Best Practices for Testing and Validating Electronic Components
Testing and validating electronic components not only reduce the risk of failures but also safeguard the quality, durability, and safety of the final product.
2/18/20256 min read
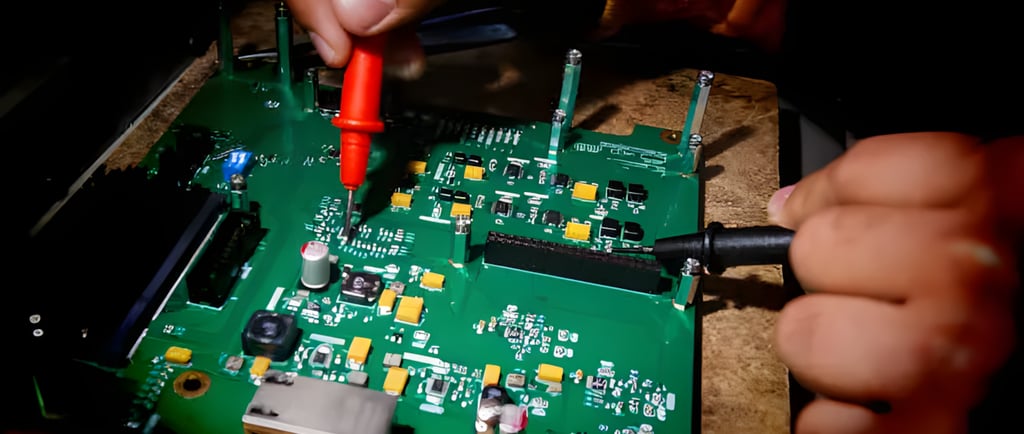
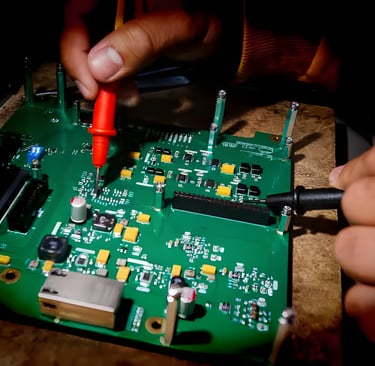
In the world of electronics development, the performance of individual components often determines the success or failure of an entire product. Whether you're designing the latest smartphone, building a cutting-edge medical device, or working on high-stakes aerospace equipment, ensuring that your components meet rigorous performance standards is non-negotiable. Testing and validating electronic components not only reduce the risk of failures but also safeguard the quality, durability, and safety of the final product.
In this article, we’ll explore the best practices for testing and validating electronic components. We’ll dive into the different methods of testing, provide real-world examples, and share insights on how to ensure your components perform as expected. By the end, you'll have a comprehensive understanding of how to approach component testing in electronics development.
1. Understanding the Basics of Component Testing and Validation
At the heart of electronics development, two critical concepts often intertwine: testing and validation. Both are aimed at ensuring that components work as expected and meet design requirements, but they focus on different aspects of the process.
Testing refers to the examination of a component’s behavior and functionality under various conditions. It’s about checking whether the component works according to its specifications.
Validation, however, ensures that a component is suitable for its intended application. It validates that the component not only meets specifications but also performs as expected within the system it’s designed for.
Real-World Example:
For instance, in the automotive industry, a semiconductor chip that controls airbag deployment must be tested for both functionality (is it correctly reading signals?) and validation (will it deploy the airbag in extreme crash scenarios?).
Testing is essential for components ranging from semiconductors and resistors to capacitors and connectors. A small failure in any of these could lead to catastrophic consequences. In fact, faulty components were found to be responsible for 30% of product recalls in the automotive industry alone in 2022, according to the National Highway Traffic Safety Administration (NHTSA).
2. Pre-Testing Considerations
Before diving into testing methods, the groundwork must be laid with pre-testing considerations. These early decisions will guide the testing process and ensure that you focus on the right areas.
Defining Testing Objectives
Clearly defining your testing objectives is crucial. Are you simply checking if the component works, or are you pushing it to its limits? For example, a capacitor in a power supply needs functional testing to ensure it handles the correct voltage, but it might also require stress testing to ensure it can withstand power surges without failure.
Case Study: Semiconductor Industry
In the semiconductor industry, validation is often done using Automated Test Equipment (ATE), which helps simulate the actual operating conditions of the semiconductor before integration into the final product. A real-world case can be drawn from Intel, which conducts over 200 types of tests on its chips, including burn-in tests (extended periods of operation under high temperature) and electrical tests for functionality.
Understanding Standards and Certifications
Industry standards like RoHS (Restriction of Hazardous Substances) and UL (Underwriters Laboratories) certifications play a crucial role. For instance, medical devices need to comply with ISO 13485, which ensures consistent quality in medical component manufacturing. These standards guide the testing process to ensure components are both safe and reliable.
Operating Environment
Understanding where the component will operate is just as important. Components for consumer electronics may only need to withstand moderate temperatures, while those in space applications need rigorous testing to endure extreme cold, high radiation, and vacuum conditions. A famous case here is NASA’s Mars Rover program, where components are subjected to thermal cycling tests and vibration tests to simulate the harsh conditions of space travel.
3. Common Testing Methods for Electronic Components
Once the groundwork is laid, the actual testing can begin. There are several methodologies used to test components, each suited to different needs.
Visual Inspection
Visual inspection might seem basic, but it is an important first step in detecting defects such as cracks, incorrect markings, or soldering issues. This method is particularly useful for components like PCBs (printed circuit boards) or connectors where physical integrity plays a crucial role in performance.
Electrical Testing
Electrical testing involves measuring parameters such as resistance, voltage, current, and capacitance. Using tools like multimeters, oscilloscopes, and function generators, engineers can identify whether a component behaves as expected. For instance, when testing a diode, electrical testing can confirm its forward voltage drop to ensure proper functionality in a circuit.
Case Study: Testing Power Supply Components
For example, Toshiba conducts electrical tests on its power supply components using a power analyzer to ensure they can handle fluctuations in voltage, preventing potential product failures in high-demand applications like medical equipment.
Functional Testing
This type of testing ensures the component works within the broader system. For example, when testing an IC (integrated circuit), you might need to ensure that it communicates correctly with other components, processes signals appropriately, and triggers the intended actions in the system.
Functional testing is critical in industries like automotive electronics, where a component such as an ABS braking system sensor must be thoroughly validated to work accurately in real-time conditions, detecting minute changes in pressure or temperature.
Stress Testing
Stress testing pushes components beyond their normal operating conditions to determine their limits. For example, a battery used in electric vehicles (EVs) will undergo high-temperature testing to ensure it can handle the heat generated during fast charging or long-duration use.
Case Study: Smartphone Industry
A well-known example of stress testing comes from Apple, which performs thermal cycling and over-voltage tests on its phone components to ensure that they can withstand the pressure of prolonged use in diverse climates. Apple’s iPhone 13 was subjected to 500 test hours under high temperatures and rapid charging conditions to ensure reliability over time.
Environmental Testing
Environmental tests simulate the conditions components will experience in the real world, such as moisture, vibration, temperature extremes, and UV exposure. Components in products like wearable devices or outdoor security cameras undergo environmental testing to ensure they can withstand rain, snow, and even direct sunlight.
4. Choosing the Right Testing Equipment
The choice of testing equipment plays a crucial role in the success of your testing strategy. The right tools allow you to carry out more precise and efficient testing, which can ultimately save time and money.
For instance:
Multimeters are useful for basic measurements such as voltage and resistance.
Oscilloscopes help visualize electrical signals in real time.
Automated Test Systems (ATS) allow high-volume, consistent testing, essential in industries like consumer electronics where large quantities of components need to be tested simultaneously.
Real-World Example: Automotive Industry
The automotive industry relies heavily on Automated Test Equipment (ATE) for ECUs (electronic control units). For example, Bosch uses ATE systems to simulate the real-world operating conditions of ECUs in various car models, helping to detect any failure points before mass production.
5. Validation vs. Verification
Both validation and verification are essential, but they address different aspects of the testing process.
Validation checks if the component meets the intended specifications. For example, Intel validates its processors by checking performance parameters such as processing speed, temperature, and power consumption.
Verification, on the other hand, checks if the component works correctly within the system. For instance, an automotive sensor might be verified for its response times and compatibility with other sensors and the vehicle’s control systems.
6. Automating the Testing Process
In today’s fast-paced electronics market, automation has become a key player. Automated testing systems can perform repetitive tasks with higher efficiency and accuracy than manual testing methods. These systems are essential in high-volume manufacturing environments, where consistency is paramount.
For example, Samsung uses robotic testing systems to automate the testing of smartphone components. These robots run continuous tests on thousands of components each day, ensuring that every device meets stringent performance requirements.
7. Documenting Test Results and Creating Reports
Accurate and thorough documentation of test results is essential for compliance and quality assurance. Test reports should clearly outline:
Test methodology: How the test was performed.
Test conditions: The environment in which the test was conducted.
Results: Pass/fail status, along with any anomalies observed.
Corrective actions: If the component failed, what steps were taken to resolve the issue.
Real-World Example: Aerospace Industry
In aerospace, precise documentation is critical for safety. Boeing, for example, maintains an exhaustive record of test results for every component in its aircraft. These reports not only ensure compliance with aviation regulations but also serve as a basis for any troubleshooting or improvements needed in future designs.
8. Post-Testing Actions and Troubleshooting
When a component fails testing, it’s crucial to understand why. Engineers must analyze the test data and determine whether the issue lies with the component itself, the design, or the manufacturing process.
Case Study: Consumer Electronics
In the consumer electronics space, companies like Sony conduct root-cause analysis when components fail in testing. For instance, if a microphone component in a smartphone fails an acoustic test, the team will evaluate if the issue stems from a design flaw, faulty materials, or suboptimal manufacturing processes.
9. Best Practices for Ongoing Testing and Quality Assurance
Testing should not be a one-time event. Continuous testing throughout the lifecycle of a product ensures that it remains reliable and safe. This means performing tests even after production begins, using feedback loops from the production line to identify issues early.
In addition, collaborating with suppliers to ensure consistent component quality is vital for ongoing success. For example, Apple works closely with suppliers to ensure that the components meet exacting standards, which helps to prevent issues in the mass production stage.
Conclusion
The process of testing and validating electronic components is complex but vital to ensuring the quality and reliability of your product. By following best practices, choosing the right testing methods, and using the right tools, you can avoid costly mistakes and deliver products that meet or exceed expectations. From semiconductors in space applications to capacitors in consumer electronics, thorough testing ensures that every component plays its part in the overall success of the product.
By implementing the strategies outlined in this article, electronics designers and decision-makers can improve their development processes, enhance product reliability, and reduce risks, ultimately creating innovative and high-quality products that stand the test of time.