8 Strategies for Optimizing Supply Chains in Electronics Manufacturing: The Made-in-China Advantage
With the rise of global supply chain disruptions, component shortages, and evolving regulations, companies must build robust and resilient supply networks to stay competitive.
2/19/20254 min read
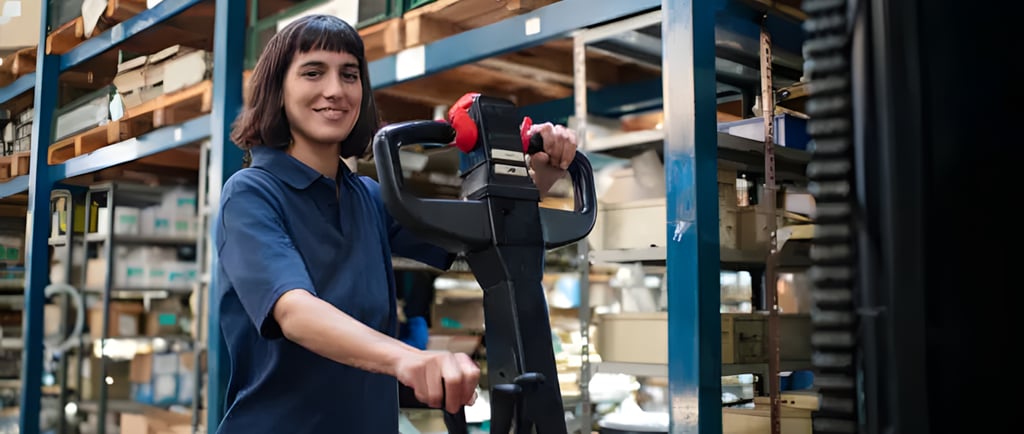
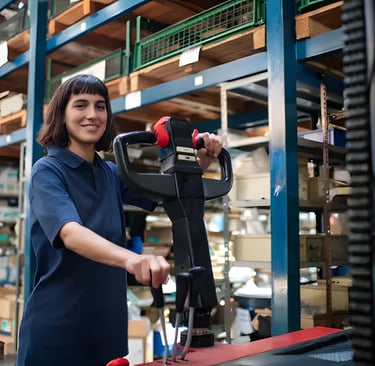
The electronics manufacturing industry operates in a high-stakes, fast-moving landscape where supply chain efficiency can determine a company’s success or failure. From product design to manufacturing, distribution, and end-of-life management, every step presents challenges that require strategic planning.
With the rise of global supply chain disruptions, component shortages, and evolving regulations, companies must build robust and resilient supply networks to stay competitive. In this article, we explore eight best practices for optimizing supply chains, with a special focus on the “Made in China” advantage—how manufacturers in China have fine-tuned these processes for efficiency, scalability, and cost-effectiveness.
1. Streamline the Design-to-Launch Process
A well-optimized design-to-launch process minimizes risks and delays. Chinese manufacturers have mastered rapid product development by closely integrating suppliers, engineers, and manufacturers from the outset. By leveraging well-established production hubs like Shenzhen, companies can prototype and scale production faster than anywhere else in the world.
Key benefits of early supplier involvement include:
Faster feedback loops to refine designs for manufacturability.
Immediate access to raw material availability insights.
Improved cost estimation and production planning.
For example, leading contract manufacturers in China work closely with startups and established brands alike to provide Design for Manufacturing (DFM) analysis, ensuring products are not just innovative but also feasible to produce at scale.
2. Address Preventable Challenges
Supply chain disruptions—such as delays, component shortages, and sudden price hikes—are common in the microelectronics sector. The Chinese supply chain ecosystem mitigates these risks by:
Utilizing smart manufacturing technologies and automation.
Establishing strong relationships with multiple component suppliers to ensure backup sourcing.
Leveraging real-time data analytics to monitor supply chain health.
Cloud-based supply chain management and AI-driven forecasting tools are widely adopted in China, helping companies predict potential bottlenecks and proactively address them before they become critical problems.
3. Achieve Faster Time-to-Market
Speed to market is a critical competitive advantage in the electronics industry. China’s unparalleled manufacturing infrastructure, experienced workforce, and deep supplier networks enable companies to go from concept to mass production in record time.
Ways to accelerate time-to-market include:
Rapid prototyping services available in manufacturing hubs like Shenzhen and Dongguan.
Highly flexible production lines that accommodate quick design iterations.
Efficient supply chain logistics that shorten lead times for components and finished products.
A major reason why global tech giants partner with Chinese manufacturers is their ability to turn around high-quality, production-ready prototypes in as little as a few days—a process that could take weeks or months elsewhere.
4. Prepare for Supply Chain Disruptions
Uncertainty is a given in global supply chains, whether due to geopolitical tensions, natural disasters, or unforeseen market shifts. A proactive approach to risk management is essential.
Chinese manufacturers excel in resilience planning by:
Maintaining extensive supplier networks to mitigate reliance on a single source.
Investing in large-scale component warehousing and inventory management.
Adopting dual-sourcing strategies to prevent bottlenecks.
For instance, some leading electronics manufacturers maintain redundant supply chains by sourcing critical components from both domestic and international suppliers, ensuring production continuity even if one supply source is disrupted.
5. Prioritize Manufacturing Capacity
Production bottlenecks can delay product launches and impact profitability. To avoid this, companies must work closely with contract manufacturers (CMs) to align production capacity with demand forecasts.
Chinese manufacturers manage capacity effectively by:
Operating large-scale production facilities with flexible scheduling.
Deploying automation and AI-driven production line optimization.
Offering tiered production scaling, allowing brands to ramp up or down as needed.
A well-known advantage of working with Chinese CMs is their ability to scale rapidly without compromising quality—a crucial factor for companies launching new electronics products.
6. Manage Obsolescence Risk
Component obsolescence is a major challenge in electronics manufacturing. To mitigate this risk, manufacturers should have a structured plan for dealing with discontinued components.
Best practices include:
Partnering with suppliers who provide early notifications about upcoming component phase-outs.
Investing in last-time buys for critical components.
Using AI-driven BOM (Bill of Materials) management systems to identify alternative parts.
Chinese manufacturers excel in proactive obsolescence management, often maintaining deep relationships with component suppliers to ensure timely transitions to alternative components.
7. Secure Authorized Distribution Channels
Using authorized distribution channels is essential for ensuring product quality and reliability. Counterfeit or substandard components can introduce significant risks to product performance and brand reputation.
To safeguard supply chain integrity, manufacturers should:
Source components from verified, reputable distributors.
Implement stringent quality control measures at incoming inspection stages.
Work with CMs that have established partnerships with top-tier suppliers.
China’s electronics ecosystem includes several industry-leading component distributors that enforce strict quality assurance standards, helping manufacturers maintain high product reliability.
8. Plan for Product End-of-Life
End-of-life (EOL) planning is often overlooked but plays a critical role in long-term supply chain efficiency. Manufacturers should develop exit strategies for products that are being phased out to minimize waste and maximize value recovery.
Key strategies include:
Identifying opportunities for product repurposing or resale.
Managing last-time buys effectively to avoid excess inventory.
Recycling and sustainability initiatives to reduce environmental impact.
Many Chinese manufacturers integrate EOL planning into the initial product development phase, ensuring a seamless transition when a product reaches the end of its lifecycle.
The Made-in-China Edge: A Holistic Advantage
China’s dominance in electronics manufacturing is no accident—it’s the result of decades of investment in infrastructure, workforce development, and supply chain optimization. Companies that leverage the strengths of the Chinese supply chain can benefit from:
Cost Efficiency: Competitive production costs without sacrificing quality.
Speed to Market: Rapid prototyping and mass production capabilities.
Scalability: The ability to scale up production quickly as demand grows.
Supply Chain Resilience: Strong supplier networks and risk mitigation strategies.
Innovation Ecosystem: Close proximity to cutting-edge technology development hubs.
For businesses looking to optimize their electronics supply chains, integrating Chinese manufacturing advantages into their strategy can yield significant competitive benefits. By adopting these best practices and tapping into China’s extensive manufacturing ecosystem, companies can navigate supply chain complexities and achieve long-term success in the dynamic world of electronics manufacturing.
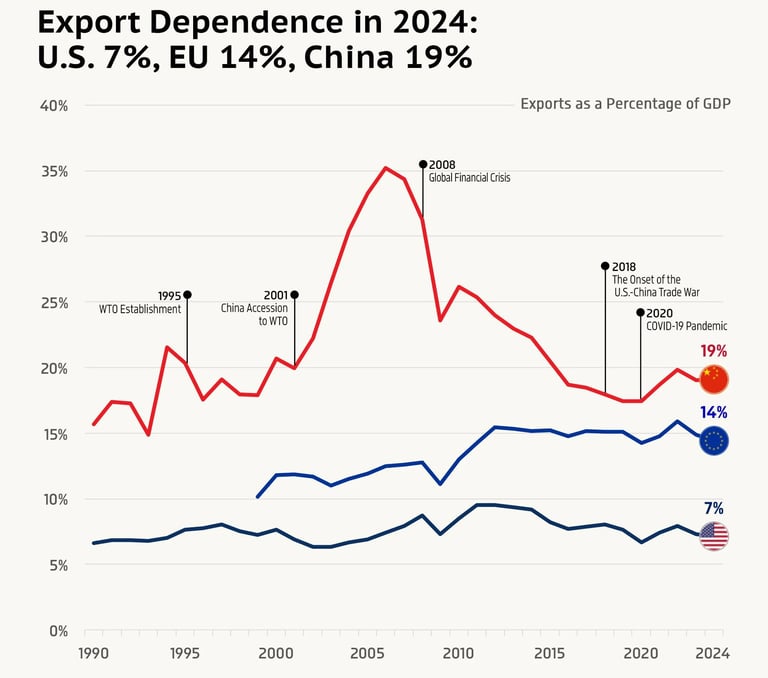
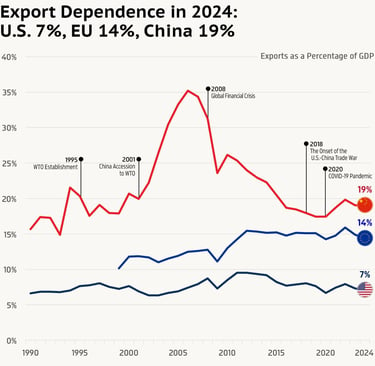