light the way. Got a case study of your own? Share it below—I’d love to swap notes over a virtual beer.