Breaking Down Electronics Manufacturing Costs: A Designer’s Guide to Smarter Decisions in 2025
In today’s fast-moving world of tech, costs can make or break a project. From raw materials to labor, equipment to logistics, every choice you make ripples through the budget.
3/2/20256 min read
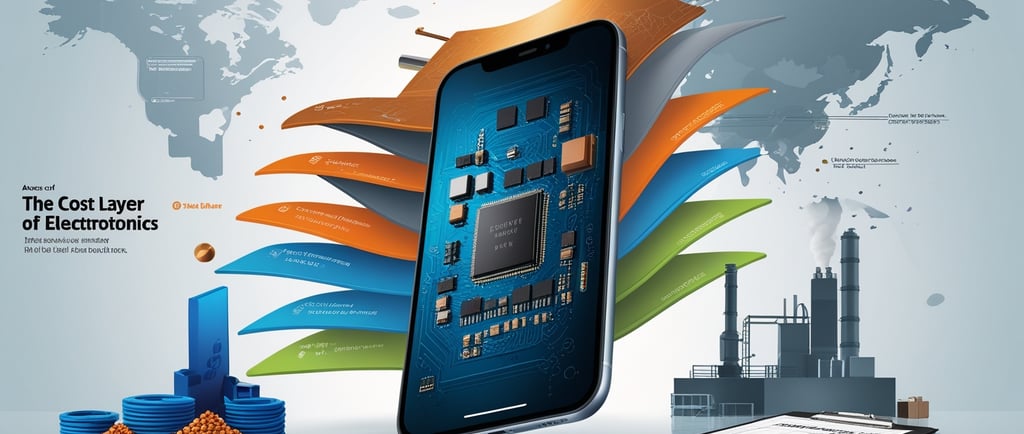
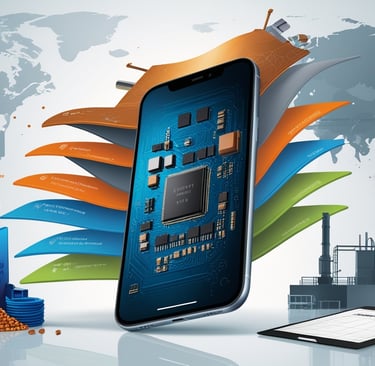
Picture this: You’re a designer sketching out the next big thing in electronics—a sleek wearable, a lightning-fast industrial sensor, or maybe a life-saving medical device. Your brain’s buzzing with ideas, but then reality hits. How much is this going to cost to make? Whether you’re a seasoned engineer or a decision-maker steering the ship, understanding electronics manufacturing costs isn’t just a nice-to-know—it’s your ticket to turning vision into reality without breaking the bank.
In today’s fast-moving world of tech, costs can make or break a project. From raw materials to labor, equipment to logistics, every choice you make ripples through the budget. This article’s here to pull back the curtain on what drives electronics manufacturing costs, why they matter to you, and how you can navigate them like a pro in 2025. Let’s dive in and get practical—because your next big design deserves to shine.
1. Key Components of Electronics Manufacturing Costs
Every gadget starts somewhere, and for you, that means knowing the building blocks of cost. Here’s what’s eating up the budget—and how you can think about it as a designer or decider.
1.1 Raw Materials
Think of raw materials as the DNA of your product. Semiconductors, printed circuit boards (PCBs), copper wiring, and even the plastic casing—all these pieces add up. I’ve seen projects where a designer picked a premium-grade chip for a prototype, only to realize later it doubled the cost for no real gain. Material quality matters, but so does availability. Remember the chip shortages a few years back? In 2025, supply chains are still shaky, and prices for rare metals or cutting-edge components can swing wildly. Your takeaway? Spec materials early and keep an eye on global trends.
1.2 Labor
Next up is the human touch—or lack thereof. Are you relying on skilled technicians to assemble delicate parts, or is a robot doing the heavy lifting? I once chatted with a factory manager in Shenzhen who swore by automation for smartphones but admitted hand-assembly was still king for niche prototypes. Labor costs vary wildly by region—think $2 an hour in parts of Asia versus $20+ in the U.S. or Europe. As a designer, your choices (like how intricate your PCB layout is) can dictate whether you need pricey skilled labor or can lean on machines.
1.3 Equipment and Technology
The tools of the trade aren’t cheap. Surface-mount machines, testing rigs, and even the software you use to simulate designs come with hefty price tags. I’ve watched startups balk at the cost of a single piece of equipment, only to realize it pays off in precision and speed. Automation’s a game-changer here—think Industry 4.0 with its smart factories—but it’s an upfront investment. Your job? Weigh whether that shiny new tech saves money long-term or just looks good on paper.
1.4 Overhead Costs
Don’t sleep on the “boring” stuff. Renting a facility, paying the electric bill, shipping parts across continents—it all piles up. A buddy of mine once oversaw a project that got hit with unexpected regulatory fees because they didn’t account for RoHS compliance. Certifications like FCC or CE can sneak up on you too. As a decider, push for a buffer in your budget for these hidden costs—they’re not sexy, but they’re real.
2. Factors Influencing Manufacturing Costs
Now that you’ve got the basics, let’s talk about what twists the dial on those costs. These are the levers you can pull—or at least understand—as you design and decide.
2.1 Economies of Scale
Here’s a truth I’ve learned the hard way: One unit costs a fortune; a million units cost pennies (relatively). Mass production spreads fixed costs thin, like butter on toast. Designing a consumer gadget like a smartwatch? You’re golden if you can hit high volumes. But a specialized aerospace component? Small batches mean higher per-unit costs. Think about your market size early—it’s a cost driver you can’t ignore.
2.2 Design Complexity
I’ll be blunt: The cooler your design, the more it might cost to make. Tiny components, tight tolerances, or a fancy multi-layer PCB—I’ve seen designers fall in love with these only to face a manufacturer shaking their head. Complexity slows production and ups the risk of defects. Your challenge is finding that sweet spot where innovation meets practicality.
2.3 Supply Chain and Logistics
Ever had a package stuck in customs? Now imagine that’s your entire component shipment. Global supply chains are a rollercoaster—shipping costs, delays, even trade wars can jack up prices. I once worked with a team that switched to local suppliers mid-project; it saved time but cost more upfront. As a designer, ask: Can I source closer to home, or is overseas still worth it?
2.4 Research and Development (R&D)
R&D is where dreams are born—and budgets get tested. Prototyping, testing, tweaking—it’s all money out the door before you even hit production. But here’s the flip side: A solid R&D phase can optimize your design, slashing costs later. I’ve seen teams skimp here and regret it when assembly hit snags. Invest smartly upfront; it’s your insurance policy.
3. Cost Breakdown by Product Type
Not all electronics are created equal. Here’s how costs play out depending on what you’re building.
3.1 Consumer Electronics
Smartphones, TVs, laptops—these are the bread and butter of high-volume, low-margin manufacturing. Costs here are all about scale and competition. I’ve heard designers groan about razor-thin budgets, but that’s the game. Your focus? Streamline for mass production and keep an eye on trends like foldable screens driving up material costs.
3.2 Industrial Electronics
Think sensors or factory controllers. These don’t need to be cheap—they need to last. I once toured a plant where a single ruggedized component cost more than my car, but it ran 24/7 for years. Durability and precision trump price here, so your designs might lean on pricier materials or testing.
3.3 Specialized Electronics
Medical devices or aerospace parts are the VIPs of manufacturing. Low volumes, insane standards (think FDA or MIL-SPEC), and zero room for error mean costs soar. I’ve seen teams pour months into a single prototype—and it paid off when lives were on the line. Your mantra? Quality over cost, every time.
4. Strategies to Optimize Electronics Manufacturing Costs
You’re not helpless here. As a designer or decider, you’ve got tools to keep costs in check without sacrificing your vision.
4.1 Design for Manufacturability (DFM)
This is my favorite trick: Design with the factory in mind. Simplify assembly, reduce part counts, avoid tricky tolerances—I’ve seen DFM cut costs by 20% on a project without losing functionality. Talk to your manufacturer early; they’ll thank you, and so will your wallet.
4.2 Supplier Negotiations
Don’t just take the first quote. Build relationships with suppliers—I’ve watched a savvy decider lock in better rates by promising repeat business. It’s not just about haggling; it’s about partnership.
4.3 Automation and AI Integration
Robots and AI aren’t sci-fi anymore—they’re your allies. Automating repetitive tasks or using AI to predict defects can trim labor costs and boost quality. I’ve seen small firms resist this, only to fall behind. Dip your toe in; the payoff’s worth it.
4.4 Lean Manufacturing
Cut the fat. Lean principles—minimizing waste, streamlining workflows—can save big. A colleague once slashed prototyping time by rethinking material scraps. It’s practical, not preachy, and it works.
5. Current Trends Impacting Costs (as of March 2025)
The world’s shifting under our feet, and 2025’s no exception. Here’s what’s shaking up costs right now.
Sustainability Push: Eco-friendly materials like recycled plastics or lead-free solder are hot, but they’re pricier. Customers love green, though—worth it for your brand?
Chip Shortage Hangover: Supplies are rebounding, but prices haven’t fully settled. Plan for flexibility in your designs.
3D Printing Rise: Additive manufacturing’s cutting prototyping costs for small runs. I’ve seen it firsthand—game-changing for niche projects.
Regional Shifts: Trade policies are nudging manufacturing back to places like the U.S. or Mexico. Closer might mean faster, but not always cheaper.
6. Case Study: The Smartphone Cost Puzzle
Take a smartphone—say, a mid-range model hitting shelves in 2025. Raw materials (screen, chip, battery) might run $100. Labor and assembly? Maybe $10 in a high-automation plant. Equipment and overhead tack on another $20, and R&D spreads $50 across a million units. Total cost: ~$180. Sell it for $400, and you’ve got margin—but only if volume and design align. Designers swapped a premium chip for a solid mid-tier one, saving $20 per unit. That’s your power in action.
Conclusion
Manufacturing costs aren’t just numbers—they’re the heartbeat of your project. From materials to labor, scale to complexity, every decision you make as a designer or decider shapes the outcome. In 2025, with trends like sustainability and automation in play, you’ve got more tools than ever to balance cost, quality, and innovation.
So, next time you’re sketching that brilliant idea or signing off on a production run, think about the ripple effects. Your design isn’t just a product—it’s a cost story. What’s yours going to say? Drop your thoughts or questions below—I’d love to hear how you’re tackling this beast!