Automation in Electronics Manufacturing: Robots, Cobots, and Beyond
Gone are the days when electronics manufacturing was purely a labor-intensive process. The modern factory floor is now populated with advanced machinery that can work faster and with more precision than ever before. From traditional industrial robots to collaborative robots (cobots) and cutting-edge technologies powered by artificial intelligence (AI), automation is reshaping how electronics are designed and produced.
2/16/20254 min read
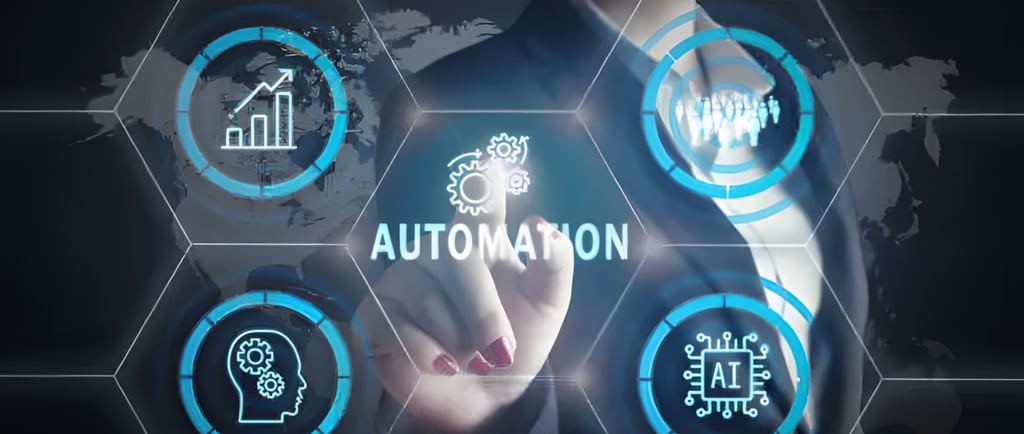
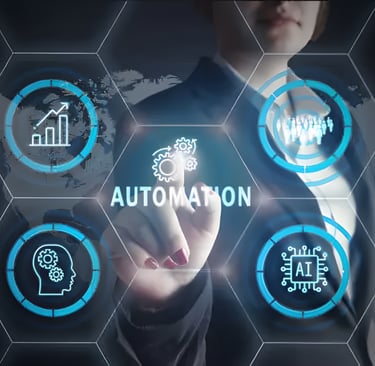
Electronics manufacturing has always been a rapidly evolving field, driven by the dual pressures of innovation and efficiency. In today’s competitive landscape, meeting customer demands while maintaining cost control is a significant challenge. To stay ahead, companies are increasingly turning to automation.
Gone are the days when electronics manufacturing was purely a labor-intensive process. The modern factory floor is now populated with advanced machinery that can work faster and with more precision than ever before. From traditional industrial robots to collaborative robots (cobots) and cutting-edge technologies powered by artificial intelligence (AI), automation is reshaping how electronics are designed and produced.
This article takes a deep dive into the role of automation in electronics manufacturing. Whether you’re a designer striving to improve production processes or a decision-maker considering the next big investment, understanding the landscape of robots, cobots, and beyond is essential to staying competitive in a rapidly changing world.
1. The Role of Automation in Electronics Manufacturing
Automation in electronics manufacturing isn’t just about replacing human workers. It’s about enhancing precision, improving consistency, and scaling production to meet growing demands. As consumer electronics become smaller and more complex, manual processes struggle to keep up. Automation, however, allows for the production of intricate components at scales unimaginable just a few decades ago.
Key Benefits of Automation:
Increased Efficiency: Machines can operate around the clock without fatigue, accelerating production timelines.
Precision and Consistency: Automated systems reduce human error and ensure uniform quality across batches.
Cost Reduction: Although the initial investment can be high, automation reduces long-term labor costs and minimizes waste.
Scalability: Automated processes can be quickly scaled to accommodate spikes in demand without sacrificing quality.
However, implementing automation isn’t without its challenges. High upfront costs, integration complexities, and the need to retrain workers can pose barriers. Successful adoption requires careful planning and a long-term vision.
2. Robots in Electronics Manufacturing
When people think about automation, the image that often comes to mind is a robotic arm working tirelessly on an assembly line. This isn’t far from reality. Robots have become a staple in electronics manufacturing, handling tasks ranging from assembly to quality inspection.
Types of Robots Used in Electronics Manufacturing:
Industrial Robots:
These are the workhorses of the factory floor, capable of performing repetitive tasks with extreme precision. They are often used for soldering, welding, and high-speed assembly.
SCARA Robots (Selective Compliance Assembly Robot Arm):
Ideal for delicate and precise tasks like assembling small electronic components. Their speed and accuracy make them indispensable in printed circuit board (PCB) manufacturing.
Articulated Robots:
With multiple joints, these robots offer increased flexibility. They are used in inspection, packaging, and material handling.
Key Applications of Robots in Electronics Manufacturing:
PCB Assembly: Robots can place tiny components onto boards with speed and precision that humans simply cannot match.
Component Soldering: Automated soldering ensures consistent and reliable joints, improving product durability.
Quality Inspection: Advanced robots equipped with vision systems can identify defects at microscopic levels.
Warehousing and Material Handling: Robots can transport raw materials and finished products, optimizing logistics.
While robots have revolutionized many aspects of manufacturing, they still operate in isolation, often fenced off from human workers for safety reasons. This is where cobots come into play.
3. Cobots: Enhancing Human-Robot Collaboration
Collaborative robots, or cobots, are designed to work alongside human operators. Unlike traditional robots, which often require safety cages, cobots are equipped with sensors and safety mechanisms that allow them to operate safely in human environments.
What Sets Cobots Apart?
Safety Features: Built-in collision detection ensures that cobots can work near humans without posing a safety risk.
Flexibility: Cobots are easier to program and reconfigure, making them ideal for low-volume, high-mix production environments.
Cost-Effective: With lower upfront costs compared to industrial robots, cobots are accessible to small and medium-sized manufacturers.
Applications of Cobots in Electronics Manufacturing:
Soldering and Assembly Assistance: Cobots can perform repetitive soldering tasks while human workers handle complex adjustments.
Quality Control: Cobots equipped with advanced vision systems can perform detailed inspections alongside human inspectors.
Packaging and Labeling: Cobots handle delicate electronics packaging without damaging sensitive components.
The ability of cobots to collaborate seamlessly with human workers opens new possibilities for electronics manufacturing. They are especially useful for tasks requiring a blend of human judgment and machine precision.
4. Beyond Robots and Cobots: Emerging Automation Technologies
The automation landscape extends far beyond traditional robotics. New technologies are pushing the boundaries of what’s possible, enhancing productivity and enabling smarter manufacturing environments.
AI and Machine Learning:
Predictive Maintenance: AI can analyze data from machines to predict and prevent failures before they occur.
Quality Control: Machine learning algorithms can identify defects in real time, improving accuracy and reducing waste.
Industrial Internet of Things (IIoT):
Smart Factories: IIoT enables interconnected systems that monitor and optimize every aspect of the manufacturing process.
Data-Driven Decision Making: Real-time data collection allows manufacturers to respond quickly to production issues.
Autonomous Mobile Robots (AMRs):
Material Transport: AMRs autonomously move materials across large factory floors, reducing manual labor.
Warehouse Integration: These robots streamline logistics by integrating with warehouse management systems.
3D Printing and Additive Manufacturing:
Rapid Prototyping: 3D printing accelerates product development cycles by enabling quick prototyping.
Customized Components: Additive manufacturing allows for the creation of specialized, low-volume parts.
5. Challenges and Considerations for Implementing Automation
While the benefits of automation are substantial, implementation comes with challenges that must be carefully managed.
Cost and ROI Analysis:
Evaluate the long-term savings against the initial investment. Focus on areas where automation can deliver the highest impact.
Workforce Upskilling:
Invest in training programs to equip employees with the skills to work alongside automated systems.
System Integration:
Ensure new automation technologies are compatible with existing production lines.
Cybersecurity Risks:
Protect connected systems from cyber threats through robust security measures and regular audits.
6. The Future of Automation in Electronics Manufacturing
As technology continues to evolve, the future of automation in electronics manufacturing looks promising and dynamic.
AI-Driven Automation: Expect deeper integration of artificial intelligence to enhance decision-making and process optimization.
Fully Autonomous Factories: While still on the horizon, lights-out manufacturing is becoming increasingly feasible.
Supply Chain Transformation: Automation can improve supply chain resilience by reducing dependencies on manual labor.
Companies that embrace these advancements will not only gain a competitive edge but also position themselves to adapt to future market demands.
Conclusion
Automation is no longer a futuristic concept—it’s a present-day reality transforming electronics manufacturing. Robots bring speed and precision, cobots enhance human collaboration, and emerging technologies like AI and IIoT promise even greater possibilities.
For designers and decision-makers, understanding the automation landscape is crucial. By thoughtfully integrating these technologies, businesses can achieve new levels of efficiency, quality, and innovation.
The future of electronics manufacturing is automated. The question is: Are you ready to embrace it?