Common Mistakes to Avoid When Designing Electronic Enclosures
A well-designed electronic enclosure is crucial for protecting internal components, ensuring functionality, and enhancing user experience. Whether you're designing for consumer electronics, industrial applications, or outdoor environments, small design mistakes can lead to costly revisions, performance issues, and even regulatory failures.
2/10/20253 min read
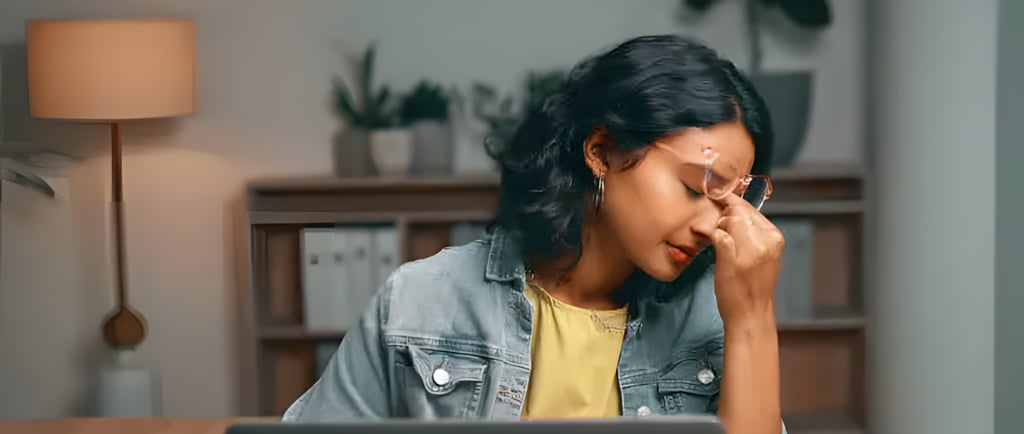
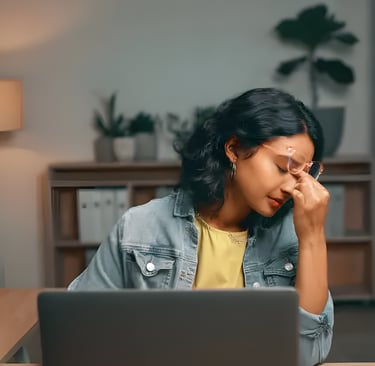
A well-designed electronic enclosure is crucial for protecting internal components, ensuring functionality, and enhancing user experience. Whether you're designing for consumer electronics, industrial applications, or outdoor environments, small design mistakes can lead to costly revisions, performance issues, and even regulatory failures.
This article explores common mistakes in enclosure design and provides actionable tips to help engineers, designers, and manufacturers avoid them. If you’re looking for insights on how to optimize your enclosure design for durability, efficiency, and compliance, read on.
1. Mistake #1: Ignoring Thermal Management
Why It’s a Problem
Overheating can damage sensitive electronic components, reduce performance, and shorten the lifespan of a device. Poor thermal management can result in product recalls or user dissatisfaction due to unexpected failures.
Common Oversights
Lack of ventilation or heat dissipation features.
Using non-conductive materials that trap heat (e.g., plastics in high-power applications).
How to Avoid It
Incorporate vents, heat sinks, or fans into the design.
Select thermally conductive materials like aluminum to dissipate heat more effectively.
Perform thermal simulations during the design phase to identify potential heat buildup.
2. Mistake #2: Overlooking Environmental Factors
Why It’s a Problem
Environmental exposure can degrade electronic enclosures quickly, leading to malfunctions, safety hazards, and increased maintenance costs.
Common Oversights
Using low IP-rated enclosures for outdoor or industrial applications.
Failing to consider UV resistance, leading to material degradation.
Ignoring vibration or impact resistance in harsh environments.
How to Avoid It
Choose enclosures with appropriate IP ratings for moisture and dust protection.
Use UV-stabilized plastics or corrosion-resistant metals for outdoor applications.
Add gaskets, seals, or shock-absorbing mounts for durability in rugged environments.
3. Mistake #3: Poor Component Layout
Why It’s a Problem
Inefficient component placement can lead to wasted space, difficult assembly, and even overheating due to poor airflow.
Common Oversights
Crowding components too closely together.
Not leaving enough space for wiring or connectors.
Overlooking future upgrades or repair needs.
How to Avoid It
Use CAD software to optimize internal layouts before finalizing the design.
Leave adequate clearance for airflow and maintenance.
Plan for modular designs to allow easy upgrades and repairs.
4. Mistake #4: Failing to Consider Manufacturing Constraints
Why It’s a Problem
Complex or impractical designs can increase production costs, lead times, and manufacturing errors.
Common Oversights
Using intricate shapes that are difficult or expensive to manufacture.
Not accounting for tolerances in CNC machining, injection molding, or 3D printing.
How to Avoid It
Collaborate with manufacturers early in the design process to ensure feasibility.
Simplify designs where possible without compromising functionality.
Choose manufacturing methods suited to your design (e.g., deep draw technology for seamless metal enclosures).
5. Mistake #5: Skipping EMI Shielding Requirements
Why It’s a Problem
Electromagnetic interference (EMI) can disrupt device performance and result in regulatory compliance failures.
Common Oversights
Using non-conductive materials without additional shielding.
Failing to seal gaps or seams that compromise EMI protection.
How to Avoid It
Use conductive materials like aluminum or steel for natural EMI shielding.
Add conductive coatings or gaskets if using plastic enclosures.
Test prototypes for EMI compliance before full production.
6. Mistake #6: Neglecting User Experience (UX)
Why It’s a Problem
Poorly designed enclosures can frustrate users and damage brand reputation.
Common Oversights
Awkward placement of buttons, ports, or displays.
Sharp edges or uncomfortable grips on handheld devices.
Difficult access for maintenance or battery replacement.
How to Avoid It
Prioritize ergonomic designs, especially for handheld devices.
Conduct user testing during prototyping to gather feedback on usability.
Ensure intuitive layouts with easy access to key features.
7. Mistake #7: Underestimating Aesthetic Importance
Why It’s a Problem
In consumer-facing markets, an unattractive enclosure can reduce product appeal and competitiveness.
Common Oversights
Using generic designs that don’t align with branding.
Ignoring surface finishes or color options.
How to Avoid It
Customize enclosures with logos, unique colors, and finishes like anodizing or powder coating.
Balance aesthetics with functionality—avoid design choices that compromise performance.
8. Mistake #8: Failing to Account for Regulatory Compliance
Why It’s a Problem
Non-compliance with industry standards can lead to fines, recalls, or market restrictions.
Common Oversights
Ignoring IP ratings for water/dust protection requirements.
Overlooking EMI/EMC compliance testing (e.g., FCC, CE).
Using non-compliant materials (e.g., not RoHS-certified).
How to Avoid It
Ensure your enclosure meets all relevant standards early in the design process.
Work with manufacturers experienced in regulatory compliance requirements.
Test prototypes thoroughly before mass production.
9. Tips for Avoiding These Mistakes
Collaborate Early with Manufacturers
Working with experienced manufacturers from the concept stage can help prevent costly design revisions and ensure smooth production. Companies like Peakingtech specialize in enclosure manufacturing and can provide valuable insights on materials, compliance, and production efficiency.
Leverage Advanced Simulation Tools
Use thermal, structural, and EMI simulations to refine your enclosure design before prototyping. This reduces the risk of unexpected failures in real-world applications.
Prioritize User Feedback
Gather feedback from engineers, manufacturers, and end users during prototyping to ensure the design is practical, user-friendly, and compliant.
Conclusion
Designing electronic enclosures involves more than just protecting internal components—it requires thoughtful consideration of heat dissipation, environmental resistance, manufacturability, compliance, and user experience. By avoiding these common mistakes, you can create reliable, cost-effective enclosures that enhance product performance and user satisfaction.
If you’re looking to optimize your electronic enclosure design, consider collaborating with industry experts and leveraging advanced simulation tools to catch design flaws before production. A well-thought-out enclosure can be the difference between a successful product launch and costly redesigns.
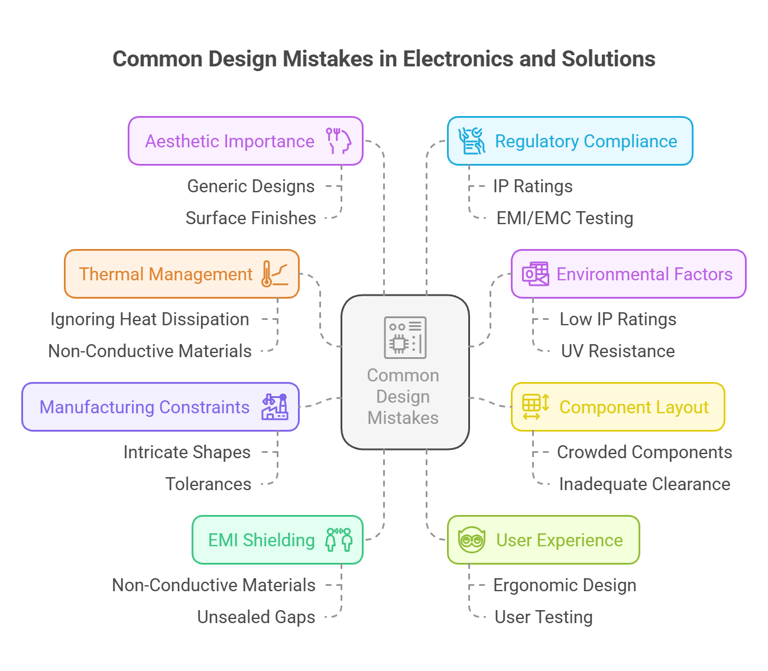
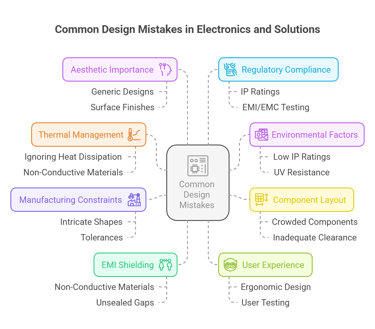