6 Cutting-Edge Trends in Metal Fabrication Revolutionizing Electronics
Metal fabrication isn’t just a backroom process—it’s the backbone of every sleek device we dream up. From the enclosures protecting your latest smartphone to the heat sinks keeping processors cool, the way we shape metal directly impacts what’s possible.
2/26/20255 min read
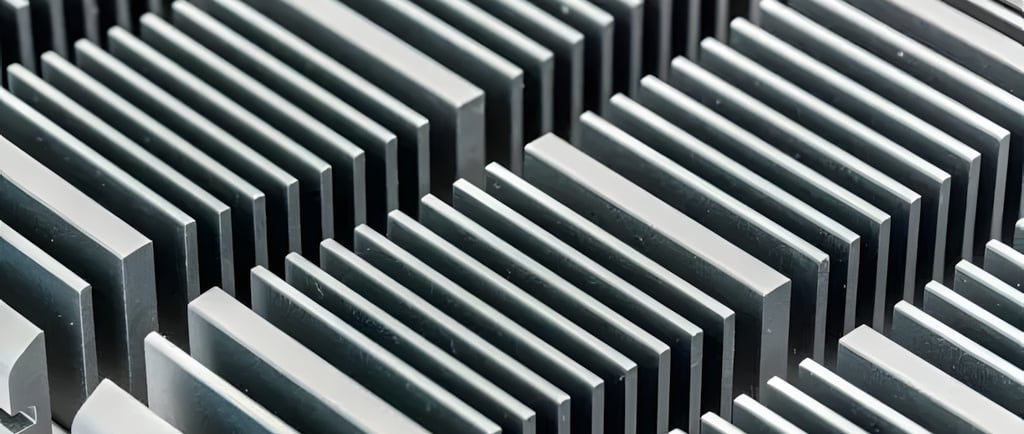
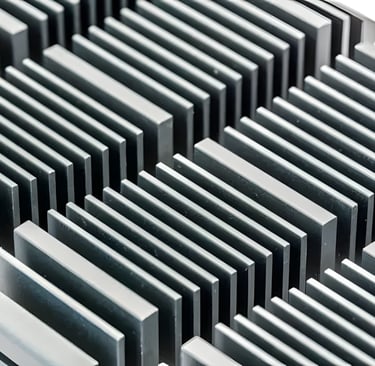
If you’re a designer or decision-maker in the electronics world, you know metal fabrication isn’t just a backroom process—it’s the backbone of every sleek device we dream up. From the enclosures protecting your latest smartphone to the heat sinks keeping processors cool, the way we shape metal directly impacts what’s possible. Lately, I’ve been diving into how this field is evolving, and let me tell you, it’s buzzing with innovations that could change the game for your next project. We’re talking automation, 3D printing with metals, and alloys that sound like they’re from a sci-fi movie. Ready to see what’s shaping the future of electronics fabrication? Let’s dig into six trends that deserve your attention.
1. Automation and Robotics: The Hands-Off Revolution
Picture this: a factory floor where robotic arms hum along, welding tiny connectors with precision no human hand could match. That’s not a distant dream—it’s happening now. Automation has taken metal fabrication by storm, and for good reason. Designers, you know how tight tolerances are in electronics. A fraction of a millimeter off, and your circuit board frame won’t fit. Robotics—think CNC machines on steroids and AI-driven welders—are stepping in to nail those specs every time.
I recently read about a company using robotic arms to churn out chassis for IoT devices at lightning speed. What used to take hours of manual tweaking now happens in minutes, with zero defects. For decision-makers, this means shorter lead times and lower labor costs—music to any budget meeting’s ears. But it’s not just about efficiency. These machines can handle the intricate, repetitive tasks that wear out even the best technicians, leaving your team free to focus on the creative stuff—like dreaming up the next big thing in wearables.
The future? I’d bet on fully automated factories. Imagine plugging your design into a system that spits out finished parts without a single coffee break. It’s coming, and it’s going to make rapid prototyping feel like a breeze.
2. Additive Manufacturing: 3D Printing Metals Like Magic
If you’ve ever sketched a wild, curvy heat sink design and sighed because “there’s no way to make that,” additive manufacturing might just be your new best friend. Metal 3D printing is flipping traditional fabrication on its head. Instead of carving away at a block of aluminum, we’re building parts layer by layer—think of it like a high-tech Lego set, but with titanium or stainless steel.
Why does this matter for electronics? Customization. You can now craft lightweight, complex shapes that were impossible with old-school methods. I’ve seen designers use this to whip up heat sinks with internal channels that boost cooling efficiency by 30%. Or take brackets for a new drone—3D printing cuts the weight while keeping them tough as nails. One startup I came across even prototyped a batch of connectors in a single afternoon, skipping the weeks-long wait for molds.
For decision-makers, the kicker is flexibility. Small-batch production becomes dirt cheap, and you can tweak designs on the fly without breaking the bank. Looking ahead, I see this going full-on “on-demand.” Need a one-off part for a client demo? Print it overnight. Less waste, less inventory—just pure, lean innovation.
3. Advanced Alloys: The Material Makeover
Let’s talk materials. If you’re designing high-performance electronics—say, a processor for a gaming rig or a wearable that tracks every heartbeat—you’re probably obsessed with heat and durability. Enter advanced alloys. These aren’t your grandpa’s steel blends. We’re seeing magnesium-aluminum mixes that shave ounces off a device, or copper-based alloys that conduct like a dream.
I stumbled across a project where engineers doped metal with graphene—yes, that wonder-material—and ended up with a processor casing that dissipates heat like it’s got superpowers. It’s not just about performance, either. These alloys are tougher, so your designs last longer in the wild—think rugged tablets or outdoor sensors. For designers, this opens up a playground of possibilities. Want a thinner enclosure that still takes a beating? Done.
Decision-makers, here’s your angle: these materials can future-proof your products. Consumers are clamoring for sleeker, faster, greener tech, and alloys like these deliver. Down the road, I’d wager we’ll see sustainable blends—maybe recycled metals infused with next-gen properties—pushing us toward eco-friendly designs without sacrificing quality.
4. Precision Laser Cutting: Small Parts, Big Impact
Ever tried fitting a puzzle piece into a slot that’s just a hair too small? That’s the nightmare of miniaturization in electronics—everything’s shrinking, and the margins for error are razor-thin. Precision laser cutting is the hero here. These beams can slice metal with accuracy down to microns, perfect for the tiny components flooding modern devices.
I chatted with a designer friend who’s been using laser-cut metal meshes for EMI shielding in a new smartphone line. The results? Flawless fit, zero interference, and a part so delicate you’d swear it was handcrafted. It’s not just phones, either—IoT sensors, medical implants, you name it. Lasers are making the impossible routine.
For decision-makers, this trend screams scalability. You can churn out thousands of micro-parts without losing consistency, and the setup’s quick—no clunky dies or molds. Looking forward, I’d put money on lasers diving into nanotechnology. Imagine crafting metal bits so small they power the next wave of quantum computing. It’s mind-boggling, and it’s closer than you think.
5. Smart Manufacturing: The Brain Behind the Brawn
Here’s where it gets nerdy—and I mean that in the best way. Smart manufacturing, tied to Industry 4.0, is like giving your fabrication shop a brain. IoT sensors, data analytics, and real-time monitoring are turning clunky old processes into something sleek and responsive. For electronics, where quality is non-negotiable, this is huge.
I heard about a plant that stuck sensors on their presses to track stress in alloy sheets as they’re formed into circuit enclosures. If something’s off—say, a weak spot that could crack—they catch it instantly. No more scrapping batches after the fact. Designers, this means your specs get met every time, no compromises. Decision-makers, it’s a cost-saver—fewer defects, less rework.
The future’s even wilder. Predictive maintenance is creeping in, where machines flag issues before they happen. Picture a fabrication line that texts you, “Hey, I need a tune-up next Tuesday,” and downtime vanishes. For electronics, where every minute counts, that’s a game-changer.
6. Sustainable Fabrication: Green Tech’s Secret Weapon
Let’s be real—sustainability isn’t just a buzzword anymore; it’s a mandate. Consumers want gadgets that don’t trash the planet, and regulators are breathing down our necks. Metal fabrication’s stepping up with greener practices that don’t skimp on quality. Think recycling scrap metal from PCB production or tweaking processes to sip less energy.
I saw a company pull off a closed-loop system—every ounce of leftover aluminum from a batch gets melted down and reused. No landfill guilt, just pure efficiency. Designers, this lets you pitch eco-friendly designs without sweating the specs. Decision-makers, it’s a PR win and a cost cut rolled into one—recycled metal’s often cheaper than virgin stock.
Where’s this headed? Carbon-neutral fabrication isn’t a pipe dream. I’d bet we’ll see plants powered by renewables, churning out parts for solar-powered gadgets or electric vehicles. It’s the kind of synergy that makes you feel good about the job—and keeps the bottom line happy.
Wrapping It Up: Why This Matters to You
So, there you have it—six trends shaking up metal fabrication for electronics. Automation’s speeding things up, additive manufacturing’s unleashing your wildest designs, and advanced alloys are pushing performance limits. Lasers are shrinking the impossible, smart tech’s keeping it flawless, and sustainability’s making it responsible. For designers, this is your toolkit to innovate like never before. For decision-makers, it’s the edge you need to stay ahead in a cutthroat market.
These aren’t just cool ideas—they’re the future of how we build the tech that runs our lives. Whether you’re sketching the next wearable or greenlighting a production run, these trends are your runway to breakthroughs. So, what’s your next move? Dive into one of these, test it on a project, and see where it takes you. The future’s wide open, and it’s forged in metal.