Choosing the Right Soldering Materials: Lead vs. Lead-Free
The debate over lead vs. lead-free solder isn't just theoretical; it's a practical dilemma that affects product quality, environmental impact, and worker health.
2/18/20254 min read
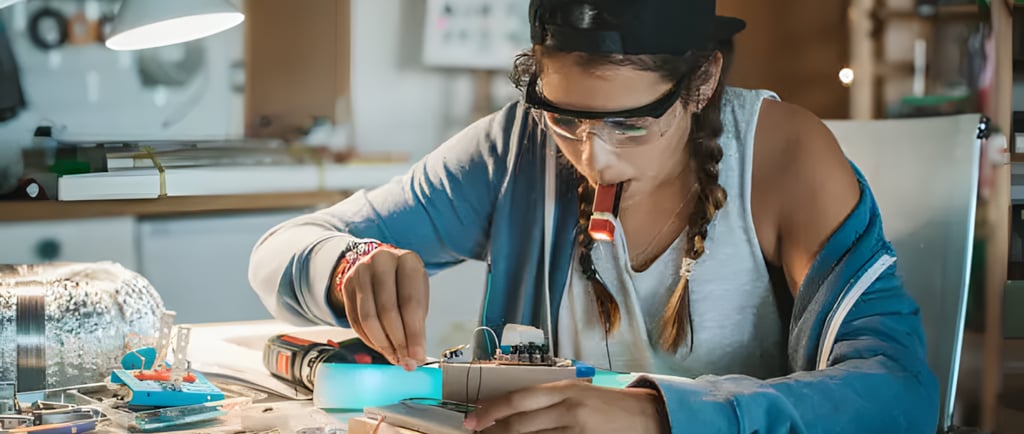
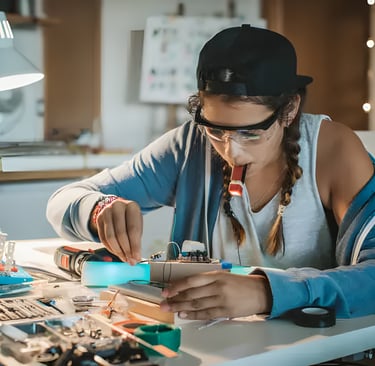
As someone who's spent years soldering everything from simple circuit boards for personal projects to complex assemblies for industrial applications, I've witnessed firsthand the evolution of solder materials. The debate over lead vs. lead-free solder isn't just theoretical; it's a practical dilemma that affects product quality, environmental impact, and worker health. Let's explore this critical choice with real-world examples, case studies, and hard facts to guide electronics designers and decision-makers.
Section 1: Understanding Soldering Materials
Solder is the unsung hero in electronics assembly, an alloy primarily composed of tin, with or without lead, and flux to ensure a clean, strong bond. The choice of solder impacts not only the ease of assembly but also the durability and compliance of the final product.
Section 2: The Case for Lead-Based Solder
For decades, lead-based solder was the industry standard due to several compelling reasons:
Pros:
Lower Melting Point: With a melting point around 183°C, traditional 63/37 (tin/lead) solder allowed for a wide operational window, making it ideal for hand soldering. For instance, the assembly of vintage musical synthesizers in the '70s and '80s often used this alloy for its forgiving nature.
Better Wetting Properties: Lead solder's ability to spread easily across metal surfaces leads to excellent joint strength. This was crucial in the manufacturing of high-reliability components for military applications where failure wasn't an option.
Cost-Effectiveness: Historically, lead solder was significantly cheaper. Before the RoHS directive, companies like IBM used lead solder for bulk production due to its cost efficiency, translating into lower product prices.
Cons:
Health and Environmental Concerns: Lead toxicity became a stark reality with cases like the lead poisoning of workers at a Massachusetts electronics factory in 1982, prompting a reevaluation of its use.
Regulatory Restrictions: The RoHS directive in 2003 by the EU effectively banned lead in many electronic products, compelling a global shift towards alternatives.
Section 3: The Rise of Lead-Free Solder
The transition to lead-free wasn't merely a compliance issue; it was a step towards sustainability:
Pros:
Environmental and Health Safety: The adoption of lead-free solders in Apple's products from 2006 onwards was not only about meeting regulations but also about reducing toxic waste in landfills.
Regulatory Compliance: Companies like Samsung have leveraged their RoHS compliance for marketing, emphasizing their commitment to green electronics.
Long-term Reliability: Studies by NIST have shown that certain lead-free alloys, like SAC305 (tin-silver-copper), offer superior thermal fatigue resistance, crucial for automotive electronics where temperatures can fluctuate dramatically.
Cons:
Higher Melting Point: Lead-free solders typically melt at around 217°C or higher, requiring more precise temperature control. This was a learning curve for many, like the case with Nokia's early 2000s mobile phones where issues with solder joint reliability were initially attributed to the switch to lead-free.
Less Forgiving: The higher melting point can lead to thermal shock in components if not managed correctly, as seen in some early adoptions where manufacturers reported higher failure rates.
Joint Quality: While lead-free solders have improved, some sectors, like high-frequency applications, still debate their performance. The NASA Mars Curiosity Rover, for instance, used lead-based solder for critical joints due to proven performance under extreme conditions.
Section 4: Comparing Performance
Mechanical Properties: Research from the University of Maryland demonstrated that while lead-free solders can be more brittle, advancements in alloys like SnAgCu (SAC) have mitigated this, offering comparable or even superior fatigue life in certain conditions.
Electrical Properties: A study from NXP Semiconductors found that while lead-free solders might show higher initial resistance, this stabilizes over time, with no significant difference in conductivity in operational environments.
Thermal Properties: The higher melting point of lead-free can be beneficial in environments like data centers where thermal cycling is frequent. IBM's POWER8 servers utilized lead-free solder for this reason, showcasing reduced failure rates.
Application Suitability: Lead-free has become the norm for consumer electronics, medical devices, and automotive sectors. However, for niche applications like space exploration, lead solder might still be used for its proven track record.
Section 5: Environmental and Health Considerations
The push for lead-free is backed by sobering statistics. According to the EPA, reducing lead exposure in manufacturing has led to a significant decrease in blood lead levels among workers in the electronics industry since the early 2000s. Moreover, recycling units in Europe have seen a drop in hazardous waste from electronics, thanks to RoHS.
Section 6: Practical Tips for Choosing Between Lead and Lead-Free
For Hobbyists/Beginners: While lead solder might be easier for home projects, consider the long-term benefits of learning lead-free techniques. Tools like Weller's WES51 soldering station are now designed with lead-free in mind.
For Professionals: A case study from Siemens showed that investing in training and equipment for lead-free soldering not only met compliance but also improved product reliability.
Safety Precautions: The case of Foxconn's adoption of lead-free soldering in their manufacturing facilities in China underscores the need for strict safety protocols, including proper ventilation and personal protective equipment.
Section 7: Future Trends in Soldering
Innovation continues with:
New Alloys: Researchers at Indium Corporation are exploring alloys that offer the benefits of lead without the drawbacks, like their Indalloy 241.
Alternative Fluxes: Companies like Kester are developing no-clean fluxes to complement lead-free solders, reducing post-soldering cleanup.
Automated Soldering: The automotive industry, particularly with electric vehicles, is pushing for automation in soldering, where precision in using lead-free materials is paramount.
Conclusion
The choice between lead and lead-free solder is multifaceted, involving not just technical performance but also ethical considerations. From my years at the bench, I've learned that while lead offers simplicity, lead-free pushes us towards innovation and responsibility. Your decision might vary based on application, but arming yourself with knowledge from real-world scenarios is crucial.
Call to Action
Have you encountered challenges or successes with these solders in your work? Share your stories in the comments. Remember, each solder joint is a commitment to quality, safety, and sustainability. Choose wisely, solder with precision, and let's keep innovating together.