DIY Injection Molding: Can You Really Pull It Off in Your Garage?
You’ve got a 3D printer humming in the corner, but you’re dreaming bigger—faster production, smoother finishes, and parts that scream “pro” without begging a factory to take your small-batch order. Enter DIY injection molding.
2/23/20256 min read
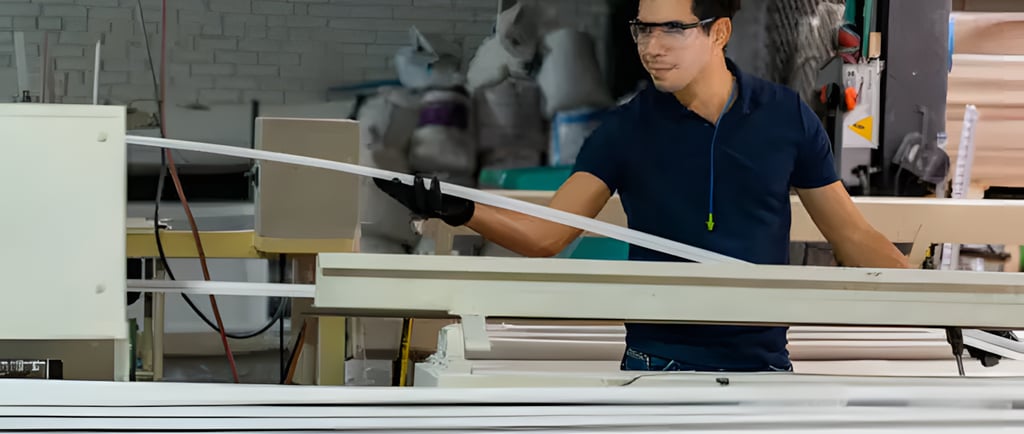
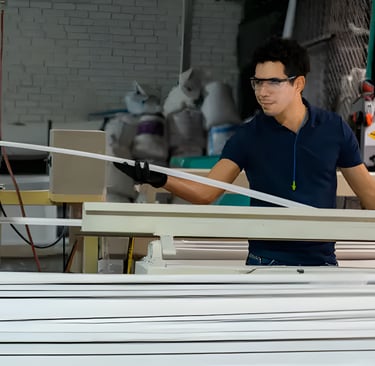
Picture this: You’re sitting in your workshop, coffee in hand, staring at a pile of plastic pellets and a sketch of a custom enclosure for your latest electronics prototype. You’ve got a 3D printer humming in the corner, but you’re dreaming bigger—faster production, smoother finishes, and parts that scream “pro” without begging a factory to take your small-batch order. Enter DIY injection molding. Yeah, the same process those big industrial outfits use to churn out millions of plastic bits. But here’s the kicker: Can you, a designer or decision-maker in electronics development, actually make it happen at home? Let’s find out—grab your safety goggles and let’s get experimental.
I’ve been down this rabbit hole myself, and trust me, it’s equal parts thrilling and terrifying. As someone who’s spent years tinkering with circuits and enclosures, I couldn’t resist the lure of molding my own parts. So, this isn’t just theory—it’s a story from the trenches, with a dash of “what if” for you folks steering the ship in electronics innovation.
Why Even Try DIY Injection Molding?
First off, why bother? You’re a designer or a decision-maker—your day’s already packed with specs, deadlines, and budgets. But hear me out. Injection molding at home isn’t just about making stuff; it’s about owning the process. Imagine crafting a bespoke housing for that new IoT device you’re pitching, or whipping up a dozen precise mounting brackets for a client demo—without waiting weeks for a supplier or shelling out for minimum orders that’d make your CFO faint.
For electronics folks, this is gold. Think custom connectors, sleek faceplates, or even tiny gears for a motor assembly—all molded to your exact specs. I once needed a weirdly shaped battery cover for a prototype, and instead of outsourcing, I started wondering: Could I melt some plastic and squish it into shape myself? It’s that spark of curiosity that drives this. Plus, there’s the street cred. Walking into a meeting with a part you molded in your garage? That’s a flex.
It’s not about replacing industrial production—it’s about prototyping faster, iterating on the fly, and proving a concept before you commit big bucks. And let’s be real: There’s a kid-in-a-candy-store joy in saying, “I made this from scratch.”
The Basics—What You’ll Need to Play Mad Scientist
Alright, let’s talk gear. You’re not building a factory, but you’ll need some stuff to pull this off. I learned this the hard way—my first attempt involved a kitchen oven and a lot of regret. Here’s the rundown for you electronics wizards:
The Machine: You can buy desktop injection molding kits (think Precious Plastic or LNS Technologies’ benchtop models), which are pricey but plug-and-play-ish—perfect if you’re justifying it to the budget overlords. Or, go full DIY: a plunger setup with a heated barrel. I rigged one using a drill press and a hacked-together heater. It’s janky, but it works. For electronics, precision matters, so lean toward something you can control.
Materials: Plastic pellets are your ammo—ABS or polypropylene are cheap, melt nicely, and play well with enclosures or structural parts. Bonus: You can recycle old plastic cases (check your e-waste bin!). For molds, silicone’s quick for one-offs, but if you’re serious, CNC a metal mold for durability. I started with silicone and a 3D-printed master—crude, but it got me a usable prototype.
Heat and Safety: You’ll need a heat source—think a small oven, a custom barrel heater, or even a hot plate if you’re brave. Melting plastic stinks (literally), so ventilate like your life depends on it. Gloves, goggles, and a fire extinguisher? Non-negotiable. I scorched a workbench once—don’t be me.
This is where you channel your inner Tony Stark, minus the billion-dollar lab. Duct tape’s optional, but enthusiasm isn’t. For electronics pros, this setup’s less about toys and more about rapid proof-of-concept—think of it as 3D printing’s rowdy cousin.
The DIY Process—Let’s Get Messy!
Ready to roll? Here’s how it goes down. I’ll walk you through my first go at molding a circuit board standoff—spoiler: It wasn’t pretty, but it worked.
Step 1: Design Your Mold
Start with your part—say, a housing for a PCB. Sketch it in CAD (you’re pros at this), then make a mold. I 3D-printed a positive, poured silicone over it, and prayed. For tighter tolerances, machine a metal mold—but silicone’s fine for testing. Embrace the chaos; this isn’t mass production yet.Step 2: Melt Your Plastic
Heat your pellets to the sweet spot (around 200–250°C for ABS—check your spec sheet). I used a hacked-together barrel with a thermometer, stirring like a nervous chef. You’ll smell it—kinda like burnt popcorn. That’s your cue to move fast.Step 3: Inject It
Pour or scoop the goo into your injector (syringe, plunger, whatever you’ve got). Push it into the mold with steady pressure—too slow, and it cools; too hard, and it’s a mess. My first shot squirted everywhere but the mold. Laugh it off and tweak your rig.Step 4: Cool and Pop It Out
Let it chill—submerge in water if you’re impatient like me. Then, crack open the mold. My standoff was lumpy, but it held a board. If yours is a blob, call it modern art and adjust the heat or pressure next time.
It’s trial and error, but that’s the fun. For electronics, this is your chance to test fitment or durability before committing to a supplier. Messy? Sure. Worth it? You bet.
The Reality Check—What Could Go Wrong?
Let’s not kid ourselves—this isn’t all sunshine and perfectly molded parts. I’ve had my share of disasters, and you will too. Here’s the scoop:
The Struggles: Warped parts from uneven cooling, air bubbles from sloppy injection, or molds that cling like a bad ex. My first enclosure wouldn’t release—I pried it out and scratched it to death. Tight tolerances for electronics? Tricky without practice.
Safety Oopsies: Hot plastic burns—I’ve got a scar to prove it. Fumes can choke you out, so crack a window or rig a fan. One whiff of molten ABS taught me that lesson.
Cost vs. Reward: A decent DIY setup might run you $200–$500—more if you splurge on a kit. Compare that to 3D printing (cheaper upfront) or outsourcing (pricier per part). For small runs or prototypes, it’s a win—but don’t expect to undercut factories.
Every fail’s a story, though. I once showed a warped bracket to my team, and we laughed it off over beers. It’s the maker spirit—learn, tweak, repeat. For decision-makers, weigh this: Is the time and risk worth skipping the vendor waitlist? Sometimes, yes.
Success Stories (and Epic Fails) From the DIY Frontier
I’m not alone in this madness. Scroll through maker forums or YouTube, and you’ll find hobbyists molding everything from chess pieces to car parts. One guy I saw online nailed a set of custom drone frames—smooth as butter. Another? His “gear” was a puddle with teeth. Both are wins in my book.
My own highlight was a functional USB dongle case—rough edges, but it clicked together and shielded the board. My flop? That battery cover I mentioned—it fused to the mold like cement. I scrapped it and started over, wiser for it. For electronics pros, these tales prove it’s doable—your next prototype could be a garage success.
So, Can You Do It? The Verdict
Here’s the deal: Yes, you can pull off DIY injection molding at home, but it’s not a plug-and-play gig. It’s for tinkerers who thrive on challenges—designers who’d rather iterate in-house than wait, and decision-makers who see value in cutting lead times. Compared to 3D printing, it’s trickier to set up but faster for batches once you’re dialed in. For electronics, that speed could mean beating a competitor to market.
If you’ve got a garage (or a corner of the lab) and a itch to experiment, why not? It’s not about replacing your supply chain—it’s about owning the early stages. My advice? Start small—a clip, a standoff—and scale up as you learn.
Unleash Your Inner Plastic Wizard
So there you have it—DIY injection molding, warts and all. It’s messy, it’s wild, and it’s peak DIY for the electronics crowd. You’ll sweat, you’ll curse, and you might just end up with a part that makes your next pitch a slam dunk. I’m still tweaking my setup, chasing that perfect mold, and loving every minute.
Grab some plastic, rig something up, and drop me a line—I want to hear about your masterpieces (or hilarious flops). Who needs a factory when you’ve got grit, a heat gun, and a vision? Now go make something awesome.