5 Case Studies: Metal Fabrication Success Stories in Electronics
We’re diving into five real-world stories where metal fabrication didn’t just solve problems but turned good ideas into great products. These aren’t hypothetical scenarios; they’re lessons from the trenches of innovation, showing how this craft can shrink devices, boost durability, tame heat, polish aesthetics, and speed up timelines.
2/26/20255 min read
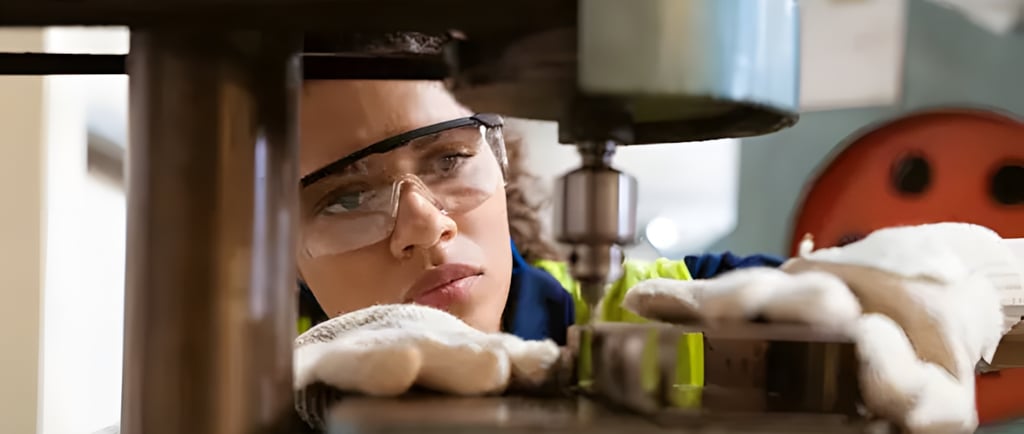
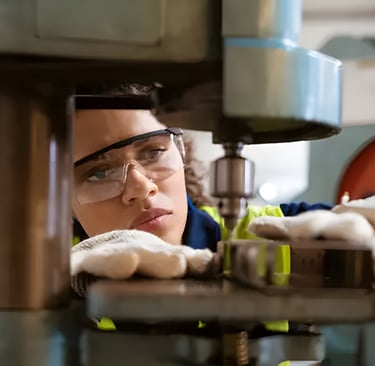
Picture this: you’re holding the latest smartphone, marveling at how something so slim can pack such a punch—or maybe you’re tinkering with a rugged tablet that laughs in the face of dust and drops. Behind these everyday wonders lies an unsung hero: metal fabrication. It’s the craft of bending, cutting, and shaping metal into the precise forms that make modern electronics tick. For designers and decision-makers in electronics development, it’s not just a process—it’s a game-changer.
In this article, we’re diving into five real-world stories where metal fabrication didn’t just solve problems but turned good ideas into great products. These aren’t hypothetical scenarios; they’re lessons from the trenches of innovation, showing how this craft can shrink devices, boost durability, tame heat, polish aesthetics, and speed up timelines. Whether you’re sketching the next big thing or signing off on production, these examples might just spark your next breakthrough.
The Miniaturization Marvel – Shrinking Devices Without Sacrificing Power
Let’s start with a classic challenge: making things smaller. A few years back, a major smartphone maker—let’s call them “TechTrend”—was racing to launch their slimmest model yet. The design team dreamed of a phone so thin it’d slip into a wallet, but the engineers were sweating bullets. Smaller meant cramming more power into less space, and heat was the enemy. One misstep, and they’d have a toasty brick instead of a sleek gadget.
Enter metal fabrication. TechTrend turned to precision sheet metal techniques, crafting micro-enclosures and heat-conductive shields that were thinner than a dime yet tough as nails. These parts weren’t just small—they were smart, channeling heat away from delicate circuits like a tiny air conditioner. The result? A phone that hit the market ahead of schedule, wowing users with its featherweight feel and unflinching performance.
For designers, this is a wake-up call: miniaturization isn’t a pipe dream when you’ve got fabrication in your toolkit. Decision-makers, take note too—investing in precision metalwork can mean the difference between a product that flops and one that flies off shelves. It’s about pushing boundaries without breaking the bank—or the device.
Custom Enclosures for a Niche Market – Tailoring Solutions for Specialty Devices
Next up, meet “RuggedTech,” a company with a mission to build tablets that could survive a construction site or a factory floor. Their customers weren’t casual users—they were folks who needed tech that wouldn’t blink at a little mud or a hard knock. The problem? Off-the-shelf enclosures were too flimsy, and they couldn’t handle extras like reinforced screens or custom ports for industrial sensors.
RuggedTech’s designers sketched out a wishlist: enclosures that were tough, lightweight, and tailored to their quirky specs. Their fabrication partners stepped up, using laser-cut aluminum and stainless steel to build enclosures that fit like a glove. They added corrosion-resistant coatings for good measure, ensuring these tablets could take a beating and keep on computing. The outcome was a product line that didn’t just meet expectations—it set a new standard, earning RuggedTech a loyal following in a niche market.
Here’s the human angle: I once chatted with a designer who worked on a similar project. He said, “It’s like building armor for a knight—you’ve got to protect the guts without weighing it down.” That’s the beauty of custom fabrication—it lets you dream up solutions that fit your vision, not some cookie-cutter mold. For decision-makers, it’s a reminder that niche doesn’t mean small potatoes; with the right approach, it’s a goldmine.
Cooling the Heat – Boosting Efficiency in High-Performance Computing
Now, let’s talk heat—because in electronics, it’s the silent killer. A tech firm we’ll call “ChipMaster” was deep into designing microchips for data centers, the kind that power cloud computing and AI. Trouble was, their new chips were so densely packed with transistors that they were running hotter than a summer barbecue. Overheating meant slower performance, higher failure rates, and unhappy clients.
The team knew they needed a fix, fast. They turned to metal fabrication, commissioning heat sinks and enclosures made from high-conductivity alloys like copper and aluminum. These weren’t your average heat sinks—fabricators sculpted them with intricate fins to maximize surface area, pulling heat away from the chips like a pro. The enclosures were designed to double as thermal pathways, keeping everything cool under pressure. The payoff? Chips that ran faster, lasted longer, and slashed energy costs for their clients.
I remember a friend who works in thermal design telling me, “Heat’s like a bad roommate—you can’t kick it out, but you can manage it.” For designers, this case screams opportunity: pair your circuits with clever metalwork, and you’ve got a winner. Decision-makers, think ROI—better cooling means happier customers and fewer returns. It’s not sexy, but it’s smart.
Aesthetic Edge – Elevating Consumer Electronics with Sleek Designs
Not every success story is about function—sometimes it’s about flair. Take “SoundWave,” a startup dreaming of premium wireless speakers that didn’t just sound good but looked like art. Their challenge was blending beauty with brains. They wanted a casing that turned heads, but it also had to house drivers, batteries, and wiring without rattling or overheating.
SoundWave’s design lead—a guy I’d bet has a vinyl collection to rival any hipster’s—pushed for sheet metal fabrication. They worked with fabricators to craft enclosures from brushed aluminum, with smooth curves and a polished finish that caught the light just right. Inside, the metal doubled as a resonance dampener, keeping sound crisp. When these speakers hit the market, they didn’t just compete—they stood out, earning rave reviews for style and substance.
This one’s personal for me—I’ve always believed good design sells itself. Designers, here’s your cue: don’t settle for plastic when metal can give you that premium edge. Decision-makers, consider this: a product that looks like a million bucks can command a higher price tag. Fabrication isn’t just engineering—it’s branding.
Rapid Prototyping to Market – Speeding Up Innovation
Last but not least, let’s talk speed. “FitTrack,” an up-and-coming player in wearable tech, was in a sprint to launch a fitness tracker before the holiday rush. Their designers had a killer concept—sleek, functional, and packed with sensors—but prototyping was dragging. Traditional methods meant weeks of waiting, and the competition was closing in.
FitTrack’s team pivoted to metal fabrication for rapid prototyping. Using CNC machining and quick-turnaround sheet metal, they churned out enclosures and mounting brackets in days, not weeks. Each iteration was tested, tweaked, and sent back for another round until it was perfect. The result? They beat the clock, launching a tracker that snagged early adopters and set sales records.
I once met a product manager who lived through a similar crunch. She told me, “It’s like cooking under pressure—you’ve got to move fast, but the dish still has to taste good.” Designers, this is your green light: fabrication can keep your creativity on track. Decision-makers, it’s a no-brainer—faster prototyping means faster profits. Time is money, and metal can save you both.
Conclusion
So, there you have it—five stories where metal fabrication turned challenges into triumphs. From shrinking smartphones to armoring tablets, taming heat, polishing speakers, and racing to market, this craft is the backbone of electronics innovation. It’s not just about solving problems; it’s about unlocking possibilities.
For designers, these examples are a playground—proof you can push limits and still deliver. For decision-makers, they’re a business case: invest in fabrication, and you’re investing in products that stand out, perform better, and get to market faster. Next time you’re sketching a concept or crunching numbers, think about how metal could tip the scales.
The future’s bright for electronics, and fabrication’s role is only growing. Maybe your next project will be the sixth success story—why not find out?
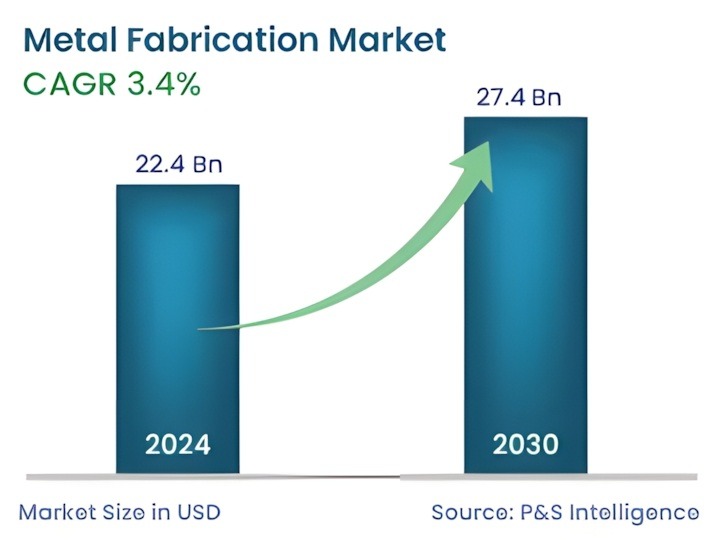
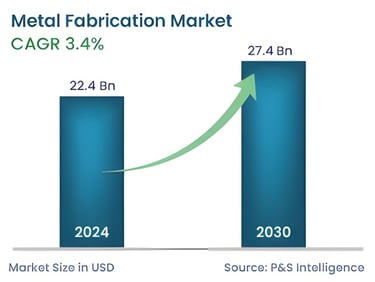