Design Optimization for Metal Fabrication in Electronics: Practical Tips for Success
By optimizing your designs for metal fabrication, you can streamline production, cut waste, and ensure your parts are manufacturable without endless back-and-forth.
2/26/20256 min read

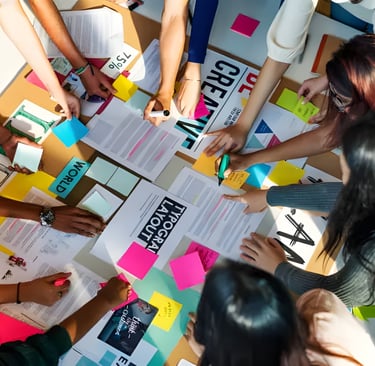
Imagine this: you’ve spent weeks perfecting the design for a sleek new electronic component—a heat sink, maybe, or a custom enclosure—and you’re buzzing with excitement to see it come to life. Then the fabricator calls. “This is going to cost 30% more than you budgeted,” they say, “and we’ll need extra time to tweak the tolerances.” Ouch. Suddenly, that brilliant design feels more like a headache. If that scenario sounds familiar, you’re not alone. In electronics development, where metal fabrication is the backbone of everything from connectors to chassis, small design choices can make or break your project’s timeline, budget, and sustainability goals.
The good news? You can avoid those headaches. By optimizing your designs for metal fabrication, you can streamline production, cut waste, and ensure your parts are manufacturable without endless back-and-forth. Whether you’re a designer sketching the next big thing or a decision-maker steering the ship, this article is for you. I’ll walk you through practical, real-world tips to make your designs shine—both on the drawing board and on the shop floor. Let’s dive in.
Understanding Metal Fabrication in Electronics
First, let’s get on the same page about what we’re dealing with. Metal fabrication in electronics isn’t just about slapping some aluminum into shape. It’s a dance of processes—stamping, laser cutting, bending, welding—that turns raw metal into the enclosures, heat sinks, and brackets that keep our devices humming. These processes are amazing when they work smoothly, but they’re also finicky. A bend radius that’s too tight, a tolerance that’s overly ambitious, or a part layout that wastes half the sheet can throw everything off.
The stakes are high. Poorly optimized designs lead to material waste (hello, rising costs), production delays (goodbye, deadlines), and parts that just don’t fit together right. I’ve seen teams scramble to fix these issues mid-project, and it’s never pretty. But here’s the kicker: most of these problems start with the design itself. That’s why you—the designer or decider—hold the power to make fabrication a breeze instead of a battle.
Practical Tips for Design Optimization
So, how do you design electronics components that fabricators love, budgets applaud, and timelines thank you for? Here are six hands-on tips to get you there.
Tip 1: Design with Material Efficiency in Mind
Let’s start with the raw stuff: the metal. Every sheet you order has a cost, and every scrap that hits the floor is money lost. One of the easiest ways to keep waste in check is to design with standard material sizes and thicknesses. Say you’re sketching an enclosure. Instead of calling for a quirky 1.3mm-thick sheet—because it sounded cool in your head—stick to something like 1mm or 2mm, which suppliers stock by the truckload. It’s not just about availability; fabricators can cut standard sizes faster and with less leftover scrap.
I once worked with a designer who insisted on a non-standard thickness for a prototype. The result? A three-week delay waiting for custom material, plus a bill that made everyone wince. Lesson learned: align your vision with what’s practical. You’ll save time, money, and a few gray hairs.
Tip 2: Simplify Geometries for Fabrication
Complex is cool—until it’s not. Those intricate curves and funky angles might look dazzling in CAD, but they’re a nightmare for fabricators. Every extra cut, bend, or tool change slows things down and ups the odds of mistakes. Instead, aim for simplicity wherever you can. Straight edges, uniform bends, and basic shapes are your friends.
Picture this: you’re designing a metal chassis. Instead of sculpting it with swooping curves that need five separate machining steps, go for clean lines and a single 90-degree bend. I’ve seen fabricators grin when they get designs like that—they can knock it out in half the time. Plus, simpler geometries mean fewer chances for errors, which keeps your production on track.
Tip 3: Incorporate Tolerances That Match Fabrication Capabilities
Tolerances are where dreams meet reality. You might want every edge perfect to the micron, but most fabrication tools—like laser cutters (±0.1mm) or stamping presses (±0.05mm)—have limits. Over-specifying tolerances is like asking a chef to measure salt grains with a microscope: it’s overkill, and it slows everything down.
Here’s a trick: for non-critical features—like the outer edge of a bracket—relax the tolerance to something like ±0.2mm. Save the tight specs (say, ±0.05mm) for where it really matters, like mounting holes that need a perfect fit. I once saw a team rework an entire batch because they demanded ultra-tight tolerances on a part that didn’t need it. The fix? Looser specs and a happier fabricator. Match your tolerances to the process, and you’ll avoid costly do-overs.
Tip 4: Optimize for Assembly During Fabrication
Fabrication doesn’t end when the part’s cut—it’s just the start. If your component takes an hour to assemble because it needs 20 screws, you’ve missed a golden opportunity. Smart design can make assembly a snap (sometimes literally). Think about adding self-aligning features—like tabs, slots, or notches—that let parts lock into place without extra hardware.
I remember a project where we redesigned a control box to include built-in tabs instead of relying on a dozen tiny screws. Assembly time dropped by 40%, and we cut the parts list down, too. Fewer fasteners mean less waste and faster production. Next time you’re drafting, ask yourself: “Could this snap together instead?” Your assembly team will thank you.
Tip 5: Leverage Simulation Tools Early
Here’s where tech saves the day. Before you send a design to the fabricator, run it through simulation tools like CAD or finite element analysis (FEA). These let you test how your part will behave—thermally, structurally, or otherwise—without wasting a single sheet of metal. It’s like a crystal ball for spotting trouble.
Take a heat sink, for example. You could guess at fin spacing and hope it cools your chip, or you could simulate airflow and tweak the design until it’s perfect. I’ve seen teams skip this step, build a prototype, and then scramble when it overheats. One simulation run could’ve saved them weeks and a pile of scrap. Invest a little time upfront with these tools, and you’ll dodge big headaches later.
Tip 6: Collaborate with Fabricators During Design
You’re not in this alone. Fabricators aren’t just the folks who make your design real—they’re partners who know their machines inside out. Bring them into the loop early. A quick chat about their preferred bend radii, hole sizes, or cutting methods can steer your design away from trouble.
I once sat down with a fabricator who pointed out that my 2mm bend radius was pushing their press brake’s limits. A tweak to 3mm made the job smoother and cheaper—no redesign required. That conversation took 15 minutes and saved us days. Don’t wait for feedback after the fact; get their input while you’re still sketching. It’s a win-win.
Reducing Waste Through Smart Design
Waste isn’t just a cost issue—it’s a sustainability one, too. In electronics, where every gram of metal counts, smart design can keep scrap out of the bin. One of my favorite tricks is material nesting. Think of it like a puzzle: arrange your parts on the sheet so they fit together tightly, leaving minimal gaps. Software can help, but even a little planning goes a long way. I’ve seen nesting cut material use by 20% on a single run—numbers that make both wallets and eco-goals happy.
Then there’s recycling. Design with end-of-life in mind. Use single-material components where possible—like all-aluminum enclosures instead of mixed metals—so they’re easier to recycle. It’s a small choice that pays off down the road. I once worked on a project where we switched to a uniform alloy, and the recycling team practically threw a party. Less waste, better planet—why not?
Putting It All Together
Designing for metal fabrication in electronics isn’t about stifling creativity—it’s about channeling it smarter. By picking standard materials, simplifying shapes, dialing in tolerances, easing assembly, testing with simulations, and teaming up with fabricators, you’re not just making parts; you’re crafting a process that hums. Add in waste-saving moves like nesting and recyclability, and you’ve got a recipe for success that keeps costs down, timelines tight, and quality high.
Next time you’re at the drawing board—or signing off on a design—think about the shop floor. Picture the fabricator grinning as they load your file, the assembly team snapping parts together effortlessly, and the budget staying green. That’s the power of optimization. It’s not just good design; it’s good business.
So, what’s your next project? Try these tips out, and let me know how it goes—I’d love to hear your stories from the trenches. Happy designing!