6 Types of Electronics Manufacturing Explained: A Guide for Designers and Decision-Makers
From the tiniest microchip to the dashboard of an electric car, manufacturing is where ideas turn into reality. And for designers and decision-makers like you, understanding the different types of electronics manufacturing isn’t just useful—it’s essential.
2/27/20256 min read
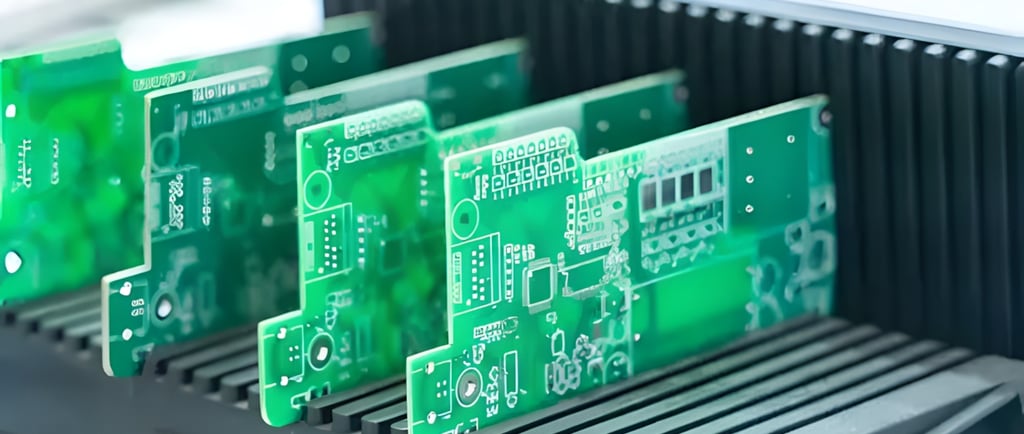
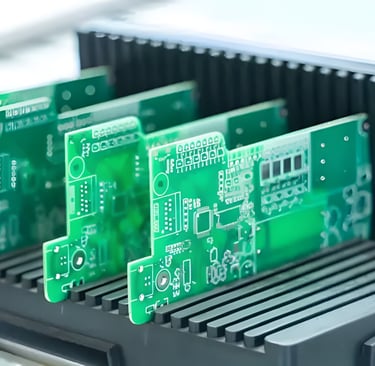
Picture this: you’re holding your shiny new smartphone, marveling at its sleek design and lightning-fast performance. Or maybe you’re in a meeting, deciding which processor will power your company’s next big product. Either way, none of it would exist without electronics manufacturing—the unsung hero behind every gadget, gizmo, and game-changer in our lives. From the tiniest microchip to the dashboard of an electric car, manufacturing is where ideas turn into reality. And for designers and decision-makers like you, understanding the different types of electronics manufacturing isn’t just useful—it’s essential.
So, let’s take a deep dive into this world. We’ll explore the key types, break down what makes them tick, and figure out how they fit into your next project. Ready? Let’s get started.
What is Electronics Manufacturing?
At its core, electronics manufacturing is about turning raw materials and brilliant designs into functional devices. It’s the process of designing, assembling, and testing electronic components—everything from resistors to full-blown systems like medical scanners or gaming consoles. If you’re a designer, you’re sketching the blueprints. If you’re a decision-maker, you’re picking the paths that bring those blueprints to life.
This isn’t some niche corner of industry—it’s everywhere. Think consumer electronics (your phone, your TV), healthcare (MRI machines), aerospace (navigation systems), even the automotive world (self-driving car tech). Every sector leans on manufacturing to deliver. But here’s the kicker: not all manufacturing is created equal. Depending on your product, budget, and timeline, you’ll need to know which type fits the bill. So, let’s unpack the six big players in this game.
Types of Electronics Manufacturing
1. Printed Circuit Board (PCB) Manufacturing
If electronics had a backbone, it’d be the PCB. This is where it all starts—those flat, green boards you’ve probably seen inside every device. They’re the foundation that holds and connects every component, from capacitors to chips. For you designers out there, this is your canvas. You’re sketching traces and plotting layouts, dreaming up how power and signals will flow.
The process? It’s a mix of art and science. It starts with designing the board—often using software like Altium or Eagle—then etching copper onto a substrate to create circuits. Layers get stacked, holes drilled, and voilà, you’ve got a PCB ready for components. Think of it as building the skeleton of your product, whether it’s a motherboard for a laptop or a control board for a smart thermostat.
Why should you care? Because every choice here—single-layer vs. multi-layer, rigid vs. flexible—impacts cost, size, and performance. Mess it up, and your whole design could falter. Get it right, and you’ve got a solid base to build on.
2. Surface-Mount Technology (SMT)
Now, let’s zoom in. Surface-mount technology (SMT) is how those tiny components—like resistors, capacitors, and ICs—get slapped onto your PCB. It’s the go-to for modern devices because it’s fast, precise, and perfect for miniaturization. If you’re designing a sleek wearable or a compact IoT sensor, SMT is your best friend.
Here’s how it works: automated machines use solder paste to stick components directly onto the board’s surface—no drilling required. Then, the whole thing gets baked in a reflow oven to lock everything in place. I’ve seen SMT lines in action, and it’s like watching a high-speed ballet—robots whirring, components flying into place. The result? Devices like smartphones or LED panels that pack insane tech into tiny spaces.
For decision-makers, SMT’s speed and scalability are gold. But it’s not invincible—vibration or heat can stress those surface connections. Still, when you need small and efficient, this is the way to go.
3. Through-Hole Technology
On the flip side, we’ve got through-hole technology—the old-school champ that’s still kicking. This method involves drilling holes in the PCB and threading component leads through them, soldering them on the other side. It’s hands-on, sturdy, and built to last. Think of it like riveting a bridge—less about speed, more about strength.
You’ll see through-hole in heavy-duty gear: industrial machines, military equipment, or even vintage amps. I once helped a buddy fix an old guitar amp, and those chunky solder joints were a testament to this method’s durability. It’s not as fast as SMT—sometimes it’s even manual—but it holds up under stress or high power.
Designers, this one’s for you when reliability trumps size. Decision-makers, weigh the trade-off: it’s costlier and slower, but if your product needs to survive a beating, through-hole’s got your back.
4. Semiconductor Manufacturing
Now we’re talking the brains of the operation—semiconductors. These are the microchips and integrated circuits that power everything from your laptop to your car’s navigation. If you’re designing cutting-edge tech, this is where your innovation lives. If you’re deciding budgets, this is where costs can skyrocket.
The process is mind-blowing. It starts with purifying silicon into wafers, then using photolithography—basically light-based etching—to carve intricate patterns. Add some chemical doping to tweak conductivity, and you’ve got a chip. I toured a fab once, and it felt like stepping into a sci-fi movie—cleanrooms, bunny suits, machines humming. Companies like TSMC and Intel have turned this into an art form, churning out processors that fit billions of transistors into a fingernail-sized space.
Why it matters? Performance. Your product’s speed, efficiency, and smarts hinge on this. But fair warning: lead times are long, and costs are steep—especially with today’s chip shortages. Plan ahead.
5. Electronics Assembly (Box Build)
This is where it all comes together—electronics assembly, or “box build.” It’s the final sprint: taking PCBs, wiring, enclosures, and software, then turning them into a finished product. Imagine assembling a puzzle—every piece has to fit perfectly. For designers, this is where your prototypes get real. For decision-makers, it’s where timelines and quality control collide.
The process varies—some lines are automated, others need human hands for custom tweaks. Testing’s huge here; no one wants a TV that fries on day one. I’ve seen assembly floors buzzing with energy—workers slotting boards into casings, running diagnostics, boxing up dreams.
This stage is make-or-break. A flawless design can still flop if assembly’s sloppy. So, choose your partners wisely—whether in-house or outsourced, precision is non-negotiable.
6. Contract Manufacturing
Speaking of outsourcing, let’s talk contract manufacturing. This is when you hand the reins to a third party—think Foxconn building iPhones for Apple. They handle design tweaks, production, even assembly, while you focus on strategy and branding. It’s a lifeline for scaling fast without building your own factory.
How it works? You send specs, they deliver. Some offer end-to-end services; others specialize in PCBs or assembly. I’ve worked with teams who swear by this—frees up time and cash. But here’s the catch: communication’s critical. One misstep, and your vision’s lost in translation.
For decision-makers, it’s about cost vs. control. Designers, it’s a chance to lean on expertise. Either way, it’s a powerhouse option in today’s global market.
Comparing the Types
So, how do these stack up? Let’s break it down. PCB manufacturing sets the stage—cost varies by complexity (multi-layer boards aren’t cheap). SMT’s fast and lean, perfect for mass production, but lacks the ruggedness of through-hole, which shines in durability at a higher price. Semiconductors are the priciest and most complex—think millions in R&D—but they’re unmatched for performance. Assembly ties it all together, balancing labor and precision, while contract manufacturing hinges on your partner’s efficiency.
Take SMT vs. through-hole: one’s a sprinter, the other’s a tank. Your choice depends on the product—sleek consumer tech or rugged industrial gear? Every type has its sweet spot. Know your goals, and you’ll pick the winner.
Trends Shaping Electronics Manufacturing
This field’s not standing still. Automation’s exploding—robots now handle SMT and assembly with eerie precision. Miniaturization’s pushing limits; I saw a prototype last year so small it fit on a dime. Sustainability’s creeping in too—recycled materials, energy-efficient fabs. And AI? It’s optimizing everything, from design software to supply chains.
The future’s wild. Think 3D-printed circuits or bio-integrated chips. For you designers, it’s a playground. For decision-makers, it’s a chance to leap ahead—or get left behind. Stay sharp.
Conclusion
From PCBs to contract manufacturing, electronics manufacturing is a tapestry of choices—each thread weaving its own story. As a designer, you’re crafting the next big thing. As a decision-maker, you’re steering the ship. Together, you’re shaping a world where tech keeps us connected, healthy, and moving.
Next time you hold a gadget, think about the magic behind it—the etching, the soldering, the assembly line hustle. Got a favorite type or a project in mind? Drop a comment—I’d love to hear your take. Let’s keep building the future, one circuit at a time.