Eco-Friendly Metal Fabrication: Sustainable Practices for the Electronics Industry
Metal fabrication is at the heart of electronics—think circuit board traces, connectors, enclosures. But traditional methods? They’re energy hogs, waste machines, and sometimes downright toxic. The good news is there’s a better way. Sustainable practices like recycling metals, leaning into energy-efficient processes, and ditching harmful chemicals can transform how we build tech.
2/26/20256 min read
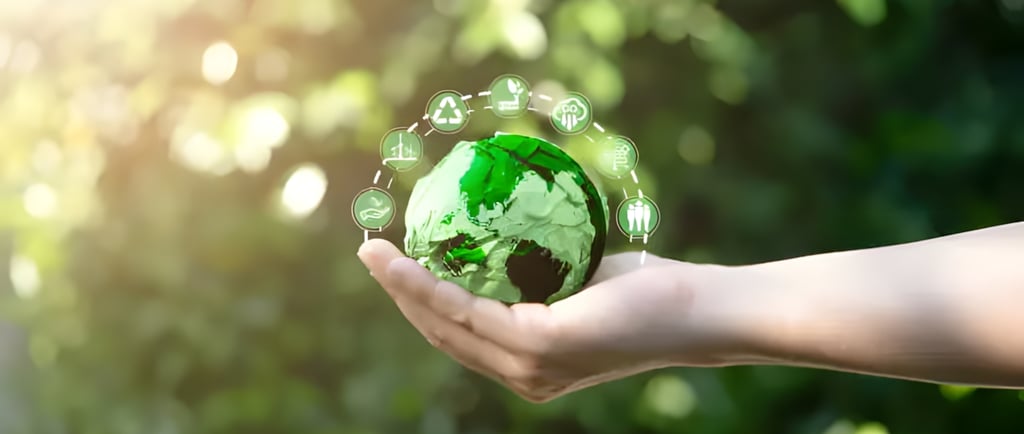
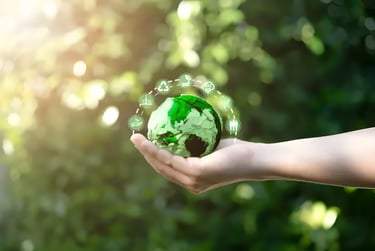
Picture this: You’re designing the next big thing in electronics—a sleek, cutting-edge device that’s going to fly off the shelves. You’ve got the specs nailed down, the team’s buzzing with ideas, and then it hits you: how’s this thing going to be made? More importantly, how can it be made without leaving a giant carbon footprint or a pile of scrap metal behind? If you’re a designer or decision-maker in the electronics world, these questions aren’t just nice-to-haves—they’re becoming must-haves. Consumers care, regulators are watching, and honestly, the planet’s kind of counting on us.
Metal fabrication is at the heart of electronics—think circuit board traces, connectors, enclosures. But traditional methods? They’re energy hogs, waste machines, and sometimes downright toxic. The good news is there’s a better way. Sustainable practices like recycling metals, leaning into energy-efficient processes, and ditching harmful chemicals can transform how we build tech. This isn’t just about tree-hugging—it’s about staying ahead in an industry that’s racing toward greener solutions. Let’s dive into how we can make it happen, step by step, and why it’s worth the effort.
The Environmental Cost of Business as Usual
Let’s start with the elephant in the room: traditional metal fabrication isn’t exactly Mother Nature’s best friend. Mining raw metals like copper or aluminum takes a toll—blasting through mountains, guzzling fuel, and spitting out emissions. Then there’s the processing—smelting ores into usable forms can burn through energy like a kid with a new video game console. And don’t get me started on the waste. Every time we cut, shape, or mill a piece of metal, scraps pile up, and a lot of it ends up in landfills instead of back in the supply chain.
I remember chatting with a friend who works in manufacturing a while back. He told me about a project where they lost nearly 30% of their raw material to scraps—just bits and pieces that didn’t make the final cut. “It’s normal,” he shrugged. But is it? When you zoom out, that “normal” adds up to a massive carbon footprint for an industry that’s supposed to be pushing humanity forward. For designers and deciders like us, it’s a wake-up call: the electronics we love come at a hidden cost. The question is, how do we fix it?
Recycling Metals: Turning Old into New
One of the simplest, most powerful fixes is right under our noses: recycling. Metals like aluminum, copper, and steel don’t lose their mojo when they’re melted down and reused. In fact, recycling them uses a fraction of the energy compared to mining fresh ore—up to 95% less for aluminum, according to some studies I’ve come across. That’s not just a win for the planet; it’s a win for your bottom line over time.
Think about your last phone upgrade. Where’d the old one go? If it’s sitting in a drawer, it’s a missed opportunity. Companies like Apple and Dell are already catching on—they’re pulling metals from old devices to build new ones. I read about a program where they’re salvaging copper from discarded motherboards to make connectors for the next generation of laptops. It’s brilliant, right? Your old gadget could literally power tomorrow’s tech.
For designers, this means rethinking components with recycled materials in mind. Can that casing be made from reclaimed aluminum? Could those circuit traces use copper from last year’s trade-ins? Decision-makers, meanwhile, can push suppliers to prioritize recycled stock. It’s not always the cheapest upfront, but the savings in energy and waste disposal add up—and your brand gets to wear that shiny “sustainable” badge consumers love.
Energy-Efficient Processes: Smarter, Not Harder
Next up, let’s talk about how we actually shape those metals. Traditional fabrication—think smelting furnaces or heavy-duty milling—burns through electricity like nobody’s business. But there’s a new wave of processes that are lighter on the grid and just as effective. Take laser cutting: it’s precise, fast, and uses way less energy than old-school methods. Or additive manufacturing—3D printing metal parts layer by layer instead of carving them out of a big block. Less waste, less power, same quality.
I saw this in action at a trade show last year. A small startup was demoing a 3D printer that churned out tiny, intricate connectors for wearable tech. The guy running the booth grinned and said, “This little machine does in an hour what used to take a day—and it barely sips electricity.” Precision like that doesn’t just save energy; it cuts down on material scraps, too. For designers, it’s a chance to dream up parts that couldn’t be made any other way. For decision-makers, it’s a reason to invest in tech that pays off long-term.
The catch? These tools can cost a pretty penny upfront. But here’s the thing: energy-efficient processes often run leaner, meaning lower bills and less downtime. Pair that with renewable energy sources—solar-powered factories are popping up more and more—and you’ve got a recipe for a fabrication line that’s as green as it is profitable.
Non-Toxic Materials: Clean from the Start
Now, let’s get into the messy stuff—literally. Traditional metal fabrication leans on some nasty chemicals. Lead in solder, mercury in finishes, harsh coolants that linger in the environment long after the job’s done. It’s rough on workers, rough on ecosystems, and a nightmare when those devices hit the trash heap. But we’ve got options.
Switching to lead-free solder is a no-brainer—it’s been around for years, and it works just as well. Water-based coolants or biodegradable lubricants can replace the toxic soups we used to rely on. I talked to an engineer recently who swore by a plant-based coolant his team adopted. “Smells like a salad bar instead of a chem lab,” he laughed, “and it washes off with soap.” Small changes, big impact.
For designers, this is a chance to spec materials that aren’t just functional but safe—safe to make, safe to use, safe to toss. Decision-makers can lean on this, too—pushing for supply chains that prioritize non-toxic inputs. It’s not just about dodging regulations (though that’s a perk); it’s about building electronics that don’t leave a dirty legacy. Green tech starts with clean ingredients, and that’s a story your customers will eat up.
Challenges and Solutions: Making It Work
Okay, let’s be real—going green isn’t all sunshine and rainbows. There are hurdles. Upgrading to energy-efficient machines or sourcing recycled metals can hit your budget hard at first. I’ve heard execs groan about this: “Why spend more when the old way works?” Fair point, but here’s the counter: those upfront costs fade when you factor in lower energy bills, less waste hauling, and even tax breaks for sustainable practices. Governments are throwing incentives at this stuff—might as well cash in.
Then there’s scale. One company going eco-friendly is great, but the industry’s a beast. How do we get everyone on board? Collaboration’s the answer. Designers can spec sustainable designs, decision-makers can nudge suppliers, and we can all lean on consumer demand. People want green tech—surveys show it, sales prove it. If we build it, they’ll buy it, and the rest of the supply chain will have to follow.
I’ve seen this play out in small ways. A buddy of mine works for a mid-sized electronics firm that started pushing recycled materials. At first, suppliers balked—too niche, they said. But once orders piled up, those same suppliers scrambled to adapt. It’s a slow burn, but it works.
The Future: Where We’re Headed
So, what’s next? The future of eco-friendly metal fabrication is buzzing with potential. Closed-loop recycling—where every scrap gets reused in-house—is picking up steam. Imagine a factory where nothing hits the dumpster. Renewable energy’s another game-changer—picture solar panels powering your next production run. I visited a facility last summer that ran entirely on wind and hydro. The hum of the machines felt… cleaner, somehow.
Consumers are driving this, too. They’re not just asking for cool gadgets; they want to feel good about buying them. As designers and deciders, we’ve got the power to deliver. Spec that recycled alloy. Push for that low-energy process. It’s not just about checking a sustainability box—it’s about staying relevant in a world that’s waking up to its limits.
Wrapping It Up
Here’s the bottom line: eco-friendly metal fabrication isn’t a pipe dream. Recycling metals, streamlining energy use, and kicking toxic materials to the curb are all within reach—today. For designers, it’s a chance to innovate with purpose. For decision-makers, it’s a smart play that pays off in efficiency, reputation, and sales.
I’ll leave you with this: the tech we build shapes the future. Why not make it a future where innovation and nature don’t have to fight? Let’s rethink how we craft electronics—one sustainable choice at a time. What do you think—got a favorite green tech brand or an idea to share? Drop it in the comments. I’d love to hear how you’re tackling this in your own work.