Common Materials Used in Injection Molding: Pros and Cons
Picking the right material for injection molding feels like a high-stakes poker game—one wrong call, and your project’s either too flimsy, too pricey, or just plain late. For folks like us in electronics development, the big three—ABS, polycarbonate, and nylon—keep popping up as the go-to plastics.
2/22/20255 min read
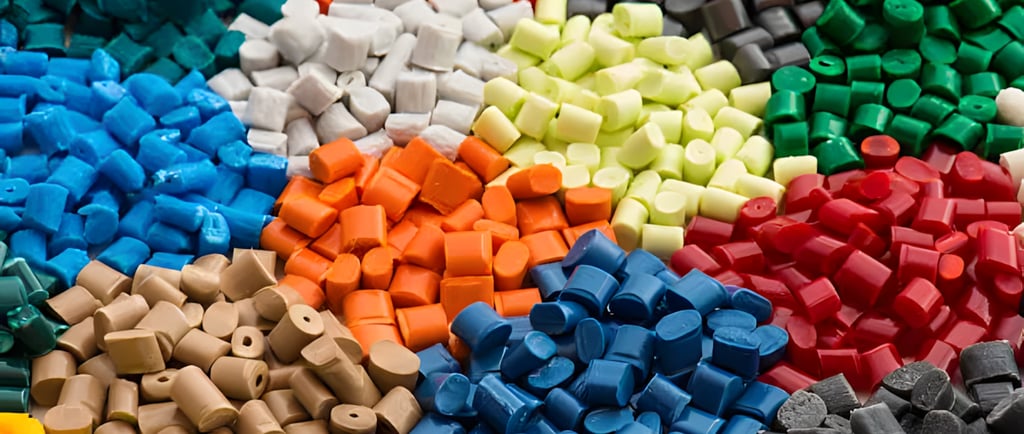
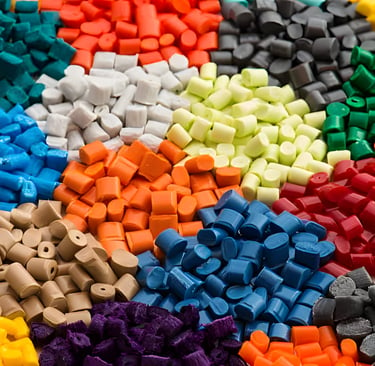
Picture this: you’re an electronics designer, hunched over your desk, sketching the housing for a new IoT sensor. Or maybe you’re a decision-maker, staring at a budget spreadsheet, trying to figure out how to get 10,000 wearable casings out the door without breaking the bank. Either way, picking the right material for injection molding feels like a high-stakes poker game—one wrong call, and your project’s either too flimsy, too pricey, or just plain late. For folks like us in electronics development, the big three—ABS, polycarbonate, and nylon—keep popping up as the go-to plastics. But which one’s the ace up your sleeve?
I’ve been burnt by material missteps before—think warped prototypes and angry emails—so I get the pressure. Let’s crack open these plastics, weigh their pros and cons, and figure out what fits your next molded masterpiece. This isn’t just a spec sheet dump; it’s a real talk about what works, what flops, and why it matters to you.
ABS (Acrylonitrile Butadiene Styrene)
What is ABS?
ABS is the Swiss Army knife of thermoplastics—a blend of acrylonitrile (for strength), butadiene (for toughness), and styrene (for that shiny rigidity). It’s the stuff behind your keyboard, the dashboard trim in your car, even those LEGO bricks you stepped on last week. In electronics, it’s a staple for enclosures that need to look good and take a beating without costing a fortune.
Pros
This plastic’s got some serious perks. It’s tough—drop your molded mouse from the desk, and it’ll shrug it off, thanks to an impact strength around 200-300 J/m. The finish? Straight out of the mold, it’s glossy and smooth—no extra polishing needed, which saves time. Plus, it’s cheap—bulk prices hover at $1-2 per pound, per 2023 Plastics Insight data. I’ve leaned on ABS for quick prototypes when budgets were tight, and it’s never let me down.
Cons
But it’s not invincible. Heat’s its kryptonite—softening kicks in at 105°C (221°F), so forget under-hood electronics or devices near a hot chip. UV rays chew it up too; leave an ABS casing outside, and it’ll yellow and crack in a year without stabilizers. And chemicals? Solvents like acetone dissolve it fast. I learned that the hard way when a solvent-wiped prototype turned into goo.
Best For
ABS shines for indoor gear—think router shells, USB dongles, or anything where cost and cosmetics trump extreme conditions. It’s your budget buddy with a pretty face.
Polycarbonate (PC)
What is Polycarbonate?
Polycarbonate’s the tank of the group—transparent, crazy strong, and built to last. It’s what shields your LED lights, guards machinery, or (if you’re old-school) held your CDs. In electronics, it’s the pick for parts needing clarity or brute durability, like phone cases or display covers.
Pros
This stuff’s a beast. Impact strength? Try 600-850 J/m—250 times tougher than glass, per SABIC’s specs. It laughs off drops that’d shatter ABS. Heat resistance is solid too—up to 135°C (275°F)—perfect for gadgets near warm circuits. Need see-through parts? It’s crystal clear, and flame-retardant grades (UL94 V-0) make it a safety champ. I’ve spec’d it for prototypes where failure wasn’t an option, and it delivered every time.
Cons
The trade-off’s steep. It costs more—$2-4 per pound—and that adds up fast on big runs. Scratches are a headache too; without a coating, your glossy cover turns hazy quick. And chemicals? Prolonged exposure to cleaners or oils can trigger stress cracks. I once saw a batch of PC lens covers fail after a cleaning mishap—lesson learned.
Best For
Polycarbonate’s your pick for tough, transparent, or heat-tolerant parts—think smartwatch faces or industrial sensor shields. It’s premium, but it earns its keep.
Nylon (Polyamide, PA)
What is Nylon?
Nylon’s the workhorse—a family of polyamides (PA6, PA66, etc.) known for strength and grit. You’ll find it in gears, cable ties, or those beefy connectors under your car’s hood. In electronics, it’s the go-to for parts that flex, wear, or fight friction—like plug housings or moving clips.
Pros
Nylon’s a warrior. Tensile strength hits 80-100 MPa (unfilled), and glass-filled grades push past 150 MPa—perfect for stress-heavy jobs. It’s abrasion-resistant too; think of those cable ties lasting years. Oils and fuels? It shrugs them off better than ABS or PC. I’ve used PA66 for a prototype switch that got clicked a thousand times—no wear, no tear.
Cons
Here’s the rub: nylon drinks water—2-3% uptake for PA6, per DuPont’s data—causing swelling or strength dips if not dried right. Cost climbs too—$2-5 per pound, more with fillers like glass—and molding it’s a pain. It needs pre-drying (80°C for 4 hours) to avoid bubbles or burns. I’ve botched a run skipping that step; the parts looked like Swiss cheese.
Best For
Nylon’s your MVP for functional parts—connectors, hinges, anything moving or load-bearing. It’s tough but demands respect.
Comparing the Big Three
Let’s stack them up, electronics-style.
Cost
ABS: The wallet’s friend at $1-2/lb—ideal for tight budgets.
Polycarbonate: Mid-tier at $2-4/lb—invest if you need the muscle.
Nylon: $2-5/lb, pricier with additives—pay for performance.
Strength and Durability
ABS: Decent at 40-50 MPa tensile strength—fine for light impacts.
Polycarbonate: A champ at 60-70 MPa, plus that insane impact resistance.
Nylon: Tops out at 80-150 MPa—king of wear and tear.
Heat and Environmental Resistance
ABS: Weakest link—105°C max, indoor-only sans UV help.
Polycarbonate: Holds at 135°C, solid outdoors with coatings.
Nylon: Up to 150°C (PA66), but moisture’s a wild card.
Ease of Molding
ABS: Flows like butter—1-2% shrinkage, 230°C melt temp, no fuss.
Polycarbonate: Hotter (300°C), trickier, but manageable.
Nylon: Picky—260-290°C, needs drying, shrinks 1-3%.
I’ve run these through molds myself—ABS is forgiving, PC’s a step up, nylon’s a diva but worth it.
Real-World Applications in Electronics
ABS in Action
Logitech’s mice—like the G203—rely on ABS shells. They’re light (85g), smooth, and cheap to churn out—30 million units sold by 2022, per Logitech’s reports. It’s the pragmatic pick for mass-market gear.
Polycarbonate at Work
Apple’s iPhone screen protectors? Polycarbonate, molded thin and tough—0.5mm thick, surviving drops from 1.5m, per OtterBox tests. Clarity and strength make it a no-brainer for displays.
Nylon’s Niche
Molex Mini-Fit Jr. connectors—those little power plugs in your PC—use glass-filled PA66. They handle 9A at 600V, per Molex specs, and last through 100+ mating cycles. Durability’s the name of the game.
I’ve spec’d all three—ABS for mockups, PC for demos, nylon for final runs. Each has its moment.
Choosing the Right Material for Your Project
So, how do you pick? Ask yourself:
Budget: Can you splurge past ABS’s bargain bin? A 10,000-unit run in ABS might save $20,000 over PC.
Environment: Indoor desk toy or outdoor sensor? ABS fades, PC holds, nylon adapts if dry.
Performance: Need impact (PC), wear (nylon), or just good enough (ABS)?
Tips
ABS: Prototypes, budget consumer stuff—think USB hubs.
Polycarbonate: Safety-critical or clear parts—LED covers, rugged cases.
Nylon: Moving or high-stress bits—plugs, clips, gears.
Hybrid Options
Can’t decide? PC/ABS blends—like in car dashboards—mix toughness and cost. I’ve used it for a hybrid enclosure once—best of both worlds.
I’ve lost sleep over these calls. Last year, I picked nylon for a connector, fought the moisture battle, and won—client’s still raving. Match the material to the mission.
Conclusion
ABS, polycarbonate, and nylon aren’t just plastics—they’re your toolkit. ABS keeps it cheap and pretty, polycarbonate flexes its muscle with clarity and heat, nylon grinds through the tough stuff with a smirk. Each has quirks, but that’s the beauty—there’s a fit for every electronics challenge you’re tackling.
I’ve been there, staring down a mold design, second-guessing my choice. Here’s my two cents: know your project’s soul—cost, conditions, demands—and pick with guts. Your next sensor, wearable, or gadget depends on it. What’s your go-to material? Hit the comments—I’d love to swap war stories or brainstorm your next mold.